Digital Temperature Humidity Meter
$0.00
Digital Temperature Humidity Meter
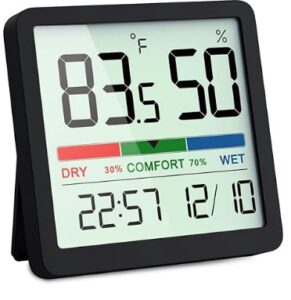
Digital Temperature Humidity Meter
A Digital Temperature Humidity Meter, also known as a digital hygrometer, is an electronic device used to measure and display the relative humidity (RH) of the air, often along with temperature. It’s commonly used in laboratories, industrial settings, storage areas, and homes to monitor moisture levels.
Key Features of Digital Temperature Humidity Meter:
– Digital Display: Shows humidity (in % RH) and often temperature (in °C/°F).
– Sensor-Based Measurement: Uses capacitive or resistive sensors for accurate readings.
– Compact & Portable: Available in handheld or wall-mountable forms.
– Data Logging (in some models): Records humidity levels over time for analysis.
– Min/Max Readings: Displays historical high and low humidity values.
Common Applications of Digital Temperature Humidity Meter:
– Laboratories: Maintaining stable humidity for experiments or sample storage.
– Warehouses: Monitoring conditions for sensitive goods (e.g., electronics, paper, pharmaceuticals).
– HVAC Systems: Ensuring proper climate control.
– Homes: Preventing mold growth or overly dry conditions.
Benefits of Digital Temperature Humidity Meter:
– Accurate and quick readings
– Easy to use and read
– Helps in maintaining comfort, safety, and product integrity
Would you like recommendations for models or guidance on calibration?
Benefits of Digital Humidity meter
Here are the key benefits of using a Digital Humidity Meter:
✅ 1. Accurate Humidity Monitoring
– Provides precise relative humidity (%RH) readings, essential for sensitive environments.
✅ 2. Fast and Real-Time Results
– Displays immediate data, allowing for quick adjustments to environmental conditions.
✅ 3. Dual Measurement
– Many models also measure temperature, offering a more complete picture of ambient conditions.
✅ 4. Easy to Use
– Simple digital interface with clear display, suitable for both professionals and non-technical users.
✅ 5. Compact and Portable
– Lightweight design makes it ideal for field use, indoor monitoring, or mounting on walls.
✅ 6. Prevents Damage
– Helps avoid moisture-related issues like mold, corrosion, static buildup, and product degradation.
✅ 7. Supports Quality Control
– Essential for labs, warehouses, and manufacturing environments to maintain product integrity.
✅ 8. Data Logging (Optional)
How to use Digital Humidity meter
Here are the key features of a Digital Humidity Meter:
1. Digital Display
– Shows real-time humidity (%) and often temperature (°C/°F).
– Some include backlit screens for easy viewing.
2. High Accuracy Sensors
– Uses capacitive or resistive sensors for accurate and stable humidity readings.
3. Min/Max & Hold Functions
– Displays minimum, maximum, and current readings.
– “Hold” function freezes the current reading for review.
4. Data Logging (in advanced models)
– Records humidity data over time for monitoring trends.
5. Portable or Wall-Mountable
– Available as handheld, desktop, or wall-mounted units for different environments.
6. Battery or USB Powered
– Operates on standard batteries or via USB power for flexibility.
7. Optional External Probes
– Some models support external humidity/temperature sensors for remote monitoring.
8. Calibration Option
– Allows manual or automatic calibration to maintain accuracy.
Here’s a quick step-by-step guide on how to use a Digital Temperature Humidity Meter:
✅ 1. Power On the Device
– Insert batteries (if portable) or plug it in (if wall-mounted).
– Press the power button to turn it on.
✅ 2. Place It Properly
– Set the meter in an open, well-ventilated area.
– Avoid placing near windows, vents, or direct heat sources for accurate readings.
✅ 3. Wait for Stabilization
– Allow the device a few seconds to stabilize and show accurate humidity and temperature readings.
✅ 4. Read the Display
– Humidity will be shown as % RH (Relative Humidity).
– Most models also display temperature in °C or °F.
✅ 5. Use Additional Features (if available)
– Press buttons to view Min/Max, Data Log, or switch units.
– Some advanced models may have Bluetooth or USB for data transfer.
✅ 6. Maintain the Device
– Clean sensor area gently if dusty.
– Calibrate periodically if required (check manual).
Related products
fabric moisture permeability tester
Fabric Moisture Permeability Tester
A Fabric Moisture Permeability Tester, also known as a Water Vapor Permeability Tester, is a laboratory instrument designed to measure the rate at which water vapor passes through textile materials. This measurement is crucial for assessing the breathability and comfort of fabrics, especially those used in active wear, outdoor gear, medical textiles, and protective clothing. Purpose of Fabric Moisture Permeability Tester The primary function of this tester is to evaluate a fabric's ability to allow moisture vapor to pass through it, which directly impacts the wearer's comfort by facilitating sweat evaporation and thermal regulation. High moisture permeability indicates better breathability, making the fabric suitable for applications where moisture management is essential. Working Principle of Fabric Moisture Permeability Tester The tester operates by placing a fabric specimen over a container filled with water. Under controlled temperature and humidity conditions, water vapor passes through the fabric over a specified period. The amount of water vapor transmitted is determined by measuring the weight loss of the container, allowing for the calculation of the Water Vapor Transmission Rate (WVTR). Common Testing Methods- Upright Cup Method: The fabric covers a cup containing water, and the assembly is placed upright in a controlled environment. After a set duration, the weight loss is measured to determine the WVTR.
- Inverted Cup Method: The fabric is sealed over a cup, which is then inverted and exposed to a controlled environment. The amount of water vapor absorbed by the fabric is measured over time.
- Sweating Hot Plate Test: Simulates human perspiration by measuring the energy required to maintain a constant temperature on a heated plate covered with the fabric, providing insights into the fabric's breathability.
- Multi-Cup Design - Typically includes 6 or more test cups for simultaneous testing of multiple samples.
- Rotating Turntable - Ensures uniform air exposure and consistent vapor transmission across all samples.
- Precision Weighing System- Accurate measurement of weight loss to calculate water vapor transmission rate (WVTR).
- Temperature & Humidity Control - Maintains stable environmental conditions (e.g., 23°C, 50% RH) for reliable results.
- Digital Display or Software Interface - Displays real-time data and test status; advanced models offer data logging and export.
- Compliance with Standards - Supports ASTM E96, ISO 15496, BS 7209, JIS L1099 testing methods.
- Sealed Test Chambers- Prevents external air interference, improving accuracy.
- Corrosion-Resistant Construction - Durable materials suitable for long-term use in lab environments.
- Easy Sample Mounting - Quick and secure fabric placement on test cups with sealing rings.
- Low Maintenance Design- Simplified components for easy cleaning and upkeep.
- Prepare the Test Solution - Fill each test cup with a set amount of water (e.g., 50 ml), or a desiccant if using inverted method.
- Mount the Fabric - Cut the fabric into circular pieces matching the cup size.
- Weigh the Cups - Record the initial weight of each cup with the fabric mounted.
- Place on Turntable - Position all cups on the rotating tray inside the controlled chamber.
- Set Conditions - Close the chamber and maintain temperature (e.g., 23°C) and relative humidity (e.g., 50%) as per test standard.
- Start the Test - Begin rotation (usually ~2 RPM) and let it run for the specified time (often 24 hours).
- Weigh the Cups Again- After the test duration, reweigh the cups to determine weight loss due to moisture vapor passing through the fabric.
- Calculate WVTR - Use the formula: WVTR = (Weight Loss in grams × 24) / (Test Area in m² × Time in hours) Expressed in g/m²/24h.
- Clean and Store - Clean cups and components for future use.

Perspiration Tester
Perspiration Tester

Perspiration Tester
- Fabric samples are treated with synthetic perspiration solution (acidic or alkaline).
- They are sandwiched with adjacent fabric and placed between glass or acrylic plates.
- The assembly is loaded into the tester and pressed under specific pressure.
- it’s then incubated at 37°C (body temperature) for a fixed time (typically 4 or 16 hours).
- Afterward, color change and staining are evaluated using a gray scale.
- Accurate Sweat Simulation - Mimics real-life effects of acidic and alkaline perspiration on fabrics.
- Improves Product Quality - Ensures textiles retain color and don’t bleed or stain when worn.
- Supports Standard Compliance - Follows ISO and AATCC test standards for global market approval.
- Protects Brand Reputation- Reduces customer complaints due to dye transfer or fading.
- Simple and Repeatable- Provides consistent pressure and conditions for reliable results.
- Multi-Sample Testing- Tests multiple specimens at once, saving time in labs.
- Durable and Low Maintenance- Robust frame with minimal moving parts makes it long-lasting and easy to care for.
- Stainless Steel Frame - Corrosion-resistant body for durability and long-term use.
- Multi-Sample Capacity - Can hold up to 20 or more specimens for batch testing.
- Standardized Loading Weight- Applies uniform pressure (usually 12.5 kPa) across all samples.
- Removable Plates - Glass or acrylic plates ensure even contact and easy cleaning.
- Compact Design- Space-saving, bench-top model ideal for lab environments.
- Complies with Test Standards - Meets ISO 105 E04, AATCC 15, and related perspiration fastness standards.
- Ease of Operation - Simple loading, unloading, and incubation process.
- High-Temperature Resistance - Can be used inside incubators at 37°C or ovens as required.
- Prepare the Test Solution - Mix artificial acidic or alkaline perspiration as per standard (ISO or AATCC).
- Cut the Fabric Samples - Cut both the test fabric and adjacent white fabric (usually cotton) to standard size.
- Soak the Samples - Immerse the fabric sandwich (test + adjacent) in the test solution for 30 minutes.
- Remove Excess Liquid - Gently squeeze or blot to remove extra moisture—do not dry.
- Load in the Tester- Place each sandwich between glass or acrylic separator plates in the tester.
- Apply Pressure - Tighten the top plate or place the standard weight on top to apply uniform pressure.
- Incubate - Keep the loaded tester in an oven or incubator at 37°C for 4–16 hours (depending on the method).
- Accurate Sweat Simulation - Mimics real-life effects of acidic and alkaline perspiration on fabrics.
- Improves Product Quality - Ensures textiles retain color and don’t bleed or stain when worn.
- Supports Standard Compliance - Follows ISO and AATCC test standards for global market approval.
- Protects Brand Reputation- Reduces customer complaints due to dye transfer or fading.
- Simple and Repeatable- Provides consistent pressure and conditions for reliable results.
- Multi-Sample Testing- Tests multiple specimens at once, saving time in labs.
- Durable and Low Maintenance- Robust frame with minimal moving parts makes it long-lasting and easy to care for.
- Dry and Evaluate - Remove, air dry the samples, then assess color change and staining using a gray scale.
- Fabric samples are treated with synthetic perspiration solution (acidic or alkaline).
- They are sandwiched with adjacent fabric and placed between glass or acrylic plates.
- The assembly is loaded into the tester and pressed under specific pressure.
- it’s then incubated at 37°C (body temperature) for a fixed time (typically 4 or 16 hours).
- Afterward, color change and staining are evaluated using a gray scale.
Perspiration Tester
Random Tumble Pilling Tester
Random Tumble Pilling Tester
The Random Tumble Pilling Tester is a specialized instrument designed to assess the pilling resistance of textile fabrics. Pilling refers to the formation of small, fuzzy balls (pills) on the fabric surface due to wear and friction. This tester simulates the wear conditions that fabrics experience during actual use, providing valuable data on their durability and appearance retention. Purpose of Random Tumble Pilling Tester The primary function of the Random Tumble Pilling Tester is to evaluate how fabrics resist pilling, fuzzing, and matting. This assessment is crucial for manufacturers aiming to ensure the longevity and aesthetic quality of their textile products. Working Principle of Random Tumble Pilling Tester The tester operates by placing fabric specimens into cylindrical test chambers lined with cork. Inside each chamber, a stainless steel impeller rotates at a high speed (typically around 1200 revolutions per minute), causing the fabric samples to tumble randomly. Compressed air is injected to enhance the tumbling action. This process simulates the friction and wear that fabrics undergo during regular use. After a predetermined duration, the samples are removed and visually assessed for pilling using standardized rating scales. Key Specifications of Random Tumble Pilling Tester Test Chambers: Available in configurations of 2 or 4 chambers to accommodate multiple samples simultaneously. - Rotation Speed: Approximately 1200 revolutions per minute. - Chamber Dimensions: Typically around 146 mm in diameter and 152 mm in length. - Impeller Size: Standard impellers measuring about 121 mm. - Compressed Air Pressure: Adjustable, commonly between 14–21 kPa (2–3 psi). - Timer: Digital timer allowing precise control over test duration. - Power Supply: Generally operates on 220V, 50Hz power sources. Applicable Standards of Random Tumble Pilling Tester The Random Tumble Pilling Tester complies with several international testing standards, ensuring its suitability for global applications:- ASTM D3512- ISO 12945-3- DIN 53867- JIS L 1076- GB/T 4802.4 Benefits of Random Tumble Pilling Tester - Realistic Simulation: Accurately replicates the wear and friction conditions fabrics face during actual use.- Standardized Testing: Adheres to international standards, facilitating consistent and comparable results.- Efficient Evaluation: Allows simultaneous testing of multiple samples, increasing laboratory throughput.- Quality Assurance: Provides manufacturers with critical data to improve fabric formulations and production processes. User-Friendly Operation: Features intuitive controls and clear viewing windows for easy monitoring. Applications of Random Tumble Pilling Tester The Random Tumble Pilling Tester is widely used in various sectors of the textile industry: - Apparel Manufacturing: Assessing the durability of clothing fabrics. - Home Textiles: Evaluating materials used in upholstery, curtains, and bedding. - Quality Control Laboratories: Routine testing to ensure product consistency and compliance with standards.- Research and Development: Developing new fabrics with enhanced resistance to pilling. Features of Random Tumble Pilling Tester:- Multiple Test Chambers - Typically comes with 2 or 4 cork-lined chambers for simultaneous testing of multiple fabric samples.
- High-Speed Rotating Impellers - Impellers rotate at around 1200 rpm to create intense, random tumbling motion.
- Compressed Air System - Ensures continuous fabric movement and realistic simulation of wear.
- Digital Timer- Allows precise setting of test duration with easy-to-read display.
- Viewing Windows- Transparent chamber doors for monitoring fabric movement during testing.
- Standard Compliant Design- Meets ASTM D3512, ISO 12945-3, GB/T 4802.4 and other major standards.
- Robust Construction- Durable materials and components designed for long-term laboratory use.
- Easy Sample Handling - Quick-open chamber lids and simple sample placement process.
- Compact Footprint- Saves space in laboratory environments.
- Prepare Samples- Cut fabric into standard-sized specimens (usually circular or rectangular per ASTM/ISO specs)- Condition samples as per the standard (usually 24 hrs at 21°C, 65% RH).
- Load the Chambers - Place each sample into a cork-lined test chamber. - Add a small piece of gray cotton backing fabric if required by the method.
- Set Parameters - Adjust compressed air pressure (typically 14–21 kPa or 2–3 psi).
- Start the Test- Close the chamber doors and press start. - Impellers rotate, tumbling the samples randomly with air flow.
- Stop and Unload - Once the timer ends, remove the samples carefully.
- Evaluate Pilling - Compare the tested samples to standard pilling rating photographs or scales.
- Record Results - Document the pilling grades and any observations.

Counting Balance-Weighing Scale
Counting Balance-Weighing Scale
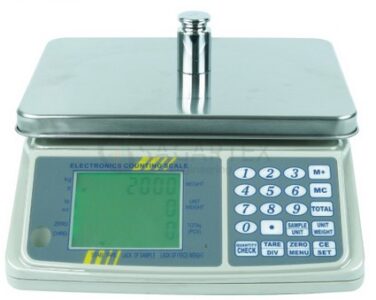
Counting Balance-Weighing Scale
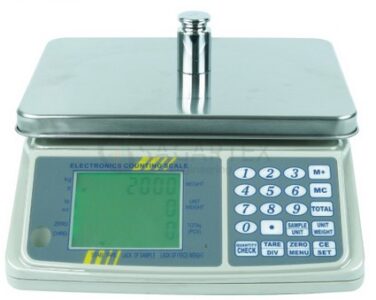
Counting Balance-Weighing Scale
Xenon Arc Light Fastness Tester
Analog Thickness Gauge
Analog Thickness Gauge
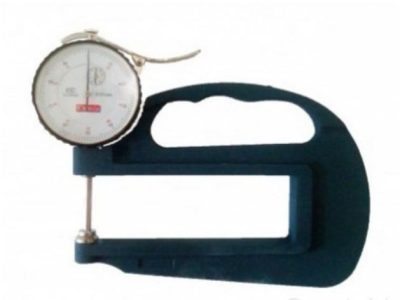
Analog Thickness Gauge
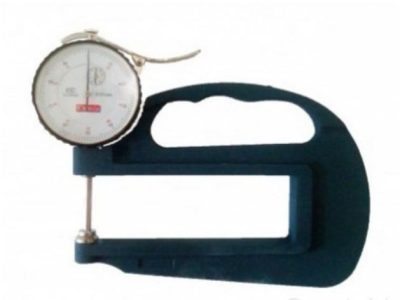
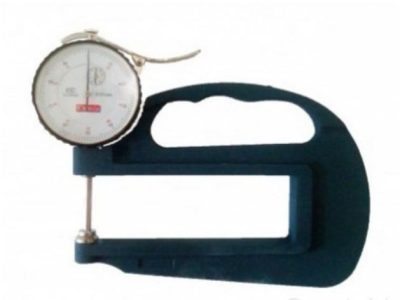
An Analog Thickness Gauge is a manual instrument used to measure the thickness of materials such as fabric, paper, leather, rubber, and plastic. Unlike digital gauges, it displays readings through a mechanical dial or scale.
Fiber Oil Fast Extractor
Fiber Oil Fast Extractor
A Fiber Oil Fast Extractor is a laboratory instrument designed to determine the oil or finish content in fibers, yarns, or fabrics, particularly wool and synthetic materials. It operates on the principle of solvent extraction followed by evaporation. Working Principle of Fiber Oil Fast Extractor:- Sample Preparation: Cut the fabric or fiber into small pieces.
- Solvent Addition: Place the sample into a metal tube and add an appropriate solvent (e.g., petroleum ether, ethyl ether).
- Extraction: Apply weight to the sample to facilitate the dissolution of oils into the solvent.
- Evaporation: The solvent-oil mixture drips onto a heated plate where the solvent evaporates, leaving behind the oil.
- Measurement: Weigh the remaining oil and calculate its percentage relative to the initial sample mass.
- Accurate Oil Content Measurement- Precisely determines oil or finish content in fibers, crucial for quality control.
- Rapid Extraction Process - Delivers fast results, improving lab efficiency and productivity.
- Simultaneous Multi-Sample Testing - Multiple workstations (e.g., 4 at once) reduce testing time for bulk samples.
- Improved Product Quality - Helps maintain consistent oil levels, which affect dyeing, processing, and fabric performance.
- Automatic Operation - Automated pressing and heating reduce manual effort and operator error.
- Digital Monitoring - Built-in timer, temperature control, and oil calculator enhance accuracy and usability.
- Compliance with Standards - Supports industry methods like GB/T 6504-2017, ensuring reliable and standard-compliant results.
- Safe Solvent Handling - Enclosed design minimizes solvent exposure and evaporation loss.
- Multiple Test Stations - Usually equipped with 2 to 4 independent work units for parallel testing.
- Automatic Weight Pressing System - Applies consistent pressure on samples for uniform solvent extraction.
- Microcomputer Temperature Control - Maintains precise heating (typically 90–120°C) with ±1°C accuracy.
- Built-in Timer and Calculator - Allows setting extraction time and calculates oil content directly.
- Solvent Evaporation Plate- Heats and evaporates solvent quickly, leaving only the oil residue.
- Digital Display - Shows time, temperature, and process status for user-friendly operation.
- Compact and Durable Design - Made with corrosion-resistant materials suited for chemical handling.
- Safety Features - Includes overheat protection and enclosed solvent chamber to reduce exposure risk.
- Standard Compliant - Designed to meet GB/T 6504-2017 and similar industry testing standards.
- Prepare the Sample - Cut 5–10 g of fiber or yarn into small pieces and place in the sample tube.
- Add Solvent - Pour a suitable solvent (e.g., petroleum ether) into the tube to cover the sample.
- Apply Weight - Place the extractor's weight or press system onto the sample to aid extraction.
- Start Extraction - Activate the machine. The solvent dissolves the oils and flows to the heating plate.
- Heat for Evaporation - Set the temperature (typically 90–120°C). The solvent evaporates, leaving oil on the plate.
- Measure Oil Content- After drying, weigh the remaining oil. Use the built-in calculator or formula:
- Clean the Unit - After cooling, clean all parts to prepare for the next test.
Fiber Oil Fast Extractor
IR Dyeing Machine Dunlin
IR Dyeing Machine Dunlin
IR Dyeing machine Dunlin is Safe, high efficiency, environment friendly, energy saving, optimum for new dyeing small sample machines0 - 3.5 ℃ / min Cooling rate 0.2 - 5 ℃ / min Cooling method Air-cooled Rotation speed 0 - 60 rpm Liquor ratio 1:5 -1:100 Power supply 1∮AC 220V 50/60HZ Dimensions( L x W x H) 670×670×780mm 860×680×780mm Weight 100kg 120kg Standard Accessories Cups 1set
Put the test sample. Cups stand 1set Place where to put cups. Protective glove 1set To avoid to be hurt by HT cups. Model: IF-24SCapacity: 24 pots Brad: DUNLIN Origin: China
Color dyeing tests for various dyestuffs of IR Dyeing machine Dunlin- Step dyeing tests. C. Dispersing, levelling and impregnating test. D. High or low liquor ratio exhausting tests. E. Fabric steak and staining tests. F. Concentration tests and others. Protection and Safety gates to protect. Temperature control accuracy +/- 0.2degree

IR Dyeing machine