Controller For IR Dyeing Machine
$0.00
Controller For IR Dyeing Machine
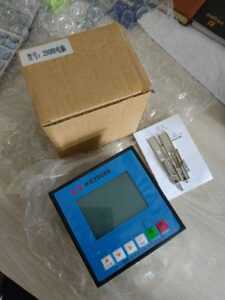
IR Dyeing machine controller
Controller For IR Dyeing Machine offers exceptional quality .purchasing of our controller provides cost efficiencies, and customization options enabling you to meet your specific requirements comfortably. Collaborate with program
A Controller for IR Dyeing Machine is a specialized control system designed to manage and automate the dyeing process in textile manufacturing, particularly using infrared heating technology. These controllers are crucial for achieving consistent dye quality, reducing energy consumption, and optimizing the dyeing process.
Key Features of an Controller For IR Dyeing Machine :
- Temperature Control:- Precisely regulates the infrared heaters to maintain uniform temperature across the dye bath. – Supports customizable heating curves (ramp-up, hold, and cool-down phases).
- Programmable Logic Control (PLC): – Allows operators to set and automate dyeing programs for different fabrics and dye types. – Supports multiple recipes or programs for different batches.
- Real-Time Monitoring and Feedback: – Monitors parameters like temperature, fabric rotation, bath circulation, and timing. – Provides real-time data and alarms for deviations.
- Touchscreen Interface / HMI (Human Machine Interface): – User-friendly interface for configuring and monitoring processes. – Multi-language support and graphical display of process curves.
- Data Logging and Traceability: – Records process data for quality control and traceability.
- Energy Efficiency Optimization: – Manages IR heater output to reduce energy usage. – Often includes features for auto shut-off or idle mode.
- Safety Features: – Includes emergency stop, over-temperature protection, and fault detection systems. 8. Connectivity: – Modern controllers may support Ethernet, Modbus, or other industrial communication protocols for integration into factory automation systems.
Using A Controller For IR Dyeing Machine provides several benefits, especially in textile manufacturing where precision and efficiency are critical. Here are the key advantages:
- Improved Dyeing Accuracy and Consistency
– Maintains precise temperature control and timing, ensuring uniform dye uptake across the fabric.
– Reduces color variation between batches.
- Enhanced Energy Efficiency- Infrared heating is more energy-efficient than traditional heating methods.- The controller optimizes energy use by adjusting the IR output based on process needs, reducing overall energy consumption.
- Time Savings- Faster heating and cooling cycles due to infrared technology.- Automated processes reduce manual intervention and cycle times. 4. Better Process Control- Programmable dyeing cycles and precise control over each stage (heating, dyeing, rinsing, cooling).- Real-time monitoring and adjustments improve reliability.
- Reduced Water and Chemical Usage- More efficient dye penetration and fixation mean less water and fewer chemicals are needed for reprocessing or corrections.6. Lower Operational Costs
– Energy savings, reduced rework, and lower labor input contribute to cost efficiency.
– Minimizes fabric damage, reducing material waste.
- Enhanced Safety Built-in alarms, emergency shut-off and automatic fault detection enhance operational safety.8. Data Logging and Traceability- Ability to record and review dyeing process data helps in quality control and troubleshooting.- Facilitates compliance with industry standards and audits.
- User-Friendly Operation- Modern touchscreen interfaces make it easier for operators to manage and monitor processes.- Multilingual support and visual feedback enhance usability.
Related products
IR Dyeing Machine Dunlin
IR Dyeing Machine Dunlin
IR Dyeing machine Dunlin is Safe, high efficiency, environment friendly, energy saving, optimum for new dyeing small sample machines0 - 3.5 ℃ / min Cooling rate 0.2 - 5 ℃ / min Cooling method Air-cooled Rotation speed 0 - 60 rpm Liquor ratio 1:5 -1:100 Power supply 1∮AC 220V 50/60HZ Dimensions( L x W x H) 670×670×780mm 860×680×780mm Weight 100kg 120kg Standard Accessories Cups 1set
Put the test sample. Cups stand 1set Place where to put cups. Protective glove 1set To avoid to be hurt by HT cups. Model: IF-24SCapacity: 24 pots Brad: DUNLIN Origin: China
Color dyeing tests for various dyestuffs of IR Dyeing machine Dunlin- Step dyeing tests. C. Dispersing, levelling and impregnating test. D. High or low liquor ratio exhausting tests. E. Fabric steak and staining tests. F. Concentration tests and others. Protection and Safety gates to protect. Temperature control accuracy +/- 0.2degree

IR Dyeing machine
HTHP Glycerin bath dyeing machine
HTHP Glycerin Bath Dyeing Machine
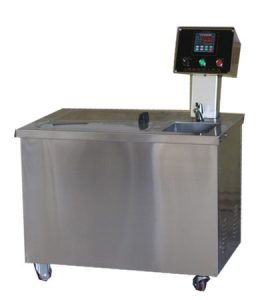
HTHP dyeing machine
- High Temperature Capability - Operates up to 140°C or more, ideal for disperse dyeing of polyester which requires elevated temperatures.
- Glycerin as Heat Transfer Medium - Glycerin allows for precise and uniform heating beyond the boiling point of water, without pressure buildup as in steam-based systems.
- Small Sample Dyeing - Used for lab-scale dyeing of fabric or yarn samples (commonly 5–10 g per tube), useful in R&D or color matching.
- Multiple Sample Capacity - Usually has multiple dyeing tubes/chambers for simultaneous dyeing of several samples under identical conditions.
- Accurate Temperature and Time Control - Digital or microprocessor-based controllers regulate temperature, heating rate, and timing precisely.
- Uniform Dyeing - Ensures even dye penetration due to consistent heat distribution and controlled rotation or agitation.
- Energy Efficient Glycerin’s heat retention reduces energy consumption compared to steam systems.
- Compact and Durable Design - Bench-top design, made from stainless steel and heat-resistant components for long life and lab use.
- Uniform Heating with Glycerin - Glycerin provides consistent heat transfer, ensuring even dye uptake and minimizing shade variation.
- Energy Efficient- Glycerin retains heat longer, reducing energy consumption compared to traditional steam-based dyeing.
- Accurate Process Control - Precise temperature and time control enhance reproducibility and dyeing consistency.
- Ideal for Lab and Sample Work - Perfect for R&D, shade matching, and recipe development with small fabric or yarn samples.
- Multi-Sample Dyeing - Allows multiple samples to be dyed simultaneously under identical conditions, saving time and effort.
- Compact and Safe - Bench-top design fits in laboratories and is safer than high-pressure steam systems.
- Low Maintenance - Simplified operation and fewer mechanical parts compared to steam-based systems lower upkeep needs.
- Faster Dyeing Cycles- Glycerin heats and cools quickly, reducing overall dyeing time.
- High-Temperature Operation - Capable of dyeing up to 140–150°C, suitable for synthetic fibers like polyester.
- Glycerin as Heat Medium - Uses glycerin for uniform, efficient heat transfer without generating high steam pressure.
- Multiple Dyeing Chambers - Usually equipped with 6–24 tubes for simultaneous multi-sample dyeing under identical conditions.
- Digital Temperature Controller- Offers precise control of temperature, time, and heating rate with programmable settings.
- Compact and Lab-Friendly Design - Bench-top model, easy to operate in laboratory environments with limited space.
- Stainless Steel Construction - Corrosion-resistant and durable for long-term, high-temperature operation.
- Safety Features - Includes over-temperature protection and thermal insulation to prevent heat loss and ensure operator safety.
- Agitation or Sample Rotation- Some models offer rotation or agitation for uniform dye penetration.
- Energy Efficient Heating - Glycerin’s heat retention improves energy efficiency over water- or steam-based systems.
- Low Maintenance - Simplified mechanical system reduces the need for frequent servicing.
Perspiration Tester
Perspiration Tester

Perspiration Tester
- Fabric samples are treated with synthetic perspiration solution (acidic or alkaline).
- They are sandwiched with adjacent fabric and placed between glass or acrylic plates.
- The assembly is loaded into the tester and pressed under specific pressure.
- it’s then incubated at 37°C (body temperature) for a fixed time (typically 4 or 16 hours).
- Afterward, color change and staining are evaluated using a gray scale.
- Accurate Sweat Simulation - Mimics real-life effects of acidic and alkaline perspiration on fabrics.
- Improves Product Quality - Ensures textiles retain color and don’t bleed or stain when worn.
- Supports Standard Compliance - Follows ISO and AATCC test standards for global market approval.
- Protects Brand Reputation- Reduces customer complaints due to dye transfer or fading.
- Simple and Repeatable- Provides consistent pressure and conditions for reliable results.
- Multi-Sample Testing- Tests multiple specimens at once, saving time in labs.
- Durable and Low Maintenance- Robust frame with minimal moving parts makes it long-lasting and easy to care for.
- Stainless Steel Frame - Corrosion-resistant body for durability and long-term use.
- Multi-Sample Capacity - Can hold up to 20 or more specimens for batch testing.
- Standardized Loading Weight- Applies uniform pressure (usually 12.5 kPa) across all samples.
- Removable Plates - Glass or acrylic plates ensure even contact and easy cleaning.
- Compact Design- Space-saving, bench-top model ideal for lab environments.
- Complies with Test Standards - Meets ISO 105 E04, AATCC 15, and related perspiration fastness standards.
- Ease of Operation - Simple loading, unloading, and incubation process.
- High-Temperature Resistance - Can be used inside incubators at 37°C or ovens as required.
- Prepare the Test Solution - Mix artificial acidic or alkaline perspiration as per standard (ISO or AATCC).
- Cut the Fabric Samples - Cut both the test fabric and adjacent white fabric (usually cotton) to standard size.
- Soak the Samples - Immerse the fabric sandwich (test + adjacent) in the test solution for 30 minutes.
- Remove Excess Liquid - Gently squeeze or blot to remove extra moisture—do not dry.
- Load in the Tester- Place each sandwich between glass or acrylic separator plates in the tester.
- Apply Pressure - Tighten the top plate or place the standard weight on top to apply uniform pressure.
- Incubate - Keep the loaded tester in an oven or incubator at 37°C for 4–16 hours (depending on the method).
- Accurate Sweat Simulation - Mimics real-life effects of acidic and alkaline perspiration on fabrics.
- Improves Product Quality - Ensures textiles retain color and don’t bleed or stain when worn.
- Supports Standard Compliance - Follows ISO and AATCC test standards for global market approval.
- Protects Brand Reputation- Reduces customer complaints due to dye transfer or fading.
- Simple and Repeatable- Provides consistent pressure and conditions for reliable results.
- Multi-Sample Testing- Tests multiple specimens at once, saving time in labs.
- Durable and Low Maintenance- Robust frame with minimal moving parts makes it long-lasting and easy to care for.
- Dry and Evaluate - Remove, air dry the samples, then assess color change and staining using a gray scale.
- Fabric samples are treated with synthetic perspiration solution (acidic or alkaline).
- They are sandwiched with adjacent fabric and placed between glass or acrylic plates.
- The assembly is loaded into the tester and pressed under specific pressure.
- it’s then incubated at 37°C (body temperature) for a fixed time (typically 4 or 16 hours).
- Afterward, color change and staining are evaluated using a gray scale.
Perspiration Tester
Hydraulic GSM Cutter
Hydraulic GSM Cutter
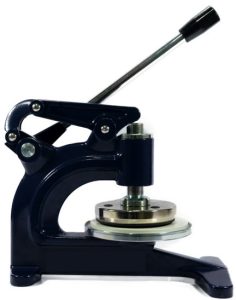
Hydraulic GSM Cutter
- High Cutting Precision - Ensures consistent and accurate fabric sample size for reliable GSM results.
- Effortless Operation- Hydraulic action reduces manual effort and operator fatigue.
- Ideal for Thick or Multi-Layer Fabrics - Cuts through dense or multiple fabric layers cleanly.
- Time-Saving - Speeds up the sample preparation process, especially for high-volume testing.
- Improves Test Accuracy - Uniform samples help eliminate errors in GSM calculation.
- Durable and Long-Lasting - Robust construction ensures stability and extended service life.
- Safety Enhancement - Reduces risk of injury compared to manual rotary cutters.
- Consistent Pressure Application - Hydraulic mechanism maintains steady force for each cut.
- Hydraulic Press Mechanism - Applies consistent and strong pressure for clean, even cuts.
- Standard Cutting Die (100 cm²) - Produces fabric samples suitable for GSM testing with standard area.
- Heavy-Duty Construction - Built with robust metal frame for long-term lab or industrial use.
- Sharp Stainless Steel Blades - Durable and replaceable blades ensure smooth, precise cuts.
- Cutting Pad Included - Comes with a rubber or nylon base to protect blades and ensure clean edges.
- Simple Lever or Button Operation - Easy to use with minimal training required.
- Non-slip Base - Provides stability during operation for safe, accurate cutting.
- Supports Various Fabric Types
- Place the Cutting Pad - Lay the rubber or nylon cutting pad on a flat surface.
- Position the Fabric - Place the fabric sample flat and smooth on the cutting pad.
- Align the Cutter - Position the GSM cutter die over the desired area of the fabric.
- Activate Hydraulic Press - Pull the lever or press the button to apply hydraulic pressure and cut the sample.
- Remove the Sample - Lift the cutter and carefully take out the circular fabric piece (usually 100 cm²).
- Weigh the Sample - Place the cut sample on a precision balance or GSM scale to determine weight.
- Calculate GSM - Multiply the sample weight (in grams) by 100 to get GSM.
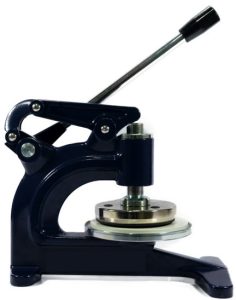
Hydraulic GSM Cutter
Bursting strength tester
Bursting strength tester

true burst
- Available with automatic test strip feeder Measurements are simple to make with the Mullen type Bursting Strength Tester. Fast automatic measurements Measurement starts automatically once a test piece has been placed in the measuring gap. The clamping foot descends, and a bursting strength measurement is made.
- Bursting pressure can reach up to 1.2MPa 5. The maximum burst and expansion degree can reach 70mm. 6. Strengthen the lighting system on the test surface. 7. The main aerodynamic force helps to clamp the sample system. 8. A variety of test areas are available, and the switching is easy.
- A variety of unit conversions between Chinese and English. 10. Reliable anti-pinch safety protection design. [Technical parameter]: 1. Test range: (0~1)Mpa (the range above 1Mpa needs to be customized) 2. The minimum graduation value: 0.0001Mpa 3. Pressurization mode: direct pressurization, timing pressurization, and expansion degree pressurization.
Color Matching Cabinet-Light Box
Color Matching Cabinet-Light Box

Color Matching Cabinet-Light Box
Laboratory tenter
Laboratory Tenter
A Laboratory Tenter (or Lab Stenter) is a small-scale version of an industrial tenter machine used in textile finishing. It is designed for heat-setting, drying, and finishing of fabric samples under controlled conditions in textile testing labs or R&D departments. Key Features:- Heat-Setting and Drying - Simulates the process of setting fabric dimensions and applying finishes using controlled temperature and tension.
- Fabric Width Control - Uses clips or pins on chains or rails to hold fabric edges and stretch them to desired width, just like in full-size tenters.
- Adjustable Temperature and Speed - Digital controls allow precise setting of drying/curing temperature and conveyor speed to match production conditions.
- Compact Design - Bench-top or floor-standing units suitable for labs with limited space.
- Transparent Viewing Chamber - Allows visual inspection of fabric behavior during processing.
- Versatile Application Range - Can process woven, knitted, and nonwoven fabrics of various compositions (cotton, polyester, blends, etc.).
- Accurate Simulation of Production - Replicates industrial finishing processes for reliable lab-scale testing and development.
- Improves Fabric Quality- Allows precise control of heat and tension, optimizing fabric properties like shrinkage, dimensional stability, and hand feel.
- Cost-Effective - Enables process trials and fabric development without using full-scale production equipment.
- Speeds Up R&D - Facilitates quick testing and adjustment of settings for new fabric styles or finishes.
- Versatile Applications - Suitable for drying, heat-setting, finishing, and evaluating different types of fabrics and treatments.
- Space-Efficient - Compact design fits easily into textile labs or sample rooms.
- Energy Efficient- Uses less power than industrial machines, ideal for small-scale and repeated testing.
- Process Control and Reproducibility- Digital controls ensure consistent and repeatable results, aiding in quality assurance and product development.
- Enhances Safety - Built with lab use in mind, featuring insulation and safety systems to protect users.
- Precise Temperature Control - Digital temperature setting (typically up to 220–250°C) for accurate heat-setting and drying.
- Adjustable Fabric Width - Equipped with clip or pin chains to hold and stretch fabric across the width, simulating real stentering.
- Variable Conveyor or Chain Speed- Adjustable speed to control fabric dwell time during processing.
- Compact and Lab-Friendly Design - Designed for bench-top or small floor space use in textile labs.
- Transparent Chamber Window - Allows monitoring of fabric behavior during treatment.
- Digital Display and Control Panel - Easy operation for setting temperature, speed, and time.
- Uniform Heat Distribution- Ensures even treatment across the fabric width for accurate testing.
- Stainless Steel Construction - Durable, corrosion-resistant body for long-term use at high temperatures.
- Safety Features - Includes over-temperature protection, insulated body, and emergency stop functions.
- Sample Versatility - Suitable for various fabric types (woven, knit, synthetic, blends) and lab finishing tasks.

laboratory mini tenter
Laboratory mini stenter Dryer
Laboratory mini stenter Dryer
A Laboratory Mini Stenter Dryer is a compact, lab-scale machine designed to simulate the drying and heat-setting processes used in textile finishing. It mimics the function of industrial stenter machines but on a much smaller scale, making it ideal for testing fabric behavior, shrinkage, and finish quality under controlled conditions. Key Features:- Controlled Heating System
- Adjustable Fabric Width
- Variable Speed Conveyor - Allows control over fabric dwell time for drying or heat-setting.
- Compact and Bench-Top Design - Space-saving design ideal for textile labs and R&D units.
- Digital Controls - Easy-to-use digital interface for setting temperature, conveyor speed, and process time.
- Transparent Viewing Window - Allows operators to monitor fabric movement and drying visually.
- Low Energy Consumption - Designed for lab use, consuming less power than industrial models.
- Accurate Simulation of Production - Mimics industrial stenter conditions on a lab scale, ideal for pre-production testing and R&D.
- Cost-Effective Testing - Enables testing and fabric finishing without the high cost or space requirements of full-scale machines.
- Energy Efficient - Consumes less power compared to large stenters, making it economical for small-scale or frequent use.
- Precise Control - Offers accurate control of temperature, speed, and fabric tension, ensuring consistent results.
- Space-Saving Design - Compact and bench-top friendly, perfect for laboratories with limited space.
- Multiple Applications - Useful for drying, heat-setting, shrinkage testing, and evaluating chemical finishes.
- Faster Development Cycles - Speeds up new product development by allowing rapid sample testing and adjustments.
- Improved Fabric Quality - Helps optimize finishing parameters for better dimensional stability, hand feel, and appearance.
- Safe and User-Friendly- Designed with lab safety in mind, including temperature safety controls and easy operation.
- Compact Bench-Top Design - Ideal for laboratory use with limited space requirements.
- Adjustable Temperature Control - Precise heating (usually up to 220–250°C) with digital controllers for accurate processing.
- Variable Conveyor Speed- Allows adjustment of fabric dwell time for different drying or heat-setting needs.
- Width Adjustment Mechanism - Equipped with clips or pins to stretch and fix fabric width-wise, simulating industrial stenter conditions.
- Transparent Viewing Window - Enables visual monitoring of fabric movement and drying inside the chamber.
- Digital Display Panel- Easy-to-use interface for setting and monitoring temperature, speed, and time.
- Stainless Steel Construction- Durable and corrosion-resistant for long-term use at high temperatures.
- Uniform Heat Distribution- Ensures consistent fabric treatment across the width.
- Safety Features- Over-temperature protection and insulated body for operator safety.
- Versatile Applications - Suitable for drying, heat-setting, shrinkage testing, and chemical finish evaluations.