Digital Yarn Twist Tester
$0.00
Digital Yarn Twist Tester

Digital Yarn Twist Tester
A Digital Yarn Twist Tester is a laboratory device used to measure the number of twists (turns) per unit length in a yarn. It’s crucial for evaluating yarn quality, strength, elasticity, and uniformity. The digital version offers precise, automated readings for both S-twist and Z-twist yarns.
Purpose Digital Yarn Twist Tester:
To determine twist per inch (TPI) or twist per meter (TPM) in single and plied yarns using direct untwist or untwist-retwist methods.
Applications Digital Yarn Twist Tester:
Quality control in spinning mills
Yarn standard testing (cotton, polyester, blends)
R&D in textile manufacturing
Working Principle Digital Yarn Twist Tester:
One end of the yarn is clamped, and the other is rotated to remove or measure twists.
The tester counts and displays twist digitally based on length and rotation.
Benefits of Digital Yarn Twist Tester:
High Accuracy – Digital readout ensures precise twist measurements.
Quick Testing – Faster than manual methods, increasing lab efficiency.
Versatile Application – Suitable for single, doubled, or plied yarns.
Reduces Human Error – Automated counting improves repeatability and consistency.
Supports Both S & Z Twist – Measures both twist directions accurately.
User-Friendly Operation – Intuitive controls and clear display simplify use.
Features of Digital Yarn Twist Tester:
Digital Display – Shows real-time twist count and length.
Motorized Rotation- Smooth, adjustable rotation speed for controlled untwisting.
Dual Clamp System – Holds yarn securely to prevent slippage.
Length Measurement Scale – Built-in ruler or encoder for precise yarn length setup.
Auto Stop Function – Automatically stops when yarn is fully untwisted.
Selectable Units – Twist readings available in TPI or TPM.
How to Use Digital Yarn Twist Tester:
Prepare the Yarn Sample
– Cut a yarn length (e.g., 250 mm or 10 inches) as per testing standard.
– Make sure it’s free from knots or damage.
Mount the Yarn – Fix one end in the stationary clamp and the other in the rotating clamp.
– Ensure the yarn is straight and under slight tension.
Set the Gauge Length – Adjust the length scale or input it digitally, depending on the machine.
Select Twist Direction – Choose S or Z direction based on the yarn’s twist.
Start the Test – Activate the motor to untwist (or untwist-retwist, if applicable). – The display shows the number of rotations. Read the Twist Value – The twist (TPI/TPM) appears automatically based on the set length.
Stop and Unload – Once reading is complete, stop the machine and remove the yarn.
Record the Result – Note the reading for documentation or further analysis.
Maintenance Tips for Digital Yarn Twist Tester:
Daily:
☐ Wipe down the machine and clamps to remove dust or fibers
☐ Check for yarn residue on rotating parts
☐ Ensure display and buttons are responsive
Weekly:
☐ Lubricate rotating spindle lightly (if required)
☐ Inspect clamps for wear or misalignment
☐ Test motor rotation for smooth operation
☐ Check twist direction selector switch
Monthly:
☐ Calibrate digital display if twist readings drift
☐ Inspect electrical wiring and connectors
☐ Tighten any loose screws or panel parts
Safety Tips:
Avoid Loose Clothing: Prevent getting caught in the rotating spindle
Use Proper Yarn Tension: Overstretching may snap the yarn or damage clamps
Handle With Care: Avoid rough handling of the digital panel or twist arm
Power Off When Not in Use: Prevents accidental operation
Follow Manual: Refer to user guide for specific calibration or cleaning procedures
Digital Yarn Twist Tester – Maintenance & Safety Checklist
Daily Maintenance:
☐ Clean clamps and body surface
☐ Remove lint or yarn fragments
☐ Verify display & control buttons function properly
Weekly Maintenance:
☐ Lightly lubricate spindle if required
☐ Inspect clamp alignment and grip
☐ Test motor for smooth, silent operation
☐ Check twist direction switch
Monthly Maintenance:
☐ Calibrate twist reading accuracy
☐ Inspect cables and connectors
☐ Tighten loose hardware
☐ Run full test to ensure system performance
Safety Checklist:
☐ Keep hands clear of rotating parts during testing
☐ Avoid loose clothing or jewelry
☐ Do not overstretch or over tension yarn
☐ Power off when cleaning or not in use
☐ Follow the machine’s manual for calibration and service
Basic Troubleshooting Guide – Digital Yarn Twist Tester
Issue: No Power / Display Not Turning On
– Check power cable and socket
– Inspect fuse or main switch
– Ensure emergency stop isn’t engaged
Issue: Twist Count Seems Inaccurate
– Recalibrate the machine
– Verify yarn length input is correct
– Check for slippage in clamps
Issue: Motor Not Rotating
– Ensure motor switch is ON
– Inspect motor connection and wiring
– Test rotation manually to check for blockage
Issue: Display Freezes or Buttons Unresponsive
– Restart the machine
– Check control panel for dust or moisture
– Contact support if issue persists
Issue: Auto-Stop Not Working
– Ensure length and twist direction are set
– Check sensor alignment or damage
– Reboot and re-run test
Scope of application
It is used for testing the twist, twist irregularity and twist shrinkage of all kinds of yarns.
[Related standards]
GB/T2543.1/2 FZ/T10001 ISO2061 ASTM D1422 JIS L1095 etc.
Technical parameters
1. Work mode:Computer program control, data processing, printout results
2. Test methods:
A, Average twisting slip elongation
B, Average maximum twisting elongation.
C, Direct counting method D, twisting twisting A method
E, Twisting twisting B method f and three times twisting twisting method
3. Sample length:10、25、50、100、200、250、500mm
4. Twist test range:1~1998 twist /10cm, 1~1998 twist /m
5. The extent of twist removal:Maximum 50mm
6. Maximum twist measurement.20mm
7. Speed:600~3000r/min
8. Pre tension:0.5~171.5cN

Digital Yarn Twist Tester
9. Size:920×170×220mm
10. Power supply:Ac220V 50Hz 25W
11. Weight:16kg
Related products
High speed hard winding machine
High Speed Hard Winding Machine

High Speed Hard Winding Machine
- Increased Productivity - High-speed operation reduces winding time significantly.
- Consistent Package Quality - Ensures uniform and firm yarn packages ideal for further processing.
- Reduced Yarn Breakage - Precise tension control minimizes yarn damage during winding.
- Versatility - Handles different types of yarns including delicate and coarse fibers.
- User-Friendly Operation - Simple controls and automation reduce operator fatigue.
- Improved Efficiency - Automatic package build-up reduces manual adjustments.
- Space Saving - Compact design fits well in production lines and labs.
- Set Up the Machine - Switch on the power and check all safety guards.
- Load Yarn - Thread the yarn through tension guides and eyelets as per the manual.
- Adjust Tension - Set tension according to yarn type to avoid slack or breakage.
- Place Empty Cone/Package - Mount the empty cone or package holder securely.
- Start Winding- Press the start button; machine will begin winding at set speed.
- Monitor the Process - Observe yarn package build-up and make adjustments if necessary.
- Stop and Remove Package - Once winding is complete, stop the machine and remove the yarn package carefully.
- Maintenance - Clean the machine regularly and lubricate moving parts as needed.
- High-Speed Operation - Capable of winding yarns at fast speeds (up to 3000 RPM) to boost productivity.
- Precise Tension Control - Adjustable tension mechanism to prevent yarn breakage and ensure tight winding.
- Automatic Package Formation - Uniform, firm package build-up for consistent yarn quality.
- Versatile Yarn Compatibility - Suitable for cotton, polyester, wool, and blended yarns.
- User-Friendly Interface - Easy controls with digital or analog panels for speed and tension adjustment.
- Robust Construction - Durable stainless steel or metal frame for long-term reliability.
- Safety Features - Includes emergency stop buttons and yarn break sensors.
- Compact Design - Space-saving structure ideal for labs and production floors.
- Low Maintenance - Designed for easy cleaning and minimal upkeep.

High Speed Hard Winding Machine
Fully Automatic Radio Frequency Dryer
Fully Automatic Radio Frequency Dryer
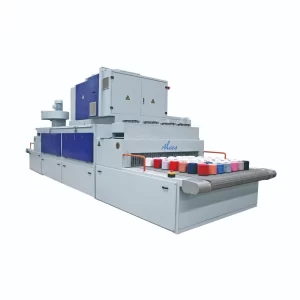
Fully Automatic Radio Frequency Dryer
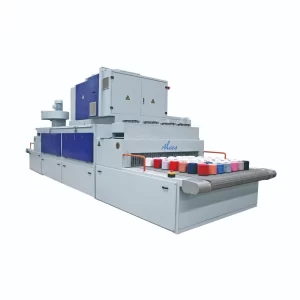
Fully Automatic Radio Frequency Dryer
IR Dyeing Machine Dunlin
IR Dyeing Machine Dunlin
IR Dyeing machine Dunlin is Safe, high efficiency, environment friendly, energy saving, optimum for new dyeing small sample machines0 - 3.5 ℃ / min Cooling rate 0.2 - 5 ℃ / min Cooling method Air-cooled Rotation speed 0 - 60 rpm Liquor ratio 1:5 -1:100 Power supply 1∮AC 220V 50/60HZ Dimensions( L x W x H) 670×670×780mm 860×680×780mm Weight 100kg 120kg Standard Accessories Cups 1set
Put the test sample. Cups stand 1set Place where to put cups. Protective glove 1set To avoid to be hurt by HT cups. Model: IF-24SCapacity: 24 pots Brad: DUNLIN Origin: China
Color dyeing tests for various dyestuffs of IR Dyeing machine Dunlin- Step dyeing tests. C. Dispersing, levelling and impregnating test. D. High or low liquor ratio exhausting tests. E. Fabric steak and staining tests. F. Concentration tests and others. Protection and Safety gates to protect. Temperature control accuracy +/- 0.2degree

IR Dyeing machine
Steam Soaping machine
Steam Soaping Machine
A Steam Soaping Machine is a specialized laboratory apparatus used in textile dyeing processes, particularly for post-dyeing treatments like soaping, which enhances color fastness and removes unfixed dyes from fabric samples. This machine is designed to perform soaping treatments on dyed textile samples using steam. Soaping is a critical step in dyeing, especially for reactive dyes, as it removes unfixed dye particles, ensuring better color fastness and preventing dye bleeding. The steam soaping process involves treating the dyed fabric with a soaping solution at elevated temperatures, facilitated by steam, to achieve optimal results. ⚙️ Key Features of Steam Soaping Machine - Beaker Material: Constructed with high-grade 316L stainless steel for excellent corrosion resistance and durability.- Operation Modes: Offers both automatic control and manual water filling options, providing flexibility in operation. - Drainage System: Equipped with an automatic drainage device for efficient removal of used solutions.- Temperature Control: Precise temperature regulation to maintain optimal soaping conditions.- Compact Design: Suitable for laboratory settings, occupying minimal space while delivering effective performance. ✅ Benefits of Steam Soaping Machine - Enhanced Color Fastness: Effectively removes unfixed dyes, resulting in improved wash and rub fastness of the fabric.- Efficient Processing: Reduces the time required for post-dyeing treatments compared to conventional methods.- Consistent Results: Provides uniform treatment across samples, ensuring reproducibility in testing and quality control.- Resource Optimization: Minimizes water and chemical usage through controlled processing parameters.- Versatility: Applicable to various fabric types and dye classes, making it a valuable tool in research and development. Typical Applications - Laboratory Testing: Used in dyeing laboratories for evaluating the fastness properties of dyed samples. - Research and Development: Assists in developing and optimizing dyeing processes and formulations. - Quality Control: Ensures that dyed fabrics meet specified fastness standards before bulk production. In summary, a Steam Soaping Machine is an essential laboratory instrument in the textile industry, facilitating efficient and effective post-dyeing treatments to enhance the quality and durability of dyed fabrics. Features of Steam Soaping Machine:- High-Grade Stainless Steel Beakers - Made from 316L stainless steel for excellent chemical and heat resistance.
- Steam-Based Heating - Uses direct or indirect steam to maintain consistent high temperatures ideal for soaping.
- Precise Temperature Control - Maintains stable temperatures (typically up to 98–100°C) for effective removal of unfixed dyes.
- Automatic and Manual Modes - Offers both programmable automatic cycles and manual operation for flexibility.
- Beaker Agitation or Rotation - Ensures uniform soaping action across fabric surfaces.
- Automatic Drainage System - Efficiently removes used soaping solution to speed up cycle changeovers.
- Compact Design - Fits well in lab settings while allowing multiple samples to be processed simultaneously.
- Safety Features - Includes pressure and temperature protection systems to ensure safe operation.
- Low Water and Chemical Use - Designed for minimal liquor ratios, enhancing sustainability.
- User-Friendly Interface - Simple digital controls or touch panel for easy operation and cycle programming.
- Prepare the Dyed Sample - After dyeing, rinse the fabric to remove surface dye and prepare it for soaping.
- Load the Fabric - Place the dyed fabric or sample into the beakers or holders inside the machine.
- Add Soaping Solution - Pour the prepared soaping agent (usually a detergent solution) into the beakers or tank as per recipe.
- Set Parameters
- Start the Cycle - Begin the soaping process. The machine will heat the solution using steam and agitate/rotate the beakers for even treatment.
- Drain and Rinse - After the cycle ends, the machine may auto-drain. Rinse the fabric with warm water to remove residual chemicals.
- Unload the Samples - Carefully remove the fabric. Inspect for evenness and color fastness improvement.
- Clean the Machine - Rinse and dry the beakers or tank to maintain hygiene for the next use.

Perspiration Tester
Perspiration Tester

Perspiration Tester
- Fabric samples are treated with synthetic perspiration solution (acidic or alkaline).
- They are sandwiched with adjacent fabric and placed between glass or acrylic plates.
- The assembly is loaded into the tester and pressed under specific pressure.
- it’s then incubated at 37°C (body temperature) for a fixed time (typically 4 or 16 hours).
- Afterward, color change and staining are evaluated using a gray scale.
- Accurate Sweat Simulation - Mimics real-life effects of acidic and alkaline perspiration on fabrics.
- Improves Product Quality - Ensures textiles retain color and don’t bleed or stain when worn.
- Supports Standard Compliance - Follows ISO and AATCC test standards for global market approval.
- Protects Brand Reputation- Reduces customer complaints due to dye transfer or fading.
- Simple and Repeatable- Provides consistent pressure and conditions for reliable results.
- Multi-Sample Testing- Tests multiple specimens at once, saving time in labs.
- Durable and Low Maintenance- Robust frame with minimal moving parts makes it long-lasting and easy to care for.
- Stainless Steel Frame - Corrosion-resistant body for durability and long-term use.
- Multi-Sample Capacity - Can hold up to 20 or more specimens for batch testing.
- Standardized Loading Weight- Applies uniform pressure (usually 12.5 kPa) across all samples.
- Removable Plates - Glass or acrylic plates ensure even contact and easy cleaning.
- Compact Design- Space-saving, bench-top model ideal for lab environments.
- Complies with Test Standards - Meets ISO 105 E04, AATCC 15, and related perspiration fastness standards.
- Ease of Operation - Simple loading, unloading, and incubation process.
- High-Temperature Resistance - Can be used inside incubators at 37°C or ovens as required.
- Prepare the Test Solution - Mix artificial acidic or alkaline perspiration as per standard (ISO or AATCC).
- Cut the Fabric Samples - Cut both the test fabric and adjacent white fabric (usually cotton) to standard size.
- Soak the Samples - Immerse the fabric sandwich (test + adjacent) in the test solution for 30 minutes.
- Remove Excess Liquid - Gently squeeze or blot to remove extra moisture—do not dry.
- Load in the Tester- Place each sandwich between glass or acrylic separator plates in the tester.
- Apply Pressure - Tighten the top plate or place the standard weight on top to apply uniform pressure.
- Incubate - Keep the loaded tester in an oven or incubator at 37°C for 4–16 hours (depending on the method).
- Accurate Sweat Simulation - Mimics real-life effects of acidic and alkaline perspiration on fabrics.
- Improves Product Quality - Ensures textiles retain color and don’t bleed or stain when worn.
- Supports Standard Compliance - Follows ISO and AATCC test standards for global market approval.
- Protects Brand Reputation- Reduces customer complaints due to dye transfer or fading.
- Simple and Repeatable- Provides consistent pressure and conditions for reliable results.
- Multi-Sample Testing- Tests multiple specimens at once, saving time in labs.
- Durable and Low Maintenance- Robust frame with minimal moving parts makes it long-lasting and easy to care for.
- Dry and Evaluate - Remove, air dry the samples, then assess color change and staining using a gray scale.
- Fabric samples are treated with synthetic perspiration solution (acidic or alkaline).
- They are sandwiched with adjacent fabric and placed between glass or acrylic plates.
- The assembly is loaded into the tester and pressed under specific pressure.
- it’s then incubated at 37°C (body temperature) for a fixed time (typically 4 or 16 hours).
- Afterward, color change and staining are evaluated using a gray scale.
Perspiration Tester
Electronic wrap reel
Electronic Wrap Reel

Electronic Wrap Reel

Electronic Wrap Reel
GSM Cutter with Balance
GSM Cutter with Balance

GSM Cutter with Balance
Card winding machine
Card Winding Machine
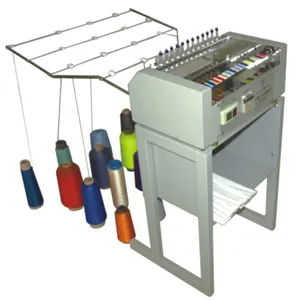
Card Winding Machine
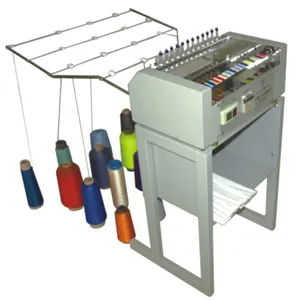
Card Winding Machine