Fabric flame retardant tester
$0.00
Fabric Flame Retardant Tester
A Fabric Flame Retardant Tester is a specialized laboratory instrument designed to evaluate the flammability characteristics of textiles. It assesses how fabrics react to direct flame exposure, measuring parameters such as ignition time, flame spread rate, after-flame duration, and afterglow time. This testing is crucial for ensuring that textiles meet safety standards for various applications, including apparel, home furnishings, and industrial uses.
Purpose and Applications
The primary purpose of a Fabric Flame Retardant Tester is to determine the flame resistance of textile materials. This is essential for:- Apparel Safety: Ensuring garments, especially children’s sleepwear and industrial work wear, meet flammability standards.
– Home Textiles: Testing curtains, drapes, upholstery, and bedding for fire safety compliance.
– Technical Textiles: Evaluating materials used in tents, protective clothing, and automotive interiors.
⚙️ Key Features
Modern Fabric Flame Retardant Testers incorporate several features to ensure accurate and reliable testing:- Adjustable Burner Angles: Allowing tests at various orientations (e.g., 0°, 45°, 90°) to simulate different real-world scenarios.
Automated Ignition Systems: Providing consistent flame application and reducing operator variability.
– Digital Timing Mechanisms: Accurately recording ignition time, flame spread, after-flame, and afterglow durations.
– Transparent Observation Windows: Enabling safe monitoring of the test without exposure to hazards.
– Compliance with International Standards: Meeting protocols such as ASTM D6413, ISO 6941, and EN ISO 15025 for standardized testing procedures.
Testing Standards
Fabric Flame Retardant Testers are designed to comply with various international standards, including:
– ASTM D6413: Standard Test Method for Flame Resistance of Textiles (Vertical Test).
– ISO 6941: Textiles — burning behavior — Measurement of flame spread properties of vertically oriented specimens.
– EN ISO 15025: Protective clothing — Protection against heat and flame — Method of test for limited flame spread.
️ How It Works
- Sample Preparation: A fabric specimen is cut to specified dimensions and conditioned as per standard requirements.
- Mounting: The sample is mounted vertically or at a specified angle in the testing chamber.
- Ignition: A controlled flame is applied to the fabric for a predetermined time.
- Observation: The tester records ignition time, flame spread, after-flame time, and afterglow time.
- Evaluation: Results are compared against standard criteria to determine compliance.
✅ Benefits
– Safety Assurance: Ensures textiles meet fire safety regulations, reducing risk in end-use applications.
– Quality Control: Identifies flammability issues during the manufacturing process.
– Regulatory Compliance: Helps manufacturers meet legal requirements for flammability.
– Product Development: Assists in developing flame-retardant materials for specialized applications.
For more detailed information on specific models and their features, you can refer to manufacturers like SDL Atlas’s Auto Flam Flammability Tester [1], TESTEX’s Vertical Flammability Chamber TF312
How to Use a Fabric Flame Retardant Tester (Vertical Flammability Test Method):
- Prepare the Sample
– Cut the fabric to standard dimensions (usually 300 × 75 mm).
– Condition the fabric for 24 hours at 21°C and 65% relative humidity.
- Mount the Sample
– Place the fabric vertically in the frame inside the test chamber.
– Ensure it’s held securely with no folds or slack.
- Set Up the Burner Position the burner at the required angle (usually 90° for vertical tests).
– Adjust flame size according to the standard (about 38 mm for ASTM D6413).
- Ignite the Flame – Apply the flame to the bottom edge of the fabric for 12 seconds.
- Observe and Measure – Start timing when flame is applied.
– Measure:
– After-flame time (how long it burns after flame removal)
– After-glow time (how long it glows after burning stops)
– Char length (distance burned vertically)
- Record the Results
– Repeat the test on multiple samples (usually 5) and calculate averages.
- Compare with Standards
– Evaluate whether the results meet the required flame resistance limits.
fabric flame retardant tester IV type (small 450 method)
Scope of application
It is used for testing the intensity and speed of
burning of flammable textile materials after ignition.
(specific ignition nozzles and sample holders can be customized to meet multiple criteria).
Related standards
GB/T14644 ASTM D1230 CFR1610 etc.
Technical parameters
1. The spread of time:0 ~ 999.9S resolution 0.1S
2. The temperature inside the box shows:Room temperature -99 degrees C resolution 1 c
3. Igniting time:1S
4. Type of igniter:4 1/2 syringe
5. Sample clip size:Outer frame:204mm * 78mm inner frame:152mm×38mm
6. Distance from the top of the igniter to the sample surface:8mm
7. Studio size and outline size
Studio size:370mm×220mm×350mm
Outline size:375mm×245mm×478mm
8. Power supply:AC220V 50Hz 20W
9. Weight:18Kg
Related products
Pantone book
Pantone Book

Pantone Book
- Formula Guide (Solid Coated & Uncoated) – For spot color printing.
- Color Bridge – Shows Pantone spot colors alongside CMYK equivalents.
- Pantone Fashion, Home + Interiors (FHI) – For textiles, soft goods, and home decor.
- Pantone CMYK and Pastels & Neons Guides – For process printing and special effect colors.
- Formula Guide (Solid Coated & Uncoated)
- Color Bridge Guide (Coated & Uncoated)
- CMYK Guide (Coated & Uncoated)
- Pastels & Neons Guide
- Metallics Guide
- FHI Color Guide (TPG – Paper)
- FHI Cotton Passport & Cotton Planner (TCX – Textile)
- FHI Polyester Swatch Book
- Pantone SkinTone Guide
- Pantone Plastic Standard Chips

Pantone Book
Laboratory Padder
Laboratory Padder
A Laboratory Padder is a compact, laboratory-scale machine used to apply liquids like dyes, chemicals, and finishes to fabric samples. It simulates the padding process in textile manufacturing, where fabric is passed through a liquid solution, then squeezed between rollers to ensure uniform application and absorption. Key Features of a Laboratory Padder:- Adjustable Rollers - The fabric is passed through two or more rollers to apply even pressure and squeeze out excess solution, ensuring uniform chemical or dye application.
- Variable Pressure Control - Allows adjustment of roller pressure for different fabric types and chemical formulations, ensuring optimal penetration without damage.
- Solution Bath - Holds the liquid (e.g., dye, finish, or other chemical treatments) in a bath through which the fabric is dipped before passing through the rollers.
- Fabric Speed Control - Adjustable conveyor speed allows for control over the time the fabric spends in contact with the liquid solution, affecting the degree of treatment.
- Digital Control Panel - Provides easy adjustment of pressure, speed, and solution volume to ensure precise and reproducible results.
- Compact Design - Smaller, lab-scale version of industrial padders, ideal for research, development, and small-scale testing.
- Safety Features - Safety guards, emergency stops, and proper handling mechanisms to prevent accidents during operation.
- Precise Application of Chemicals - Provides uniform and controlled application of dyes, finishes, and other chemicals, ensuring consistent results.
- Small-Scale Testing - Ideal for small sample testing, allowing for fabric treatment without needing full-scale production equipment.
- Versatile Use - Suitable for dyeing, finishing, and applying various chemical treatments, making it a flexible tool for R&D labs.
- Cost-Effective - Reduces the need for large-scale machinery and the associated costs, while providing reliable results for small batches.
- Controlled Fabric Treatment - Offers adjustable pressure, speed, and solution concentration, enabling fine-tuned processing for different fabric types and applications.
- Accelerates Development - Speeds up the testing and development of new products or finishes, improving time-to-market for textile manufacturers.
- Energy Efficient - Consumes less energy compared to larger, industrial-scale machines, making it suitable for lab use.
- Compact and Space-Saving - Designed for laboratory environments with limited space, without compromising on functionality.
- Reproducible Results - Ensures consistent application of treatments across multiple samples, aiding in accurate testing and comparison.
- Adjustable Roller Pressure - Allows precise control over the pressure applied to the fabric, ensuring uniform chemical or dye application.
- Variable Speed Control - Adjustable conveyor speed for controlling the time the fabric spends in the solution bath, influencing the absorption rate.
- Solution Bath - Holds dye, chemicals, or finishes, and the fabric passes through this bath before moving to the rollers.
- Digital Control Panel - Easy-to-use interface for setting and adjusting parameters like speed, pressure, and solution concentration.
- Compact and Lab-Friendly Design - Designed for smaller, space-efficient use in textile labs, allowing for small sample testing.
- Roller Gap Adjustment - Allows for fine-tuning of the gap between rollers to regulate the amount of solution squeezed out of the fabric.
- Stainless Steel Construction - Durable and resistant to corrosion from the chemicals used in textile treatments.
- Safety Mechanisms - Includes safety guards, emergency stops, and user protection features during operation.
- Even and Controlled Application - Ensures even distribution of treatments (dye, finish, etc.) on fabric with minimal waste.
- Versatility in Application - Can be used for a wide range of textiles and treatments, including dyeing, softening, flame-retardant treatments, etc.
- Prepare the Fabric Sample - Cut the fabric sample to the required size for the experiment. Ensure it’s clean and free of any debris.
- Prepare the Solution - Mix the dye, chemical, or finish solution according to the desired concentration and the fabric's needs. Ensure that the solution is homogeneous.
- Set the Parameters - Pressure: Adjust the roller pressure based on the fabric type. Different fabrics require different pressure levels to ensure uniform application. - Speed: Set the fabric conveyor speed depending on the desired treatment time (longer exposure for deeper treatment).
- Load the Fabric into the Machine - Place the fabric carefully into the machine. The fabric should go through the solution bath and then pass between the rollers.
- Start the Machine - Turn on the machine and allow the fabric to pass through the rollers. The solution will be evenly applied to the fabric as it moves through the bath and is squeezed by the rollers.
- Monitor the Process - Keep an eye on the fabric to ensure it is being treated uniformly and there are no blockages or fabric jams.
- Unload the Fabric - Once the fabric has been treated, carefully remove it from the machine. Inspect for even application of the solution and any excess liquid.
- Dry or Process Further - Depending on the treatment, proceed with further steps such as drying, heat setting, or curing, as required by the experiment or process.

Mini Lab Dyeing Padder
Oscillation type water bath Dyeing Machine
Oscillation Type Water Bath Dyeing Machine
An Oscillation Type Water Bath Dyeing Machine is a laboratory apparatus designed for dyeing and washing textile samples under controlled temperature conditions. It combines a heated water bath with an oscillating mechanism to ensure uniform dye penetration and consistent coloration across fabric or yarn samples. Key Features of Oscillation Type Water Bath Dyeing Machine - Oscillating Mechanism: Provides back-and-forth movement to agitate the dye solution, ensuring even contact between the dye and the textile sample.- Multiple Beaker Capacity: Typically accommodates 12 to 24 beakers, allowing simultaneous processing of multiple samples under identical or varied conditions. - Digital Temperature Control: Maintains precise temperature settings, usually up to 99°C, suitable for various dyeing processes including atmospheric dyeing, scouring, and bleaching.- Adjustable Oscillation Speed: Offers variable speed settings, commonly ranging from 50 to 200 cycles per minute, to accommodate different fabric types and dyeing requirements. - Programmable Settings: Advanced models come with programmable controllers, allowing users to set and save multiple dyeing protocols for repeatability and efficiency. Durable Construction: Constructed with high-quality stainless steel (e.g., SUS304), ensuring resistance to corrosion and longevity even under rigorous laboratory conditions. ✅ Benefits of Oscillation Type Water Bath Dyeing Machine - Uniform Dyeing Results: The oscillation mechanism ensures consistent dye penetration, reducing the risk of uneven coloration and enhancing the reproducibility of results.- Efficiency in Sample Processing: The ability to process multiple samples simultaneously accelerates laboratory workflows and facilitates comparative studies. - Versatility: Suitable for a range of applications including dyeing, washing, scouring, bleaching, and fastness testing across various textile materials.- Energy and Resource Conservation: Designed for low liquor ratios (e.g., 1:5 to 1:20), these machines minimize water and chemical usage, promoting sustainable laboratory practices. - Enhanced Safety and Cleanliness: Enclosed beaker systems reduce the risk of spills and exposure to chemicals, ensuring a safer laboratory environment. Typical Applications of Oscillation Type Water Bath Dyeing Machine - Textile Research and Development: Ideal for developing and testing new dye formulations and processes on a small scale before scaling up to production levels. Quality Control: Used in quality assurance laboratories to assess color fastness, dye uptake, and other critical parameters of textile products.- Educational Purposes: Serves as a practical tool in academic settings for teaching dyeing principles and techniques. In summary, the Oscillation Type Water Bath Dyeing Machine is an essential tool in textile laboratories, offering precise control over dyeing parameters, improving efficiency, and ensuring high-quality, reproducible results across various textile materials. Features of Oscillation Type Water Bath Dyeing Machine:- Oscillating Mechanism - Provides back-and-forth movement of beakers for uniform dye penetration and sample agitation.
- Multiple Beaker Capacity - Supports dyeing of 12–24 samples simultaneously, ideal for comparative lab testing.
- Digital Temperature Control - Maintains precise water bath temperature (typically up to 99°C), essential for consistent dyeing.
- Variable Oscillation Speed - Adjustable speed settings (e.g., 50–200 cycles/min) to suit different materials and processes.
- Programmable Settings - Allows setting of temperature, time, and speed for repeatable and automated dyeing cycles.
- Stainless Steel Construction - Corrosion-resistant frame and bath for durability in chemical environments.
- Beaker Safety Holders - Secure placement of beakers to prevent spills and maintain consistent treatment.
- Compact Design - Lab-friendly size for easy integration into research and quality control spaces.
- Low Liquor Ratio Operation - Efficient dyeing using minimal dye bath volume (e.g., 1:5 to 1:20), reducing chemical and water use.
- Quiet and Stable Performance

water bath/Shaker bath Dyeing machine
Fiber Oil Fast Extractor
Fiber Oil Fast Extractor
A Fiber Oil Fast Extractor is a laboratory instrument designed to determine the oil or finish content in fibers, yarns, or fabrics, particularly wool and synthetic materials. It operates on the principle of solvent extraction followed by evaporation. Working Principle of Fiber Oil Fast Extractor:- Sample Preparation: Cut the fabric or fiber into small pieces.
- Solvent Addition: Place the sample into a metal tube and add an appropriate solvent (e.g., petroleum ether, ethyl ether).
- Extraction: Apply weight to the sample to facilitate the dissolution of oils into the solvent.
- Evaporation: The solvent-oil mixture drips onto a heated plate where the solvent evaporates, leaving behind the oil.
- Measurement: Weigh the remaining oil and calculate its percentage relative to the initial sample mass.
- Accurate Oil Content Measurement- Precisely determines oil or finish content in fibers, crucial for quality control.
- Rapid Extraction Process - Delivers fast results, improving lab efficiency and productivity.
- Simultaneous Multi-Sample Testing - Multiple workstations (e.g., 4 at once) reduce testing time for bulk samples.
- Improved Product Quality - Helps maintain consistent oil levels, which affect dyeing, processing, and fabric performance.
- Automatic Operation - Automated pressing and heating reduce manual effort and operator error.
- Digital Monitoring - Built-in timer, temperature control, and oil calculator enhance accuracy and usability.
- Compliance with Standards - Supports industry methods like GB/T 6504-2017, ensuring reliable and standard-compliant results.
- Safe Solvent Handling - Enclosed design minimizes solvent exposure and evaporation loss.
- Multiple Test Stations - Usually equipped with 2 to 4 independent work units for parallel testing.
- Automatic Weight Pressing System - Applies consistent pressure on samples for uniform solvent extraction.
- Microcomputer Temperature Control - Maintains precise heating (typically 90–120°C) with ±1°C accuracy.
- Built-in Timer and Calculator - Allows setting extraction time and calculates oil content directly.
- Solvent Evaporation Plate- Heats and evaporates solvent quickly, leaving only the oil residue.
- Digital Display - Shows time, temperature, and process status for user-friendly operation.
- Compact and Durable Design - Made with corrosion-resistant materials suited for chemical handling.
- Safety Features - Includes overheat protection and enclosed solvent chamber to reduce exposure risk.
- Standard Compliant - Designed to meet GB/T 6504-2017 and similar industry testing standards.
- Prepare the Sample - Cut 5–10 g of fiber or yarn into small pieces and place in the sample tube.
- Add Solvent - Pour a suitable solvent (e.g., petroleum ether) into the tube to cover the sample.
- Apply Weight - Place the extractor's weight or press system onto the sample to aid extraction.
- Start Extraction - Activate the machine. The solvent dissolves the oils and flows to the heating plate.
- Heat for Evaporation - Set the temperature (typically 90–120°C). The solvent evaporates, leaving oil on the plate.
- Measure Oil Content- After drying, weigh the remaining oil. Use the built-in calculator or formula:
- Clean the Unit - After cooling, clean all parts to prepare for the next test.
Fiber Oil Fast Extractor
Digital hot plate-magnetic stirrer
Digital hot plate-magnetic stirrer
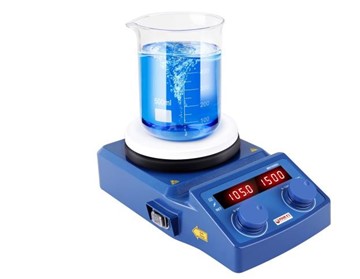
Digital hot plate-magnetic stirrer
- Magnetic Stirrer:
- Digital Display and Controls:
- Temperature Sensors: - Built-in or external probes (like a PT100 or thermocouple) for accurate temperature control.
- Precision and Control- Digital Interface: Allows accurate setting and monitoring of temperature and stirring speed.- Consistent Results: Ensures reproducibility in experiments and solution preparations.
- Efficient Mixing and Heating- Uniform Mixing: Magnetic stirring eliminates hotspots and ensures even distribution of solutes.- Simultaneous Operation: Ability to heat and stir at the same time improves efficiency.
- Safety Features- Overheat Protection: Prevents accidents by automatically shutting off at unsafe temperatures.- Sealed Surface: Reduces risk of contamination and easy to clean.
- Versatility
- Compact and User-Friendly- Takes up minimal bench space.- Simple to operate with user-friendly controls and displays.
- Durability- High-quality materials like ceramic or stainless steel tops resist corrosion and wear.
- Time-Saving Speeds up preparation of solutions and reactions compared to manual stirring and separate heating. Would you like these benefits presented in a slide format or for a product brochure?
Steam Soaping machine
Steam Soaping Machine
A Steam Soaping Machine is a specialized laboratory apparatus used in textile dyeing processes, particularly for post-dyeing treatments like soaping, which enhances color fastness and removes unfixed dyes from fabric samples. This machine is designed to perform soaping treatments on dyed textile samples using steam. Soaping is a critical step in dyeing, especially for reactive dyes, as it removes unfixed dye particles, ensuring better color fastness and preventing dye bleeding. The steam soaping process involves treating the dyed fabric with a soaping solution at elevated temperatures, facilitated by steam, to achieve optimal results. ⚙️ Key Features of Steam Soaping Machine - Beaker Material: Constructed with high-grade 316L stainless steel for excellent corrosion resistance and durability.- Operation Modes: Offers both automatic control and manual water filling options, providing flexibility in operation. - Drainage System: Equipped with an automatic drainage device for efficient removal of used solutions.- Temperature Control: Precise temperature regulation to maintain optimal soaping conditions.- Compact Design: Suitable for laboratory settings, occupying minimal space while delivering effective performance. ✅ Benefits of Steam Soaping Machine - Enhanced Color Fastness: Effectively removes unfixed dyes, resulting in improved wash and rub fastness of the fabric.- Efficient Processing: Reduces the time required for post-dyeing treatments compared to conventional methods.- Consistent Results: Provides uniform treatment across samples, ensuring reproducibility in testing and quality control.- Resource Optimization: Minimizes water and chemical usage through controlled processing parameters.- Versatility: Applicable to various fabric types and dye classes, making it a valuable tool in research and development. Typical Applications - Laboratory Testing: Used in dyeing laboratories for evaluating the fastness properties of dyed samples. - Research and Development: Assists in developing and optimizing dyeing processes and formulations. - Quality Control: Ensures that dyed fabrics meet specified fastness standards before bulk production. In summary, a Steam Soaping Machine is an essential laboratory instrument in the textile industry, facilitating efficient and effective post-dyeing treatments to enhance the quality and durability of dyed fabrics. Features of Steam Soaping Machine:- High-Grade Stainless Steel Beakers - Made from 316L stainless steel for excellent chemical and heat resistance.
- Steam-Based Heating - Uses direct or indirect steam to maintain consistent high temperatures ideal for soaping.
- Precise Temperature Control - Maintains stable temperatures (typically up to 98–100°C) for effective removal of unfixed dyes.
- Automatic and Manual Modes - Offers both programmable automatic cycles and manual operation for flexibility.
- Beaker Agitation or Rotation - Ensures uniform soaping action across fabric surfaces.
- Automatic Drainage System - Efficiently removes used soaping solution to speed up cycle changeovers.
- Compact Design - Fits well in lab settings while allowing multiple samples to be processed simultaneously.
- Safety Features - Includes pressure and temperature protection systems to ensure safe operation.
- Low Water and Chemical Use - Designed for minimal liquor ratios, enhancing sustainability.
- User-Friendly Interface - Simple digital controls or touch panel for easy operation and cycle programming.
- Prepare the Dyed Sample - After dyeing, rinse the fabric to remove surface dye and prepare it for soaping.
- Load the Fabric - Place the dyed fabric or sample into the beakers or holders inside the machine.
- Add Soaping Solution - Pour the prepared soaping agent (usually a detergent solution) into the beakers or tank as per recipe.
- Set Parameters
- Start the Cycle - Begin the soaping process. The machine will heat the solution using steam and agitate/rotate the beakers for even treatment.
- Drain and Rinse - After the cycle ends, the machine may auto-drain. Rinse the fabric with warm water to remove residual chemicals.
- Unload the Samples - Carefully remove the fabric. Inspect for evenness and color fastness improvement.
- Clean the Machine - Rinse and dry the beakers or tank to maintain hygiene for the next use.

Digital Elmendorf tearing tester
Digital Elmendorf Tearing Tester
Digital Elmendorf Tearing Tester is a precision instrument used to measure the tear strength of materials like woven fabrics, paper, plastic films, and nonwovens. It determines how much force is required to continue tearing a pre-slit sample. Key Functions of Digital Elmendorf Tearing Tester: - Measures propagation tear resistance, not initial tear. - Uses a pendulum to apply force; the energy lost during tearing is calculated to determine tear strength. - Equipped with a digital display for direct reading of results in grams or millinewtons. Core Components: - Pendulum Arm: Applies tearing force. - Clamps: Secure the sample before and after the tear. - Cutting Blade: Creates a precise slit at the start of the test. - Digital Display Unit: Shows the tearing force result clearly and instantly. - Counterweights: Optional weights for increasing test range (for stronger materials). Applications of Digital Elmendorf Tearing Tester: - Testing tear resistance of: - Textile fabrics (especially woven) - Paper and cardboard - Plastic films - Nonwovens - Packaging materials Benefits of Digital Elmendorf Tearing Tester:- Accurate Tear Strength Measurement - Provides precise data on tear resistance, critical for quality control and product performance.
- Digital Readout - Easy-to-read display gives instant, reliable results without manual calculations.
- High Reproducibility - Ensures consistent test outcomes due to controlled tearing angle and speed.
- Fast Testing Process - Simple loading and quick test cycle increase lab efficiency.
- Suitable for Various Materials - Tests a wide range of flexible materials like textiles, paper, plastic, and packaging.
- Customizable Range - Use of optional weights extends the test range for low to high tear strength materials.
- Low Sample Waste - Requires small fabric or material samples, reducing waste during testing.
- Standards Compliance - Meets international testing standards (e.g., ASTM D1424, ISO 13937) for credibility and uniformity.
- Precision Sample Clamp - Securely holds samples in place to ensure accurate tear initiation.
- Pre-Cutting Blade - Integrated knife creates a precise initial slit in the sample before tearing.
- User-Friendly Interface - Simple buttons and screen navigation for ease of operation.
- Standard Test Compliance - Compatible with ASTM D1424, ISO 1974, ISO 13937, and other tear strength standards.
- Sturdy Construction - Made with durable materials for long-lasting performance and stable operation.
- Compact Design - Space-efficient footprint ideal for laboratory environments.
- Data Output Options- Some models offer USB or printer connectivity for result documentation.
- Prepare the Sample - Cut the material (fabric, paper, film, etc.) to standard size (typically 100 × 63 mm for textiles) and slit it with the pre-cutter as required.
- Select Pendulum Weight - Choose the appropriate pendulum or add counterweights based on expected tear strength.
- Calibrate the Machine - Set the pendulum to its starting position and zero the display.
- Clamp the Sample - Fix one half of the sample in the stationary clamp and the other in the moving clamp.
- Cut the Initial Slit - Use the integrated blade to make a precise cut at the marked slit area (usually 20 mm).
- Release the Pendulum - Trigger the pendulum to swing and tear the sample through the pre-slit.
- Read the Result - The digital display will show the tearing force automatically (in g, mN, or cN).
- Record or Export Data - Save or print the result if your model supports USB or printer connection.
- Reset for Next Test - Reposition the pendulum and prepare a new sample for the next cycle.

Digital Bench top PH Meter
Digital Bench top PH Meter

Digital Bench top PH Meter
Brand: Hanna Model: HI2002 Country of Manufacture: Romania Origin: USA
Digital Bench top PH Meter
Single parameter of Digital Bench top PH Meter features user-friendly tablet design with bench, portable or wall mount options for ultimate flexibility. Switch from portable to bench in the same procedure or clear the surface for easier working and hang on the wall. Digital Bench top PH Meter Range -2.00 to 16.00pH; pH Digital smart electrode compatible Accuracy: ±0.01 pH edge® pH is dedicated to testing pH. Using Hanna's latest innovation in technology and design, edge® can be adapted to suit your working method. Select from hand held, wall mount or bench top - or switch between them all. edge® is happy any which way. Simply plug in the electrode, then play. Measurement is simpler, quicker and more accurate than ever. Results are fast and reliable. Combining high precision technology with the user-friendly dimensions and format of a small digital tablet, edge® is breaking new ground in electrochemistry. This is a must-have meter for your laboratory.pH Range | basic mode: -2.00 to 16.00 pH; standard mode: -2.000 to 16.000 pH | |
Resolution | basic mode: 0.01 pH; standard mode: 0.001 pH | |
Accuracy (@25°C) | basic mode: ±0.01 pH; standard mode: ±0.002 pH | |
Calibration | basic mode: automatic, up to three points calibration, 5 standard buffers available; standard mode: automatic, up to five point calibration, 7 standard buffers available and two custom buffers | |
Temperature Compensation | automatic, -5.0 to 100.0°C (using integral temperature sensor) | |
Electrode Diagnostics | standard mode: probe condition, response time and out of calibration range | |
mV pH Range | ±1000 mV | |
Resolution | 0.1 mV | |
Accuracy (@25°C) | ±0.2 mV | |
ORP Range | ±2000 mV | |
Resolution | 0.1 mV | |
Accuracy (@25°C) | ±0.2 mV | |
Temperature Range | -20.0 to 120.0°C | |
Resolution | 0.1°C | |
Accuracy | ±0.5°C | |
Additional Specifications: | ||
Probe | HI-11310 digital glass body pH electrode with 3.5mm connector and 1m cable | |
Logging | up to 1000 (400 for basic mode) records organised in: manual log-on demand (max. 200 logs), manual log-on-stability (max. 200 logs), interval logging (max. 600 samples; 100 lots) | |
Connectivity | 1 USB port for storage; 1 micro USB port for charging and PC connectivity | |
Environment | 0 to 50°C; RH max 95% non-condensing | |
Power Supply | 5 VDC adapter (included) | |
Dimensions | 2020 x 140 x 12 mm | |
Weight | 250 g |
- High Accuracy and Resolution
- Digital Display - Large, clear LCD or LED screen shows pH readings, temperature, and sometimes mV or ion concentration. - Some models include a backlit display for better visibility.
- Electrode System - Uses a pH-sensitive electrode (usually glass) connected to a reference electrode. Electrodes are often replaceable and require regular calibration and maintenance.
- Temperature Compensation - Automatic or manual temperature compensation to correct pH readings based on sample temperature. - Integrated temperature sensors or separate probes are used.
- Calibration Functions - Supports 2-point, 3-point, or multi-point calibration using standard buffer solutions. - Auto-recognition of calibration buffers in advanced models.
- Data Storage and Connectivity - Internal memory for storing results. - USB or RS232 ports for data export to PCs or printers; some models support wireless connectivity.
- Sturdy Design - Benchtop models are larger and more stable than portable meters. - Often come with a durable casing and electrode arm for hands-free operation.
- High Accuracy and Precision
- User-Friendly Interface- Digital displays (LCD/LED) make readings easy to see and interpret.- Many models offer intuitive controls and guided calibration, simplifying operation.
- Advanced Calibration Features- Supports multi-point calibration for improved accuracy across a wide pH range.- Some models automatically recognize buffer solutions, reducing user error.
- Temperature Compensation- Automatic temperature compensation (ATC) corrects readings based on sample temperature, ensuring accuracy.
- Stable and Durable Design- Benchtop units are more robust and stable than handheld devices, reducing the risk of spills or tipping.- Often include electrode holders or arms for secure, hands-free measurements.
- Data Management and Connectivity- Built-in memory for storing measurement data.USB, RS232, or wireless connectivity for exporting data to computers or laboratory information systems (LIS).
- Multi-Functionality- Some models also measure ORP (oxidation-reduction potential), ion concentration, or conductivity.- Suitable for a variety of testing needs beyond just pH.
- Ideal for Long-Term Use- Designed for prolonged and repeated use in laboratory environments.- Replaceable electrodes and parts extend the meter’s usable life.
- Compliance and Documentation- Data logging features support documentation and compliance with regulatory standards in regulated industries (e.g., pharma, food, environmental testing).