Automatic Bobbin Hydro extractor
$0.00
Automatic Bobbin Hydro extractor

Automatic Bobbin Hydro extractor
An Automatic Bobbin Hydro extractor is a high-speed centrifugal machine used in textile dyeing units to remove excess water from yarn bobbins after dyeing. It operates by spinning the bobbins at high speed, extracting water via centrifugal force, significantly reducing drying time.
Purpose of Automatic Bobbin Hydro extractor:
To dewater dyed yarn bobbins quickly and efficiently before final drying.
Applications of Automatic Bobbin Hydro extractor:
Textile dye houses
Cone and bobbin dyeing units
Pre-drying in yarn processing
Working Principle of Automatic Bobbin Hydro extractor:
Dyed bobbins are loaded into perforated baskets.
The machine spins rapidly, forcing water outwards and draining it away.
Automatic controls manage cycle time, speed, and safety functions.
Benefits of Automatic Bobbin Hydro extractor:
Fast Water Removal – Greatly reduces moisture content before drying, saving energy.
Gentle on Yarn – Designed to avoid damage or deformation of soft dyed bobbins.
Labor-Saving Operation – Fully automatic with programmable cycles for ease of use.
Shortens Drying Time – Cuts drying time in hot air or RF dryers significantly.
Improves Production Efficiency – Speeds up workflow in dyeing and finishing processes.
Reduces Manual Handling – Often includes hydraulic or pneumatic lifting for easy bobbin loading/unloading.
Features of Automatic Bobbin Hydro extractor:
High-Speed Stainless Steel Drum – Rust-resistant and built for stable, high-speed spinning.
PLC or Digital Controller – For setting speed, time, and safety interlocks.
Soft Start & Stop Function – Protects yarn and machine from sudden movement or shock.
Automatic Lid Locking System – Ensures safety during operation.
Efficient Drainage System – Quickly removes expelled water to drain line.
Vibration-Free Design – Balanced system reduces noise and mechanical wear.
How to Use Automatic Bobbin Hydro extractor:
Prepare Bobbins – Ensure dyed bobbins are properly packed and free of loose ends.
Load the Machine – Open the lid and place bobbins evenly inside the perforated drum. – Avoid overloading to maintain balance during spinning.
Close and Lock Lid – Securely close the lid; the automatic locking system will engage.
Set Parameters- Use the control panel to set spinning speed and time according to yarn type.
Start the Cycle – Press start; the machine will gradually accelerate to the preset speed.
Monitor Operation – The machine runs, extracting water by centrifugal force.
Cycle Completion – After the set time, the machine slows down and stops automatically.
Unload Bobbins – Open the lid once unlocked and carefully remove the hydro-extracted bobbins.
Clean the Machine – Remove any residual water or lint from the drum after use.
Maintenance Tips for Automatic Bobbin Hydro extractor:
Daily:
☐ Clean the drum and interior to remove lint and water residues
☐ Check lid locking mechanism for smooth operation
☐ Inspect drain pipes for clogging
Weekly:
☐ Lubricate moving parts as per manufacturer instructions
☐ Inspect belt or motor coupling for wear
☐ Test safety interlocks and emergency stop
Monthly:
☐ Check electrical wiring and control panel for damage
☐ Balance drum if vibrations are noticeable
☐ Tighten all bolts and fasteners
Safety Tips:
☐ Always ensure the lid is properly locked before starting
☐ Do not overload the drum to avoid imbalance and damage
☐ Keep hands and loose clothing clear of moving parts
☐ Use emergency stop in case of abnormal noise or vibration
☐ Turn off power before cleaning or maintenance
Automatic Bobbin Hydro extractor
Maintenance Checklist
Daily:
☐ Clean drum and interior from lint & water
☐ Check lid locking mechanism
☐ Inspect drain pipes for clogging
Weekly:
☐ Lubricate moving parts as per manual
☐ Inspect belt/motor coupling for wear
☐ Test safety interlocks & emergency stop
Monthly:
☐ Check electrical wiring and control panel
☐ Balance drum if vibration occurs
☐ Tighten bolts and fasteners
Safety Checklist
☐ Confirm lid is locked before operation
☐ Avoid overloading drum
☐ Keep hands & loose clothing away from moving parts
☐ Use emergency stop if needed
☐ Power off before cleaning or maintenance
TECHNICAL DATA OF THE MACHINE
- Computer system: Foshan HuaGao Chinese English computer, equipped with LG PLC.
- Electromagnetic valve: Ningbo Jiaerling
- Frequency converter: Use Made in China frequency converters.
- Pump: self-made high head and large flow centrifugal water pump.
- Main pump motor: Anhui Wannan Motor.
- Master cylinder liquid level: Use 4-20mA analog signal output.
- Level of deputy temporary worker: use foam water level gauge. (American Mike)
- Temperature detection and display: digital temperature display instrument, dual temperature measuring probes.
- The safety system has a triple cylinder head safety interlock mechanism, and the main cylinder is equipped with a stainless
- steel safety valve.
- Heat exchanger: external spacer heating.
- Feeding system: Quantitative feeding based on the process curve.
- Circulation system: The main pump flows internally and externally, which is automatically controlled by a computer or manually controlled by a relay.
- Valves: Y valves are used for heating, stainless steel Y valves are used for single inlet and single row, and other Y valves are produced by joint ventures.
- Temperature control: on-off temperature control, controlled by a computer, with automatic heating, cooling, and insulation functions.
- Dyeing method: air cushion type.
- Opening method: manual opening.
- Surface treatment: polishing inside and outside the cylinder.
- Cage: Each dyeing machine is equipped with butterfly blades and self-locking locks.
- Body plate: high-quality stainless steel. (S31603)
- Bath ratio: 1:5-1:6
- Chemical material system: including heating and water adding functions, including overflow type salt melting device.
- Overflow cleaning: The cleaning port is installed on the upper part of the cylinder port, and the bottom of the cylinder is filled with water, while the cylinder is drained for easy cleaning.
- Commutation method: Novel “U” type commutation.
- Random accessories: Each model comes with one set of mechanical seals, pot mouth rings, and reversing seals for the main and auxiliary pumps.
Automatic Bobbin Hydro extractor
Related products
Oscillation type water bath Dyeing Machine
Oscillation Type Water Bath Dyeing Machine
An Oscillation Type Water Bath Dyeing Machine is a laboratory apparatus designed for dyeing and washing textile samples under controlled temperature conditions. It combines a heated water bath with an oscillating mechanism to ensure uniform dye penetration and consistent coloration across fabric or yarn samples. Key Features of Oscillation Type Water Bath Dyeing Machine - Oscillating Mechanism: Provides back-and-forth movement to agitate the dye solution, ensuring even contact between the dye and the textile sample.- Multiple Beaker Capacity: Typically accommodates 12 to 24 beakers, allowing simultaneous processing of multiple samples under identical or varied conditions. - Digital Temperature Control: Maintains precise temperature settings, usually up to 99°C, suitable for various dyeing processes including atmospheric dyeing, scouring, and bleaching.- Adjustable Oscillation Speed: Offers variable speed settings, commonly ranging from 50 to 200 cycles per minute, to accommodate different fabric types and dyeing requirements. - Programmable Settings: Advanced models come with programmable controllers, allowing users to set and save multiple dyeing protocols for repeatability and efficiency. Durable Construction: Constructed with high-quality stainless steel (e.g., SUS304), ensuring resistance to corrosion and longevity even under rigorous laboratory conditions. ✅ Benefits of Oscillation Type Water Bath Dyeing Machine - Uniform Dyeing Results: The oscillation mechanism ensures consistent dye penetration, reducing the risk of uneven coloration and enhancing the reproducibility of results.- Efficiency in Sample Processing: The ability to process multiple samples simultaneously accelerates laboratory workflows and facilitates comparative studies. - Versatility: Suitable for a range of applications including dyeing, washing, scouring, bleaching, and fastness testing across various textile materials.- Energy and Resource Conservation: Designed for low liquor ratios (e.g., 1:5 to 1:20), these machines minimize water and chemical usage, promoting sustainable laboratory practices. - Enhanced Safety and Cleanliness: Enclosed beaker systems reduce the risk of spills and exposure to chemicals, ensuring a safer laboratory environment. Typical Applications of Oscillation Type Water Bath Dyeing Machine - Textile Research and Development: Ideal for developing and testing new dye formulations and processes on a small scale before scaling up to production levels. Quality Control: Used in quality assurance laboratories to assess color fastness, dye uptake, and other critical parameters of textile products.- Educational Purposes: Serves as a practical tool in academic settings for teaching dyeing principles and techniques. In summary, the Oscillation Type Water Bath Dyeing Machine is an essential tool in textile laboratories, offering precise control over dyeing parameters, improving efficiency, and ensuring high-quality, reproducible results across various textile materials. Features of Oscillation Type Water Bath Dyeing Machine:- Oscillating Mechanism - Provides back-and-forth movement of beakers for uniform dye penetration and sample agitation.
- Multiple Beaker Capacity - Supports dyeing of 12–24 samples simultaneously, ideal for comparative lab testing.
- Digital Temperature Control - Maintains precise water bath temperature (typically up to 99°C), essential for consistent dyeing.
- Variable Oscillation Speed - Adjustable speed settings (e.g., 50–200 cycles/min) to suit different materials and processes.
- Programmable Settings - Allows setting of temperature, time, and speed for repeatable and automated dyeing cycles.
- Stainless Steel Construction - Corrosion-resistant frame and bath for durability in chemical environments.
- Beaker Safety Holders - Secure placement of beakers to prevent spills and maintain consistent treatment.
- Compact Design - Lab-friendly size for easy integration into research and quality control spaces.
- Low Liquor Ratio Operation - Efficient dyeing using minimal dye bath volume (e.g., 1:5 to 1:20), reducing chemical and water use.
- Quiet and Stable Performance

water bath/Shaker bath Dyeing machine
Card winding machine
Card Winding Machine
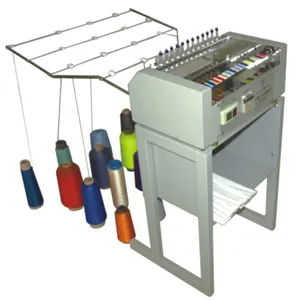
Card Winding Machine
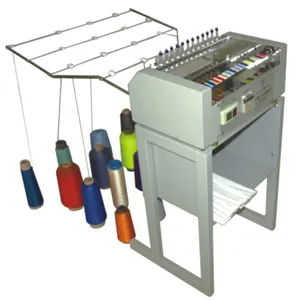
Card Winding Machine
High speed hard winding machine
High Speed Hard Winding Machine

High Speed Hard Winding Machine
- Increased Productivity - High-speed operation reduces winding time significantly.
- Consistent Package Quality - Ensures uniform and firm yarn packages ideal for further processing.
- Reduced Yarn Breakage - Precise tension control minimizes yarn damage during winding.
- Versatility - Handles different types of yarns including delicate and coarse fibers.
- User-Friendly Operation - Simple controls and automation reduce operator fatigue.
- Improved Efficiency - Automatic package build-up reduces manual adjustments.
- Space Saving - Compact design fits well in production lines and labs.
- Set Up the Machine - Switch on the power and check all safety guards.
- Load Yarn - Thread the yarn through tension guides and eyelets as per the manual.
- Adjust Tension - Set tension according to yarn type to avoid slack or breakage.
- Place Empty Cone/Package - Mount the empty cone or package holder securely.
- Start Winding- Press the start button; machine will begin winding at set speed.
- Monitor the Process - Observe yarn package build-up and make adjustments if necessary.
- Stop and Remove Package - Once winding is complete, stop the machine and remove the yarn package carefully.
- Maintenance - Clean the machine regularly and lubricate moving parts as needed.
- High-Speed Operation - Capable of winding yarns at fast speeds (up to 3000 RPM) to boost productivity.
- Precise Tension Control - Adjustable tension mechanism to prevent yarn breakage and ensure tight winding.
- Automatic Package Formation - Uniform, firm package build-up for consistent yarn quality.
- Versatile Yarn Compatibility - Suitable for cotton, polyester, wool, and blended yarns.
- User-Friendly Interface - Easy controls with digital or analog panels for speed and tension adjustment.
- Robust Construction - Durable stainless steel or metal frame for long-term reliability.
- Safety Features - Includes emergency stop buttons and yarn break sensors.
- Compact Design - Space-saving structure ideal for labs and production floors.
- Low Maintenance - Designed for easy cleaning and minimal upkeep.

High Speed Hard Winding Machine
Sample Cone Yarn Dyeing machine
Sample Cone Yarn Dyeing Machine

Sample Cone Yarn Dyeing Machine
- Computer system: Foshan HuaGao Chinese English computer, equipped with LG PLC.
- Electromagnetic valve: Ningbo Jiaerling
- Frequency converter: Use Made in China frequency converters.
- Pump: self-made high head and large flow centrifugal water pump.
- Main pump motor: Anhui Wannan Motor.
- Master cylinder liquid level: Use 4-20mA analog signal output.
- Level of deputy temporary worker: use foam water level gauge. (American Mike)
- Temperature detection and display: digital temperature display instrument, dual temperature measuring probes.
- The safety system has a triple cylinder head safety interlock mechanism, and the main cylinder is equipped with a stainless
- steel safety valve.
- Heat exchanger: external spacer heating.
- Feeding system: Quantitative feeding based on the process curve.
- Circulation system: The main pump flows internally and externally, which is automatically controlled by a computer or manually controlled by a relay.
- Valves: Y valves are used for heating, stainless steel Y valves are used for single inlet and single row, and other Y valves are produced by joint ventures.
- Temperature control: on-off temperature control, controlled by a computer, with automatic heating, cooling, and insulation functions.
- Dyeing method: air cushion type.
- Opening method: manual opening.
- Surface treatment: polishing inside and outside the cylinder.
- Cage: Each dyeing machine is equipped with butterfly blades and self-locking locks.
- Body plate: high-quality stainless steel. (S31603)
- Bath ratio: 1:5-1:6
- Chemical material system: including heating and water adding functions, including overflow type salt melting device.
- Overflow cleaning: The cleaning port is installed on the upper part of the cylinder port, and the bottom of the cylinder is filled with water, while the cylinder is drained for easy cleaning.
- Commutation method: Novel "U" type commutation.
- Random accessories: Each model comes with one set of mechanical seals, pot mouth rings, and reversing seals for the main and auxiliary pumps.
Sample Cone Yarn Dyeing Machine
Fully Automatic Radio Frequency Dryer
Fully Automatic Radio Frequency Dryer
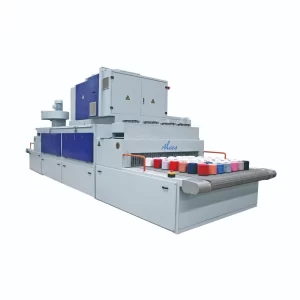
Fully Automatic Radio Frequency Dryer
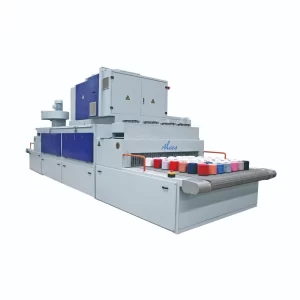
Fully Automatic Radio Frequency Dryer
Thread Cone Winding Machine
Thread Cone Winding Machine

Thread Cone Winding Machine
- Efficient Yarn Packaging - Speeds up the process of preparing thread for sewing or embroidery.
- Uniform Cone Formation - Ensures consistent cone shape and tension for smooth downstream use.
- Reduces Thread Breakage - Controlled tension and smooth guiding minimize thread damage.
- Time & Labor saving- Automates winding, reducing manual effort and increasing productivity.
- Improves Thread Quality - Removes loose fibers and irregularities during winding.
- Supports Multiple Yarn Types - Compatible with cotton, polyester, silk, and blended threads.
- Adjustable Winding Speed - Variable speed control for different thread types.
- Thread Tension Control System - Maintains consistent tension for smooth winding.
- Auto Stop Mechanism - Stops automatically when cone is full or thread breaks.
- Multiple Spindle Options - Single or multi-spindle designs for higher output.
- Traverse Mechanism - Ensures even layering of thread across the cone.
- Compact & Durable Build - Space-saving, long-lasting structure for industrial use.
- Set Up the Machine - Turn on the power and check all safety covers and switches.
- Load the Yarn Source - Place the yarn hank, bobbin, or spool on the supply holder.
- Mount the Empty Cone - Fix an empty cone securely onto the spindle.
- Thread the Machine - Guide the thread through tension disks, guides, and eyelets as per the machine path.
- Adjust Settings - Set the desired winding speed and tension based on thread type.
- Start the Machine - Press the start button; the thread begins winding onto the cone.
- Monitor the Process - Ensure even winding and tension; adjust traverse if needed.
- Auto-Stop or Manual Stop - The machine will stop automatically if the cone is full or thread breaks.
- Remove the Cone - Carefully remove the finished cone and load a new one if needed.
- Clean and Shut Down - Turn off the machine and clean any thread residue after use.
- Always Use Safety Guards - Ensure all protective covers are in place before operation.
- Avoid Loose Clothing - Prevent thread or moving parts from catching clothes or jewelry.
- Power Off Before Maintenance - Always turn off the machine before threading, cleaning, or adjustments.
- Check Thread Path - Use correct threading to prevent sudden breakage or tangling.
- Don’t Overload the Cone - Stop the machine once the cone is adequately filled to avoid jamming.
- Keep Area Clean - Remove lint and thread waste regularly to prevent fire hazards or machine faults.
- Daily Cleaning - Wipe dust and thread particles from guides, spindles, and tension parts.
- Lubrication - Oil moving parts (as per manual) weekly to reduce wear.
- Check Tension Settings - Inspect and calibrate tension mechanisms for consistent winding.
- Inspect Belts and Motors - Look for wear or looseness in drive belts and check motor sound regularly.
- Replace Worn Parts Promptly - Replace traverse mechanisms, springs, or tension disks if worn out.

Thread Cone Winding Machine
Laboratory hydro Extractor
Laboratory Hydro Extractor
A Laboratory Hydro Extractor is a compact, high-speed centrifuge used in textile labs to remove excess water from fabric or yarn samples after dyeing or washing. It works on the principle of centrifugal force, efficiently reducing moisture content before drying. Key Features:- Centrifugal Water Extraction - Uses high-speed spinning (typically 1400–2800 RPM) to extract water from textiles.
- Stainless Steel Inner Basket - Perforated drum holds fabric/yarn securely and allows water to drain efficiently.
- Compact Lab Design - Space-saving unit designed specifically for laboratory sample sizes.
- Digital Timer and Speed Control - Allows precise setting of spin duration and RPM to match sample needs.
- Safety Lock System - Ensures the lid remains closed during operation for user safety.
- Quick Water Removal - Significantly reduces drying time by extracting up to 90–95% of water content.
- Low Noise and Vibration - Balanced design ensures quiet and stable operation.
- Efficient Water Removal - Rapidly extracts 90–95% of water from samples, reducing drying time significantly.
- Saves Time and Energy - Cuts down the load on dryers and shortens total processing time in lab workflows.
- Improves Sample Quality - Gentle spinning preserves fabric structure, avoiding damage or distortion.
- Precise Control - Adjustable speed and timer ensure optimal settings for different fabric types.
- Compact and Lab-Friendly - Small footprint ideal for laboratory use with limited space.
- User Safety - Safety lock prevents lid opening during operation, protecting the user.
- Cost-Effective - Reduces the need for extended dryer use, saving on electricity and equipment wear.
- Versatile Use - Suitable for yarn, fabric, and garment samples across various fiber types.
- High-Speed Centrifugal Operation - Typically runs at 1400–2800 RPM for quick and efficient water removal.
- Stainless Steel Inner Drum - Corrosion-resistant, perforated basket for durability and efficient water drainage.
- Digital Timer and Speed Control - Allows precise control of spin duration and speed based on sample type.
- Compact and Portable Design - Ideal for lab environments with limited space.
- Safety Lock Mechanism - Prevents the lid from opening while the machine is in operation.
- Shock Absorption System- Reduces vibration and noise for smooth, stable performance.
- Quick Cycle Times - Short dewatering cycles improve lab throughput and efficiency.
- Low Maintenance Design - Simple mechanical setup with easy-to-clean components.
- Sample Versatility - Suitable for small fabric swatches, yarns, and small garments.
- Energy Efficient - Uses minimal power while delivering high performance.
- Prepare the Sample - After dyeing or washing, gently squeeze excess water from the fabric or yarn sample by hand.
- Load the Sample - Open the lid and place the sample evenly in the stainless steel drum. - Avoid overloading or uneven placement to maintain balance.
- Close the Lid securely - Ensure the safety lid is properly closed and locked.
- Set the Timer and Speed - Use the control panel to set the spin time (typically 1–5 minutes) and RPM suitable for the sample type.
- Start the Machine- Press the start button. The extractor will spin at the selected speed to remove water via centrifugal force.
- Wait for Spin Completion - The machine will automatically stop after the timer runs out.
- Unload the Sample - Once the drum stops completely, open the lid and carefully remove the sample.
- Proceed to Drying - The dewatered sample can now be air-dried or placed in a drying oven or stenter.

Laboratory hydro Extractor Machine Dunlin price in Bangladesh Laboratory hydro Extractor Machine Dunlin in textile Textile testing equipment in Bangladesh Textile testing equipment in Dhaka Textile testing equipment in Uttara MAAM tex Laboratory hydro Extractor Machine Dunlin price in Bangladesh
Laboratory hydro ExtractorElectronic wrap reel
Electronic Wrap Reel

Electronic Wrap Reel

Electronic Wrap Reel