Stretch Recovery Tester Static Method
$0.00
Stretch Recovery Tester Static Method

Stretch Recovery Tester
A Stretch Recovery Tester Static Method is a lab instrument used to evaluate the stretch ability and recovery properties of fabrics, elastomers, or other stretchable materials. This method is crucial in textiles and material science to assess how well a material returns to its original shape after being stretched.
Key Functions of Stretch Recovery Tester Static Method :
– Measures elongation under a fixed force or length.
– Assesses the recovery percentage after a specified recovery time once the force is removed.
– Evaluates fabric’s resilience, durability, and comfort properties.
How It Works Stretch Recovery Tester Static Method:
- A sample is stretched to a predetermined extension or force.
- The stretch is maintained for a set period.
- After removing the load, the recovery (return to original length) is measured after a fixed time.
- The fabric sample is clamped and stretched to a specific length or force.
- It’s held for a fixed duration (e.g., 1–5 minutes).
- The tension is released, and the sample is allowed to recover.
- The recovered length is measured after a set time.
Main Components:
– Fixed clamps to hold the sample.
– Movable clamps for stretching.
– Precision scale or ruler for measuring elongation and recovery.
– Timing device (manual or digital) to control stretching and recovery periods.
– To assess elastic recovery and dimensional stability after stretching.
Applications:
– Used in testing knitwear, sportswear, elastic fabrics, and compression garments.
– Helps in product development and quality assurance.
Stretch Recovery Tester Static Method is designed to determine the stretch recovery property of elastic material by static method. 2.0mm thickness stainless steel frame and base board, makes the tester firm and stable. Sample holder can be slid along the guide rail smoothly and can be fixed at any position of the rail.
Test Scope:elastomeric material
Testing Standards:ASTM D2594、ASTM D3107, etc.
key features of a Stretch Recovery Tester Static Method:
Adjustable clamps and measurement scale.
– Timer for accurate stretch/recovery periods.
– Simple mechanical design for ease of use.
✅ 1. Manual or Semi-Automatic Operation
– Allows controlled stretching and recovery measurements.
– Simple setup for routine quality control.
✅ 2. Adjustable Clamp System
– Securely holds samples of various sizes and thicknesses.
– Ensures consistent test conditions.
✅ 3. Precision Measurement Scale
– Provides accurate readings of elongation and recovery length.
– Often graduated in millimeters or inches.
✅ 4. Sturdy Frame
– Made of corrosion-resistant metal or coated steel.
– Ensures durability and stability during testing.
✅ 5. Time Control Support
– Timer to monitor stretch and recovery durations.
– Helps standardize test procedures.
✅ 6. Compact Design
– Space-saving for lab environments.
– Easy to move and operate.
✅ 7. Compliance with Standards
– Often designed to meet standards like ASTM D3107 or BS 4294.
Would you like a comparison with the dynamic method or specifications for a particular model?
key benefits of using a Stretch Recovery Tester Static Method:
✅ 1. Accurate Fabric Performance Analysis- Provides reliable data on stretch and recovery, critical for assessing elasticity and fit.
✅ 2. Easy to Operate- Simple, manual setup makes it ideal for routine testing and quality control.
✅ 3. Cost-Effective- More affordable than dynamic testers, making it suitable for smaller labs or production units.
✅ 4. Standardized Testing- Supports industry-standard methods (e.g., ASTM D3107), ensuring consistency across tests.
✅ 5. Versatile Applications- Suitable for testing knit fabrics, elastic bands, spandex materials, and other stretchable textiles.
✅ 6. Durable and Low Maintenance- Mechanically straightforward with minimal upkeep required.
✅ 7. Enhances Product Development- Helps designers and manufacturers optimize materials for comfort, performance, and durability.
Applications:
– Textile R&D
– Production quality control

Stretch Recovery Tester
– Evaluating materials for comfort, durability, and fit
Stretch Recovery Tester Diller In Bangladesh, Stretch Recovery Tester Importer In Bangladesh, Stretch Recovery Tester in Bangladesh, Stretch Recovery Tester in Bd, Stretch Recovery Tester In Uttara, Stretch Recovery Tester Price in Bangladesh, Stretch Recovery Tester Supplier in Bangladesh
Related products
Pantone book
Pantone Book

Pantone Book
- Formula Guide (Solid Coated & Uncoated) – For spot color printing.
- Color Bridge – Shows Pantone spot colors alongside CMYK equivalents.
- Pantone Fashion, Home + Interiors (FHI) – For textiles, soft goods, and home decor.
- Pantone CMYK and Pastels & Neons Guides – For process printing and special effect colors.
- Formula Guide (Solid Coated & Uncoated)
- Color Bridge Guide (Coated & Uncoated)
- CMYK Guide (Coated & Uncoated)
- Pastels & Neons Guide
- Metallics Guide
- FHI Color Guide (TPG – Paper)
- FHI Cotton Passport & Cotton Planner (TCX – Textile)
- FHI Polyester Swatch Book
- Pantone SkinTone Guide
- Pantone Plastic Standard Chips

Pantone Book
Counting Balance-Weighing Scale
Counting Balance-Weighing Scale
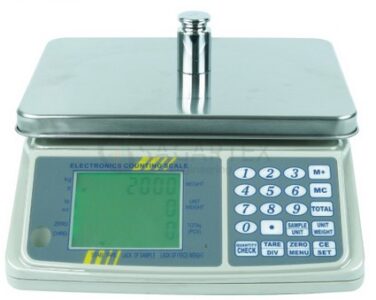
Counting Balance-Weighing Scale
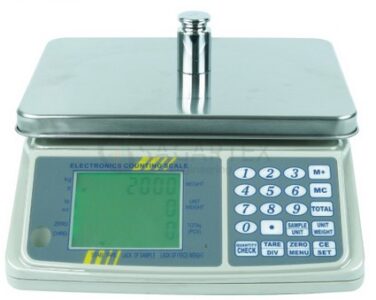
Counting Balance-Weighing Scale
Color fastness to washing machine
COLOR FASTNESS TO WASHING MACHINE
Color fastness to washing machine refers to a fabric’s resistance to fading or bleeding when subjected to washing processes. This test measures how well the dye or colorant stays on the fabric when exposed to water, detergent, heat, and mechanical action—conditions typically found in household or industrial washing machines. Purpose of Color fastness to washing machine - To evaluate the durability of dyed or printed textiles during laundering.- Essential for determining fabric quality and suitability for end-use (e.g., clothing, upholstery). Test Method Usually based on international standards such as: - ISO 105-C06 - AATCC 61- IS 3361- AATCC 28/61/132/151/190, BS 1006 C01-C05, ISO 105 Part C01-C06/C08/D01, M&S C4/C5/C10A/P3B, FTMS 191-5610, NEXT TM2/3/5, GB/T 5711/3921 Procedure (Simplified)1. Sample Preparation: - A fabric specimen is stitched with undyed adjacent fabrics (usually cotton or wool).2. Washing: - Washed in a laboratory washing machine using standard detergent, water, and specific temperature/time settings (e.g., 40°C for 30 minutes).- Drying: - After washing, the sample is dried, typically air-dried or tumble-dried.4. Evaluation: - Color change and staining on adjacent fabrics are assessed using a gray scale (1 to 5 scale; 5 = no change, 1 = severe change). - Results may also be evaluated visually under standard lighting.
- Supports Brand Reputation - Reliable color fastness contributes to a premium product image and consistent performance.4. Compliance with Standards - Meets industry requirements (e.g., ISO, AATCC), crucial for export, certifications, and regulatory compliance.
- Improves Process Control- Helps identify dyeing or finishing process issues early, leading to better production control.6. Reduces Rework and Waste - Minimizes production losses due to color defects after washing.
- Essential for Specific End Uses - Critical for items subject to frequent washing (e.g., uniforms, baby clothes, hospital linens).8. Supports Material Selection - Guides textile manufacturers in choosing appropriate dyes and fabrics for specific applications.
- Assessment of Color Change and Staining- Evaluates both the fabric’s color retention and the staining of adjacent fabrics using grey scales (1 to 5 rating).4. Multi-Fiber Fabric Use - Tests include fabric stitched with adjacent test strips (cotton, wool, etc.) to assess color bleeding onto different fibers.
- Multiple Test Options - Includes domestic, accelerated, and industrial washing conditions depending on the end-use of the fabric.6. Temperature and Time Control - Precise control over wash temperature (e.g., 40°C, 60°C) and duration (e.g., 30 mins), simulating specific washing cycles.
- Detergent and Additive Use - Uses standardized detergent formulations with/without optical brighteners, and sometimes alkaline or oxidizing agents.8. Reproducible and Quantifiable - Provides repeatable results that can be objectively measured and documented.
- Applicability to All Textile Types - Suitable for dyed, printed, or coated fabrics across various fibers (cotton, polyester, blends, etc.).
- Rate of temperature rise: Maximum speed for 2ºC/min 7. Internal materials: Imported Stainless Steel 316L 8. Control panel: Touch screen
- Rack point control function helps to replace containers easily 10. Safety device: Safety door switch, over-temperature protector and dry heating protector 11. Heating media: Distilled water 12. Power supply: AC220V 50Hz 30A
Controller For IR Dyeing Machine
Controller For IR Dyeing Machine
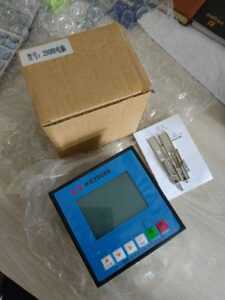
IR Dyeing machine controller
- Temperature Control:- Precisely regulates the infrared heaters to maintain uniform temperature across the dye bath. - Supports customizable heating curves (ramp-up, hold, and cool-down phases).
- Programmable Logic Control (PLC): - Allows operators to set and automate dyeing programs for different fabrics and dye types. - Supports multiple recipes or programs for different batches.
- Real-Time Monitoring and Feedback: - Monitors parameters like temperature, fabric rotation, bath circulation, and timing. - Provides real-time data and alarms for deviations.
- Touchscreen Interface / HMI (Human Machine Interface): - User-friendly interface for configuring and monitoring processes. - Multi-language support and graphical display of process curves.
- Data Logging and Traceability: - Records process data for quality control and traceability.
- Energy Efficiency Optimization: - Manages IR heater output to reduce energy usage. - Often includes features for auto shut-off or idle mode.
- Safety Features: - Includes emergency stop, over-temperature protection, and fault detection systems. 8. Connectivity: - Modern controllers may support Ethernet, Modbus, or other industrial communication protocols for integration into factory automation systems.
- Improved Dyeing Accuracy and Consistency
- Enhanced Energy Efficiency- Infrared heating is more energy-efficient than traditional heating methods.- The controller optimizes energy use by adjusting the IR output based on process needs, reducing overall energy consumption.
- Time Savings- Faster heating and cooling cycles due to infrared technology.- Automated processes reduce manual intervention and cycle times. 4. Better Process Control- Programmable dyeing cycles and precise control over each stage (heating, dyeing, rinsing, cooling).- Real-time monitoring and adjustments improve reliability.
- Reduced Water and Chemical Usage- More efficient dye penetration and fixation mean less water and fewer chemicals are needed for reprocessing or corrections.6. Lower Operational Costs
- Enhanced Safety Built-in alarms, emergency shut-off and automatic fault detection enhance operational safety.8. Data Logging and Traceability- Ability to record and review dyeing process data helps in quality control and troubleshooting.- Facilitates compliance with industry standards and audits.
- User-Friendly Operation- Modern touchscreen interfaces make it easier for operators to manage and monitor processes.- Multilingual support and visual feedback enhance usability.
Fabric Stiffness Tester
Fabric Stiffness Tester
Fabric Stiffness Tester is a lab instrument used to measure the stiffness or flexural rigidity of fabric materials. It evaluates how resistant a fabric is to bending, which influences its drape, comfort, and handling characteristics. Purpose of Fabric Stiffness Tester: To determine the stiffness of textiles by measuring the bending length and calculating flexural rigidity, often using methods like the Cantilever Test (as per ASTM D1388 or ISO 9073-7). Working Principle of Fabric Stiffness Tester: A fabric strip is slid over a horizontal platform until its free end bends under its own weight to a specific angle (usually 41.5°). The length at which this occurs is used to calculate bending length and stiffness. Main Components of Fabric Stiffness Tester: - Test Platform: Flat surface for sample movement. - Graduated Scale: Measures the overhanging length of fabric. - Angle Indicator: Guides the measurement based on standard deflection angle. - Fabric Clamp or Guide: Helps place and move the sample smoothly. Applications of Fabric Stiffness Tester: - Apparel fabrics (e.g., for comfort and drape analysis) - Technical textiles (e.g., automotive, medical fabrics) - Paper, nonwovens, and films Benefits of Fabric Stiffness Tester:- Accurate Measurement of Flexibility - Provides reliable data on fabric stiffness, essential for quality control and product development.
- Improves Product Comfort - Helps assess how soft or rigid a fabric will feel in clothing or furnishings.
- Supports Material Selection - Aids designers and engineers in choosing the right fabric for specific applications based on stiffness.
- Quality Assurance - Detects fabric inconsistencies or defects that affect handling or drape.
- Standards Compliance - Enables testing as per international standards like ASTM D1388 and ISO 9073-7 for global product approval.
- Quick and Simple Operation - Delivers fast results with minimal operator training or preparation.
- Applicable to Multiple Materials - Suitable for woven, nonwoven, knitted fabrics, paper, and films.
- Enhances R&D Accuracy - Supports consistent material testing during product innovation and textile finishing.
- Graduated Measurement Scale - Precise scale to measure overhang length for accurate stiffness calculation.
- Flat Test Platform - Smooth, level surface ensures consistent and reliable fabric movement.
- Standard Deflection Angle Guide - Built-in 41.5° angle reference for consistent stiffness testing (per ASTM/ISO).
- Manual or Motorized Models - Available in both types for simple or automated operation depending on lab needs.
- Compact Design - Space-saving unit ideal for textile labs and quality control rooms.
- Sample Holder or Clamp - Ensures correct alignment and smooth feeding of fabric strips during testing.
- Durable Construction - Made of corrosion-resistant materials like stainless steel or aluminum for long-term use.
- Compliance with Standards - Supports methods like ASTM D1388, ISO 9073-7 for stiffness testing of fabrics.
- Lightweight and Portable - Easy to move and use in various lab settings.
- Low Maintenance - Simple mechanical parts require minimal servicing.
- Prepare the Sample - Cut the fabric into a rectangular strip (e.g., 25 mm × 200 mm), as per standard.
- Place the Sample - Lay the fabric strip flat on the test platform with one end aligned at the zero mark.
- Slide the Fabric - Gently push the fabric forward so it slowly overhangs the platform.
- Watch for Deflection - Stop sliding when the free end of the fabric bends down to the reference angle (typically 41.5°).
- Read the Bending Length - Measure the overhang distance from the scale. This is the bending length (C).
- Calculate Flexural Rigidity
- Repeat for Accuracy - Test both warp and weft directions and average the results for better accuracy.

Digital Elmendorf tearing tester
Digital Elmendorf Tearing Tester
Digital Elmendorf Tearing Tester is a precision instrument used to measure the tear strength of materials like woven fabrics, paper, plastic films, and nonwovens. It determines how much force is required to continue tearing a pre-slit sample. Key Functions of Digital Elmendorf Tearing Tester: - Measures propagation tear resistance, not initial tear. - Uses a pendulum to apply force; the energy lost during tearing is calculated to determine tear strength. - Equipped with a digital display for direct reading of results in grams or millinewtons. Core Components: - Pendulum Arm: Applies tearing force. - Clamps: Secure the sample before and after the tear. - Cutting Blade: Creates a precise slit at the start of the test. - Digital Display Unit: Shows the tearing force result clearly and instantly. - Counterweights: Optional weights for increasing test range (for stronger materials). Applications of Digital Elmendorf Tearing Tester: - Testing tear resistance of: - Textile fabrics (especially woven) - Paper and cardboard - Plastic films - Nonwovens - Packaging materials Benefits of Digital Elmendorf Tearing Tester:- Accurate Tear Strength Measurement - Provides precise data on tear resistance, critical for quality control and product performance.
- Digital Readout - Easy-to-read display gives instant, reliable results without manual calculations.
- High Reproducibility - Ensures consistent test outcomes due to controlled tearing angle and speed.
- Fast Testing Process - Simple loading and quick test cycle increase lab efficiency.
- Suitable for Various Materials - Tests a wide range of flexible materials like textiles, paper, plastic, and packaging.
- Customizable Range - Use of optional weights extends the test range for low to high tear strength materials.
- Low Sample Waste - Requires small fabric or material samples, reducing waste during testing.
- Standards Compliance - Meets international testing standards (e.g., ASTM D1424, ISO 13937) for credibility and uniformity.
- Precision Sample Clamp - Securely holds samples in place to ensure accurate tear initiation.
- Pre-Cutting Blade - Integrated knife creates a precise initial slit in the sample before tearing.
- User-Friendly Interface - Simple buttons and screen navigation for ease of operation.
- Standard Test Compliance - Compatible with ASTM D1424, ISO 1974, ISO 13937, and other tear strength standards.
- Sturdy Construction - Made with durable materials for long-lasting performance and stable operation.
- Compact Design - Space-efficient footprint ideal for laboratory environments.
- Data Output Options- Some models offer USB or printer connectivity for result documentation.
- Prepare the Sample - Cut the material (fabric, paper, film, etc.) to standard size (typically 100 × 63 mm for textiles) and slit it with the pre-cutter as required.
- Select Pendulum Weight - Choose the appropriate pendulum or add counterweights based on expected tear strength.
- Calibrate the Machine - Set the pendulum to its starting position and zero the display.
- Clamp the Sample - Fix one half of the sample in the stationary clamp and the other in the moving clamp.
- Cut the Initial Slit - Use the integrated blade to make a precise cut at the marked slit area (usually 20 mm).
- Release the Pendulum - Trigger the pendulum to swing and tear the sample through the pre-slit.
- Read the Result - The digital display will show the tearing force automatically (in g, mN, or cN).
- Record or Export Data - Save or print the result if your model supports USB or printer connection.
- Reset for Next Test - Reposition the pendulum and prepare a new sample for the next cycle.

Laboratory Padder
Laboratory Padder
A Laboratory Padder is a compact, laboratory-scale machine used to apply liquids like dyes, chemicals, and finishes to fabric samples. It simulates the padding process in textile manufacturing, where fabric is passed through a liquid solution, then squeezed between rollers to ensure uniform application and absorption. Key Features of a Laboratory Padder:- Adjustable Rollers - The fabric is passed through two or more rollers to apply even pressure and squeeze out excess solution, ensuring uniform chemical or dye application.
- Variable Pressure Control - Allows adjustment of roller pressure for different fabric types and chemical formulations, ensuring optimal penetration without damage.
- Solution Bath - Holds the liquid (e.g., dye, finish, or other chemical treatments) in a bath through which the fabric is dipped before passing through the rollers.
- Fabric Speed Control - Adjustable conveyor speed allows for control over the time the fabric spends in contact with the liquid solution, affecting the degree of treatment.
- Digital Control Panel - Provides easy adjustment of pressure, speed, and solution volume to ensure precise and reproducible results.
- Compact Design - Smaller, lab-scale version of industrial padders, ideal for research, development, and small-scale testing.
- Safety Features - Safety guards, emergency stops, and proper handling mechanisms to prevent accidents during operation.
- Precise Application of Chemicals - Provides uniform and controlled application of dyes, finishes, and other chemicals, ensuring consistent results.
- Small-Scale Testing - Ideal for small sample testing, allowing for fabric treatment without needing full-scale production equipment.
- Versatile Use - Suitable for dyeing, finishing, and applying various chemical treatments, making it a flexible tool for R&D labs.
- Cost-Effective - Reduces the need for large-scale machinery and the associated costs, while providing reliable results for small batches.
- Controlled Fabric Treatment - Offers adjustable pressure, speed, and solution concentration, enabling fine-tuned processing for different fabric types and applications.
- Accelerates Development - Speeds up the testing and development of new products or finishes, improving time-to-market for textile manufacturers.
- Energy Efficient - Consumes less energy compared to larger, industrial-scale machines, making it suitable for lab use.
- Compact and Space-Saving - Designed for laboratory environments with limited space, without compromising on functionality.
- Reproducible Results - Ensures consistent application of treatments across multiple samples, aiding in accurate testing and comparison.
- Adjustable Roller Pressure - Allows precise control over the pressure applied to the fabric, ensuring uniform chemical or dye application.
- Variable Speed Control - Adjustable conveyor speed for controlling the time the fabric spends in the solution bath, influencing the absorption rate.
- Solution Bath - Holds dye, chemicals, or finishes, and the fabric passes through this bath before moving to the rollers.
- Digital Control Panel - Easy-to-use interface for setting and adjusting parameters like speed, pressure, and solution concentration.
- Compact and Lab-Friendly Design - Designed for smaller, space-efficient use in textile labs, allowing for small sample testing.
- Roller Gap Adjustment - Allows for fine-tuning of the gap between rollers to regulate the amount of solution squeezed out of the fabric.
- Stainless Steel Construction - Durable and resistant to corrosion from the chemicals used in textile treatments.
- Safety Mechanisms - Includes safety guards, emergency stops, and user protection features during operation.
- Even and Controlled Application - Ensures even distribution of treatments (dye, finish, etc.) on fabric with minimal waste.
- Versatility in Application - Can be used for a wide range of textiles and treatments, including dyeing, softening, flame-retardant treatments, etc.
- Prepare the Fabric Sample - Cut the fabric sample to the required size for the experiment. Ensure it’s clean and free of any debris.
- Prepare the Solution - Mix the dye, chemical, or finish solution according to the desired concentration and the fabric's needs. Ensure that the solution is homogeneous.
- Set the Parameters - Pressure: Adjust the roller pressure based on the fabric type. Different fabrics require different pressure levels to ensure uniform application. - Speed: Set the fabric conveyor speed depending on the desired treatment time (longer exposure for deeper treatment).
- Load the Fabric into the Machine - Place the fabric carefully into the machine. The fabric should go through the solution bath and then pass between the rollers.
- Start the Machine - Turn on the machine and allow the fabric to pass through the rollers. The solution will be evenly applied to the fabric as it moves through the bath and is squeezed by the rollers.
- Monitor the Process - Keep an eye on the fabric to ensure it is being treated uniformly and there are no blockages or fabric jams.
- Unload the Fabric - Once the fabric has been treated, carefully remove it from the machine. Inspect for even application of the solution and any excess liquid.
- Dry or Process Further - Depending on the treatment, proceed with further steps such as drying, heat setting, or curing, as required by the experiment or process.

Mini Lab Dyeing Padder
IR Dyeing Machine Dunlin
IR Dyeing Machine Dunlin
IR Dyeing machine Dunlin is Safe, high efficiency, environment friendly, energy saving, optimum for new dyeing small sample machines0 - 3.5 ℃ / min Cooling rate 0.2 - 5 ℃ / min Cooling method Air-cooled Rotation speed 0 - 60 rpm Liquor ratio 1:5 -1:100 Power supply 1∮AC 220V 50/60HZ Dimensions( L x W x H) 670×670×780mm 860×680×780mm Weight 100kg 120kg Standard Accessories Cups 1set
Put the test sample. Cups stand 1set Place where to put cups. Protective glove 1set To avoid to be hurt by HT cups. Model: IF-24SCapacity: 24 pots Brad: DUNLIN Origin: China
Color dyeing tests for various dyestuffs of IR Dyeing machine Dunlin- Step dyeing tests. C. Dispersing, levelling and impregnating test. D. High or low liquor ratio exhausting tests. E. Fabric steak and staining tests. F. Concentration tests and others. Protection and Safety gates to protect. Temperature control accuracy +/- 0.2degree

IR Dyeing machine