Card winding machine
$0.00
Card Winding Machine
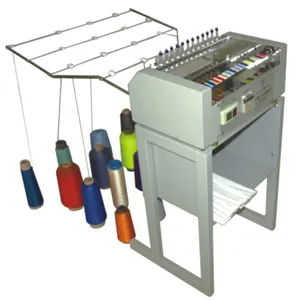
Card Winding Machine
A Card Winding Machine is used in textile processing to wind yarn from hanks, bobbins, or cones onto cards or perforated boards, typically for dyeing or sampling purposes. It ensures uniform yarn distribution and tension, crucial for consistent dye penetration.
Purpose Card Winding Machine:
To wind yarn onto flat cards or holders for lab dyeing, color matching, or textile sample display.
Applications Card Winding Machine:
Yarn dyeing labs
R&D and sample development
Display or swatch card preparation
Yarn shade catalog creation
Working Principle Card Winding Machine:
The yarn is drawn from a source (cone or bobbin) and wound evenly onto a card.
The machine controls the winding speed, spacing, and tension to avoid tangles or breaks.
Benefits of Card Winding Machine:
Uniform Yarn Placement- Ensures even winding for consistent dyeing and presentation.
Ideal for Sampling – Perfect for creating lab dye samples, color cards, and swatches.
Time-Saving – Automates a manual process, increasing efficiency.
Low Yarn Waste – Allows controlled use of small yarn amounts for trials.
Supports Various Yarn Types – Can handle cotton, polyester, blends, and fancy yarns.
Features of Card Winding Machine:
Adjustable Winding Tension – Maintains constant tension to prevent yarn breakage.
Speed Control – Variable winding speed for different yarn types and applications.
Card Size Compatibility – Supports multiple card sizes and formats.
Precision Traverse System- Ensures neat layer formation without overlapping.
Compact Design – Table-top or stand-mounted; suitable for labs or sample rooms.
How to Use a Card Winding Machine:
Prepare the Yarn Source – Place the yarn cone or bobbin on the yarn holder. – Thread the yarn through the tensioner and guide system. Insert the Card – Mount the empty card or board onto the winding platform/clamp securely.
Set Winding Parameters- Adjust winding speed, tension, and traverse width based on yarn type and card size.
Start the Machine – Turn on the power and begin winding; monitor the yarn flow and tension.
Monitor the Winding – Ensure yarn is winding evenly and smoothly across the card.
Stop the Machine – Once the desired coverage or length is reached, stop the machine.
Remove the Card – Carefully take out the wound card and trim any loose yarn ends.
Label or Store – Label for testing or sample purposes as needed.
Maintenance Tips for Card Winding Machine:
Daily:
☐ Clean yarn guides and tensioners
☐ Wipe down the machine to remove dust or lint
☐ Check for smooth yarn feeding
Weekly:
☐ Lubricate moving parts if required
☐ Inspect tension device and traverse system for wear
☐ Test speed control and motor function
Monthly:
☐ Tighten all screws, knobs, and clamps
☐ Inspect electrical parts and connections
☐ Clean internal components if accessible
Safety Tips:
☐ Keep fingers away from moving yarn and parts during operation
☐ Do not exceed machine speed limits for delicate yarns
☐ Ensure proper grounding of the machine
☐ Always power off before cleaning or adjusting settings
☐ Wear snug clothing to avoid yarn entanglement
We could make special type according to the customers request.
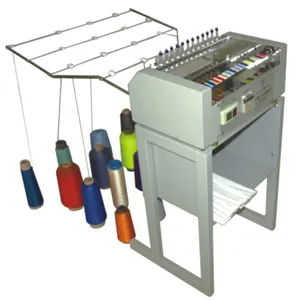
Card Winding Machine
Related products
Spray Rating Tester
Spray Rating Tester

Spray Rating Tester
- Quick and Simple Evaluation - Offers a fast way to assess fabric water repellency without complex setup.
- Standardized Testing- Complies with AATCC 22 and ISO 4920, ensuring globally accepted results.
- Cost-Effective- Low maintenance and no power requirement make it economical for routine lab use.
- Improves Fabric Performance - Helps manufacturers develop or improve water-resistant textiles.
- Non-Destructive Test - Does not damage the fabric, allowing for additional tests on the same sample.
- Visual Grading- Easy to interpret using a standard spray rating chart (0 to 100 scale).
- Supports Quality Control - Detects finish degradation or variation in water-repellent treatments.
- Portable and Compact- Lightweight design allows easy use in various lab or field settings.
- Standardized Spray Nozzle - Delivers consistent water spray per AATCC and ISO specifications.
- 45° Specimen Mounting Angle - Ensures uniform test setup for accurate and repeatable results.
- Stainless Steel or Aluminum Frame - Corrosion-resistant and durable for long-term use with water exposure.
- Water Reservoir and Funnel System - Provides precise water volume (usually 250 ml) for each test.
- Graduated Spray Stand- Fixed height (150 mm above specimen) for controlled spray impact.
- Detachable Specimen Holder- Easy loading and removal of fabric samples.
- Compact and Lightweight Design - Portable and convenient for both lab and field testing.
- No Electricity Required - Fully manual operation increases reliability and reduces operating costs.
- Prepare the Sample - Cut fabric to standard size (usually 180 × 180 mm). - Condition the sample if required (21°C, 65% RH for 24 hours).
- Mount the Fabric - Place the fabric on the specimen holder at a 45° angle.
- Fill the Reservoir - Pour 250 ml of distilled water into the upper funnel.
- Start the Test - Release the water through the nozzle; it sprays over the fabric for about 25–30 seconds.
- Inspect the Fabric - After spraying, visually assess the water beading or penetration on the surface.
- Rate the Sample - Compare the fabric’s wetting pattern with the standard spray rating chart: - 100 = No sticking/wetting - 90–50 = Partial wetting - 0 = Complete wetting
- Record the Rating - Document the spray rating for quality control or reporting.

Automatic Bobbin Hydro extractor
Automatic Bobbin Hydro extractor

Automatic Bobbin Hydro extractor
- Computer system: Foshan HuaGao Chinese English computer, equipped with LG PLC.
- Electromagnetic valve: Ningbo Jiaerling
- Frequency converter: Use Made in China frequency converters.
- Pump: self-made high head and large flow centrifugal water pump.
- Main pump motor: Anhui Wannan Motor.
- Master cylinder liquid level: Use 4-20mA analog signal output.
- Level of deputy temporary worker: use foam water level gauge. (American Mike)
- Temperature detection and display: digital temperature display instrument, dual temperature measuring probes.
- The safety system has a triple cylinder head safety interlock mechanism, and the main cylinder is equipped with a stainless
- steel safety valve.
- Heat exchanger: external spacer heating.
- Feeding system: Quantitative feeding based on the process curve.
- Circulation system: The main pump flows internally and externally, which is automatically controlled by a computer or manually controlled by a relay.
- Valves: Y valves are used for heating, stainless steel Y valves are used for single inlet and single row, and other Y valves are produced by joint ventures.
- Temperature control: on-off temperature control, controlled by a computer, with automatic heating, cooling, and insulation functions.
- Dyeing method: air cushion type.
- Opening method: manual opening.
- Surface treatment: polishing inside and outside the cylinder.
- Cage: Each dyeing machine is equipped with butterfly blades and self-locking locks.
- Body plate: high-quality stainless steel. (S31603)
- Bath ratio: 1:5-1:6
- Chemical material system: including heating and water adding functions, including overflow type salt melting device.
- Overflow cleaning: The cleaning port is installed on the upper part of the cylinder port, and the bottom of the cylinder is filled with water, while the cylinder is drained for easy cleaning.
- Commutation method: Novel "U" type commutation.
- Random accessories: Each model comes with one set of mechanical seals, pot mouth rings, and reversing seals for the main and auxiliary pumps.
Automatic Bobbin Hydro extractor
Perspiration Tester
Perspiration Tester

Perspiration Tester
- Fabric samples are treated with synthetic perspiration solution (acidic or alkaline).
- They are sandwiched with adjacent fabric and placed between glass or acrylic plates.
- The assembly is loaded into the tester and pressed under specific pressure.
- it’s then incubated at 37°C (body temperature) for a fixed time (typically 4 or 16 hours).
- Afterward, color change and staining are evaluated using a gray scale.
- Accurate Sweat Simulation - Mimics real-life effects of acidic and alkaline perspiration on fabrics.
- Improves Product Quality - Ensures textiles retain color and don’t bleed or stain when worn.
- Supports Standard Compliance - Follows ISO and AATCC test standards for global market approval.
- Protects Brand Reputation- Reduces customer complaints due to dye transfer or fading.
- Simple and Repeatable- Provides consistent pressure and conditions for reliable results.
- Multi-Sample Testing- Tests multiple specimens at once, saving time in labs.
- Durable and Low Maintenance- Robust frame with minimal moving parts makes it long-lasting and easy to care for.
- Stainless Steel Frame - Corrosion-resistant body for durability and long-term use.
- Multi-Sample Capacity - Can hold up to 20 or more specimens for batch testing.
- Standardized Loading Weight- Applies uniform pressure (usually 12.5 kPa) across all samples.
- Removable Plates - Glass or acrylic plates ensure even contact and easy cleaning.
- Compact Design- Space-saving, bench-top model ideal for lab environments.
- Complies with Test Standards - Meets ISO 105 E04, AATCC 15, and related perspiration fastness standards.
- Ease of Operation - Simple loading, unloading, and incubation process.
- High-Temperature Resistance - Can be used inside incubators at 37°C or ovens as required.
- Prepare the Test Solution - Mix artificial acidic or alkaline perspiration as per standard (ISO or AATCC).
- Cut the Fabric Samples - Cut both the test fabric and adjacent white fabric (usually cotton) to standard size.
- Soak the Samples - Immerse the fabric sandwich (test + adjacent) in the test solution for 30 minutes.
- Remove Excess Liquid - Gently squeeze or blot to remove extra moisture—do not dry.
- Load in the Tester- Place each sandwich between glass or acrylic separator plates in the tester.
- Apply Pressure - Tighten the top plate or place the standard weight on top to apply uniform pressure.
- Incubate - Keep the loaded tester in an oven or incubator at 37°C for 4–16 hours (depending on the method).
- Accurate Sweat Simulation - Mimics real-life effects of acidic and alkaline perspiration on fabrics.
- Improves Product Quality - Ensures textiles retain color and don’t bleed or stain when worn.
- Supports Standard Compliance - Follows ISO and AATCC test standards for global market approval.
- Protects Brand Reputation- Reduces customer complaints due to dye transfer or fading.
- Simple and Repeatable- Provides consistent pressure and conditions for reliable results.
- Multi-Sample Testing- Tests multiple specimens at once, saving time in labs.
- Durable and Low Maintenance- Robust frame with minimal moving parts makes it long-lasting and easy to care for.
- Dry and Evaluate - Remove, air dry the samples, then assess color change and staining using a gray scale.
- Fabric samples are treated with synthetic perspiration solution (acidic or alkaline).
- They are sandwiched with adjacent fabric and placed between glass or acrylic plates.
- The assembly is loaded into the tester and pressed under specific pressure.
- it’s then incubated at 37°C (body temperature) for a fixed time (typically 4 or 16 hours).
- Afterward, color change and staining are evaluated using a gray scale.
Perspiration Tester
Digital Yarn Twist Tester
Digital Yarn Twist Tester

Digital Yarn Twist Tester

Digital Yarn Twist Tester
Fabric Stiffness Tester
Fabric Stiffness Tester
Fabric Stiffness Tester is a lab instrument used to measure the stiffness or flexural rigidity of fabric materials. It evaluates how resistant a fabric is to bending, which influences its drape, comfort, and handling characteristics. Purpose of Fabric Stiffness Tester: To determine the stiffness of textiles by measuring the bending length and calculating flexural rigidity, often using methods like the Cantilever Test (as per ASTM D1388 or ISO 9073-7). Working Principle of Fabric Stiffness Tester: A fabric strip is slid over a horizontal platform until its free end bends under its own weight to a specific angle (usually 41.5°). The length at which this occurs is used to calculate bending length and stiffness. Main Components of Fabric Stiffness Tester: - Test Platform: Flat surface for sample movement. - Graduated Scale: Measures the overhanging length of fabric. - Angle Indicator: Guides the measurement based on standard deflection angle. - Fabric Clamp or Guide: Helps place and move the sample smoothly. Applications of Fabric Stiffness Tester: - Apparel fabrics (e.g., for comfort and drape analysis) - Technical textiles (e.g., automotive, medical fabrics) - Paper, nonwovens, and films Benefits of Fabric Stiffness Tester:- Accurate Measurement of Flexibility - Provides reliable data on fabric stiffness, essential for quality control and product development.
- Improves Product Comfort - Helps assess how soft or rigid a fabric will feel in clothing or furnishings.
- Supports Material Selection - Aids designers and engineers in choosing the right fabric for specific applications based on stiffness.
- Quality Assurance - Detects fabric inconsistencies or defects that affect handling or drape.
- Standards Compliance - Enables testing as per international standards like ASTM D1388 and ISO 9073-7 for global product approval.
- Quick and Simple Operation - Delivers fast results with minimal operator training or preparation.
- Applicable to Multiple Materials - Suitable for woven, nonwoven, knitted fabrics, paper, and films.
- Enhances R&D Accuracy - Supports consistent material testing during product innovation and textile finishing.
- Graduated Measurement Scale - Precise scale to measure overhang length for accurate stiffness calculation.
- Flat Test Platform - Smooth, level surface ensures consistent and reliable fabric movement.
- Standard Deflection Angle Guide - Built-in 41.5° angle reference for consistent stiffness testing (per ASTM/ISO).
- Manual or Motorized Models - Available in both types for simple or automated operation depending on lab needs.
- Compact Design - Space-saving unit ideal for textile labs and quality control rooms.
- Sample Holder or Clamp - Ensures correct alignment and smooth feeding of fabric strips during testing.
- Durable Construction - Made of corrosion-resistant materials like stainless steel or aluminum for long-term use.
- Compliance with Standards - Supports methods like ASTM D1388, ISO 9073-7 for stiffness testing of fabrics.
- Lightweight and Portable - Easy to move and use in various lab settings.
- Low Maintenance - Simple mechanical parts require minimal servicing.
- Prepare the Sample - Cut the fabric into a rectangular strip (e.g., 25 mm × 200 mm), as per standard.
- Place the Sample - Lay the fabric strip flat on the test platform with one end aligned at the zero mark.
- Slide the Fabric - Gently push the fabric forward so it slowly overhangs the platform.
- Watch for Deflection - Stop sliding when the free end of the fabric bends down to the reference angle (typically 41.5°).
- Read the Bending Length - Measure the overhang distance from the scale. This is the bending length (C).
- Calculate Flexural Rigidity
- Repeat for Accuracy - Test both warp and weft directions and average the results for better accuracy.

Cone yarn Dyeing machine
Cone Yarn Dyeing Machine

Cone Yarn Dyeing Machine
- Computer system: Foshan HuaGao Chinese English computer, equipped with LG PLC.
- Electromagnetic valve: Ningbo Jiaerling
- Frequency converter: Use Made in China frequency converters.
- Pump: self-made high head and large flow centrifugal water pump.
- Main pump motor: Anhui Wannan Motor.
- Master cylinder liquid level: Use 4-20mA analog signal output.
- Level of deputy temporary worker: use foam water level gauge. (American Mike)
- Temperature detection and display: digital temperature display instrument, dual temperature measuring probes.
- The safety system has a triple cylinder head safety interlock mechanism, and the main cylinder is equipped with a stainless
- steel safety valve.
- Heat exchanger: external spacer heating.
- Feeding system: Quantitative feeding based on the process curve.
- Circulation system: The main pump flows internally and externally, which is automatically controlled by a computer or manually controlled by a relay.
- Valves: Y valves are used for heating, stainless steel Y valves are used for single inlet and single row, and other Y valves are produced by joint ventures.
- Temperature control: on-off temperature control, controlled by a computer, with automatic heating, cooling, and insulation functions.
- Dyeing method: air cushion type.
- Opening method: manual opening.
- Surface treatment: polishing inside and outside the cylinder.
- Cage: Each dyeing machine is equipped with butterfly blades and self-locking locks.
- Body plate: high-quality stainless steel. (S31603)
- Bath ratio: 1:5-1:6
- Chemical material system: including heating and water adding functions, including overflow type salt melting device.
- Overflow cleaning: The cleaning port is installed on the upper part of the cylinder port, and the bottom of the cylinder is filled with water, while the cylinder is drained for easy cleaning.
- Commutation method: Novel "U" type commutation.
- Random accessories: Each model comes with one set of mechanical seals, pot mouth rings, and reversing seals for the main and auxiliary pumps.
Steam Soaping machine
Steam Soaping Machine
A Steam Soaping Machine is a specialized laboratory apparatus used in textile dyeing processes, particularly for post-dyeing treatments like soaping, which enhances color fastness and removes unfixed dyes from fabric samples. This machine is designed to perform soaping treatments on dyed textile samples using steam. Soaping is a critical step in dyeing, especially for reactive dyes, as it removes unfixed dye particles, ensuring better color fastness and preventing dye bleeding. The steam soaping process involves treating the dyed fabric with a soaping solution at elevated temperatures, facilitated by steam, to achieve optimal results. ⚙️ Key Features of Steam Soaping Machine - Beaker Material: Constructed with high-grade 316L stainless steel for excellent corrosion resistance and durability.- Operation Modes: Offers both automatic control and manual water filling options, providing flexibility in operation. - Drainage System: Equipped with an automatic drainage device for efficient removal of used solutions.- Temperature Control: Precise temperature regulation to maintain optimal soaping conditions.- Compact Design: Suitable for laboratory settings, occupying minimal space while delivering effective performance. ✅ Benefits of Steam Soaping Machine - Enhanced Color Fastness: Effectively removes unfixed dyes, resulting in improved wash and rub fastness of the fabric.- Efficient Processing: Reduces the time required for post-dyeing treatments compared to conventional methods.- Consistent Results: Provides uniform treatment across samples, ensuring reproducibility in testing and quality control.- Resource Optimization: Minimizes water and chemical usage through controlled processing parameters.- Versatility: Applicable to various fabric types and dye classes, making it a valuable tool in research and development. Typical Applications - Laboratory Testing: Used in dyeing laboratories for evaluating the fastness properties of dyed samples. - Research and Development: Assists in developing and optimizing dyeing processes and formulations. - Quality Control: Ensures that dyed fabrics meet specified fastness standards before bulk production. In summary, a Steam Soaping Machine is an essential laboratory instrument in the textile industry, facilitating efficient and effective post-dyeing treatments to enhance the quality and durability of dyed fabrics. Features of Steam Soaping Machine:- High-Grade Stainless Steel Beakers - Made from 316L stainless steel for excellent chemical and heat resistance.
- Steam-Based Heating - Uses direct or indirect steam to maintain consistent high temperatures ideal for soaping.
- Precise Temperature Control - Maintains stable temperatures (typically up to 98–100°C) for effective removal of unfixed dyes.
- Automatic and Manual Modes - Offers both programmable automatic cycles and manual operation for flexibility.
- Beaker Agitation or Rotation - Ensures uniform soaping action across fabric surfaces.
- Automatic Drainage System - Efficiently removes used soaping solution to speed up cycle changeovers.
- Compact Design - Fits well in lab settings while allowing multiple samples to be processed simultaneously.
- Safety Features - Includes pressure and temperature protection systems to ensure safe operation.
- Low Water and Chemical Use - Designed for minimal liquor ratios, enhancing sustainability.
- User-Friendly Interface - Simple digital controls or touch panel for easy operation and cycle programming.
- Prepare the Dyed Sample - After dyeing, rinse the fabric to remove surface dye and prepare it for soaping.
- Load the Fabric - Place the dyed fabric or sample into the beakers or holders inside the machine.
- Add Soaping Solution - Pour the prepared soaping agent (usually a detergent solution) into the beakers or tank as per recipe.
- Set Parameters
- Start the Cycle - Begin the soaping process. The machine will heat the solution using steam and agitate/rotate the beakers for even treatment.
- Drain and Rinse - After the cycle ends, the machine may auto-drain. Rinse the fabric with warm water to remove residual chemicals.
- Unload the Samples - Carefully remove the fabric. Inspect for evenness and color fastness improvement.
- Clean the Machine - Rinse and dry the beakers or tank to maintain hygiene for the next use.

Thread Cone Winding Machine
Thread Cone Winding Machine

Thread Cone Winding Machine
- Efficient Yarn Packaging - Speeds up the process of preparing thread for sewing or embroidery.
- Uniform Cone Formation - Ensures consistent cone shape and tension for smooth downstream use.
- Reduces Thread Breakage - Controlled tension and smooth guiding minimize thread damage.
- Time & Labor saving- Automates winding, reducing manual effort and increasing productivity.
- Improves Thread Quality - Removes loose fibers and irregularities during winding.
- Supports Multiple Yarn Types - Compatible with cotton, polyester, silk, and blended threads.
- Adjustable Winding Speed - Variable speed control for different thread types.
- Thread Tension Control System - Maintains consistent tension for smooth winding.
- Auto Stop Mechanism - Stops automatically when cone is full or thread breaks.
- Multiple Spindle Options - Single or multi-spindle designs for higher output.
- Traverse Mechanism - Ensures even layering of thread across the cone.
- Compact & Durable Build - Space-saving, long-lasting structure for industrial use.
- Set Up the Machine - Turn on the power and check all safety covers and switches.
- Load the Yarn Source - Place the yarn hank, bobbin, or spool on the supply holder.
- Mount the Empty Cone - Fix an empty cone securely onto the spindle.
- Thread the Machine - Guide the thread through tension disks, guides, and eyelets as per the machine path.
- Adjust Settings - Set the desired winding speed and tension based on thread type.
- Start the Machine - Press the start button; the thread begins winding onto the cone.
- Monitor the Process - Ensure even winding and tension; adjust traverse if needed.
- Auto-Stop or Manual Stop - The machine will stop automatically if the cone is full or thread breaks.
- Remove the Cone - Carefully remove the finished cone and load a new one if needed.
- Clean and Shut Down - Turn off the machine and clean any thread residue after use.
- Always Use Safety Guards - Ensure all protective covers are in place before operation.
- Avoid Loose Clothing - Prevent thread or moving parts from catching clothes or jewelry.
- Power Off Before Maintenance - Always turn off the machine before threading, cleaning, or adjustments.
- Check Thread Path - Use correct threading to prevent sudden breakage or tangling.
- Don’t Overload the Cone - Stop the machine once the cone is adequately filled to avoid jamming.
- Keep Area Clean - Remove lint and thread waste regularly to prevent fire hazards or machine faults.
- Daily Cleaning - Wipe dust and thread particles from guides, spindles, and tension parts.
- Lubrication - Oil moving parts (as per manual) weekly to reduce wear.
- Check Tension Settings - Inspect and calibrate tension mechanisms for consistent winding.
- Inspect Belts and Motors - Look for wear or looseness in drive belts and check motor sound regularly.
- Replace Worn Parts Promptly - Replace traverse mechanisms, springs, or tension disks if worn out.

Thread Cone Winding Machine