Laboratory mini stenter Dryer
$0.00
Laboratory mini stenter Dryer
A Laboratory Mini Stenter Dryer is a compact, lab-scale machine designed to simulate the drying and heat-setting processes used in textile finishing. It mimics the function of industrial stenter machines but on a much smaller scale, making it ideal for testing fabric behavior, shrinkage, and finish quality under controlled conditions.
Key Features:
- Controlled Heating System
– Typically uses electric heating with adjustable temperature (up to 220–250°C).
– Ensures uniform and precise temperature control.
- Adjustable Fabric Width
– Equipped with clips or pins to hold and stretch fabric width-wise, simulating stenter frame action.
- Variable Speed Conveyor – Allows control over fabric dwell time for drying or heat-setting.
- Compact and Bench-Top Design – Space-saving design ideal for textile labs and R&D units.
- Digital Controls – Easy-to-use digital interface for setting temperature, conveyor speed, and process time.
- Transparent Viewing Window – Allows operators to monitor fabric movement and drying visually.
- Low Energy Consumption – Designed for lab use, consuming less power than industrial models.
Applications:
– Heat-setting of synthetic fabrics. Drying and curing of samples post-dyeing or printing.
– Evaluating fabric shrinkage, dimensional stability, and finish behavior.
– Testing chemicals and auxiliaries used in textile finishing.
Benefits of Laboratory Mini Stenter Dryer:
- Accurate Simulation of Production – Mimics industrial stenter conditions on a lab scale, ideal for pre-production testing and R&D.
- Cost-Effective Testing – Enables testing and fabric finishing without the high cost or space requirements of full-scale machines.
- Energy Efficient – Consumes less power compared to large stenters, making it economical for small-scale or frequent use.
- Precise Control – Offers accurate control of temperature, speed, and fabric tension, ensuring consistent results.
- Space-Saving Design – Compact and bench-top friendly, perfect for laboratories with limited space.
- Multiple Applications – Useful for drying, heat-setting, shrinkage testing, and evaluating chemical finishes.
- Faster Development Cycles – Speeds up new product development by allowing rapid sample testing and adjustments.
- Improved Fabric Quality – Helps optimize finishing parameters for better dimensional stability, hand feel, and appearance.
- Safe and User-Friendly- Designed with lab safety in mind, including temperature safety controls and easy operation.
Features of Laboratory Mini Stenter Dryer:
- Compact Bench-Top Design – Ideal for laboratory use with limited space requirements.
- Adjustable Temperature Control – Precise heating (usually up to 220–250°C) with digital controllers for accurate processing.
- Variable Conveyor Speed- Allows adjustment of fabric dwell time for different drying or heat-setting needs.
- Width Adjustment Mechanism – Equipped with clips or pins to stretch and fix fabric width-wise, simulating industrial stenter conditions.
- Transparent Viewing Window – Enables visual monitoring of fabric movement and drying inside the chamber.
- Digital Display Panel- Easy-to-use interface for setting and monitoring temperature, speed, and time.
- Stainless Steel Construction- Durable and corrosion-resistant for long-term use at high temperatures.
- Uniform Heat Distribution- Ensures consistent fabric treatment across the width.
- Safety Features- Over-temperature protection and insulated body for operator safety.
- Versatile Applications – Suitable for drying, heat-setting, shrinkage testing, and chemical finish evaluations.
Laboratory Mini Stenter Dryer dealer In Bangladesh,
Lab Mini Stenter Dryer Importer in Bangladesh,
Mini Stenter Dryer in Bangladesh,
Laboratory Stenter Dryer in Bd,
Lab Stenter Dryer In Uttara,
Lab Stenter Price in Bangladesh,
Laboratory Stenter Dryer in Bangladesh,
Laboratory Mini Dryer in Bangladesh,
Automatic fixing dryer
Application:
used for simulating the production onsite to produce the textile that meets customer requirement,
including the time、temperature、resin auxiliary agent formula, elongation of the same textile, and
it is also can provide basis manufacture and to ensure the correctness of mass production.
Basic design as Automatic Fixing Dryer,also connect external steam for printing sample
steaming. Owing the wide adjusting ranges regarding temperature, humidity, dwelling time, this
apparatus can be used for :
a) Electric heating for drying, curing and thermofixation, room temp.~230℃.
b) Steaming with saturated steam 102±2℃
c) Electric heating and steam together for HT steaming between 102±230℃
Textile Testing Instruments
Automatic Fixing Dryer dealer In Bangladesh,
Automatic Fixing Dryer Importer in Bangladesh,
Automatic Fixing Dryer in Bangladesh,
Automatic Fixing Dryer in Bd,
Automatic Fixing Dryer In Uttara,
Automatic Fixing Dryer Price in Bangladesh,
Automatic Fixing Dryer Supplier in Bangladesh,
Lab Dryer Machine in Bangladesh,
Rapid Dryer Mini Stanter in Bangladesh
Related products
Oscillation type water bath Dyeing Machine
Oscillation Type Water Bath Dyeing Machine
An Oscillation Type Water Bath Dyeing Machine is a laboratory apparatus designed for dyeing and washing textile samples under controlled temperature conditions. It combines a heated water bath with an oscillating mechanism to ensure uniform dye penetration and consistent coloration across fabric or yarn samples. Key Features of Oscillation Type Water Bath Dyeing Machine - Oscillating Mechanism: Provides back-and-forth movement to agitate the dye solution, ensuring even contact between the dye and the textile sample.- Multiple Beaker Capacity: Typically accommodates 12 to 24 beakers, allowing simultaneous processing of multiple samples under identical or varied conditions. - Digital Temperature Control: Maintains precise temperature settings, usually up to 99°C, suitable for various dyeing processes including atmospheric dyeing, scouring, and bleaching.- Adjustable Oscillation Speed: Offers variable speed settings, commonly ranging from 50 to 200 cycles per minute, to accommodate different fabric types and dyeing requirements. - Programmable Settings: Advanced models come with programmable controllers, allowing users to set and save multiple dyeing protocols for repeatability and efficiency. Durable Construction: Constructed with high-quality stainless steel (e.g., SUS304), ensuring resistance to corrosion and longevity even under rigorous laboratory conditions. ✅ Benefits of Oscillation Type Water Bath Dyeing Machine - Uniform Dyeing Results: The oscillation mechanism ensures consistent dye penetration, reducing the risk of uneven coloration and enhancing the reproducibility of results.- Efficiency in Sample Processing: The ability to process multiple samples simultaneously accelerates laboratory workflows and facilitates comparative studies. - Versatility: Suitable for a range of applications including dyeing, washing, scouring, bleaching, and fastness testing across various textile materials.- Energy and Resource Conservation: Designed for low liquor ratios (e.g., 1:5 to 1:20), these machines minimize water and chemical usage, promoting sustainable laboratory practices. - Enhanced Safety and Cleanliness: Enclosed beaker systems reduce the risk of spills and exposure to chemicals, ensuring a safer laboratory environment. Typical Applications of Oscillation Type Water Bath Dyeing Machine - Textile Research and Development: Ideal for developing and testing new dye formulations and processes on a small scale before scaling up to production levels. Quality Control: Used in quality assurance laboratories to assess color fastness, dye uptake, and other critical parameters of textile products.- Educational Purposes: Serves as a practical tool in academic settings for teaching dyeing principles and techniques. In summary, the Oscillation Type Water Bath Dyeing Machine is an essential tool in textile laboratories, offering precise control over dyeing parameters, improving efficiency, and ensuring high-quality, reproducible results across various textile materials. Features of Oscillation Type Water Bath Dyeing Machine:- Oscillating Mechanism - Provides back-and-forth movement of beakers for uniform dye penetration and sample agitation.
- Multiple Beaker Capacity - Supports dyeing of 12–24 samples simultaneously, ideal for comparative lab testing.
- Digital Temperature Control - Maintains precise water bath temperature (typically up to 99°C), essential for consistent dyeing.
- Variable Oscillation Speed - Adjustable speed settings (e.g., 50–200 cycles/min) to suit different materials and processes.
- Programmable Settings - Allows setting of temperature, time, and speed for repeatable and automated dyeing cycles.
- Stainless Steel Construction - Corrosion-resistant frame and bath for durability in chemical environments.
- Beaker Safety Holders - Secure placement of beakers to prevent spills and maintain consistent treatment.
- Compact Design - Lab-friendly size for easy integration into research and quality control spaces.
- Low Liquor Ratio Operation - Efficient dyeing using minimal dye bath volume (e.g., 1:5 to 1:20), reducing chemical and water use.
- Quiet and Stable Performance

water bath/Shaker bath Dyeing machine
Steam Soaping machine
Steam Soaping Machine
A Steam Soaping Machine is a specialized laboratory apparatus used in textile dyeing processes, particularly for post-dyeing treatments like soaping, which enhances color fastness and removes unfixed dyes from fabric samples. This machine is designed to perform soaping treatments on dyed textile samples using steam. Soaping is a critical step in dyeing, especially for reactive dyes, as it removes unfixed dye particles, ensuring better color fastness and preventing dye bleeding. The steam soaping process involves treating the dyed fabric with a soaping solution at elevated temperatures, facilitated by steam, to achieve optimal results. ⚙️ Key Features of Steam Soaping Machine - Beaker Material: Constructed with high-grade 316L stainless steel for excellent corrosion resistance and durability.- Operation Modes: Offers both automatic control and manual water filling options, providing flexibility in operation. - Drainage System: Equipped with an automatic drainage device for efficient removal of used solutions.- Temperature Control: Precise temperature regulation to maintain optimal soaping conditions.- Compact Design: Suitable for laboratory settings, occupying minimal space while delivering effective performance. ✅ Benefits of Steam Soaping Machine - Enhanced Color Fastness: Effectively removes unfixed dyes, resulting in improved wash and rub fastness of the fabric.- Efficient Processing: Reduces the time required for post-dyeing treatments compared to conventional methods.- Consistent Results: Provides uniform treatment across samples, ensuring reproducibility in testing and quality control.- Resource Optimization: Minimizes water and chemical usage through controlled processing parameters.- Versatility: Applicable to various fabric types and dye classes, making it a valuable tool in research and development. Typical Applications - Laboratory Testing: Used in dyeing laboratories for evaluating the fastness properties of dyed samples. - Research and Development: Assists in developing and optimizing dyeing processes and formulations. - Quality Control: Ensures that dyed fabrics meet specified fastness standards before bulk production. In summary, a Steam Soaping Machine is an essential laboratory instrument in the textile industry, facilitating efficient and effective post-dyeing treatments to enhance the quality and durability of dyed fabrics. Features of Steam Soaping Machine:- High-Grade Stainless Steel Beakers - Made from 316L stainless steel for excellent chemical and heat resistance.
- Steam-Based Heating - Uses direct or indirect steam to maintain consistent high temperatures ideal for soaping.
- Precise Temperature Control - Maintains stable temperatures (typically up to 98–100°C) for effective removal of unfixed dyes.
- Automatic and Manual Modes - Offers both programmable automatic cycles and manual operation for flexibility.
- Beaker Agitation or Rotation - Ensures uniform soaping action across fabric surfaces.
- Automatic Drainage System - Efficiently removes used soaping solution to speed up cycle changeovers.
- Compact Design - Fits well in lab settings while allowing multiple samples to be processed simultaneously.
- Safety Features - Includes pressure and temperature protection systems to ensure safe operation.
- Low Water and Chemical Use - Designed for minimal liquor ratios, enhancing sustainability.
- User-Friendly Interface - Simple digital controls or touch panel for easy operation and cycle programming.
- Prepare the Dyed Sample - After dyeing, rinse the fabric to remove surface dye and prepare it for soaping.
- Load the Fabric - Place the dyed fabric or sample into the beakers or holders inside the machine.
- Add Soaping Solution - Pour the prepared soaping agent (usually a detergent solution) into the beakers or tank as per recipe.
- Set Parameters
- Start the Cycle - Begin the soaping process. The machine will heat the solution using steam and agitate/rotate the beakers for even treatment.
- Drain and Rinse - After the cycle ends, the machine may auto-drain. Rinse the fabric with warm water to remove residual chemicals.
- Unload the Samples - Carefully remove the fabric. Inspect for evenness and color fastness improvement.
- Clean the Machine - Rinse and dry the beakers or tank to maintain hygiene for the next use.

Xenon Arc Light Fastness Tester
Hydraulic GSM Cutter
Hydraulic GSM Cutter
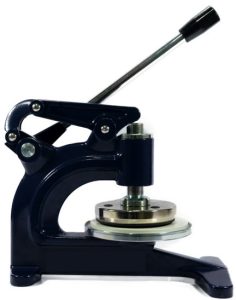
Hydraulic GSM Cutter
- High Cutting Precision - Ensures consistent and accurate fabric sample size for reliable GSM results.
- Effortless Operation- Hydraulic action reduces manual effort and operator fatigue.
- Ideal for Thick or Multi-Layer Fabrics - Cuts through dense or multiple fabric layers cleanly.
- Time-Saving - Speeds up the sample preparation process, especially for high-volume testing.
- Improves Test Accuracy - Uniform samples help eliminate errors in GSM calculation.
- Durable and Long-Lasting - Robust construction ensures stability and extended service life.
- Safety Enhancement - Reduces risk of injury compared to manual rotary cutters.
- Consistent Pressure Application - Hydraulic mechanism maintains steady force for each cut.
- Hydraulic Press Mechanism - Applies consistent and strong pressure for clean, even cuts.
- Standard Cutting Die (100 cm²) - Produces fabric samples suitable for GSM testing with standard area.
- Heavy-Duty Construction - Built with robust metal frame for long-term lab or industrial use.
- Sharp Stainless Steel Blades - Durable and replaceable blades ensure smooth, precise cuts.
- Cutting Pad Included - Comes with a rubber or nylon base to protect blades and ensure clean edges.
- Simple Lever or Button Operation - Easy to use with minimal training required.
- Non-slip Base - Provides stability during operation for safe, accurate cutting.
- Supports Various Fabric Types
- Place the Cutting Pad - Lay the rubber or nylon cutting pad on a flat surface.
- Position the Fabric - Place the fabric sample flat and smooth on the cutting pad.
- Align the Cutter - Position the GSM cutter die over the desired area of the fabric.
- Activate Hydraulic Press - Pull the lever or press the button to apply hydraulic pressure and cut the sample.
- Remove the Sample - Lift the cutter and carefully take out the circular fabric piece (usually 100 cm²).
- Weigh the Sample - Place the cut sample on a precision balance or GSM scale to determine weight.
- Calculate GSM - Multiply the sample weight (in grams) by 100 to get GSM.
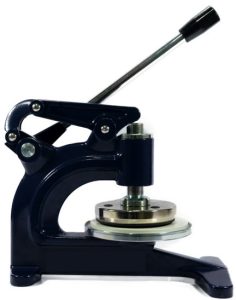
Hydraulic GSM Cutter
Laboratory Padder
Laboratory Padder
A Laboratory Padder is a compact, laboratory-scale machine used to apply liquids like dyes, chemicals, and finishes to fabric samples. It simulates the padding process in textile manufacturing, where fabric is passed through a liquid solution, then squeezed between rollers to ensure uniform application and absorption. Key Features of a Laboratory Padder:- Adjustable Rollers - The fabric is passed through two or more rollers to apply even pressure and squeeze out excess solution, ensuring uniform chemical or dye application.
- Variable Pressure Control - Allows adjustment of roller pressure for different fabric types and chemical formulations, ensuring optimal penetration without damage.
- Solution Bath - Holds the liquid (e.g., dye, finish, or other chemical treatments) in a bath through which the fabric is dipped before passing through the rollers.
- Fabric Speed Control - Adjustable conveyor speed allows for control over the time the fabric spends in contact with the liquid solution, affecting the degree of treatment.
- Digital Control Panel - Provides easy adjustment of pressure, speed, and solution volume to ensure precise and reproducible results.
- Compact Design - Smaller, lab-scale version of industrial padders, ideal for research, development, and small-scale testing.
- Safety Features - Safety guards, emergency stops, and proper handling mechanisms to prevent accidents during operation.
- Precise Application of Chemicals - Provides uniform and controlled application of dyes, finishes, and other chemicals, ensuring consistent results.
- Small-Scale Testing - Ideal for small sample testing, allowing for fabric treatment without needing full-scale production equipment.
- Versatile Use - Suitable for dyeing, finishing, and applying various chemical treatments, making it a flexible tool for R&D labs.
- Cost-Effective - Reduces the need for large-scale machinery and the associated costs, while providing reliable results for small batches.
- Controlled Fabric Treatment - Offers adjustable pressure, speed, and solution concentration, enabling fine-tuned processing for different fabric types and applications.
- Accelerates Development - Speeds up the testing and development of new products or finishes, improving time-to-market for textile manufacturers.
- Energy Efficient - Consumes less energy compared to larger, industrial-scale machines, making it suitable for lab use.
- Compact and Space-Saving - Designed for laboratory environments with limited space, without compromising on functionality.
- Reproducible Results - Ensures consistent application of treatments across multiple samples, aiding in accurate testing and comparison.
- Adjustable Roller Pressure - Allows precise control over the pressure applied to the fabric, ensuring uniform chemical or dye application.
- Variable Speed Control - Adjustable conveyor speed for controlling the time the fabric spends in the solution bath, influencing the absorption rate.
- Solution Bath - Holds dye, chemicals, or finishes, and the fabric passes through this bath before moving to the rollers.
- Digital Control Panel - Easy-to-use interface for setting and adjusting parameters like speed, pressure, and solution concentration.
- Compact and Lab-Friendly Design - Designed for smaller, space-efficient use in textile labs, allowing for small sample testing.
- Roller Gap Adjustment - Allows for fine-tuning of the gap between rollers to regulate the amount of solution squeezed out of the fabric.
- Stainless Steel Construction - Durable and resistant to corrosion from the chemicals used in textile treatments.
- Safety Mechanisms - Includes safety guards, emergency stops, and user protection features during operation.
- Even and Controlled Application - Ensures even distribution of treatments (dye, finish, etc.) on fabric with minimal waste.
- Versatility in Application - Can be used for a wide range of textiles and treatments, including dyeing, softening, flame-retardant treatments, etc.
- Prepare the Fabric Sample - Cut the fabric sample to the required size for the experiment. Ensure it’s clean and free of any debris.
- Prepare the Solution - Mix the dye, chemical, or finish solution according to the desired concentration and the fabric's needs. Ensure that the solution is homogeneous.
- Set the Parameters - Pressure: Adjust the roller pressure based on the fabric type. Different fabrics require different pressure levels to ensure uniform application. - Speed: Set the fabric conveyor speed depending on the desired treatment time (longer exposure for deeper treatment).
- Load the Fabric into the Machine - Place the fabric carefully into the machine. The fabric should go through the solution bath and then pass between the rollers.
- Start the Machine - Turn on the machine and allow the fabric to pass through the rollers. The solution will be evenly applied to the fabric as it moves through the bath and is squeezed by the rollers.
- Monitor the Process - Keep an eye on the fabric to ensure it is being treated uniformly and there are no blockages or fabric jams.
- Unload the Fabric - Once the fabric has been treated, carefully remove it from the machine. Inspect for even application of the solution and any excess liquid.
- Dry or Process Further - Depending on the treatment, proceed with further steps such as drying, heat setting, or curing, as required by the experiment or process.

Mini Lab Dyeing Padder
Bursting strength tester
Bursting strength tester

true burst
- Available with automatic test strip feeder Measurements are simple to make with the Mullen type Bursting Strength Tester. Fast automatic measurements Measurement starts automatically once a test piece has been placed in the measuring gap. The clamping foot descends, and a bursting strength measurement is made.
- Bursting pressure can reach up to 1.2MPa 5. The maximum burst and expansion degree can reach 70mm. 6. Strengthen the lighting system on the test surface. 7. The main aerodynamic force helps to clamp the sample system. 8. A variety of test areas are available, and the switching is easy.
- A variety of unit conversions between Chinese and English. 10. Reliable anti-pinch safety protection design. [Technical parameter]: 1. Test range: (0~1)Mpa (the range above 1Mpa needs to be customized) 2. The minimum graduation value: 0.0001Mpa 3. Pressurization mode: direct pressurization, timing pressurization, and expansion degree pressurization.
fabric moisture permeability tester
Fabric Moisture Permeability Tester
A Fabric Moisture Permeability Tester, also known as a Water Vapor Permeability Tester, is a laboratory instrument designed to measure the rate at which water vapor passes through textile materials. This measurement is crucial for assessing the breathability and comfort of fabrics, especially those used in active wear, outdoor gear, medical textiles, and protective clothing. Purpose of Fabric Moisture Permeability Tester The primary function of this tester is to evaluate a fabric's ability to allow moisture vapor to pass through it, which directly impacts the wearer's comfort by facilitating sweat evaporation and thermal regulation. High moisture permeability indicates better breathability, making the fabric suitable for applications where moisture management is essential. Working Principle of Fabric Moisture Permeability Tester The tester operates by placing a fabric specimen over a container filled with water. Under controlled temperature and humidity conditions, water vapor passes through the fabric over a specified period. The amount of water vapor transmitted is determined by measuring the weight loss of the container, allowing for the calculation of the Water Vapor Transmission Rate (WVTR). Common Testing Methods- Upright Cup Method: The fabric covers a cup containing water, and the assembly is placed upright in a controlled environment. After a set duration, the weight loss is measured to determine the WVTR.
- Inverted Cup Method: The fabric is sealed over a cup, which is then inverted and exposed to a controlled environment. The amount of water vapor absorbed by the fabric is measured over time.
- Sweating Hot Plate Test: Simulates human perspiration by measuring the energy required to maintain a constant temperature on a heated plate covered with the fabric, providing insights into the fabric's breathability.
- Multi-Cup Design - Typically includes 6 or more test cups for simultaneous testing of multiple samples.
- Rotating Turntable - Ensures uniform air exposure and consistent vapor transmission across all samples.
- Precision Weighing System- Accurate measurement of weight loss to calculate water vapor transmission rate (WVTR).
- Temperature & Humidity Control - Maintains stable environmental conditions (e.g., 23°C, 50% RH) for reliable results.
- Digital Display or Software Interface - Displays real-time data and test status; advanced models offer data logging and export.
- Compliance with Standards - Supports ASTM E96, ISO 15496, BS 7209, JIS L1099 testing methods.
- Sealed Test Chambers- Prevents external air interference, improving accuracy.
- Corrosion-Resistant Construction - Durable materials suitable for long-term use in lab environments.
- Easy Sample Mounting - Quick and secure fabric placement on test cups with sealing rings.
- Low Maintenance Design- Simplified components for easy cleaning and upkeep.
- Prepare the Test Solution - Fill each test cup with a set amount of water (e.g., 50 ml), or a desiccant if using inverted method.
- Mount the Fabric - Cut the fabric into circular pieces matching the cup size.
- Weigh the Cups - Record the initial weight of each cup with the fabric mounted.
- Place on Turntable - Position all cups on the rotating tray inside the controlled chamber.
- Set Conditions - Close the chamber and maintain temperature (e.g., 23°C) and relative humidity (e.g., 50%) as per test standard.
- Start the Test - Begin rotation (usually ~2 RPM) and let it run for the specified time (often 24 hours).
- Weigh the Cups Again- After the test duration, reweigh the cups to determine weight loss due to moisture vapor passing through the fabric.
- Calculate WVTR - Use the formula: WVTR = (Weight Loss in grams × 24) / (Test Area in m² × Time in hours) Expressed in g/m²/24h.
- Clean and Store - Clean cups and components for future use.

Spray Rating Tester
Spray Rating Tester

Spray Rating Tester
- Quick and Simple Evaluation - Offers a fast way to assess fabric water repellency without complex setup.
- Standardized Testing- Complies with AATCC 22 and ISO 4920, ensuring globally accepted results.
- Cost-Effective- Low maintenance and no power requirement make it economical for routine lab use.
- Improves Fabric Performance - Helps manufacturers develop or improve water-resistant textiles.
- Non-Destructive Test - Does not damage the fabric, allowing for additional tests on the same sample.
- Visual Grading- Easy to interpret using a standard spray rating chart (0 to 100 scale).
- Supports Quality Control - Detects finish degradation or variation in water-repellent treatments.
- Portable and Compact- Lightweight design allows easy use in various lab or field settings.
- Standardized Spray Nozzle - Delivers consistent water spray per AATCC and ISO specifications.
- 45° Specimen Mounting Angle - Ensures uniform test setup for accurate and repeatable results.
- Stainless Steel or Aluminum Frame - Corrosion-resistant and durable for long-term use with water exposure.
- Water Reservoir and Funnel System - Provides precise water volume (usually 250 ml) for each test.
- Graduated Spray Stand- Fixed height (150 mm above specimen) for controlled spray impact.
- Detachable Specimen Holder- Easy loading and removal of fabric samples.
- Compact and Lightweight Design - Portable and convenient for both lab and field testing.
- No Electricity Required - Fully manual operation increases reliability and reduces operating costs.
- Prepare the Sample - Cut fabric to standard size (usually 180 × 180 mm). - Condition the sample if required (21°C, 65% RH for 24 hours).
- Mount the Fabric - Place the fabric on the specimen holder at a 45° angle.
- Fill the Reservoir - Pour 250 ml of distilled water into the upper funnel.
- Start the Test - Release the water through the nozzle; it sprays over the fabric for about 25–30 seconds.
- Inspect the Fabric - After spraying, visually assess the water beading or penetration on the surface.
- Rate the Sample - Compare the fabric’s wetting pattern with the standard spray rating chart: - 100 = No sticking/wetting - 90–50 = Partial wetting - 0 = Complete wetting
- Record the Rating - Document the spray rating for quality control or reporting.
