Steam Soaping machine
Steam Soaping Machine
A Steam Soaping Machine is a specialized laboratory apparatus used in textile dyeing processes, particularly for post-dyeing treatments like soaping, which enhances color fastness and removes unfixed dyes from fabric samples. This machine is designed to perform soaping treatments on dyed textile samples using steam. Soaping is a critical step in dyeing, especially for reactive dyes, as it removes unfixed dye particles, ensuring better color fastness and preventing dye bleeding. The steam soaping process involves treating the dyed fabric with a soaping solution at elevated temperatures, facilitated by steam, to achieve optimal results. ⚙️ Key Features of Steam Soaping Machine - Beaker Material: Constructed with high-grade 316L stainless steel for excellent corrosion resistance and durability.- Operation Modes: Offers both automatic control and manual water filling options, providing flexibility in operation. - Drainage System: Equipped with an automatic drainage device for efficient removal of used solutions.- Temperature Control: Precise temperature regulation to maintain optimal soaping conditions.- Compact Design: Suitable for laboratory settings, occupying minimal space while delivering effective performance. ✅ Benefits of Steam Soaping Machine - Enhanced Color Fastness: Effectively removes unfixed dyes, resulting in improved wash and rub fastness of the fabric.- Efficient Processing: Reduces the time required for post-dyeing treatments compared to conventional methods.- Consistent Results: Provides uniform treatment across samples, ensuring reproducibility in testing and quality control.- Resource Optimization: Minimizes water and chemical usage through controlled processing parameters.- Versatility: Applicable to various fabric types and dye classes, making it a valuable tool in research and development. Typical Applications - Laboratory Testing: Used in dyeing laboratories for evaluating the fastness properties of dyed samples. - Research and Development: Assists in developing and optimizing dyeing processes and formulations. - Quality Control: Ensures that dyed fabrics meet specified fastness standards before bulk production. In summary, a Steam Soaping Machine is an essential laboratory instrument in the textile industry, facilitating efficient and effective post-dyeing treatments to enhance the quality and durability of dyed fabrics. Features of Steam Soaping Machine:- High-Grade Stainless Steel Beakers - Made from 316L stainless steel for excellent chemical and heat resistance.
- Steam-Based Heating - Uses direct or indirect steam to maintain consistent high temperatures ideal for soaping.
- Precise Temperature Control - Maintains stable temperatures (typically up to 98–100°C) for effective removal of unfixed dyes.
- Automatic and Manual Modes - Offers both programmable automatic cycles and manual operation for flexibility.
- Beaker Agitation or Rotation - Ensures uniform soaping action across fabric surfaces.
- Automatic Drainage System - Efficiently removes used soaping solution to speed up cycle changeovers.
- Compact Design - Fits well in lab settings while allowing multiple samples to be processed simultaneously.
- Safety Features - Includes pressure and temperature protection systems to ensure safe operation.
- Low Water and Chemical Use - Designed for minimal liquor ratios, enhancing sustainability.
- User-Friendly Interface - Simple digital controls or touch panel for easy operation and cycle programming.
- Prepare the Dyed Sample - After dyeing, rinse the fabric to remove surface dye and prepare it for soaping.
- Load the Fabric - Place the dyed fabric or sample into the beakers or holders inside the machine.
- Add Soaping Solution - Pour the prepared soaping agent (usually a detergent solution) into the beakers or tank as per recipe.
- Set Parameters
- Start the Cycle - Begin the soaping process. The machine will heat the solution using steam and agitate/rotate the beakers for even treatment.
- Drain and Rinse - After the cycle ends, the machine may auto-drain. Rinse the fabric with warm water to remove residual chemicals.
- Unload the Samples - Carefully remove the fabric. Inspect for evenness and color fastness improvement.
- Clean the Machine - Rinse and dry the beakers or tank to maintain hygiene for the next use.

Stretch Recovery Tester Static Method
Stretch Recovery Tester Static Method

Stretch Recovery Tester
- A sample is stretched to a predetermined extension or force.
- The stretch is maintained for a set period.
- After removing the load, the recovery (return to original length) is measured after a fixed time.
- The fabric sample is clamped and stretched to a specific length or force.
- It’s held for a fixed duration (e.g., 1–5 minutes).
- The tension is released, and the sample is allowed to recover.
- The recovered length is measured after a set time.


Stretch Recovery Tester
Tensile Strength tester
Thread Cone Winding Machine
Thread Cone Winding Machine

Thread Cone Winding Machine
- Efficient Yarn Packaging - Speeds up the process of preparing thread for sewing or embroidery.
- Uniform Cone Formation - Ensures consistent cone shape and tension for smooth downstream use.
- Reduces Thread Breakage - Controlled tension and smooth guiding minimize thread damage.
- Time & Labor saving- Automates winding, reducing manual effort and increasing productivity.
- Improves Thread Quality - Removes loose fibers and irregularities during winding.
- Supports Multiple Yarn Types - Compatible with cotton, polyester, silk, and blended threads.
- Adjustable Winding Speed - Variable speed control for different thread types.
- Thread Tension Control System - Maintains consistent tension for smooth winding.
- Auto Stop Mechanism - Stops automatically when cone is full or thread breaks.
- Multiple Spindle Options - Single or multi-spindle designs for higher output.
- Traverse Mechanism - Ensures even layering of thread across the cone.
- Compact & Durable Build - Space-saving, long-lasting structure for industrial use.
- Set Up the Machine - Turn on the power and check all safety covers and switches.
- Load the Yarn Source - Place the yarn hank, bobbin, or spool on the supply holder.
- Mount the Empty Cone - Fix an empty cone securely onto the spindle.
- Thread the Machine - Guide the thread through tension disks, guides, and eyelets as per the machine path.
- Adjust Settings - Set the desired winding speed and tension based on thread type.
- Start the Machine - Press the start button; the thread begins winding onto the cone.
- Monitor the Process - Ensure even winding and tension; adjust traverse if needed.
- Auto-Stop or Manual Stop - The machine will stop automatically if the cone is full or thread breaks.
- Remove the Cone - Carefully remove the finished cone and load a new one if needed.
- Clean and Shut Down - Turn off the machine and clean any thread residue after use.
- Always Use Safety Guards - Ensure all protective covers are in place before operation.
- Avoid Loose Clothing - Prevent thread or moving parts from catching clothes or jewelry.
- Power Off Before Maintenance - Always turn off the machine before threading, cleaning, or adjustments.
- Check Thread Path - Use correct threading to prevent sudden breakage or tangling.
- Don’t Overload the Cone - Stop the machine once the cone is adequately filled to avoid jamming.
- Keep Area Clean - Remove lint and thread waste regularly to prevent fire hazards or machine faults.
- Daily Cleaning - Wipe dust and thread particles from guides, spindles, and tension parts.
- Lubrication - Oil moving parts (as per manual) weekly to reduce wear.
- Check Tension Settings - Inspect and calibrate tension mechanisms for consistent winding.
- Inspect Belts and Motors - Look for wear or looseness in drive belts and check motor sound regularly.
- Replace Worn Parts Promptly - Replace traverse mechanisms, springs, or tension disks if worn out.

Thread Cone Winding Machine
VeriVide Colour Assessment Cabinets
VeriVide Colour Assessment Cabinets
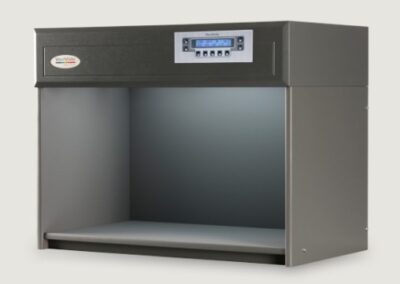
- Either 4 or 5 light sources available for each model including D65, D50, 840P15, F and UV - see Lamp Options.• Internal finishes in Munsell N5, Munsell N7 or Grey 5574 • Diffuser and/or dimmer options available Dimensions of VeriVide Colour Assessment Cabinets CAC 60-4 Dimensions (mm) Width Height Depth Overall 710 545 420