High speed hard winding machine
$0.00
High Speed Hard Winding Machine

High Speed Hard Winding Machine
A High Speed Hard Winding Machine is a textile winding machine designed to wind yarns, threads, or fibers onto cones or packages at high speeds with firm tension. It is used to prepare yarn packages for subsequent processes like weaving or knitting.
Purpose of High Speed Hard Winding Machine:
– To wind yarn evenly and tightly with controlled tension for storage or further processing.
Key Features of High Speed Hard Winding Machine
– High-speed winding for increased productivity.
– Precise tension control to avoid yarn breakage or slack.
– Automatic package building to maintain uniform shape.
– Suitable for various yarn types—cotton, polyester, wool, etc.
– User-friendly controls and safety features.
Applications of High Speed Hard Winding Machine:
– Textile mills preparing yarn for fabric production.
– Quality control labs for winding test samples.
– Textile manufacturing units needing uniform yarn packages.
Benefits of High Speed Hard Winding Machine:
- Increased Productivity – High-speed operation reduces winding time significantly.
- Consistent Package Quality – Ensures uniform and firm yarn packages ideal for further processing.
- Reduced Yarn Breakage – Precise tension control minimizes yarn damage during winding.
- Versatility – Handles different types of yarns including delicate and coarse fibers.
- User-Friendly Operation – Simple controls and automation reduce operator fatigue.
- Improved Efficiency – Automatic package build-up reduces manual adjustments.
- Space Saving – Compact design fits well in production lines and labs.
How to Use High Speed Hard Winding Machine:
- Set Up the Machine – Switch on the power and check all safety guards.
- Load Yarn – Thread the yarn through tension guides and eyelets as per the manual.
- Adjust Tension – Set tension according to yarn type to avoid slack or breakage.
- Place Empty Cone/Package – Mount the empty cone or package holder securely.
- Start Winding- Press the start button; machine will begin winding at set speed.
- Monitor the Process – Observe yarn package build-up and make adjustments if necessary.
- Stop and Remove Package – Once winding is complete, stop the machine and remove the yarn package carefully.
- Maintenance – Clean the machine regularly and lubricate moving parts as needed.
Specifications of High Speed Hard Winding Machine:
– Winding Speed: Typically 1000 to 3000 RPM (varies by model)
– Package Type: Conical or cylindrical yarn packages
– Tension Control: Adjustable mechanical or electronic tension system
– Drive System: AC motor with variable frequency drive (VFD) for speed control
– Power Supply: Usually 220V/380V, 50/60 Hz
– Package Weight Capacity: Depends on model, generally up to 2 kg
– Machine Size: Compact footprint for space-saving installation
– Control Panel: Digital or analog with start/stop and speed adjustment
– Safety Features: Emergency stop, yarn break detection, overload protection
Troubleshooting Tips:
– Yarn Breakage:
– Check and reduce tension; inspect yarn for weak spots.
– Clean guides and rollers to remove any debris.
– Uneven Winding:
– Ensure correct threading path and tension balance.
– Adjust package build-up mechanism.
– Machine Not Starting:
– Check power supply and emergency stop switch.
– Verify control panel settings.
– Excessive Noise:
– Lubricate moving parts and tighten loose components.
– Inspect bearings for wear.
– Package Slippage:
– Secure cone properly and check tension settings.
Features of High Speed Hard Winding Machine:
- High-Speed Operation – Capable of winding yarns at fast speeds (up to 3000 RPM) to boost productivity.
- Precise Tension Control – Adjustable tension mechanism to prevent yarn breakage and ensure tight winding.
- Automatic Package Formation – Uniform, firm package build-up for consistent yarn quality.
- Versatile Yarn Compatibility – Suitable for cotton, polyester, wool, and blended yarns.
- User-Friendly Interface – Easy controls with digital or analog panels for speed and tension adjustment.
- Robust Construction – Durable stainless steel or metal frame for long-term reliability.
- Safety Features – Includes emergency stop buttons and yarn break sensors.
- Compact Design – Space-saving structure ideal for labs and production floors.
- Low Maintenance – Designed for easy cleaning and minimal upkeep.
high-speed hard winding machine is used to produce hard cone packages for knitting machine,
shuttle loom, warping machine and hosiery machine. It is an ideal winding machine for cotton threads,
hemp threads and chemical fiber yarns.
TECHNICAL PARAMETERS
Grooved drum O/D 82mm, lead 2.5 (turns) ×147, angle: 0°
Take-up tubes Cylindrical or cone with conicity of 3°30′, 4 °20′
Bobbin length Standard 170mm, customized range: 170-280mm
Yarn length control Electronically set the winding yarn length up to 999999m according to the final package.
Electric waxing device (optional) Square wax piece is used for uniform waxing, a set per spindle
Slow start Ensures a slow and stable start to improve the winding quality.
Counterweight yarn brake Prevent the yarn from shaking during the feeding to provide suitable winding tension.
Electronic tensioner Tension plate
Number of spindles per section 12 per section
Number of spindles, max. 120
Drive Individual variable frequency motor per spindle
Max. winding linear speed 1100 m/min, individually controlled per section, frequency control
Traverse Standard: 147mm
Creel balancer Winding tension is controlled by a spring balancer
Yarn detector Photoelectric sensor
Package diameter Max. 280mm
Start/Stop Membrane switch control, touch screen
Vertical anti-patterning device Computer controlled
Vacuum cleaner/blower Optional, 1100W (cleaning power)
Power consumption 60W/spindle (at the highest speed), including the power of cleaner motor
Power supply 3-phase 380V 10%, 50/60Hz, 220V, 440V
Weight (12 spindles) 350kg
Dimension (12 spindles) 2250mm (L)×1100mm(W)×1400mm(H)
Cleaner weight 132 kg, depending on the number of spindles
Weight and dimension of the electricity box 45kg, 700mm(L)×300mm(W)×1320mm(H)
FUNCTIONS
The winding speed can be set and controlled automatically by the computer, offering a maximum speed of 1100 m/min.
Advanced yarn cleaning, tension device and photoelectric yarn detector avoids the yarn loop.
Accurate and sensitive speed controller ensures even and consistent winding length (weight).
Electrically rotary waxing ensures the waxing quantity and uniformity.

High Speed Hard Winding Machine
Related products
Sample Cone Yarn Dyeing machine
Sample Cone Yarn Dyeing Machine

Sample Cone Yarn Dyeing Machine
- Computer system: Foshan HuaGao Chinese English computer, equipped with LG PLC.
- Electromagnetic valve: Ningbo Jiaerling
- Frequency converter: Use Made in China frequency converters.
- Pump: self-made high head and large flow centrifugal water pump.
- Main pump motor: Anhui Wannan Motor.
- Master cylinder liquid level: Use 4-20mA analog signal output.
- Level of deputy temporary worker: use foam water level gauge. (American Mike)
- Temperature detection and display: digital temperature display instrument, dual temperature measuring probes.
- The safety system has a triple cylinder head safety interlock mechanism, and the main cylinder is equipped with a stainless
- steel safety valve.
- Heat exchanger: external spacer heating.
- Feeding system: Quantitative feeding based on the process curve.
- Circulation system: The main pump flows internally and externally, which is automatically controlled by a computer or manually controlled by a relay.
- Valves: Y valves are used for heating, stainless steel Y valves are used for single inlet and single row, and other Y valves are produced by joint ventures.
- Temperature control: on-off temperature control, controlled by a computer, with automatic heating, cooling, and insulation functions.
- Dyeing method: air cushion type.
- Opening method: manual opening.
- Surface treatment: polishing inside and outside the cylinder.
- Cage: Each dyeing machine is equipped with butterfly blades and self-locking locks.
- Body plate: high-quality stainless steel. (S31603)
- Bath ratio: 1:5-1:6
- Chemical material system: including heating and water adding functions, including overflow type salt melting device.
- Overflow cleaning: The cleaning port is installed on the upper part of the cylinder port, and the bottom of the cylinder is filled with water, while the cylinder is drained for easy cleaning.
- Commutation method: Novel "U" type commutation.
- Random accessories: Each model comes with one set of mechanical seals, pot mouth rings, and reversing seals for the main and auxiliary pumps.
Sample Cone Yarn Dyeing Machine
Card winding machine
Card Winding Machine
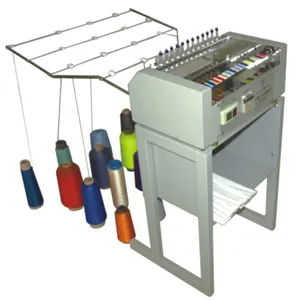
Card Winding Machine
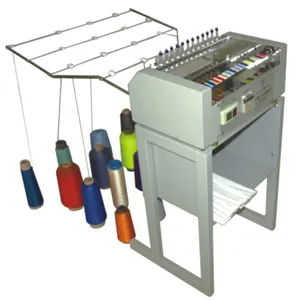
Card Winding Machine
Perspiration Tester
Perspiration Tester

Perspiration Tester
- Fabric samples are treated with synthetic perspiration solution (acidic or alkaline).
- They are sandwiched with adjacent fabric and placed between glass or acrylic plates.
- The assembly is loaded into the tester and pressed under specific pressure.
- it’s then incubated at 37°C (body temperature) for a fixed time (typically 4 or 16 hours).
- Afterward, color change and staining are evaluated using a gray scale.
- Accurate Sweat Simulation - Mimics real-life effects of acidic and alkaline perspiration on fabrics.
- Improves Product Quality - Ensures textiles retain color and don’t bleed or stain when worn.
- Supports Standard Compliance - Follows ISO and AATCC test standards for global market approval.
- Protects Brand Reputation- Reduces customer complaints due to dye transfer or fading.
- Simple and Repeatable- Provides consistent pressure and conditions for reliable results.
- Multi-Sample Testing- Tests multiple specimens at once, saving time in labs.
- Durable and Low Maintenance- Robust frame with minimal moving parts makes it long-lasting and easy to care for.
- Stainless Steel Frame - Corrosion-resistant body for durability and long-term use.
- Multi-Sample Capacity - Can hold up to 20 or more specimens for batch testing.
- Standardized Loading Weight- Applies uniform pressure (usually 12.5 kPa) across all samples.
- Removable Plates - Glass or acrylic plates ensure even contact and easy cleaning.
- Compact Design- Space-saving, bench-top model ideal for lab environments.
- Complies with Test Standards - Meets ISO 105 E04, AATCC 15, and related perspiration fastness standards.
- Ease of Operation - Simple loading, unloading, and incubation process.
- High-Temperature Resistance - Can be used inside incubators at 37°C or ovens as required.
- Prepare the Test Solution - Mix artificial acidic or alkaline perspiration as per standard (ISO or AATCC).
- Cut the Fabric Samples - Cut both the test fabric and adjacent white fabric (usually cotton) to standard size.
- Soak the Samples - Immerse the fabric sandwich (test + adjacent) in the test solution for 30 minutes.
- Remove Excess Liquid - Gently squeeze or blot to remove extra moisture—do not dry.
- Load in the Tester- Place each sandwich between glass or acrylic separator plates in the tester.
- Apply Pressure - Tighten the top plate or place the standard weight on top to apply uniform pressure.
- Incubate - Keep the loaded tester in an oven or incubator at 37°C for 4–16 hours (depending on the method).
- Accurate Sweat Simulation - Mimics real-life effects of acidic and alkaline perspiration on fabrics.
- Improves Product Quality - Ensures textiles retain color and don’t bleed or stain when worn.
- Supports Standard Compliance - Follows ISO and AATCC test standards for global market approval.
- Protects Brand Reputation- Reduces customer complaints due to dye transfer or fading.
- Simple and Repeatable- Provides consistent pressure and conditions for reliable results.
- Multi-Sample Testing- Tests multiple specimens at once, saving time in labs.
- Durable and Low Maintenance- Robust frame with minimal moving parts makes it long-lasting and easy to care for.
- Dry and Evaluate - Remove, air dry the samples, then assess color change and staining using a gray scale.
- Fabric samples are treated with synthetic perspiration solution (acidic or alkaline).
- They are sandwiched with adjacent fabric and placed between glass or acrylic plates.
- The assembly is loaded into the tester and pressed under specific pressure.
- it’s then incubated at 37°C (body temperature) for a fixed time (typically 4 or 16 hours).
- Afterward, color change and staining are evaluated using a gray scale.
Perspiration Tester
Cone yarn Dyeing machine
Cone Yarn Dyeing Machine

Cone Yarn Dyeing Machine
- Computer system: Foshan HuaGao Chinese English computer, equipped with LG PLC.
- Electromagnetic valve: Ningbo Jiaerling
- Frequency converter: Use Made in China frequency converters.
- Pump: self-made high head and large flow centrifugal water pump.
- Main pump motor: Anhui Wannan Motor.
- Master cylinder liquid level: Use 4-20mA analog signal output.
- Level of deputy temporary worker: use foam water level gauge. (American Mike)
- Temperature detection and display: digital temperature display instrument, dual temperature measuring probes.
- The safety system has a triple cylinder head safety interlock mechanism, and the main cylinder is equipped with a stainless
- steel safety valve.
- Heat exchanger: external spacer heating.
- Feeding system: Quantitative feeding based on the process curve.
- Circulation system: The main pump flows internally and externally, which is automatically controlled by a computer or manually controlled by a relay.
- Valves: Y valves are used for heating, stainless steel Y valves are used for single inlet and single row, and other Y valves are produced by joint ventures.
- Temperature control: on-off temperature control, controlled by a computer, with automatic heating, cooling, and insulation functions.
- Dyeing method: air cushion type.
- Opening method: manual opening.
- Surface treatment: polishing inside and outside the cylinder.
- Cage: Each dyeing machine is equipped with butterfly blades and self-locking locks.
- Body plate: high-quality stainless steel. (S31603)
- Bath ratio: 1:5-1:6
- Chemical material system: including heating and water adding functions, including overflow type salt melting device.
- Overflow cleaning: The cleaning port is installed on the upper part of the cylinder port, and the bottom of the cylinder is filled with water, while the cylinder is drained for easy cleaning.
- Commutation method: Novel "U" type commutation.
- Random accessories: Each model comes with one set of mechanical seals, pot mouth rings, and reversing seals for the main and auxiliary pumps.
IR Dyeing Machine Dunlin
IR Dyeing Machine Dunlin
IR Dyeing machine Dunlin is Safe, high efficiency, environment friendly, energy saving, optimum for new dyeing small sample machines0 - 3.5 ℃ / min Cooling rate 0.2 - 5 ℃ / min Cooling method Air-cooled Rotation speed 0 - 60 rpm Liquor ratio 1:5 -1:100 Power supply 1∮AC 220V 50/60HZ Dimensions( L x W x H) 670×670×780mm 860×680×780mm Weight 100kg 120kg Standard Accessories Cups 1set
Put the test sample. Cups stand 1set Place where to put cups. Protective glove 1set To avoid to be hurt by HT cups. Model: IF-24SCapacity: 24 pots Brad: DUNLIN Origin: China
Color dyeing tests for various dyestuffs of IR Dyeing machine Dunlin- Step dyeing tests. C. Dispersing, levelling and impregnating test. D. High or low liquor ratio exhausting tests. E. Fabric steak and staining tests. F. Concentration tests and others. Protection and Safety gates to protect. Temperature control accuracy +/- 0.2degree

IR Dyeing machine
Digital Yarn Twist Tester
Digital Yarn Twist Tester

Digital Yarn Twist Tester

Digital Yarn Twist Tester
Thread Cone Winding Machine
Thread Cone Winding Machine

Thread Cone Winding Machine
- Efficient Yarn Packaging - Speeds up the process of preparing thread for sewing or embroidery.
- Uniform Cone Formation - Ensures consistent cone shape and tension for smooth downstream use.
- Reduces Thread Breakage - Controlled tension and smooth guiding minimize thread damage.
- Time & Labor saving- Automates winding, reducing manual effort and increasing productivity.
- Improves Thread Quality - Removes loose fibers and irregularities during winding.
- Supports Multiple Yarn Types - Compatible with cotton, polyester, silk, and blended threads.
- Adjustable Winding Speed - Variable speed control for different thread types.
- Thread Tension Control System - Maintains consistent tension for smooth winding.
- Auto Stop Mechanism - Stops automatically when cone is full or thread breaks.
- Multiple Spindle Options - Single or multi-spindle designs for higher output.
- Traverse Mechanism - Ensures even layering of thread across the cone.
- Compact & Durable Build - Space-saving, long-lasting structure for industrial use.
- Set Up the Machine - Turn on the power and check all safety covers and switches.
- Load the Yarn Source - Place the yarn hank, bobbin, or spool on the supply holder.
- Mount the Empty Cone - Fix an empty cone securely onto the spindle.
- Thread the Machine - Guide the thread through tension disks, guides, and eyelets as per the machine path.
- Adjust Settings - Set the desired winding speed and tension based on thread type.
- Start the Machine - Press the start button; the thread begins winding onto the cone.
- Monitor the Process - Ensure even winding and tension; adjust traverse if needed.
- Auto-Stop or Manual Stop - The machine will stop automatically if the cone is full or thread breaks.
- Remove the Cone - Carefully remove the finished cone and load a new one if needed.
- Clean and Shut Down - Turn off the machine and clean any thread residue after use.
- Always Use Safety Guards - Ensure all protective covers are in place before operation.
- Avoid Loose Clothing - Prevent thread or moving parts from catching clothes or jewelry.
- Power Off Before Maintenance - Always turn off the machine before threading, cleaning, or adjustments.
- Check Thread Path - Use correct threading to prevent sudden breakage or tangling.
- Don’t Overload the Cone - Stop the machine once the cone is adequately filled to avoid jamming.
- Keep Area Clean - Remove lint and thread waste regularly to prevent fire hazards or machine faults.
- Daily Cleaning - Wipe dust and thread particles from guides, spindles, and tension parts.
- Lubrication - Oil moving parts (as per manual) weekly to reduce wear.
- Check Tension Settings - Inspect and calibrate tension mechanisms for consistent winding.
- Inspect Belts and Motors - Look for wear or looseness in drive belts and check motor sound regularly.
- Replace Worn Parts Promptly - Replace traverse mechanisms, springs, or tension disks if worn out.

Thread Cone Winding Machine
Automatic Bobbin Hydro extractor
Automatic Bobbin Hydro extractor

Automatic Bobbin Hydro extractor
- Computer system: Foshan HuaGao Chinese English computer, equipped with LG PLC.
- Electromagnetic valve: Ningbo Jiaerling
- Frequency converter: Use Made in China frequency converters.
- Pump: self-made high head and large flow centrifugal water pump.
- Main pump motor: Anhui Wannan Motor.
- Master cylinder liquid level: Use 4-20mA analog signal output.
- Level of deputy temporary worker: use foam water level gauge. (American Mike)
- Temperature detection and display: digital temperature display instrument, dual temperature measuring probes.
- The safety system has a triple cylinder head safety interlock mechanism, and the main cylinder is equipped with a stainless
- steel safety valve.
- Heat exchanger: external spacer heating.
- Feeding system: Quantitative feeding based on the process curve.
- Circulation system: The main pump flows internally and externally, which is automatically controlled by a computer or manually controlled by a relay.
- Valves: Y valves are used for heating, stainless steel Y valves are used for single inlet and single row, and other Y valves are produced by joint ventures.
- Temperature control: on-off temperature control, controlled by a computer, with automatic heating, cooling, and insulation functions.
- Dyeing method: air cushion type.
- Opening method: manual opening.
- Surface treatment: polishing inside and outside the cylinder.
- Cage: Each dyeing machine is equipped with butterfly blades and self-locking locks.
- Body plate: high-quality stainless steel. (S31603)
- Bath ratio: 1:5-1:6
- Chemical material system: including heating and water adding functions, including overflow type salt melting device.
- Overflow cleaning: The cleaning port is installed on the upper part of the cylinder port, and the bottom of the cylinder is filled with water, while the cylinder is drained for easy cleaning.
- Commutation method: Novel "U" type commutation.
- Random accessories: Each model comes with one set of mechanical seals, pot mouth rings, and reversing seals for the main and auxiliary pumps.
Automatic Bobbin Hydro extractor