Laboratory Padder
$0.00
Laboratory Padder
A Laboratory Padder is a compact, laboratory-scale machine used to apply liquids like dyes, chemicals, and finishes to fabric samples. It simulates the padding process in textile manufacturing, where fabric is passed through a liquid solution, then squeezed between rollers to ensure uniform application and absorption.
Key Features of a Laboratory Padder:
- Adjustable Rollers – The fabric is passed through two or more rollers to apply even pressure and squeeze out excess solution, ensuring uniform chemical or dye application.
- Variable Pressure Control – Allows adjustment of roller pressure for different fabric types and chemical formulations, ensuring optimal penetration without damage.
- Solution Bath – Holds the liquid (e.g., dye, finish, or other chemical treatments) in a bath through which the fabric is dipped before passing through the rollers.
- Fabric Speed Control – Adjustable conveyor speed allows for control over the time the fabric spends in contact with the liquid solution, affecting the degree of treatment.
- Digital Control Panel – Provides easy adjustment of pressure, speed, and solution volume to ensure precise and reproducible results.
- Compact Design – Smaller, lab-scale version of industrial padders, ideal for research, development, and small-scale testing.
- Safety Features – Safety guards, emergency stops, and proper handling mechanisms to prevent accidents during operation.
Applications:
– Dyeing: For even application of dye or pigment on fabric.
– Finishing: Applying finishes like softeners, water repellents, or flame retardants.
– Chemical Treatments: Applying various chemicals used in textile manufacturing, such as anti-microbial treatments or stain-resistant solutions.
– Shrinkage Testing: Simulating treatments to test fabric behavior under different conditions.
Benefits of Laboratory Padder:
- Precise Application of Chemicals – Provides uniform and controlled application of dyes, finishes, and other chemicals, ensuring consistent results.
- Small-Scale Testing – Ideal for small sample testing, allowing for fabric treatment without needing full-scale production equipment.
- Versatile Use – Suitable for dyeing, finishing, and applying various chemical treatments, making it a flexible tool for R&D labs.
- Cost-Effective – Reduces the need for large-scale machinery and the associated costs, while providing reliable results for small batches.
- Controlled Fabric Treatment – Offers adjustable pressure, speed, and solution concentration, enabling fine-tuned processing for different fabric types and applications.
- Accelerates Development – Speeds up the testing and development of new products or finishes, improving time-to-market for textile manufacturers.
- Energy Efficient – Consumes less energy compared to larger, industrial-scale machines, making it suitable for lab use.
- Compact and Space-Saving – Designed for laboratory environments with limited space, without compromising on functionality.
- Reproducible Results – Ensures consistent application of treatments across multiple samples, aiding in accurate testing and comparison.
Features of Laboratory Padder:
- Adjustable Roller Pressure – Allows precise control over the pressure applied to the fabric, ensuring uniform chemical or dye application.
- Variable Speed Control – Adjustable conveyor speed for controlling the time the fabric spends in the solution bath, influencing the absorption rate.
- Solution Bath – Holds dye, chemicals, or finishes, and the fabric passes through this bath before moving to the rollers.
- Digital Control Panel – Easy-to-use interface for setting and adjusting parameters like speed, pressure, and solution concentration.
- Compact and Lab-Friendly Design – Designed for smaller, space-efficient use in textile labs, allowing for small sample testing.
- Roller Gap Adjustment – Allows for fine-tuning of the gap between rollers to regulate the amount of solution squeezed out of the fabric.
- Stainless Steel Construction – Durable and resistant to corrosion from the chemicals used in textile treatments.
- Safety Mechanisms – Includes safety guards, emergency stops, and user protection features during operation.
- Even and Controlled Application – Ensures even distribution of treatments (dye, finish, etc.) on fabric with minimal waste.
- Versatility in Application – Can be used for a wide range of textiles and treatments, including dyeing, softening, flame-retardant treatments, etc.
How to Use a Laboratory Padder:
- Prepare the Fabric Sample – Cut the fabric sample to the required size for the experiment. Ensure it’s clean and free of any debris.
- Prepare the Solution – Mix the dye, chemical, or finish solution according to the desired concentration and the fabric’s needs. Ensure that the solution is homogeneous.
- Set the Parameters – Pressure: Adjust the roller pressure based on the fabric type. Different fabrics require different pressure levels to ensure uniform application. – Speed: Set the fabric conveyor speed depending on the desired treatment time (longer exposure for deeper treatment).
– Roller Gap: Adjust the roller gap to control the amount of liquid squeezed out from the fabric.
- Load the Fabric into the Machine – Place the fabric carefully into the machine. The fabric should go through the solution bath and then pass between the rollers.
- Start the Machine – Turn on the machine and allow the fabric to pass through the rollers. The solution will be evenly applied to the fabric as it moves through the bath and is squeezed by the rollers.
- Monitor the Process – Keep an eye on the fabric to ensure it is being treated uniformly and there are no blockages or fabric jams.
- Unload the Fabric – Once the fabric has been treated, carefully remove it from the machine. Inspect for even application of the solution and any excess liquid.
- Dry or Process Further – Depending on the treatment, proceed with further steps such as drying, heat setting, or curing, as required by the experiment or process.
Safety Tips:- Always wear appropriate personal protective equipment (PPE), such as gloves and goggles, when handling dyes or chemicals. – Ensure the machine is turned off and the rollers are stopped before attempting to remove or adjust the fabric.
Laboratory Padder dealer In Bangladesh,
Lab Padder Importer in Bangladesh,
Laboratory Padding mangle in Bangladesh,
Laboratory Padding mangle in Bd,
Laboratory Padder Price in Bangladesh,
Laboratory Padder in Bangladesh,
Laboratory Padding mangle price in Bangladesh
Laboratory Padder

Mini Lab Dyeing Padder
Brand: DUNLIN
Model:PM-A1
Origin: China
Roller position: Vertical
Rollers width :450mm
Rollers diameter:125mm
Rubbers hardness: 70degree shore
Cloth speed: 0-10m/min
Standard pressure: 0.6Mpa
Retained dyestuff ratio: 40-80%
Power supply: 1∮AC 220V 50/60HZ
Dimensions (L x W x H):710 x 600x 1340mm
Standard Accessories
English manual
Certificate of quality.
Laboratory Padder Machine Dunlin price in Bangladesh
Laboratory Padder Machine Dunlin in textile
Textile testing equipment in Bangladesh
Textile testing equipment in Dhaka
Textile testing equipment in Uttara
MAAM tex Laboratory Padder Machine Dunlin price in BangladeshLaboratory Padder
Related products
Fabric air permeability tester
Fabric Air Permeability Tester
Fabric Air Permeability Tester is a lab instrument used to measure how easily air passes through a fabric. It quantifies the air permeability, which is crucial for evaluating breathability, comfort, and functional performance in textiles. Purpose Fabric Air Permeability Tester: It determines the rate of airflow through a fabric sample under a set air pressure, typically reported in units like cm³/cm²/s or L/m²/s. Working Principle: The tester creates a pressure difference across the fabric sample and measures the volume of air flowing through it. Higher air permeability means the fabric is more breathable. Main Components of Fabric Air Permeability Tester: - Test Head / Clamp: Holds the fabric securely without leakage. - Pressure Regulator: Maintains a constant air pressure during testing. - Flow Meter or Digital Sensor: Measures the actual airflow rate through the fabric. - Display Unit: Shows readings of air permeability instantly. Applications of Fabric Air Permeability Tester: - Performance textiles (sportswear, PPE) - Technical fabrics (filters, tents, airbags) - Medical textiles (masks, gowns) - Nonwovens and industrial materials Benefits of Fabric Air Permeability Tester:- Accurate Breathability Measurement - Precisely measures how breathable a fabric is, essential for comfort and performance.
- Supports Quality Control - Ensures consistent air permeability in fabric batches, critical for products like PPE, sportswear, and filters.
- Enhances Product Design - Helps in selecting or engineering fabrics with the right airflow properties for specific uses.
- Standard Compliance - Conforms to international testing standards (e.g., ASTM D737, ISO 9237), ensuring global credibility.
- Quick and Reliable Testing - Provides rapid results, increasing lab efficiency and production decision-making speed.
- Wide Material Compatibility - Suitable for woven, nonwoven, knitted fabrics, and even paper or coated materials.
- Improves Functional Performance - Helps optimize products for ventilation, moisture control, and thermal comfort.
- Reduces Product Failure - Identifies underperforming fabrics early, minimizing risks in high-performance applications.
- Digital Display - Shows air permeability readings clearly in units like L/m²/s or cm³/cm²/s.
- Precise Test Head/Clamp - Provides an airtight seal to prevent air leakage and ensure accurate results.
- Adjustable Pressure Settings - Allows testing under various pressure drops (e.g., 10–2500 Pa), depending on fabric type.
- Automatic Airflow Measurement - Built-in sensors or flow meters capture airflow rate automatically for quick analysis.
- Multiple Test Area Sizes - Interchangeable test plates to match different sample sizes and standard requirements.
- Data Logging and Export - Some models include USB or software connectivity for storing and exporting test results.
- Standard Compliance - Conforms to ASTM D737, ISO 9237, BS 5636, DIN 53887, etc.
- Robust Construction - Built with corrosion-resistant materials and durable components for long-term lab use.
- Low Maintenance - Simple cleaning and calibration process for reliable performance.
- Compact and User-Friendly Design - Ideal for lab benches and easy operation with minimal training.
- Prepare the Sample - Cut the fabric sample to the required size (usually circular, e.g., 20 cm²).
- Mount the Sample - Place the fabric securely in the test clamp or holder, ensuring no wrinkles or gaps.
- Set Test Parameters - Adjust the air pressure drop according to the fabric type or standard (e.g., 100 Pa).
- Start the Test - Turn on the air supply and start the airflow through the fabric.
- Read the Measurement - The digital display will show the air permeability value in the selected units.
- Record the Results - Note the readings or export data if the device supports it.
- Repeat if needed - Test multiple samples or areas for accuracy and average the results.
- Clean and Maintain - After testing, clean the clamp and ensure the device is calibrated regularly.

Stretch Recovery Tester Static Method
Stretch Recovery Tester Static Method

Stretch Recovery Tester
- A sample is stretched to a predetermined extension or force.
- The stretch is maintained for a set period.
- After removing the load, the recovery (return to original length) is measured after a fixed time.
- The fabric sample is clamped and stretched to a specific length or force.
- It’s held for a fixed duration (e.g., 1–5 minutes).
- The tension is released, and the sample is allowed to recover.
- The recovered length is measured after a set time.


Stretch Recovery Tester
IR Dyeing Machine Dunlin
IR Dyeing Machine Dunlin
IR Dyeing machine Dunlin is Safe, high efficiency, environment friendly, energy saving, optimum for new dyeing small sample machines0 - 3.5 ℃ / min Cooling rate 0.2 - 5 ℃ / min Cooling method Air-cooled Rotation speed 0 - 60 rpm Liquor ratio 1:5 -1:100 Power supply 1∮AC 220V 50/60HZ Dimensions( L x W x H) 670×670×780mm 860×680×780mm Weight 100kg 120kg Standard Accessories Cups 1set
Put the test sample. Cups stand 1set Place where to put cups. Protective glove 1set To avoid to be hurt by HT cups. Model: IF-24SCapacity: 24 pots Brad: DUNLIN Origin: China
Color dyeing tests for various dyestuffs of IR Dyeing machine Dunlin- Step dyeing tests. C. Dispersing, levelling and impregnating test. D. High or low liquor ratio exhausting tests. E. Fabric steak and staining tests. F. Concentration tests and others. Protection and Safety gates to protect. Temperature control accuracy +/- 0.2degree

IR Dyeing machine
Fabric flame retardant tester
Fabric Flame Retardant Tester
A Fabric Flame Retardant Tester is a specialized laboratory instrument designed to evaluate the flammability characteristics of textiles. It assesses how fabrics react to direct flame exposure, measuring parameters such as ignition time, flame spread rate, after-flame duration, and afterglow time. This testing is crucial for ensuring that textiles meet safety standards for various applications, including apparel, home furnishings, and industrial uses. Purpose and Applications The primary purpose of a Fabric Flame Retardant Tester is to determine the flame resistance of textile materials. This is essential for:- Apparel Safety: Ensuring garments, especially children's sleepwear and industrial work wear, meet flammability standards. - Home Textiles: Testing curtains, drapes, upholstery, and bedding for fire safety compliance. - Technical Textiles: Evaluating materials used in tents, protective clothing, and automotive interiors. ⚙️ Key Features Modern Fabric Flame Retardant Testers incorporate several features to ensure accurate and reliable testing:- Adjustable Burner Angles: Allowing tests at various orientations (e.g., 0°, 45°, 90°) to simulate different real-world scenarios. Automated Ignition Systems: Providing consistent flame application and reducing operator variability. - Digital Timing Mechanisms: Accurately recording ignition time, flame spread, after-flame, and afterglow durations. - Transparent Observation Windows: Enabling safe monitoring of the test without exposure to hazards. - Compliance with International Standards: Meeting protocols such as ASTM D6413, ISO 6941, and EN ISO 15025 for standardized testing procedures. Testing Standards Fabric Flame Retardant Testers are designed to comply with various international standards, including: - ASTM D6413: Standard Test Method for Flame Resistance of Textiles (Vertical Test). - ISO 6941: Textiles — burning behavior — Measurement of flame spread properties of vertically oriented specimens. - EN ISO 15025: Protective clothing — Protection against heat and flame — Method of test for limited flame spread. ️ How It Works- Sample Preparation: A fabric specimen is cut to specified dimensions and conditioned as per standard requirements.
- Mounting: The sample is mounted vertically or at a specified angle in the testing chamber.
- Ignition: A controlled flame is applied to the fabric for a predetermined time.
- Observation: The tester records ignition time, flame spread, after-flame time, and afterglow time.
- Evaluation: Results are compared against standard criteria to determine compliance.
- Prepare the Sample
- Mount the Sample
- Set Up the Burner Position the burner at the required angle (usually 90° for vertical tests).
- Ignite the Flame - Apply the flame to the bottom edge of the fabric for 12 seconds.
- Observe and Measure - Start timing when flame is applied.
- Record the Results
- Compare with Standards

Oscillation type water bath Dyeing Machine
Oscillation Type Water Bath Dyeing Machine
An Oscillation Type Water Bath Dyeing Machine is a laboratory apparatus designed for dyeing and washing textile samples under controlled temperature conditions. It combines a heated water bath with an oscillating mechanism to ensure uniform dye penetration and consistent coloration across fabric or yarn samples. Key Features of Oscillation Type Water Bath Dyeing Machine - Oscillating Mechanism: Provides back-and-forth movement to agitate the dye solution, ensuring even contact between the dye and the textile sample.- Multiple Beaker Capacity: Typically accommodates 12 to 24 beakers, allowing simultaneous processing of multiple samples under identical or varied conditions. - Digital Temperature Control: Maintains precise temperature settings, usually up to 99°C, suitable for various dyeing processes including atmospheric dyeing, scouring, and bleaching.- Adjustable Oscillation Speed: Offers variable speed settings, commonly ranging from 50 to 200 cycles per minute, to accommodate different fabric types and dyeing requirements. - Programmable Settings: Advanced models come with programmable controllers, allowing users to set and save multiple dyeing protocols for repeatability and efficiency. Durable Construction: Constructed with high-quality stainless steel (e.g., SUS304), ensuring resistance to corrosion and longevity even under rigorous laboratory conditions. ✅ Benefits of Oscillation Type Water Bath Dyeing Machine - Uniform Dyeing Results: The oscillation mechanism ensures consistent dye penetration, reducing the risk of uneven coloration and enhancing the reproducibility of results.- Efficiency in Sample Processing: The ability to process multiple samples simultaneously accelerates laboratory workflows and facilitates comparative studies. - Versatility: Suitable for a range of applications including dyeing, washing, scouring, bleaching, and fastness testing across various textile materials.- Energy and Resource Conservation: Designed for low liquor ratios (e.g., 1:5 to 1:20), these machines minimize water and chemical usage, promoting sustainable laboratory practices. - Enhanced Safety and Cleanliness: Enclosed beaker systems reduce the risk of spills and exposure to chemicals, ensuring a safer laboratory environment. Typical Applications of Oscillation Type Water Bath Dyeing Machine - Textile Research and Development: Ideal for developing and testing new dye formulations and processes on a small scale before scaling up to production levels. Quality Control: Used in quality assurance laboratories to assess color fastness, dye uptake, and other critical parameters of textile products.- Educational Purposes: Serves as a practical tool in academic settings for teaching dyeing principles and techniques. In summary, the Oscillation Type Water Bath Dyeing Machine is an essential tool in textile laboratories, offering precise control over dyeing parameters, improving efficiency, and ensuring high-quality, reproducible results across various textile materials. Features of Oscillation Type Water Bath Dyeing Machine:- Oscillating Mechanism - Provides back-and-forth movement of beakers for uniform dye penetration and sample agitation.
- Multiple Beaker Capacity - Supports dyeing of 12–24 samples simultaneously, ideal for comparative lab testing.
- Digital Temperature Control - Maintains precise water bath temperature (typically up to 99°C), essential for consistent dyeing.
- Variable Oscillation Speed - Adjustable speed settings (e.g., 50–200 cycles/min) to suit different materials and processes.
- Programmable Settings - Allows setting of temperature, time, and speed for repeatable and automated dyeing cycles.
- Stainless Steel Construction - Corrosion-resistant frame and bath for durability in chemical environments.
- Beaker Safety Holders - Secure placement of beakers to prevent spills and maintain consistent treatment.
- Compact Design - Lab-friendly size for easy integration into research and quality control spaces.
- Low Liquor Ratio Operation - Efficient dyeing using minimal dye bath volume (e.g., 1:5 to 1:20), reducing chemical and water use.
- Quiet and Stable Performance

water bath/Shaker bath Dyeing machine
Color Matching Cabinet-Light Box
Color Matching Cabinet-Light Box

Color Matching Cabinet-Light Box
HTHP Glycerin bath dyeing machine
HTHP Glycerin Bath Dyeing Machine
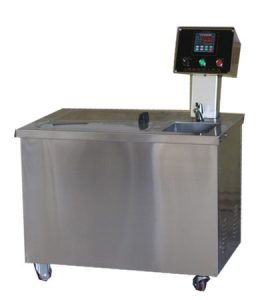
HTHP dyeing machine
- High Temperature Capability - Operates up to 140°C or more, ideal for disperse dyeing of polyester which requires elevated temperatures.
- Glycerin as Heat Transfer Medium - Glycerin allows for precise and uniform heating beyond the boiling point of water, without pressure buildup as in steam-based systems.
- Small Sample Dyeing - Used for lab-scale dyeing of fabric or yarn samples (commonly 5–10 g per tube), useful in R&D or color matching.
- Multiple Sample Capacity - Usually has multiple dyeing tubes/chambers for simultaneous dyeing of several samples under identical conditions.
- Accurate Temperature and Time Control - Digital or microprocessor-based controllers regulate temperature, heating rate, and timing precisely.
- Uniform Dyeing - Ensures even dye penetration due to consistent heat distribution and controlled rotation or agitation.
- Energy Efficient Glycerin’s heat retention reduces energy consumption compared to steam systems.
- Compact and Durable Design - Bench-top design, made from stainless steel and heat-resistant components for long life and lab use.
- Uniform Heating with Glycerin - Glycerin provides consistent heat transfer, ensuring even dye uptake and minimizing shade variation.
- Energy Efficient- Glycerin retains heat longer, reducing energy consumption compared to traditional steam-based dyeing.
- Accurate Process Control - Precise temperature and time control enhance reproducibility and dyeing consistency.
- Ideal for Lab and Sample Work - Perfect for R&D, shade matching, and recipe development with small fabric or yarn samples.
- Multi-Sample Dyeing - Allows multiple samples to be dyed simultaneously under identical conditions, saving time and effort.
- Compact and Safe - Bench-top design fits in laboratories and is safer than high-pressure steam systems.
- Low Maintenance - Simplified operation and fewer mechanical parts compared to steam-based systems lower upkeep needs.
- Faster Dyeing Cycles- Glycerin heats and cools quickly, reducing overall dyeing time.
- High-Temperature Operation - Capable of dyeing up to 140–150°C, suitable for synthetic fibers like polyester.
- Glycerin as Heat Medium - Uses glycerin for uniform, efficient heat transfer without generating high steam pressure.
- Multiple Dyeing Chambers - Usually equipped with 6–24 tubes for simultaneous multi-sample dyeing under identical conditions.
- Digital Temperature Controller- Offers precise control of temperature, time, and heating rate with programmable settings.
- Compact and Lab-Friendly Design - Bench-top model, easy to operate in laboratory environments with limited space.
- Stainless Steel Construction - Corrosion-resistant and durable for long-term, high-temperature operation.
- Safety Features - Includes over-temperature protection and thermal insulation to prevent heat loss and ensure operator safety.
- Agitation or Sample Rotation- Some models offer rotation or agitation for uniform dye penetration.
- Energy Efficient Heating - Glycerin’s heat retention improves energy efficiency over water- or steam-based systems.
- Low Maintenance - Simplified mechanical system reduces the need for frequent servicing.
Steam Soaping machine
Steam Soaping Machine
A Steam Soaping Machine is a specialized laboratory apparatus used in textile dyeing processes, particularly for post-dyeing treatments like soaping, which enhances color fastness and removes unfixed dyes from fabric samples. This machine is designed to perform soaping treatments on dyed textile samples using steam. Soaping is a critical step in dyeing, especially for reactive dyes, as it removes unfixed dye particles, ensuring better color fastness and preventing dye bleeding. The steam soaping process involves treating the dyed fabric with a soaping solution at elevated temperatures, facilitated by steam, to achieve optimal results. ⚙️ Key Features of Steam Soaping Machine - Beaker Material: Constructed with high-grade 316L stainless steel for excellent corrosion resistance and durability.- Operation Modes: Offers both automatic control and manual water filling options, providing flexibility in operation. - Drainage System: Equipped with an automatic drainage device for efficient removal of used solutions.- Temperature Control: Precise temperature regulation to maintain optimal soaping conditions.- Compact Design: Suitable for laboratory settings, occupying minimal space while delivering effective performance. ✅ Benefits of Steam Soaping Machine - Enhanced Color Fastness: Effectively removes unfixed dyes, resulting in improved wash and rub fastness of the fabric.- Efficient Processing: Reduces the time required for post-dyeing treatments compared to conventional methods.- Consistent Results: Provides uniform treatment across samples, ensuring reproducibility in testing and quality control.- Resource Optimization: Minimizes water and chemical usage through controlled processing parameters.- Versatility: Applicable to various fabric types and dye classes, making it a valuable tool in research and development. Typical Applications - Laboratory Testing: Used in dyeing laboratories for evaluating the fastness properties of dyed samples. - Research and Development: Assists in developing and optimizing dyeing processes and formulations. - Quality Control: Ensures that dyed fabrics meet specified fastness standards before bulk production. In summary, a Steam Soaping Machine is an essential laboratory instrument in the textile industry, facilitating efficient and effective post-dyeing treatments to enhance the quality and durability of dyed fabrics. Features of Steam Soaping Machine:- High-Grade Stainless Steel Beakers - Made from 316L stainless steel for excellent chemical and heat resistance.
- Steam-Based Heating - Uses direct or indirect steam to maintain consistent high temperatures ideal for soaping.
- Precise Temperature Control - Maintains stable temperatures (typically up to 98–100°C) for effective removal of unfixed dyes.
- Automatic and Manual Modes - Offers both programmable automatic cycles and manual operation for flexibility.
- Beaker Agitation or Rotation - Ensures uniform soaping action across fabric surfaces.
- Automatic Drainage System - Efficiently removes used soaping solution to speed up cycle changeovers.
- Compact Design - Fits well in lab settings while allowing multiple samples to be processed simultaneously.
- Safety Features - Includes pressure and temperature protection systems to ensure safe operation.
- Low Water and Chemical Use - Designed for minimal liquor ratios, enhancing sustainability.
- User-Friendly Interface - Simple digital controls or touch panel for easy operation and cycle programming.
- Prepare the Dyed Sample - After dyeing, rinse the fabric to remove surface dye and prepare it for soaping.
- Load the Fabric - Place the dyed fabric or sample into the beakers or holders inside the machine.
- Add Soaping Solution - Pour the prepared soaping agent (usually a detergent solution) into the beakers or tank as per recipe.
- Set Parameters
- Start the Cycle - Begin the soaping process. The machine will heat the solution using steam and agitate/rotate the beakers for even treatment.
- Drain and Rinse - After the cycle ends, the machine may auto-drain. Rinse the fabric with warm water to remove residual chemicals.
- Unload the Samples - Carefully remove the fabric. Inspect for evenness and color fastness improvement.
- Clean the Machine - Rinse and dry the beakers or tank to maintain hygiene for the next use.
