Laboratory hydro Extractor
$0.00
Laboratory Hydro Extractor
A Laboratory Hydro Extractor is a compact, high-speed centrifuge used in textile labs to remove excess water from fabric or yarn samples after dyeing or washing. It works on the principle of centrifugal force, efficiently reducing moisture content before drying.
Key Features:
- Centrifugal Water Extraction – Uses high-speed spinning (typically 1400–2800 RPM) to extract water from textiles.
- Stainless Steel Inner Basket – Perforated drum holds fabric/yarn securely and allows water to drain efficiently.
- Compact Lab Design – Space-saving unit designed specifically for laboratory sample sizes.
- Digital Timer and Speed Control – Allows precise setting of spin duration and RPM to match sample needs.
- Safety Lock System – Ensures the lid remains closed during operation for user safety.
- Quick Water Removal – Significantly reduces drying time by extracting up to 90–95% of water content.
- Low Noise and Vibration – Balanced design ensures quiet and stable operation.
Applications:
– Dewatering of dyed or washed fabric/yarn lab samples.
– Pre-drying step in dyeing and finishing tests.
– Useful in textile, apparel, and dyeing labs for faster workflow.
Benefits of Laboratory Hydro Extractor:
- Efficient Water Removal – Rapidly extracts 90–95% of water from samples, reducing drying time significantly.
- Saves Time and Energy – Cuts down the load on dryers and shortens total processing time in lab workflows.
- Improves Sample Quality – Gentle spinning preserves fabric structure, avoiding damage or distortion.
- Precise Control – Adjustable speed and timer ensure optimal settings for different fabric types.
- Compact and Lab-Friendly – Small footprint ideal for laboratory use with limited space.
- User Safety – Safety lock prevents lid opening during operation, protecting the user.
- Cost-Effective – Reduces the need for extended dryer use, saving on electricity and equipment wear.
- Versatile Use – Suitable for yarn, fabric, and garment samples across various fiber types.
Features of Laboratory Hydro Extractor:
- High-Speed Centrifugal Operation – Typically runs at 1400–2800 RPM for quick and efficient water removal.
- Stainless Steel Inner Drum – Corrosion-resistant, perforated basket for durability and efficient water drainage.
- Digital Timer and Speed Control – Allows precise control of spin duration and speed based on sample type.
- Compact and Portable Design – Ideal for lab environments with limited space.
- Safety Lock Mechanism – Prevents the lid from opening while the machine is in operation.
- Shock Absorption System- Reduces vibration and noise for smooth, stable performance.
- Quick Cycle Times – Short dewatering cycles improve lab throughput and efficiency.
- Low Maintenance Design – Simple mechanical setup with easy-to-clean components.
- Sample Versatility – Suitable for small fabric swatches, yarns, and small garments.
- Energy Efficient – Uses minimal power while delivering high performance.
How to Use a Laboratory Hydro Extractor:
- Prepare the Sample – After dyeing or washing, gently squeeze excess water from the fabric or yarn sample by hand.
- Load the Sample – Open the lid and place the sample evenly in the stainless steel drum. – Avoid overloading or uneven placement to maintain balance.
- Close the Lid securely – Ensure the safety lid is properly closed and locked.
- Set the Timer and Speed – Use the control panel to set the spin time (typically 1–5 minutes) and RPM suitable for the sample type.
- Start the Machine- Press the start button. The extractor will spin at the selected speed to remove water via centrifugal force.
- Wait for Spin Completion – The machine will automatically stop after the timer runs out.
- Unload the Sample – Once the drum stops completely, open the lid and carefully remove the sample.
- Proceed to Drying – The dewatered sample can now be air-dried or placed in a drying oven or stenter.
Safety Tips:
– Always ensure the lid is closed before starting.
– Do not open the lid while the drum is spinning.
– Balance the load to prevent vibration or noise.
Laboratory Hydro Extractor dealer In Bangladesh,
Lab Hydro Extractor Importer in Bangladesh,
Laboratory Hydro in Bangladesh,
Lab Hydro in Bd,
Hydro Extractor Price in Bangladesh,
Laboratory Hydro Extractor in Bangladesh,
Laboratory hydro Extractor
Small Dehydrator
Model: DUN-SD185
Brad: DUNLIN
Origin: China
Application scope of small dehydrator:
This dehydrator is a kind of small sample dehydration
experimental equipment with micro capacity
Parameter specification:
Inner barrel size: 185mm in diameter * 80Hmm
Outer barrel size: ∮200*125Hmm
Overall dimension: 290 * 220* 295Hmm
Power supply: single phase 220 V / 50 Hz power: 60 W speed: 1800 R / min
Laboratory hydro Extractor Machine Dunlin price in Bangladesh
Laboratory hydro Extractor Machine Dunlin in textile
Textile testing equipment in Bangladesh
Textile testing equipment in Dhaka
Textile testing equipment in Uttara
MAAM tex Laboratory hydro Extractor Machine Dunlin price in Bangladesh
Related products
Fabric Stiffness Tester
Fabric Stiffness Tester
Fabric Stiffness Tester is a lab instrument used to measure the stiffness or flexural rigidity of fabric materials. It evaluates how resistant a fabric is to bending, which influences its drape, comfort, and handling characteristics. Purpose of Fabric Stiffness Tester: To determine the stiffness of textiles by measuring the bending length and calculating flexural rigidity, often using methods like the Cantilever Test (as per ASTM D1388 or ISO 9073-7). Working Principle of Fabric Stiffness Tester: A fabric strip is slid over a horizontal platform until its free end bends under its own weight to a specific angle (usually 41.5°). The length at which this occurs is used to calculate bending length and stiffness. Main Components of Fabric Stiffness Tester: - Test Platform: Flat surface for sample movement. - Graduated Scale: Measures the overhanging length of fabric. - Angle Indicator: Guides the measurement based on standard deflection angle. - Fabric Clamp or Guide: Helps place and move the sample smoothly. Applications of Fabric Stiffness Tester: - Apparel fabrics (e.g., for comfort and drape analysis) - Technical textiles (e.g., automotive, medical fabrics) - Paper, nonwovens, and films Benefits of Fabric Stiffness Tester:- Accurate Measurement of Flexibility - Provides reliable data on fabric stiffness, essential for quality control and product development.
- Improves Product Comfort - Helps assess how soft or rigid a fabric will feel in clothing or furnishings.
- Supports Material Selection - Aids designers and engineers in choosing the right fabric for specific applications based on stiffness.
- Quality Assurance - Detects fabric inconsistencies or defects that affect handling or drape.
- Standards Compliance - Enables testing as per international standards like ASTM D1388 and ISO 9073-7 for global product approval.
- Quick and Simple Operation - Delivers fast results with minimal operator training or preparation.
- Applicable to Multiple Materials - Suitable for woven, nonwoven, knitted fabrics, paper, and films.
- Enhances R&D Accuracy - Supports consistent material testing during product innovation and textile finishing.
- Graduated Measurement Scale - Precise scale to measure overhang length for accurate stiffness calculation.
- Flat Test Platform - Smooth, level surface ensures consistent and reliable fabric movement.
- Standard Deflection Angle Guide - Built-in 41.5° angle reference for consistent stiffness testing (per ASTM/ISO).
- Manual or Motorized Models - Available in both types for simple or automated operation depending on lab needs.
- Compact Design - Space-saving unit ideal for textile labs and quality control rooms.
- Sample Holder or Clamp - Ensures correct alignment and smooth feeding of fabric strips during testing.
- Durable Construction - Made of corrosion-resistant materials like stainless steel or aluminum for long-term use.
- Compliance with Standards - Supports methods like ASTM D1388, ISO 9073-7 for stiffness testing of fabrics.
- Lightweight and Portable - Easy to move and use in various lab settings.
- Low Maintenance - Simple mechanical parts require minimal servicing.
- Prepare the Sample - Cut the fabric into a rectangular strip (e.g., 25 mm × 200 mm), as per standard.
- Place the Sample - Lay the fabric strip flat on the test platform with one end aligned at the zero mark.
- Slide the Fabric - Gently push the fabric forward so it slowly overhangs the platform.
- Watch for Deflection - Stop sliding when the free end of the fabric bends down to the reference angle (typically 41.5°).
- Read the Bending Length - Measure the overhang distance from the scale. This is the bending length (C).
- Calculate Flexural Rigidity
- Repeat for Accuracy - Test both warp and weft directions and average the results for better accuracy.

Stretch Recovery Tester Static Method
Stretch Recovery Tester Static Method

Stretch Recovery Tester
- A sample is stretched to a predetermined extension or force.
- The stretch is maintained for a set period.
- After removing the load, the recovery (return to original length) is measured after a fixed time.
- The fabric sample is clamped and stretched to a specific length or force.
- It’s held for a fixed duration (e.g., 1–5 minutes).
- The tension is released, and the sample is allowed to recover.
- The recovered length is measured after a set time.


Stretch Recovery Tester
Color fastness to washing machine
COLOR FASTNESS TO WASHING MACHINE
Color fastness to washing machine refers to a fabric’s resistance to fading or bleeding when subjected to washing processes. This test measures how well the dye or colorant stays on the fabric when exposed to water, detergent, heat, and mechanical action—conditions typically found in household or industrial washing machines. Purpose of Color fastness to washing machine - To evaluate the durability of dyed or printed textiles during laundering.- Essential for determining fabric quality and suitability for end-use (e.g., clothing, upholstery). Test Method Usually based on international standards such as: - ISO 105-C06 - AATCC 61- IS 3361- AATCC 28/61/132/151/190, BS 1006 C01-C05, ISO 105 Part C01-C06/C08/D01, M&S C4/C5/C10A/P3B, FTMS 191-5610, NEXT TM2/3/5, GB/T 5711/3921 Procedure (Simplified)1. Sample Preparation: - A fabric specimen is stitched with undyed adjacent fabrics (usually cotton or wool).2. Washing: - Washed in a laboratory washing machine using standard detergent, water, and specific temperature/time settings (e.g., 40°C for 30 minutes).- Drying: - After washing, the sample is dried, typically air-dried or tumble-dried.4. Evaluation: - Color change and staining on adjacent fabrics are assessed using a gray scale (1 to 5 scale; 5 = no change, 1 = severe change). - Results may also be evaluated visually under standard lighting.
- Supports Brand Reputation - Reliable color fastness contributes to a premium product image and consistent performance.4. Compliance with Standards - Meets industry requirements (e.g., ISO, AATCC), crucial for export, certifications, and regulatory compliance.
- Improves Process Control- Helps identify dyeing or finishing process issues early, leading to better production control.6. Reduces Rework and Waste - Minimizes production losses due to color defects after washing.
- Essential for Specific End Uses - Critical for items subject to frequent washing (e.g., uniforms, baby clothes, hospital linens).8. Supports Material Selection - Guides textile manufacturers in choosing appropriate dyes and fabrics for specific applications.
- Assessment of Color Change and Staining- Evaluates both the fabric’s color retention and the staining of adjacent fabrics using grey scales (1 to 5 rating).4. Multi-Fiber Fabric Use - Tests include fabric stitched with adjacent test strips (cotton, wool, etc.) to assess color bleeding onto different fibers.
- Multiple Test Options - Includes domestic, accelerated, and industrial washing conditions depending on the end-use of the fabric.6. Temperature and Time Control - Precise control over wash temperature (e.g., 40°C, 60°C) and duration (e.g., 30 mins), simulating specific washing cycles.
- Detergent and Additive Use - Uses standardized detergent formulations with/without optical brighteners, and sometimes alkaline or oxidizing agents.8. Reproducible and Quantifiable - Provides repeatable results that can be objectively measured and documented.
- Applicability to All Textile Types - Suitable for dyed, printed, or coated fabrics across various fibers (cotton, polyester, blends, etc.).
- Rate of temperature rise: Maximum speed for 2ºC/min 7. Internal materials: Imported Stainless Steel 316L 8. Control panel: Touch screen
- Rack point control function helps to replace containers easily 10. Safety device: Safety door switch, over-temperature protector and dry heating protector 11. Heating media: Distilled water 12. Power supply: AC220V 50Hz 30A
Automatic Bobbin Hydro extractor
Automatic Bobbin Hydro extractor

Automatic Bobbin Hydro extractor
- Computer system: Foshan HuaGao Chinese English computer, equipped with LG PLC.
- Electromagnetic valve: Ningbo Jiaerling
- Frequency converter: Use Made in China frequency converters.
- Pump: self-made high head and large flow centrifugal water pump.
- Main pump motor: Anhui Wannan Motor.
- Master cylinder liquid level: Use 4-20mA analog signal output.
- Level of deputy temporary worker: use foam water level gauge. (American Mike)
- Temperature detection and display: digital temperature display instrument, dual temperature measuring probes.
- The safety system has a triple cylinder head safety interlock mechanism, and the main cylinder is equipped with a stainless
- steel safety valve.
- Heat exchanger: external spacer heating.
- Feeding system: Quantitative feeding based on the process curve.
- Circulation system: The main pump flows internally and externally, which is automatically controlled by a computer or manually controlled by a relay.
- Valves: Y valves are used for heating, stainless steel Y valves are used for single inlet and single row, and other Y valves are produced by joint ventures.
- Temperature control: on-off temperature control, controlled by a computer, with automatic heating, cooling, and insulation functions.
- Dyeing method: air cushion type.
- Opening method: manual opening.
- Surface treatment: polishing inside and outside the cylinder.
- Cage: Each dyeing machine is equipped with butterfly blades and self-locking locks.
- Body plate: high-quality stainless steel. (S31603)
- Bath ratio: 1:5-1:6
- Chemical material system: including heating and water adding functions, including overflow type salt melting device.
- Overflow cleaning: The cleaning port is installed on the upper part of the cylinder port, and the bottom of the cylinder is filled with water, while the cylinder is drained for easy cleaning.
- Commutation method: Novel "U" type commutation.
- Random accessories: Each model comes with one set of mechanical seals, pot mouth rings, and reversing seals for the main and auxiliary pumps.
Automatic Bobbin Hydro extractor
Orbital Shaker Machine
Orbital Shaker Machine

Orbital Shaker Machine
- Orbital Motion - Provides a smooth circular shaking pattern, ideal for gentle mixing without foaming or splashing.
- Adjustable Speed Control - Speed typically ranges from 50 to 300 RPM, depending on the model and application.
- Timer Function - Allows users to set shaking time from minutes to hours for precise control of experiments.
- Platform with Clamps or Mats - Holds flasks, beakers, test tubes, or trays securely during operation.
- Digital Display (in advanced models) - Shows speed and time settings for accurate and repeatable performance.
- Variable Capacity - Available in sizes to accommodate different lab needs—from a few samples to dozens.
- Quiet Operation - Designed for minimal vibration and noise during continuous use.
- Uniform Mixing - Ensures even distribution of dyes, chemicals, or cultures without manual stirring.
- Gentle Agitation - Ideal for delicate samples like cell cultures or fabric swatches, reducing damage or splashing.
- Hands-Free Operation - Allows continuous, unattended mixing—improving lab efficiency and freeing up personnel.
- Customizable Settings - Adjustable speed and timer let users tailor mixing to specific sample types and needs.
- Versatile Use - Suitable for a wide range of applications including dye mixing, sample incubation, chemical reaction enhancement, and microbial growth.
- Enhanced Reproducibility - Consistent shaking patterns and digital controls ensure repeatable results across experiments.
- Reduces Human Error - Automated operation minimizes variability and manual handling mistakes.
- Compact and Lab-Friendly - Takes up minimal space while accommodating multiple sample containers.
- Orbital Shaking Motion - Moves samples in a circular path for uniform and consistent mixing.
- Variable Speed Control - Adjustable shaking speed (typically 50–300 RPM) to suit different sample types.
- Digital Timer - Programmable run time for precise and repeatable operations.
- Flat Platform Design - Accommodates flasks, beakers, tubes, or trays with optional clamps or non-slip mats.
- LCD or LED Display (in advanced models) - Shows speed, time, and operating status clearly.
- Quiet Operation - Low-noise motor and stable base minimize vibration and disturbance in the lab.
- Overload Protection - Prevents motor damage from excessive weight or resistance.
- Compact and Durable Build - Designed to fit standard lab benches and withstand regular use.
- Versatile Capacity Options - Available in various sizes to handle different numbers and sizes of containers. User-Friendly Interface - Simple control panel for easy setup and operation.

Fatigue tester for Elastic fabric
Fatigue Tester for Elastic Fabric
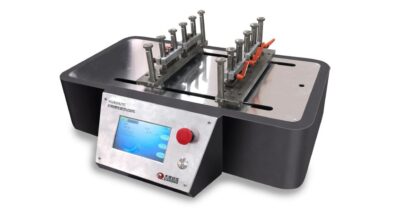
Fatigue tester for Elastic fabric
- Adjustable Stretch Range - Allows setting stretch levels (e.g., 0–100%) to simulate real-life fabric use.
- High-Cycle Capability - Supports up to millions of stretch-relax cycles for long-term fatigue analysis.
- Touch Screen Control - 7-inch color display for easy setup, monitoring, and data entry.
- Servo Motor Driven - Ensures precise and smooth linear motion during testing.
- Customizable Speed - Adjustable test speed (e.g., up to 40 cycles per minute) based on test requirements.
- Multi-Sample Testing - Some models allow testing multiple specimens simultaneously.
- Cycle Counter with Alarm - Built-in counter with programmable stop after preset cycles and auto-alert feature.
- Durable Construction - Robust metal frame suitable for continuous testing in lab environments.
- Standard Compliance - Designed to follow standards like GB/T 37635 for elastic fabric testing.
- Prepare the Sample
- Mount the Sample - Secure both ends of the fabric in the upper and lower clamps.
- Set Test Parameters
- Start the Test - Press start on the touch screen interface. - The machine will cyclically stretch and release the sample.
- Monitor Progress - Observe operation or let it run automatically.
- Remove and inspect - Take out the fabric and measure elongation, recovery, or visual defects.
- Record and Compare Results - Compare with initial measurements or standard performance criteria.
Fatigue tester for Elastic fabric
Rainin Digital Pipette
Rainin Digital Pipette
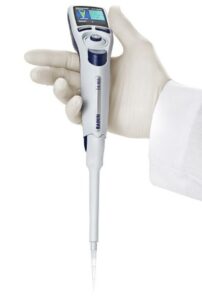
Digital Pipette
- Digital Volume Setting
- High Accuracy and Precision
- Ergonomic Design
- Easy Calibration and Maintenance
- Durable and Chemically Resistant - Built with high-quality materials that resist damage from chemicals and frequent use.
- Models and Volume Ranges - Available in single-channel and multi-channel versions.
- LTS (LiteTouch System) - Many Rainin pipettes use the LTS tip system which reduces tip ejection force and ensures a consistent seal.
- Compliance and Traceability - Some digital models offer data storage or integration with lab information systems for traceability.
- High Accuracy and Precision - Ensures reliable and reproducible results, essential for sensitive experiments.
- Digital Volume Control - Reduces human error with easy and precise volume setting via digital interface.
- Ergonomic Design- Minimizes hand strain and fatigue during prolonged use; ideal for repetitive pipetting tasks.
- LiteTouch System (LTS) - Eases tip attachment and ejection, reducing risk of RSI (Repetitive Strain Injury) and improving comfort.
- Versatile Volume Range - Available in multiple models to handle volumes from microliters to milliliters.
- Durable and Reliable - Built with high-quality materials for long life and resistance to chemicals and frequent use.
- Easy Maintenance and Calibration - Simplified calibration and cleaning ensure long-term performance and compliance.
- Data Integrity and Traceability -Some models store data, supporting audit trails and regulatory compliance.
- Enhanced Productivity - Quick setup, easy operation, and consistent performance speed up lab workflows.
- Digital Volume Adjustment - Precise and easy-to-read digital display for accurate volume setting.
- High Precision and Accuracy- Delivers consistent results, meeting ISO and GLP/GMP standards.
- Ergonomic Design- Lightweight, balanced with low plunger and tip ejection force to reduce fatigue.
- LiteTouch Tip Ejection System (LTS) - Reduces tip attachment/ejection force, improving comfort and consistency.
- Durable Construction - Built with high-quality, chemically resistant materials for long-term use.
- Wide Volume Range - Available in multiple models from 0.1 µL to 10 mL.
- Single-Channel and Multi-Channel Options - Suitable for various applications including high-throughput assays.
- Autoclavable Components- Some parts can be autoclaved for sterilization and contamination control.
- Easy Calibration and Maintenance - User-friendly calibration settings with accessible parts for cleaning.
- Optional Electronic Models - Some versions include programmable features, multiple modes (e.g., reverse pipetting), and memory storage.
Fabric air permeability tester
Fabric Air Permeability Tester
Fabric Air Permeability Tester is a lab instrument used to measure how easily air passes through a fabric. It quantifies the air permeability, which is crucial for evaluating breathability, comfort, and functional performance in textiles. Purpose Fabric Air Permeability Tester: It determines the rate of airflow through a fabric sample under a set air pressure, typically reported in units like cm³/cm²/s or L/m²/s. Working Principle: The tester creates a pressure difference across the fabric sample and measures the volume of air flowing through it. Higher air permeability means the fabric is more breathable. Main Components of Fabric Air Permeability Tester: - Test Head / Clamp: Holds the fabric securely without leakage. - Pressure Regulator: Maintains a constant air pressure during testing. - Flow Meter or Digital Sensor: Measures the actual airflow rate through the fabric. - Display Unit: Shows readings of air permeability instantly. Applications of Fabric Air Permeability Tester: - Performance textiles (sportswear, PPE) - Technical fabrics (filters, tents, airbags) - Medical textiles (masks, gowns) - Nonwovens and industrial materials Benefits of Fabric Air Permeability Tester:- Accurate Breathability Measurement - Precisely measures how breathable a fabric is, essential for comfort and performance.
- Supports Quality Control - Ensures consistent air permeability in fabric batches, critical for products like PPE, sportswear, and filters.
- Enhances Product Design - Helps in selecting or engineering fabrics with the right airflow properties for specific uses.
- Standard Compliance - Conforms to international testing standards (e.g., ASTM D737, ISO 9237), ensuring global credibility.
- Quick and Reliable Testing - Provides rapid results, increasing lab efficiency and production decision-making speed.
- Wide Material Compatibility - Suitable for woven, nonwoven, knitted fabrics, and even paper or coated materials.
- Improves Functional Performance - Helps optimize products for ventilation, moisture control, and thermal comfort.
- Reduces Product Failure - Identifies underperforming fabrics early, minimizing risks in high-performance applications.
- Digital Display - Shows air permeability readings clearly in units like L/m²/s or cm³/cm²/s.
- Precise Test Head/Clamp - Provides an airtight seal to prevent air leakage and ensure accurate results.
- Adjustable Pressure Settings - Allows testing under various pressure drops (e.g., 10–2500 Pa), depending on fabric type.
- Automatic Airflow Measurement - Built-in sensors or flow meters capture airflow rate automatically for quick analysis.
- Multiple Test Area Sizes - Interchangeable test plates to match different sample sizes and standard requirements.
- Data Logging and Export - Some models include USB or software connectivity for storing and exporting test results.
- Standard Compliance - Conforms to ASTM D737, ISO 9237, BS 5636, DIN 53887, etc.
- Robust Construction - Built with corrosion-resistant materials and durable components for long-term lab use.
- Low Maintenance - Simple cleaning and calibration process for reliable performance.
- Compact and User-Friendly Design - Ideal for lab benches and easy operation with minimal training.
- Prepare the Sample - Cut the fabric sample to the required size (usually circular, e.g., 20 cm²).
- Mount the Sample - Place the fabric securely in the test clamp or holder, ensuring no wrinkles or gaps.
- Set Test Parameters - Adjust the air pressure drop according to the fabric type or standard (e.g., 100 Pa).
- Start the Test - Turn on the air supply and start the airflow through the fabric.
- Read the Measurement - The digital display will show the air permeability value in the selected units.
- Record the Results - Note the readings or export data if the device supports it.
- Repeat if needed - Test multiple samples or areas for accuracy and average the results.
- Clean and Maintain - After testing, clean the clamp and ensure the device is calibrated regularly.
