Gray scale
$0.00
Gray Scale

Gray Scale
The Gray Scale is a visual tool used in the textile and dyeing industry to evaluate and grade the color change or staining of a fabric after testing (e.g., washing, rubbing, and light exposure). It helps assess how much a fabric’s color has altered or transferred during durability or fastness tests.
Types of Gray Scale:
- Gray Scale for Color Change – Compares the original and tested sample to measure color fading or alteration.
- Gray Scale for Staining – Compares a white adjacent fabric (before and after testing) to assess color transfer or staining.
Rating System :
– Uses a 1 to 5 scale:
– Grade 5: No change or staining (excellent)
– Grade 1: Severe change or heavy staining (poor)
Intermediate grades (like 4–5, 3–4, etc.) are also used for finer evaluation.
Construction :- Each scale includes pairs of gray chips with varying contrast levels to visually match the test results.
Usage Areas:- Textile testing labs- Dyeing and finishing quality control- Standards like ISO, AATCC, and BIS tests
Benefits :
- Standardized Evaluation – Provides a consistent and objective way to assess color change or staining.
- Simple and Quick to Use – Enables rapid visual comparison during fabric testing.
- Widely Accepted – Complies with international standards (ISO, AATCC) for color fastness grading.
- Cost-Effective Tool – Inexpensive yet essential for reliable quality control in textiles.
- Enhances Quality Assurance – Helps detect dyeing or printing issues before bulk production.
- Supports Multiple Tests – Used for evaluating wash fastness, rubbing fastness, perspiration, light exposure, and more.
- Portable and Durable – Easy to carry and long-lasting with proper care.
Features :
- Dual Type Availability – Comes in two types: for Color Change and for Staining.
- 5-Point Grading System – Grades from 1 (poor) to 5 (excellent), with half-step intervals like 4–5, 3–4.
- Standardized Grey Chips – Includes contrasting grey color pairs to match fabric changes accurately.
- Compact Design – Small, portable card or booklet format for easy lab and field use.
- Durable Material – Made from stable, fade-resistant plastic or cardboard for long-term use.
- Compliance with Standards – Follows ISO 105-A02 (Color Change) and ISO 105-A03 (Staining) norms.
- Easy Visual Comparison – Designed for quick side-by-side assessment of fabric before and after testing.
How to Use :
Select the Right Gray Scale – Use Color Change scale to check fading, or staining scale to check color transfer.
- Place the Samples – Lay the untested (original) and tested fabric side by side (for color change)
– Or place the adjacent white fabric next to the gray scale (for staining).
- Match Against Gray Scale Chips – Visually compare the difference between the samples and find the closest matching gray pair on the scale.
- Assign a Grade
– Grade from 1 to 5, where:
– Grade 5 = no change/staining
– Grade 1 = severe change/staining
– Use half-grades like 4–5 if needed.
- Record the Result – Note the grade in your test report as per the test method (e.g., ISO 105).
- Store Properly – Keep the gray scale away from light and moisture to avoid fading.
- Features :
- Dual Type Availability – Comes in two types: for Color Change and for Staining.
- 5-Point Grading System – Grades from 1 (poor) to 5 (excellent), with half-step intervals like 4–5, 3–4.
- Standardized Grey Chips – Includes contrasting grey color pairs to match fabric changes accurately.
- Compact Design – Small, portable card or booklet format for easy lab and field use.
Categories:
- Gray Scale for Color Change – Used to evaluate the degree of color fading or change in a fabric after testing (e.g., washing, light exposure). – Assesses how much the original color has altered.
- Gray Scale for Staining – Used to assess the degree of color transfer from a dyed fabric to an adjacent white fabric during testing (e.g., rubbing, washing).
– Evaluates staining on undyed fabrics.
These two types are essential tools in color fastness testing across textile labs. Want to know which standard tests use each type?

Gray Scale
Related products
Random Tumble Pilling Tester
Random Tumble Pilling Tester
The Random Tumble Pilling Tester is a specialized instrument designed to assess the pilling resistance of textile fabrics. Pilling refers to the formation of small, fuzzy balls (pills) on the fabric surface due to wear and friction. This tester simulates the wear conditions that fabrics experience during actual use, providing valuable data on their durability and appearance retention. Purpose of Random Tumble Pilling Tester The primary function of the Random Tumble Pilling Tester is to evaluate how fabrics resist pilling, fuzzing, and matting. This assessment is crucial for manufacturers aiming to ensure the longevity and aesthetic quality of their textile products. Working Principle of Random Tumble Pilling Tester The tester operates by placing fabric specimens into cylindrical test chambers lined with cork. Inside each chamber, a stainless steel impeller rotates at a high speed (typically around 1200 revolutions per minute), causing the fabric samples to tumble randomly. Compressed air is injected to enhance the tumbling action. This process simulates the friction and wear that fabrics undergo during regular use. After a predetermined duration, the samples are removed and visually assessed for pilling using standardized rating scales. Key Specifications of Random Tumble Pilling Tester Test Chambers: Available in configurations of 2 or 4 chambers to accommodate multiple samples simultaneously. - Rotation Speed: Approximately 1200 revolutions per minute. - Chamber Dimensions: Typically around 146 mm in diameter and 152 mm in length. - Impeller Size: Standard impellers measuring about 121 mm. - Compressed Air Pressure: Adjustable, commonly between 14–21 kPa (2–3 psi). - Timer: Digital timer allowing precise control over test duration. - Power Supply: Generally operates on 220V, 50Hz power sources. Applicable Standards of Random Tumble Pilling Tester The Random Tumble Pilling Tester complies with several international testing standards, ensuring its suitability for global applications:- ASTM D3512- ISO 12945-3- DIN 53867- JIS L 1076- GB/T 4802.4 Benefits of Random Tumble Pilling Tester - Realistic Simulation: Accurately replicates the wear and friction conditions fabrics face during actual use.- Standardized Testing: Adheres to international standards, facilitating consistent and comparable results.- Efficient Evaluation: Allows simultaneous testing of multiple samples, increasing laboratory throughput.- Quality Assurance: Provides manufacturers with critical data to improve fabric formulations and production processes. User-Friendly Operation: Features intuitive controls and clear viewing windows for easy monitoring. Applications of Random Tumble Pilling Tester The Random Tumble Pilling Tester is widely used in various sectors of the textile industry: - Apparel Manufacturing: Assessing the durability of clothing fabrics. - Home Textiles: Evaluating materials used in upholstery, curtains, and bedding. - Quality Control Laboratories: Routine testing to ensure product consistency and compliance with standards.- Research and Development: Developing new fabrics with enhanced resistance to pilling. Features of Random Tumble Pilling Tester:- Multiple Test Chambers - Typically comes with 2 or 4 cork-lined chambers for simultaneous testing of multiple fabric samples.
- High-Speed Rotating Impellers - Impellers rotate at around 1200 rpm to create intense, random tumbling motion.
- Compressed Air System - Ensures continuous fabric movement and realistic simulation of wear.
- Digital Timer- Allows precise setting of test duration with easy-to-read display.
- Viewing Windows- Transparent chamber doors for monitoring fabric movement during testing.
- Standard Compliant Design- Meets ASTM D3512, ISO 12945-3, GB/T 4802.4 and other major standards.
- Robust Construction- Durable materials and components designed for long-term laboratory use.
- Easy Sample Handling - Quick-open chamber lids and simple sample placement process.
- Compact Footprint- Saves space in laboratory environments.
- Prepare Samples- Cut fabric into standard-sized specimens (usually circular or rectangular per ASTM/ISO specs)- Condition samples as per the standard (usually 24 hrs at 21°C, 65% RH).
- Load the Chambers - Place each sample into a cork-lined test chamber. - Add a small piece of gray cotton backing fabric if required by the method.
- Set Parameters - Adjust compressed air pressure (typically 14–21 kPa or 2–3 psi).
- Start the Test- Close the chamber doors and press start. - Impellers rotate, tumbling the samples randomly with air flow.
- Stop and Unload - Once the timer ends, remove the samples carefully.
- Evaluate Pilling - Compare the tested samples to standard pilling rating photographs or scales.
- Record Results - Document the pilling grades and any observations.

Fastness Rotary Friction Tester
Fastness Rotary Friction Tester
A Fastness Rotary Friction Tester, also known as a Rotary Crock meter, is a specialized instrument used to evaluate the color fastness of textiles and materials when subjected to rotational rubbing. This test simulates the wear and friction that fabrics experience during use, helping manufacturers assess the durability of dyes and finishes. Purpose of Fastness Rotary Friction Tester The primary function of the Fastness Rotary Friction Tester is to determine how well a fabric's color withstands rubbing, both in dry and wet conditions. This is crucial for ensuring the longevity and appearance of textiles in real-world applications, such as clothing, upholstery, and footwear. Working Principle of Fastness Rotary Friction Tester The tester operates by applying a specified pressure to a fabric sample using a standardized rubbing finger covered with a test cloth. The rubbing finger performs a set number of rotational movements (typically 1.125 turns clockwise followed by 1.125 turns counterclockwise) over the fabric surface. After the test, the degree of color transfer to the test cloth and any changes in the fabric's appearance are evaluated against standardized gray scales. Common Testing Standards - AATCC 116: Colorfastness to Crocking: Rotary Vertical Crock meter Method. ISO 105 X16: Textiles—Tests for color fastness—Part X16: Color fastness to rubbing—small areas. - SATRA TM8: Color fastness to rubbing. Key Specifications of Fastness Rotary Friction Tester - Rubbing Head Diameter: Typically 16 mm. - Applied Pressure: Approximately 1134 grams (11.1 N). - Rotation: 1.125 turns clockwise followed by 1.125 turns counterclockwise. - Sample Size: Commonly 60 mm × 60 mm. - Test Cloth: Standardized white cotton cloth, either dry or wetted depending on the test condition. Benefits of Fastness Rotary Friction Tester - Realistic Simulation: Mimics the actual wear and friction fabrics undergo during use. - Versatility: Applicable to a wide range of materials, including textiles, leather, and printed fabrics. - Quality Assurance: Ensures products meet industry standards for color durability. - Standard Compliance: Aligns with international testing standards, facilitating global trade and quality benchmarks. Applications Fastness Rotary Friction Tester - Textile Industry: Assessing the color durability of garments, upholstery, and other fabric products. - Footwear Manufacturing: Testing the colorfastness of shoe uppers and linings. - Automotive Interiors: Evaluating the wear resistance of seat covers and other interior fabrics. Quality Control Laboratories: Routine testing to ensure product consistency and compliance with standards. Benefits of Fastness Rotary Friction Tester:- Accurate Colorfastness Evaluation- Provides precise assessment of how well fabric resists color loss and staining from rubbing.
- Simulates Real-World Wear - Recreates rotational friction found in actual use (e.g., seat covers, apparel wear points).
- Supports Wet & Dry Testing - Can test under both dry and wet conditions for comprehensive results.
- Standardized Testing - Complies with global standards (AATCC 116, ISO 105 X16), ensuring reliable and comparable results.
- Time-Saving & Efficient - Quick to set up and run, allowing for high-throughput testing in labs.
- Versatile Use- Suitable for textiles, leather, coated fabrics, and printed surfaces.
- Improves Quality Control - Identifies potential durability issues early in the production process.
- Enhances Product Performance - Helps in developing fabrics with better resistance to rubbing and abrasion.
- Rotary Rubbing Mechanism - Simulates 1.125 clockwise and 1.125 counterclockwise turns for realistic friction.
- Standardized Rubbing Head - Fixed diameter (typically 16 mm) with specified pressure (≈1134 g) for consistent results.
- Dry and Wet Testing Capability - Can perform tests using dry or wet rubbing cloths.
- Sample Holder- Secure and easy-to-use fixture for holding fabric samples in place.
- Test Cloth Mounting Arm- Quick attachment for standardized white rubbing cloths.
- Simple Operation - Manual or motorized operation depending on model; easy to handle for lab technicians.
- Compliance with Standards - Follows AATCC 116, ISO 105 X16, and SATRA TM8 protocols.
- Prepare the Sample - Cut a fabric piece (typically 60 × 60 mm) and condition it per standard requirements.
- Mount the Fabric - Secure the fabric sample on the sample holder or base plate of the tester.
- Attach Rubbing Cloth - Place a standard white test cloth (dry or wetted as required) over the rubbing head.
- Apply Pressure - Lower the rubbing head onto the fabric. Standard weight is about 1134 g.
- Start the Test - Operate the tester: the head performs 1.125 turns clockwise, then 1.125 turns counterclockwise.- Number of cycles (typically 10 or 20) is set based on the test standard.
- Remove and Inspect - After testing, remove the rubbing cloth and assess any color transfer using a gray scale.
- Evaluate Fabric Surface - Check the fabric for visible changes, fading, or wear.
- Record Results - Grade both staining and fabric change per standard gray scale ratings.

Spray Rating Tester
Spray Rating Tester

Spray Rating Tester
- Quick and Simple Evaluation - Offers a fast way to assess fabric water repellency without complex setup.
- Standardized Testing- Complies with AATCC 22 and ISO 4920, ensuring globally accepted results.
- Cost-Effective- Low maintenance and no power requirement make it economical for routine lab use.
- Improves Fabric Performance - Helps manufacturers develop or improve water-resistant textiles.
- Non-Destructive Test - Does not damage the fabric, allowing for additional tests on the same sample.
- Visual Grading- Easy to interpret using a standard spray rating chart (0 to 100 scale).
- Supports Quality Control - Detects finish degradation or variation in water-repellent treatments.
- Portable and Compact- Lightweight design allows easy use in various lab or field settings.
- Standardized Spray Nozzle - Delivers consistent water spray per AATCC and ISO specifications.
- 45° Specimen Mounting Angle - Ensures uniform test setup for accurate and repeatable results.
- Stainless Steel or Aluminum Frame - Corrosion-resistant and durable for long-term use with water exposure.
- Water Reservoir and Funnel System - Provides precise water volume (usually 250 ml) for each test.
- Graduated Spray Stand- Fixed height (150 mm above specimen) for controlled spray impact.
- Detachable Specimen Holder- Easy loading and removal of fabric samples.
- Compact and Lightweight Design - Portable and convenient for both lab and field testing.
- No Electricity Required - Fully manual operation increases reliability and reduces operating costs.
- Prepare the Sample - Cut fabric to standard size (usually 180 × 180 mm). - Condition the sample if required (21°C, 65% RH for 24 hours).
- Mount the Fabric - Place the fabric on the specimen holder at a 45° angle.
- Fill the Reservoir - Pour 250 ml of distilled water into the upper funnel.
- Start the Test - Release the water through the nozzle; it sprays over the fabric for about 25–30 seconds.
- Inspect the Fabric - After spraying, visually assess the water beading or penetration on the surface.
- Rate the Sample - Compare the fabric’s wetting pattern with the standard spray rating chart: - 100 = No sticking/wetting - 90–50 = Partial wetting - 0 = Complete wetting
- Record the Rating - Document the spray rating for quality control or reporting.

ICI Pilling & Snagging Test Machine
Tensile Strength tester
VeriVide Colour Assessment Cabinets
VeriVide Colour Assessment Cabinets
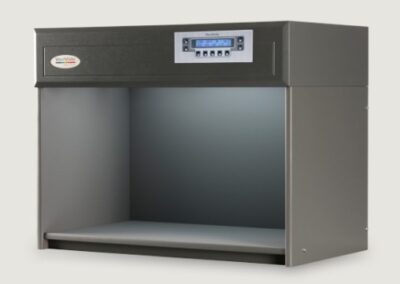
- Either 4 or 5 light sources available for each model including D65, D50, 840P15, F and UV - see Lamp Options.• Internal finishes in Munsell N5, Munsell N7 or Grey 5574 • Diffuser and/or dimmer options available Dimensions of VeriVide Colour Assessment Cabinets CAC 60-4 Dimensions (mm) Width Height Depth Overall 710 545 420
Digital Elmendorf tearing tester
Digital Elmendorf Tearing Tester
Digital Elmendorf Tearing Tester is a precision instrument used to measure the tear strength of materials like woven fabrics, paper, plastic films, and nonwovens. It determines how much force is required to continue tearing a pre-slit sample. Key Functions of Digital Elmendorf Tearing Tester: - Measures propagation tear resistance, not initial tear. - Uses a pendulum to apply force; the energy lost during tearing is calculated to determine tear strength. - Equipped with a digital display for direct reading of results in grams or millinewtons. Core Components: - Pendulum Arm: Applies tearing force. - Clamps: Secure the sample before and after the tear. - Cutting Blade: Creates a precise slit at the start of the test. - Digital Display Unit: Shows the tearing force result clearly and instantly. - Counterweights: Optional weights for increasing test range (for stronger materials). Applications of Digital Elmendorf Tearing Tester: - Testing tear resistance of: - Textile fabrics (especially woven) - Paper and cardboard - Plastic films - Nonwovens - Packaging materials Benefits of Digital Elmendorf Tearing Tester:- Accurate Tear Strength Measurement - Provides precise data on tear resistance, critical for quality control and product performance.
- Digital Readout - Easy-to-read display gives instant, reliable results without manual calculations.
- High Reproducibility - Ensures consistent test outcomes due to controlled tearing angle and speed.
- Fast Testing Process - Simple loading and quick test cycle increase lab efficiency.
- Suitable for Various Materials - Tests a wide range of flexible materials like textiles, paper, plastic, and packaging.
- Customizable Range - Use of optional weights extends the test range for low to high tear strength materials.
- Low Sample Waste - Requires small fabric or material samples, reducing waste during testing.
- Standards Compliance - Meets international testing standards (e.g., ASTM D1424, ISO 13937) for credibility and uniformity.
- Precision Sample Clamp - Securely holds samples in place to ensure accurate tear initiation.
- Pre-Cutting Blade - Integrated knife creates a precise initial slit in the sample before tearing.
- User-Friendly Interface - Simple buttons and screen navigation for ease of operation.
- Standard Test Compliance - Compatible with ASTM D1424, ISO 1974, ISO 13937, and other tear strength standards.
- Sturdy Construction - Made with durable materials for long-lasting performance and stable operation.
- Compact Design - Space-efficient footprint ideal for laboratory environments.
- Data Output Options- Some models offer USB or printer connectivity for result documentation.
- Prepare the Sample - Cut the material (fabric, paper, film, etc.) to standard size (typically 100 × 63 mm for textiles) and slit it with the pre-cutter as required.
- Select Pendulum Weight - Choose the appropriate pendulum or add counterweights based on expected tear strength.
- Calibrate the Machine - Set the pendulum to its starting position and zero the display.
- Clamp the Sample - Fix one half of the sample in the stationary clamp and the other in the moving clamp.
- Cut the Initial Slit - Use the integrated blade to make a precise cut at the marked slit area (usually 20 mm).
- Release the Pendulum - Trigger the pendulum to swing and tear the sample through the pre-slit.
- Read the Result - The digital display will show the tearing force automatically (in g, mN, or cN).
- Record or Export Data - Save or print the result if your model supports USB or printer connection.
- Reset for Next Test - Reposition the pendulum and prepare a new sample for the next cycle.

Laboratory mini stenter Dryer
Laboratory mini stenter Dryer
A Laboratory Mini Stenter Dryer is a compact, lab-scale machine designed to simulate the drying and heat-setting processes used in textile finishing. It mimics the function of industrial stenter machines but on a much smaller scale, making it ideal for testing fabric behavior, shrinkage, and finish quality under controlled conditions. Key Features:- Controlled Heating System
- Adjustable Fabric Width
- Variable Speed Conveyor - Allows control over fabric dwell time for drying or heat-setting.
- Compact and Bench-Top Design - Space-saving design ideal for textile labs and R&D units.
- Digital Controls - Easy-to-use digital interface for setting temperature, conveyor speed, and process time.
- Transparent Viewing Window - Allows operators to monitor fabric movement and drying visually.
- Low Energy Consumption - Designed for lab use, consuming less power than industrial models.
- Accurate Simulation of Production - Mimics industrial stenter conditions on a lab scale, ideal for pre-production testing and R&D.
- Cost-Effective Testing - Enables testing and fabric finishing without the high cost or space requirements of full-scale machines.
- Energy Efficient - Consumes less power compared to large stenters, making it economical for small-scale or frequent use.
- Precise Control - Offers accurate control of temperature, speed, and fabric tension, ensuring consistent results.
- Space-Saving Design - Compact and bench-top friendly, perfect for laboratories with limited space.
- Multiple Applications - Useful for drying, heat-setting, shrinkage testing, and evaluating chemical finishes.
- Faster Development Cycles - Speeds up new product development by allowing rapid sample testing and adjustments.
- Improved Fabric Quality - Helps optimize finishing parameters for better dimensional stability, hand feel, and appearance.
- Safe and User-Friendly- Designed with lab safety in mind, including temperature safety controls and easy operation.
- Compact Bench-Top Design - Ideal for laboratory use with limited space requirements.
- Adjustable Temperature Control - Precise heating (usually up to 220–250°C) with digital controllers for accurate processing.
- Variable Conveyor Speed- Allows adjustment of fabric dwell time for different drying or heat-setting needs.
- Width Adjustment Mechanism - Equipped with clips or pins to stretch and fix fabric width-wise, simulating industrial stenter conditions.
- Transparent Viewing Window - Enables visual monitoring of fabric movement and drying inside the chamber.
- Digital Display Panel- Easy-to-use interface for setting and monitoring temperature, speed, and time.
- Stainless Steel Construction- Durable and corrosion-resistant for long-term use at high temperatures.
- Uniform Heat Distribution- Ensures consistent fabric treatment across the width.
- Safety Features- Over-temperature protection and insulated body for operator safety.
- Versatile Applications - Suitable for drying, heat-setting, shrinkage testing, and chemical finish evaluations.