Digital Yarn Twist Tester
$0.00
Digital Yarn Twist Tester

Digital Yarn Twist Tester
A Digital Yarn Twist Tester is a laboratory device used to measure the number of twists (turns) per unit length in a yarn. It’s crucial for evaluating yarn quality, strength, elasticity, and uniformity. The digital version offers precise, automated readings for both S-twist and Z-twist yarns.
Purpose Digital Yarn Twist Tester:
To determine twist per inch (TPI) or twist per meter (TPM) in single and plied yarns using direct untwist or untwist-retwist methods.
Applications Digital Yarn Twist Tester:
Quality control in spinning mills
Yarn standard testing (cotton, polyester, blends)
R&D in textile manufacturing
Working Principle Digital Yarn Twist Tester:
One end of the yarn is clamped, and the other is rotated to remove or measure twists.
The tester counts and displays twist digitally based on length and rotation.
Benefits of Digital Yarn Twist Tester:
High Accuracy – Digital readout ensures precise twist measurements.
Quick Testing – Faster than manual methods, increasing lab efficiency.
Versatile Application – Suitable for single, doubled, or plied yarns.
Reduces Human Error – Automated counting improves repeatability and consistency.
Supports Both S & Z Twist – Measures both twist directions accurately.
User-Friendly Operation – Intuitive controls and clear display simplify use.
Features of Digital Yarn Twist Tester:
Digital Display – Shows real-time twist count and length.
Motorized Rotation- Smooth, adjustable rotation speed for controlled untwisting.
Dual Clamp System – Holds yarn securely to prevent slippage.
Length Measurement Scale – Built-in ruler or encoder for precise yarn length setup.
Auto Stop Function – Automatically stops when yarn is fully untwisted.
Selectable Units – Twist readings available in TPI or TPM.
How to Use Digital Yarn Twist Tester:
Prepare the Yarn Sample
– Cut a yarn length (e.g., 250 mm or 10 inches) as per testing standard.
– Make sure it’s free from knots or damage.
Mount the Yarn – Fix one end in the stationary clamp and the other in the rotating clamp.
– Ensure the yarn is straight and under slight tension.
Set the Gauge Length – Adjust the length scale or input it digitally, depending on the machine.
Select Twist Direction – Choose S or Z direction based on the yarn’s twist.
Start the Test – Activate the motor to untwist (or untwist-retwist, if applicable). – The display shows the number of rotations. Read the Twist Value – The twist (TPI/TPM) appears automatically based on the set length.
Stop and Unload – Once reading is complete, stop the machine and remove the yarn.
Record the Result – Note the reading for documentation or further analysis.
Maintenance Tips for Digital Yarn Twist Tester:
Daily:
☐ Wipe down the machine and clamps to remove dust or fibers
☐ Check for yarn residue on rotating parts
☐ Ensure display and buttons are responsive
Weekly:
☐ Lubricate rotating spindle lightly (if required)
☐ Inspect clamps for wear or misalignment
☐ Test motor rotation for smooth operation
☐ Check twist direction selector switch
Monthly:
☐ Calibrate digital display if twist readings drift
☐ Inspect electrical wiring and connectors
☐ Tighten any loose screws or panel parts
Safety Tips:
Avoid Loose Clothing: Prevent getting caught in the rotating spindle
Use Proper Yarn Tension: Overstretching may snap the yarn or damage clamps
Handle With Care: Avoid rough handling of the digital panel or twist arm
Power Off When Not in Use: Prevents accidental operation
Follow Manual: Refer to user guide for specific calibration or cleaning procedures
Digital Yarn Twist Tester – Maintenance & Safety Checklist
Daily Maintenance:
☐ Clean clamps and body surface
☐ Remove lint or yarn fragments
☐ Verify display & control buttons function properly
Weekly Maintenance:
☐ Lightly lubricate spindle if required
☐ Inspect clamp alignment and grip
☐ Test motor for smooth, silent operation
☐ Check twist direction switch
Monthly Maintenance:
☐ Calibrate twist reading accuracy
☐ Inspect cables and connectors
☐ Tighten loose hardware
☐ Run full test to ensure system performance
Safety Checklist:
☐ Keep hands clear of rotating parts during testing
☐ Avoid loose clothing or jewelry
☐ Do not overstretch or over tension yarn
☐ Power off when cleaning or not in use
☐ Follow the machine’s manual for calibration and service
Basic Troubleshooting Guide – Digital Yarn Twist Tester
Issue: No Power / Display Not Turning On
– Check power cable and socket
– Inspect fuse or main switch
– Ensure emergency stop isn’t engaged
Issue: Twist Count Seems Inaccurate
– Recalibrate the machine
– Verify yarn length input is correct
– Check for slippage in clamps
Issue: Motor Not Rotating
– Ensure motor switch is ON
– Inspect motor connection and wiring
– Test rotation manually to check for blockage
Issue: Display Freezes or Buttons Unresponsive
– Restart the machine
– Check control panel for dust or moisture
– Contact support if issue persists
Issue: Auto-Stop Not Working
– Ensure length and twist direction are set
– Check sensor alignment or damage
– Reboot and re-run test
Scope of application
It is used for testing the twist, twist irregularity and twist shrinkage of all kinds of yarns.
[Related standards]
GB/T2543.1/2 FZ/T10001 ISO2061 ASTM D1422 JIS L1095 etc.
Technical parameters
1. Work mode:Computer program control, data processing, printout results
2. Test methods:
A, Average twisting slip elongation
B, Average maximum twisting elongation.
C, Direct counting method D, twisting twisting A method
E, Twisting twisting B method f and three times twisting twisting method
3. Sample length:10、25、50、100、200、250、500mm
4. Twist test range:1~1998 twist /10cm, 1~1998 twist /m
5. The extent of twist removal:Maximum 50mm
6. Maximum twist measurement.20mm
7. Speed:600~3000r/min
8. Pre tension:0.5~171.5cN

Digital Yarn Twist Tester
9. Size:920×170×220mm
10. Power supply:Ac220V 50Hz 25W
11. Weight:16kg
Related products
Steam Soaping machine
Steam Soaping Machine
A Steam Soaping Machine is a specialized laboratory apparatus used in textile dyeing processes, particularly for post-dyeing treatments like soaping, which enhances color fastness and removes unfixed dyes from fabric samples. This machine is designed to perform soaping treatments on dyed textile samples using steam. Soaping is a critical step in dyeing, especially for reactive dyes, as it removes unfixed dye particles, ensuring better color fastness and preventing dye bleeding. The steam soaping process involves treating the dyed fabric with a soaping solution at elevated temperatures, facilitated by steam, to achieve optimal results. ⚙️ Key Features of Steam Soaping Machine - Beaker Material: Constructed with high-grade 316L stainless steel for excellent corrosion resistance and durability.- Operation Modes: Offers both automatic control and manual water filling options, providing flexibility in operation. - Drainage System: Equipped with an automatic drainage device for efficient removal of used solutions.- Temperature Control: Precise temperature regulation to maintain optimal soaping conditions.- Compact Design: Suitable for laboratory settings, occupying minimal space while delivering effective performance. ✅ Benefits of Steam Soaping Machine - Enhanced Color Fastness: Effectively removes unfixed dyes, resulting in improved wash and rub fastness of the fabric.- Efficient Processing: Reduces the time required for post-dyeing treatments compared to conventional methods.- Consistent Results: Provides uniform treatment across samples, ensuring reproducibility in testing and quality control.- Resource Optimization: Minimizes water and chemical usage through controlled processing parameters.- Versatility: Applicable to various fabric types and dye classes, making it a valuable tool in research and development. Typical Applications - Laboratory Testing: Used in dyeing laboratories for evaluating the fastness properties of dyed samples. - Research and Development: Assists in developing and optimizing dyeing processes and formulations. - Quality Control: Ensures that dyed fabrics meet specified fastness standards before bulk production. In summary, a Steam Soaping Machine is an essential laboratory instrument in the textile industry, facilitating efficient and effective post-dyeing treatments to enhance the quality and durability of dyed fabrics. Features of Steam Soaping Machine:- High-Grade Stainless Steel Beakers - Made from 316L stainless steel for excellent chemical and heat resistance.
- Steam-Based Heating - Uses direct or indirect steam to maintain consistent high temperatures ideal for soaping.
- Precise Temperature Control - Maintains stable temperatures (typically up to 98–100°C) for effective removal of unfixed dyes.
- Automatic and Manual Modes - Offers both programmable automatic cycles and manual operation for flexibility.
- Beaker Agitation or Rotation - Ensures uniform soaping action across fabric surfaces.
- Automatic Drainage System - Efficiently removes used soaping solution to speed up cycle changeovers.
- Compact Design - Fits well in lab settings while allowing multiple samples to be processed simultaneously.
- Safety Features - Includes pressure and temperature protection systems to ensure safe operation.
- Low Water and Chemical Use - Designed for minimal liquor ratios, enhancing sustainability.
- User-Friendly Interface - Simple digital controls or touch panel for easy operation and cycle programming.
- Prepare the Dyed Sample - After dyeing, rinse the fabric to remove surface dye and prepare it for soaping.
- Load the Fabric - Place the dyed fabric or sample into the beakers or holders inside the machine.
- Add Soaping Solution - Pour the prepared soaping agent (usually a detergent solution) into the beakers or tank as per recipe.
- Set Parameters
- Start the Cycle - Begin the soaping process. The machine will heat the solution using steam and agitate/rotate the beakers for even treatment.
- Drain and Rinse - After the cycle ends, the machine may auto-drain. Rinse the fabric with warm water to remove residual chemicals.
- Unload the Samples - Carefully remove the fabric. Inspect for evenness and color fastness improvement.
- Clean the Machine - Rinse and dry the beakers or tank to maintain hygiene for the next use.

Fully Automatic Radio Frequency Dryer
Fully Automatic Radio Frequency Dryer
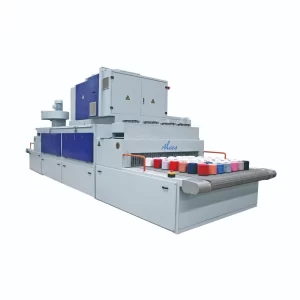
Fully Automatic Radio Frequency Dryer
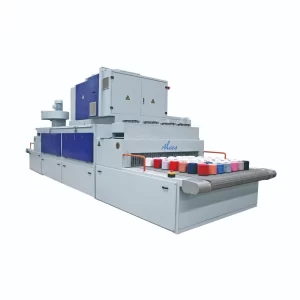
Fully Automatic Radio Frequency Dryer
High speed hard winding machine
High Speed Hard Winding Machine

High Speed Hard Winding Machine
- Increased Productivity - High-speed operation reduces winding time significantly.
- Consistent Package Quality - Ensures uniform and firm yarn packages ideal for further processing.
- Reduced Yarn Breakage - Precise tension control minimizes yarn damage during winding.
- Versatility - Handles different types of yarns including delicate and coarse fibers.
- User-Friendly Operation - Simple controls and automation reduce operator fatigue.
- Improved Efficiency - Automatic package build-up reduces manual adjustments.
- Space Saving - Compact design fits well in production lines and labs.
- Set Up the Machine - Switch on the power and check all safety guards.
- Load Yarn - Thread the yarn through tension guides and eyelets as per the manual.
- Adjust Tension - Set tension according to yarn type to avoid slack or breakage.
- Place Empty Cone/Package - Mount the empty cone or package holder securely.
- Start Winding- Press the start button; machine will begin winding at set speed.
- Monitor the Process - Observe yarn package build-up and make adjustments if necessary.
- Stop and Remove Package - Once winding is complete, stop the machine and remove the yarn package carefully.
- Maintenance - Clean the machine regularly and lubricate moving parts as needed.
- High-Speed Operation - Capable of winding yarns at fast speeds (up to 3000 RPM) to boost productivity.
- Precise Tension Control - Adjustable tension mechanism to prevent yarn breakage and ensure tight winding.
- Automatic Package Formation - Uniform, firm package build-up for consistent yarn quality.
- Versatile Yarn Compatibility - Suitable for cotton, polyester, wool, and blended yarns.
- User-Friendly Interface - Easy controls with digital or analog panels for speed and tension adjustment.
- Robust Construction - Durable stainless steel or metal frame for long-term reliability.
- Safety Features - Includes emergency stop buttons and yarn break sensors.
- Compact Design - Space-saving structure ideal for labs and production floors.
- Low Maintenance - Designed for easy cleaning and minimal upkeep.

High Speed Hard Winding Machine
Oscillation type water bath Dyeing Machine
Oscillation Type Water Bath Dyeing Machine
An Oscillation Type Water Bath Dyeing Machine is a laboratory apparatus designed for dyeing and washing textile samples under controlled temperature conditions. It combines a heated water bath with an oscillating mechanism to ensure uniform dye penetration and consistent coloration across fabric or yarn samples. Key Features of Oscillation Type Water Bath Dyeing Machine - Oscillating Mechanism: Provides back-and-forth movement to agitate the dye solution, ensuring even contact between the dye and the textile sample.- Multiple Beaker Capacity: Typically accommodates 12 to 24 beakers, allowing simultaneous processing of multiple samples under identical or varied conditions. - Digital Temperature Control: Maintains precise temperature settings, usually up to 99°C, suitable for various dyeing processes including atmospheric dyeing, scouring, and bleaching.- Adjustable Oscillation Speed: Offers variable speed settings, commonly ranging from 50 to 200 cycles per minute, to accommodate different fabric types and dyeing requirements. - Programmable Settings: Advanced models come with programmable controllers, allowing users to set and save multiple dyeing protocols for repeatability and efficiency. Durable Construction: Constructed with high-quality stainless steel (e.g., SUS304), ensuring resistance to corrosion and longevity even under rigorous laboratory conditions. ✅ Benefits of Oscillation Type Water Bath Dyeing Machine - Uniform Dyeing Results: The oscillation mechanism ensures consistent dye penetration, reducing the risk of uneven coloration and enhancing the reproducibility of results.- Efficiency in Sample Processing: The ability to process multiple samples simultaneously accelerates laboratory workflows and facilitates comparative studies. - Versatility: Suitable for a range of applications including dyeing, washing, scouring, bleaching, and fastness testing across various textile materials.- Energy and Resource Conservation: Designed for low liquor ratios (e.g., 1:5 to 1:20), these machines minimize water and chemical usage, promoting sustainable laboratory practices. - Enhanced Safety and Cleanliness: Enclosed beaker systems reduce the risk of spills and exposure to chemicals, ensuring a safer laboratory environment. Typical Applications of Oscillation Type Water Bath Dyeing Machine - Textile Research and Development: Ideal for developing and testing new dye formulations and processes on a small scale before scaling up to production levels. Quality Control: Used in quality assurance laboratories to assess color fastness, dye uptake, and other critical parameters of textile products.- Educational Purposes: Serves as a practical tool in academic settings for teaching dyeing principles and techniques. In summary, the Oscillation Type Water Bath Dyeing Machine is an essential tool in textile laboratories, offering precise control over dyeing parameters, improving efficiency, and ensuring high-quality, reproducible results across various textile materials. Features of Oscillation Type Water Bath Dyeing Machine:- Oscillating Mechanism - Provides back-and-forth movement of beakers for uniform dye penetration and sample agitation.
- Multiple Beaker Capacity - Supports dyeing of 12–24 samples simultaneously, ideal for comparative lab testing.
- Digital Temperature Control - Maintains precise water bath temperature (typically up to 99°C), essential for consistent dyeing.
- Variable Oscillation Speed - Adjustable speed settings (e.g., 50–200 cycles/min) to suit different materials and processes.
- Programmable Settings - Allows setting of temperature, time, and speed for repeatable and automated dyeing cycles.
- Stainless Steel Construction - Corrosion-resistant frame and bath for durability in chemical environments.
- Beaker Safety Holders - Secure placement of beakers to prevent spills and maintain consistent treatment.
- Compact Design - Lab-friendly size for easy integration into research and quality control spaces.
- Low Liquor Ratio Operation - Efficient dyeing using minimal dye bath volume (e.g., 1:5 to 1:20), reducing chemical and water use.
- Quiet and Stable Performance

water bath/Shaker bath Dyeing machine
GSM Cutter with Balance
GSM Cutter with Balance

GSM Cutter with Balance
Spray Rating Tester
Spray Rating Tester

Spray Rating Tester
- Quick and Simple Evaluation - Offers a fast way to assess fabric water repellency without complex setup.
- Standardized Testing- Complies with AATCC 22 and ISO 4920, ensuring globally accepted results.
- Cost-Effective- Low maintenance and no power requirement make it economical for routine lab use.
- Improves Fabric Performance - Helps manufacturers develop or improve water-resistant textiles.
- Non-Destructive Test - Does not damage the fabric, allowing for additional tests on the same sample.
- Visual Grading- Easy to interpret using a standard spray rating chart (0 to 100 scale).
- Supports Quality Control - Detects finish degradation or variation in water-repellent treatments.
- Portable and Compact- Lightweight design allows easy use in various lab or field settings.
- Standardized Spray Nozzle - Delivers consistent water spray per AATCC and ISO specifications.
- 45° Specimen Mounting Angle - Ensures uniform test setup for accurate and repeatable results.
- Stainless Steel or Aluminum Frame - Corrosion-resistant and durable for long-term use with water exposure.
- Water Reservoir and Funnel System - Provides precise water volume (usually 250 ml) for each test.
- Graduated Spray Stand- Fixed height (150 mm above specimen) for controlled spray impact.
- Detachable Specimen Holder- Easy loading and removal of fabric samples.
- Compact and Lightweight Design - Portable and convenient for both lab and field testing.
- No Electricity Required - Fully manual operation increases reliability and reduces operating costs.
- Prepare the Sample - Cut fabric to standard size (usually 180 × 180 mm). - Condition the sample if required (21°C, 65% RH for 24 hours).
- Mount the Fabric - Place the fabric on the specimen holder at a 45° angle.
- Fill the Reservoir - Pour 250 ml of distilled water into the upper funnel.
- Start the Test - Release the water through the nozzle; it sprays over the fabric for about 25–30 seconds.
- Inspect the Fabric - After spraying, visually assess the water beading or penetration on the surface.
- Rate the Sample - Compare the fabric’s wetting pattern with the standard spray rating chart: - 100 = No sticking/wetting - 90–50 = Partial wetting - 0 = Complete wetting
- Record the Rating - Document the spray rating for quality control or reporting.

Electronic wrap reel
Electronic Wrap Reel

Electronic Wrap Reel

Electronic Wrap Reel
Card winding machine
Card Winding Machine
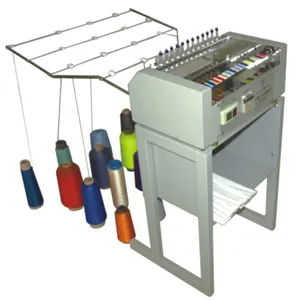
Card Winding Machine
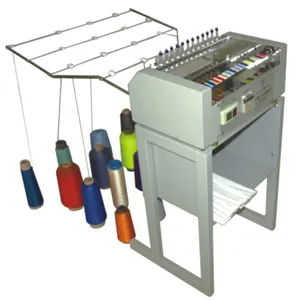
Card Winding Machine