HTHP Glycerin bath dyeing machine
$0.00
HTHP Glycerin Bath Dyeing Machine
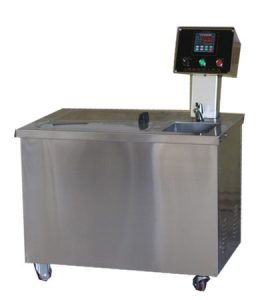
HTHP dyeing machine
The HTHP Glycerin Bath Dyeing Machine (High Temperature High Pressure) is a laboratory or small-scale dyeing machine designed to dye textile samples, especially synthetic fibers like polyester, under high temperature and pressure using glycerin as a heating medium instead of water.
Key Features:
- High Temperature Capability – Operates up to 140°C or more, ideal for disperse dyeing of polyester which requires elevated temperatures.
- Glycerin as Heat Transfer Medium – Glycerin allows for precise and uniform heating beyond the boiling point of water, without pressure buildup as in steam-based systems.
- Small Sample Dyeing – Used for lab-scale dyeing of fabric or yarn samples (commonly 5–10 g per tube), useful in R&D or color matching.
- Multiple Sample Capacity – Usually has multiple dyeing tubes/chambers for simultaneous dyeing of several samples under identical conditions.
- Accurate Temperature and Time Control – Digital or microprocessor-based controllers regulate temperature, heating rate, and timing precisely.
- Uniform Dyeing – Ensures even dye penetration due to consistent heat distribution and controlled rotation or agitation.
- Energy Efficient Glycerin’s heat retention reduces energy consumption compared to steam systems.
- Compact and Durable Design – Bench-top design, made from stainless steel and heat-resistant components for long life and lab use.
Applications:
– Disperse dyeing of polyester.
– Color matching and development.
– Small-batch dye recipe trials before production.
Benefits of HTHP Glycerin Bath Dyeing Machine:
High-Temperature Dyeing – Enables dyeing of synthetic fibers like polyester at temperatures above 100°C without requiring high-pressure steam systems.
- Uniform Heating with Glycerin – Glycerin provides consistent heat transfer, ensuring even dye uptake and minimizing shade variation.
- Energy Efficient- Glycerin retains heat longer, reducing energy consumption compared to traditional steam-based dyeing.
- Accurate Process Control – Precise temperature and time control enhance reproducibility and dyeing consistency.
- Ideal for Lab and Sample Work – Perfect for R&D, shade matching, and recipe development with small fabric or yarn samples.
- Multi-Sample Dyeing – Allows multiple samples to be dyed simultaneously under identical conditions, saving time and effort.
- Compact and Safe – Bench-top design fits in laboratories and is safer than high-pressure steam systems.
- Low Maintenance – Simplified operation and fewer mechanical parts compared to steam-based systems lower upkeep needs.
- Faster Dyeing Cycles- Glycerin heats and cools quickly, reducing overall dyeing time.
Features of HTHP Glycerin Bath Dyeing Machine:
- High-Temperature Operation – Capable of dyeing up to 140–150°C, suitable for synthetic fibers like polyester.
- Glycerin as Heat Medium – Uses glycerin for uniform, efficient heat transfer without generating high steam pressure.
- Multiple Dyeing Chambers – Usually equipped with 6–24 tubes for simultaneous multi-sample dyeing under identical conditions.
- Digital Temperature Controller- Offers precise control of temperature, time, and heating rate with programmable settings.
- Compact and Lab-Friendly Design – Bench-top model, easy to operate in laboratory environments with limited space.
- Stainless Steel Construction – Corrosion-resistant and durable for long-term, high-temperature operation.
- Safety Features – Includes over-temperature protection and thermal insulation to prevent heat loss and ensure operator safety.
- Agitation or Sample Rotation- Some models offer rotation or agitation for uniform dye penetration.
- Energy Efficient Heating – Glycerin’s heat retention improves energy efficiency over water- or steam-based systems.
- Low Maintenance – Simplified mechanical system reduces the need for frequent servicing.
HTHP Glycerin Bath Dyeing Machine dealer In Bangladesh,
Glycerin Bath Dyeing Machine Importer in Bangladesh,
HTHP Dyeing Machine in Bangladesh,
HTHP Bath Dyeing Machine in Bd,
HTHP Dyeing Machine In Uttara,
Glycerin Bath Dyeing Machine Price in Bangladesh,
HTHP Dyeing Machine Supplier in Bangladesh,
Glycerin Bath Dyeing Machine in Bangladesh,
High temperature glycerin Bath Dyeing machine.
Brad: DUNLIN
Origin: China
Application scope of high temperature glycerin machine: it is suitable for high temperature sample
dyeing and washing fastness test of needle woven fabric, woven fabric, yarn, cotton, loose fiber
and zipper. It is a high temperature dyeing sample machine specially designed for dyeing industry,
chemical industry, raw material and cloth industry. It can accurately simulate the actual production
conditions and achieve the required process effect.
Parameter specification:
Model: H-24P
Number of test cups: 24*450ml
Maximum dyeing temperature: 235 ℃
Bath ratio: 1:10~1:60
Heating power: 10800w
Heating medium: Glycerin
Motor power: 0.75w
Rotor speed: 42 r/min
Related products
Orbital Shaker Machine
Orbital Shaker Machine

Orbital Shaker Machine
- Orbital Motion - Provides a smooth circular shaking pattern, ideal for gentle mixing without foaming or splashing.
- Adjustable Speed Control - Speed typically ranges from 50 to 300 RPM, depending on the model and application.
- Timer Function - Allows users to set shaking time from minutes to hours for precise control of experiments.
- Platform with Clamps or Mats - Holds flasks, beakers, test tubes, or trays securely during operation.
- Digital Display (in advanced models) - Shows speed and time settings for accurate and repeatable performance.
- Variable Capacity - Available in sizes to accommodate different lab needs—from a few samples to dozens.
- Quiet Operation - Designed for minimal vibration and noise during continuous use.
- Uniform Mixing - Ensures even distribution of dyes, chemicals, or cultures without manual stirring.
- Gentle Agitation - Ideal for delicate samples like cell cultures or fabric swatches, reducing damage or splashing.
- Hands-Free Operation - Allows continuous, unattended mixing—improving lab efficiency and freeing up personnel.
- Customizable Settings - Adjustable speed and timer let users tailor mixing to specific sample types and needs.
- Versatile Use - Suitable for a wide range of applications including dye mixing, sample incubation, chemical reaction enhancement, and microbial growth.
- Enhanced Reproducibility - Consistent shaking patterns and digital controls ensure repeatable results across experiments.
- Reduces Human Error - Automated operation minimizes variability and manual handling mistakes.
- Compact and Lab-Friendly - Takes up minimal space while accommodating multiple sample containers.
- Orbital Shaking Motion - Moves samples in a circular path for uniform and consistent mixing.
- Variable Speed Control - Adjustable shaking speed (typically 50–300 RPM) to suit different sample types.
- Digital Timer - Programmable run time for precise and repeatable operations.
- Flat Platform Design - Accommodates flasks, beakers, tubes, or trays with optional clamps or non-slip mats.
- LCD or LED Display (in advanced models) - Shows speed, time, and operating status clearly.
- Quiet Operation - Low-noise motor and stable base minimize vibration and disturbance in the lab.
- Overload Protection - Prevents motor damage from excessive weight or resistance.
- Compact and Durable Build - Designed to fit standard lab benches and withstand regular use.
- Versatile Capacity Options - Available in various sizes to handle different numbers and sizes of containers. User-Friendly Interface - Simple control panel for easy setup and operation.

Stretch Recovery Tester Static Method
Stretch Recovery Tester Static Method

Stretch Recovery Tester
- A sample is stretched to a predetermined extension or force.
- The stretch is maintained for a set period.
- After removing the load, the recovery (return to original length) is measured after a fixed time.
- The fabric sample is clamped and stretched to a specific length or force.
- It’s held for a fixed duration (e.g., 1–5 minutes).
- The tension is released, and the sample is allowed to recover.
- The recovered length is measured after a set time.


Stretch Recovery Tester
Controller For IR Dyeing Machine
Controller For IR Dyeing Machine
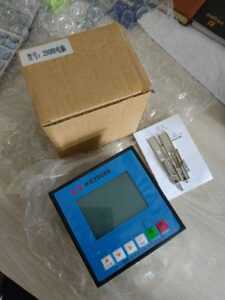
IR Dyeing machine controller
- Temperature Control:- Precisely regulates the infrared heaters to maintain uniform temperature across the dye bath. - Supports customizable heating curves (ramp-up, hold, and cool-down phases).
- Programmable Logic Control (PLC): - Allows operators to set and automate dyeing programs for different fabrics and dye types. - Supports multiple recipes or programs for different batches.
- Real-Time Monitoring and Feedback: - Monitors parameters like temperature, fabric rotation, bath circulation, and timing. - Provides real-time data and alarms for deviations.
- Touchscreen Interface / HMI (Human Machine Interface): - User-friendly interface for configuring and monitoring processes. - Multi-language support and graphical display of process curves.
- Data Logging and Traceability: - Records process data for quality control and traceability.
- Energy Efficiency Optimization: - Manages IR heater output to reduce energy usage. - Often includes features for auto shut-off or idle mode.
- Safety Features: - Includes emergency stop, over-temperature protection, and fault detection systems. 8. Connectivity: - Modern controllers may support Ethernet, Modbus, or other industrial communication protocols for integration into factory automation systems.
- Improved Dyeing Accuracy and Consistency
- Enhanced Energy Efficiency- Infrared heating is more energy-efficient than traditional heating methods.- The controller optimizes energy use by adjusting the IR output based on process needs, reducing overall energy consumption.
- Time Savings- Faster heating and cooling cycles due to infrared technology.- Automated processes reduce manual intervention and cycle times. 4. Better Process Control- Programmable dyeing cycles and precise control over each stage (heating, dyeing, rinsing, cooling).- Real-time monitoring and adjustments improve reliability.
- Reduced Water and Chemical Usage- More efficient dye penetration and fixation mean less water and fewer chemicals are needed for reprocessing or corrections.6. Lower Operational Costs
- Enhanced Safety Built-in alarms, emergency shut-off and automatic fault detection enhance operational safety.8. Data Logging and Traceability- Ability to record and review dyeing process data helps in quality control and troubleshooting.- Facilitates compliance with industry standards and audits.
- User-Friendly Operation- Modern touchscreen interfaces make it easier for operators to manage and monitor processes.- Multilingual support and visual feedback enhance usability.
Laboratory tenter
Laboratory Tenter
A Laboratory Tenter (or Lab Stenter) is a small-scale version of an industrial tenter machine used in textile finishing. It is designed for heat-setting, drying, and finishing of fabric samples under controlled conditions in textile testing labs or R&D departments. Key Features:- Heat-Setting and Drying - Simulates the process of setting fabric dimensions and applying finishes using controlled temperature and tension.
- Fabric Width Control - Uses clips or pins on chains or rails to hold fabric edges and stretch them to desired width, just like in full-size tenters.
- Adjustable Temperature and Speed - Digital controls allow precise setting of drying/curing temperature and conveyor speed to match production conditions.
- Compact Design - Bench-top or floor-standing units suitable for labs with limited space.
- Transparent Viewing Chamber - Allows visual inspection of fabric behavior during processing.
- Versatile Application Range - Can process woven, knitted, and nonwoven fabrics of various compositions (cotton, polyester, blends, etc.).
- Accurate Simulation of Production - Replicates industrial finishing processes for reliable lab-scale testing and development.
- Improves Fabric Quality- Allows precise control of heat and tension, optimizing fabric properties like shrinkage, dimensional stability, and hand feel.
- Cost-Effective - Enables process trials and fabric development without using full-scale production equipment.
- Speeds Up R&D - Facilitates quick testing and adjustment of settings for new fabric styles or finishes.
- Versatile Applications - Suitable for drying, heat-setting, finishing, and evaluating different types of fabrics and treatments.
- Space-Efficient - Compact design fits easily into textile labs or sample rooms.
- Energy Efficient- Uses less power than industrial machines, ideal for small-scale and repeated testing.
- Process Control and Reproducibility- Digital controls ensure consistent and repeatable results, aiding in quality assurance and product development.
- Enhances Safety - Built with lab use in mind, featuring insulation and safety systems to protect users.
- Precise Temperature Control - Digital temperature setting (typically up to 220–250°C) for accurate heat-setting and drying.
- Adjustable Fabric Width - Equipped with clip or pin chains to hold and stretch fabric across the width, simulating real stentering.
- Variable Conveyor or Chain Speed- Adjustable speed to control fabric dwell time during processing.
- Compact and Lab-Friendly Design - Designed for bench-top or small floor space use in textile labs.
- Transparent Chamber Window - Allows monitoring of fabric behavior during treatment.
- Digital Display and Control Panel - Easy operation for setting temperature, speed, and time.
- Uniform Heat Distribution- Ensures even treatment across the fabric width for accurate testing.
- Stainless Steel Construction - Durable, corrosion-resistant body for long-term use at high temperatures.
- Safety Features - Includes over-temperature protection, insulated body, and emergency stop functions.
- Sample Versatility - Suitable for various fabric types (woven, knit, synthetic, blends) and lab finishing tasks.

laboratory mini tenter
Pantone book
Pantone Book

Pantone Book
- Formula Guide (Solid Coated & Uncoated) – For spot color printing.
- Color Bridge – Shows Pantone spot colors alongside CMYK equivalents.
- Pantone Fashion, Home + Interiors (FHI) – For textiles, soft goods, and home decor.
- Pantone CMYK and Pastels & Neons Guides – For process printing and special effect colors.
- Formula Guide (Solid Coated & Uncoated)
- Color Bridge Guide (Coated & Uncoated)
- CMYK Guide (Coated & Uncoated)
- Pastels & Neons Guide
- Metallics Guide
- FHI Color Guide (TPG – Paper)
- FHI Cotton Passport & Cotton Planner (TCX – Textile)
- FHI Polyester Swatch Book
- Pantone SkinTone Guide
- Pantone Plastic Standard Chips

Pantone Book
Digital Elmendorf tearing tester
Digital Elmendorf Tearing Tester
Digital Elmendorf Tearing Tester is a precision instrument used to measure the tear strength of materials like woven fabrics, paper, plastic films, and nonwovens. It determines how much force is required to continue tearing a pre-slit sample. Key Functions of Digital Elmendorf Tearing Tester: - Measures propagation tear resistance, not initial tear. - Uses a pendulum to apply force; the energy lost during tearing is calculated to determine tear strength. - Equipped with a digital display for direct reading of results in grams or millinewtons. Core Components: - Pendulum Arm: Applies tearing force. - Clamps: Secure the sample before and after the tear. - Cutting Blade: Creates a precise slit at the start of the test. - Digital Display Unit: Shows the tearing force result clearly and instantly. - Counterweights: Optional weights for increasing test range (for stronger materials). Applications of Digital Elmendorf Tearing Tester: - Testing tear resistance of: - Textile fabrics (especially woven) - Paper and cardboard - Plastic films - Nonwovens - Packaging materials Benefits of Digital Elmendorf Tearing Tester:- Accurate Tear Strength Measurement - Provides precise data on tear resistance, critical for quality control and product performance.
- Digital Readout - Easy-to-read display gives instant, reliable results without manual calculations.
- High Reproducibility - Ensures consistent test outcomes due to controlled tearing angle and speed.
- Fast Testing Process - Simple loading and quick test cycle increase lab efficiency.
- Suitable for Various Materials - Tests a wide range of flexible materials like textiles, paper, plastic, and packaging.
- Customizable Range - Use of optional weights extends the test range for low to high tear strength materials.
- Low Sample Waste - Requires small fabric or material samples, reducing waste during testing.
- Standards Compliance - Meets international testing standards (e.g., ASTM D1424, ISO 13937) for credibility and uniformity.
- Precision Sample Clamp - Securely holds samples in place to ensure accurate tear initiation.
- Pre-Cutting Blade - Integrated knife creates a precise initial slit in the sample before tearing.
- User-Friendly Interface - Simple buttons and screen navigation for ease of operation.
- Standard Test Compliance - Compatible with ASTM D1424, ISO 1974, ISO 13937, and other tear strength standards.
- Sturdy Construction - Made with durable materials for long-lasting performance and stable operation.
- Compact Design - Space-efficient footprint ideal for laboratory environments.
- Data Output Options- Some models offer USB or printer connectivity for result documentation.
- Prepare the Sample - Cut the material (fabric, paper, film, etc.) to standard size (typically 100 × 63 mm for textiles) and slit it with the pre-cutter as required.
- Select Pendulum Weight - Choose the appropriate pendulum or add counterweights based on expected tear strength.
- Calibrate the Machine - Set the pendulum to its starting position and zero the display.
- Clamp the Sample - Fix one half of the sample in the stationary clamp and the other in the moving clamp.
- Cut the Initial Slit - Use the integrated blade to make a precise cut at the marked slit area (usually 20 mm).
- Release the Pendulum - Trigger the pendulum to swing and tear the sample through the pre-slit.
- Read the Result - The digital display will show the tearing force automatically (in g, mN, or cN).
- Record or Export Data - Save or print the result if your model supports USB or printer connection.
- Reset for Next Test - Reposition the pendulum and prepare a new sample for the next cycle.

Rainin Digital Pipette
Rainin Digital Pipette
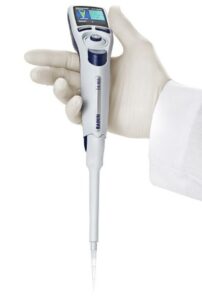
Digital Pipette
- Digital Volume Setting
- High Accuracy and Precision
- Ergonomic Design
- Easy Calibration and Maintenance
- Durable and Chemically Resistant - Built with high-quality materials that resist damage from chemicals and frequent use.
- Models and Volume Ranges - Available in single-channel and multi-channel versions.
- LTS (LiteTouch System) - Many Rainin pipettes use the LTS tip system which reduces tip ejection force and ensures a consistent seal.
- Compliance and Traceability - Some digital models offer data storage or integration with lab information systems for traceability.
- High Accuracy and Precision - Ensures reliable and reproducible results, essential for sensitive experiments.
- Digital Volume Control - Reduces human error with easy and precise volume setting via digital interface.
- Ergonomic Design- Minimizes hand strain and fatigue during prolonged use; ideal for repetitive pipetting tasks.
- LiteTouch System (LTS) - Eases tip attachment and ejection, reducing risk of RSI (Repetitive Strain Injury) and improving comfort.
- Versatile Volume Range - Available in multiple models to handle volumes from microliters to milliliters.
- Durable and Reliable - Built with high-quality materials for long life and resistance to chemicals and frequent use.
- Easy Maintenance and Calibration - Simplified calibration and cleaning ensure long-term performance and compliance.
- Data Integrity and Traceability -Some models store data, supporting audit trails and regulatory compliance.
- Enhanced Productivity - Quick setup, easy operation, and consistent performance speed up lab workflows.
- Digital Volume Adjustment - Precise and easy-to-read digital display for accurate volume setting.
- High Precision and Accuracy- Delivers consistent results, meeting ISO and GLP/GMP standards.
- Ergonomic Design- Lightweight, balanced with low plunger and tip ejection force to reduce fatigue.
- LiteTouch Tip Ejection System (LTS) - Reduces tip attachment/ejection force, improving comfort and consistency.
- Durable Construction - Built with high-quality, chemically resistant materials for long-term use.
- Wide Volume Range - Available in multiple models from 0.1 µL to 10 mL.
- Single-Channel and Multi-Channel Options - Suitable for various applications including high-throughput assays.
- Autoclavable Components- Some parts can be autoclaved for sterilization and contamination control.
- Easy Calibration and Maintenance - User-friendly calibration settings with accessible parts for cleaning.
- Optional Electronic Models - Some versions include programmable features, multiple modes (e.g., reverse pipetting), and memory storage.
Steam Soaping machine
Steam Soaping Machine
A Steam Soaping Machine is a specialized laboratory apparatus used in textile dyeing processes, particularly for post-dyeing treatments like soaping, which enhances color fastness and removes unfixed dyes from fabric samples. This machine is designed to perform soaping treatments on dyed textile samples using steam. Soaping is a critical step in dyeing, especially for reactive dyes, as it removes unfixed dye particles, ensuring better color fastness and preventing dye bleeding. The steam soaping process involves treating the dyed fabric with a soaping solution at elevated temperatures, facilitated by steam, to achieve optimal results. ⚙️ Key Features of Steam Soaping Machine - Beaker Material: Constructed with high-grade 316L stainless steel for excellent corrosion resistance and durability.- Operation Modes: Offers both automatic control and manual water filling options, providing flexibility in operation. - Drainage System: Equipped with an automatic drainage device for efficient removal of used solutions.- Temperature Control: Precise temperature regulation to maintain optimal soaping conditions.- Compact Design: Suitable for laboratory settings, occupying minimal space while delivering effective performance. ✅ Benefits of Steam Soaping Machine - Enhanced Color Fastness: Effectively removes unfixed dyes, resulting in improved wash and rub fastness of the fabric.- Efficient Processing: Reduces the time required for post-dyeing treatments compared to conventional methods.- Consistent Results: Provides uniform treatment across samples, ensuring reproducibility in testing and quality control.- Resource Optimization: Minimizes water and chemical usage through controlled processing parameters.- Versatility: Applicable to various fabric types and dye classes, making it a valuable tool in research and development. Typical Applications - Laboratory Testing: Used in dyeing laboratories for evaluating the fastness properties of dyed samples. - Research and Development: Assists in developing and optimizing dyeing processes and formulations. - Quality Control: Ensures that dyed fabrics meet specified fastness standards before bulk production. In summary, a Steam Soaping Machine is an essential laboratory instrument in the textile industry, facilitating efficient and effective post-dyeing treatments to enhance the quality and durability of dyed fabrics. Features of Steam Soaping Machine:- High-Grade Stainless Steel Beakers - Made from 316L stainless steel for excellent chemical and heat resistance.
- Steam-Based Heating - Uses direct or indirect steam to maintain consistent high temperatures ideal for soaping.
- Precise Temperature Control - Maintains stable temperatures (typically up to 98–100°C) for effective removal of unfixed dyes.
- Automatic and Manual Modes - Offers both programmable automatic cycles and manual operation for flexibility.
- Beaker Agitation or Rotation - Ensures uniform soaping action across fabric surfaces.
- Automatic Drainage System - Efficiently removes used soaping solution to speed up cycle changeovers.
- Compact Design - Fits well in lab settings while allowing multiple samples to be processed simultaneously.
- Safety Features - Includes pressure and temperature protection systems to ensure safe operation.
- Low Water and Chemical Use - Designed for minimal liquor ratios, enhancing sustainability.
- User-Friendly Interface - Simple digital controls or touch panel for easy operation and cycle programming.
- Prepare the Dyed Sample - After dyeing, rinse the fabric to remove surface dye and prepare it for soaping.
- Load the Fabric - Place the dyed fabric or sample into the beakers or holders inside the machine.
- Add Soaping Solution - Pour the prepared soaping agent (usually a detergent solution) into the beakers or tank as per recipe.
- Set Parameters
- Start the Cycle - Begin the soaping process. The machine will heat the solution using steam and agitate/rotate the beakers for even treatment.
- Drain and Rinse - After the cycle ends, the machine may auto-drain. Rinse the fabric with warm water to remove residual chemicals.
- Unload the Samples - Carefully remove the fabric. Inspect for evenness and color fastness improvement.
- Clean the Machine - Rinse and dry the beakers or tank to maintain hygiene for the next use.
