Digital Elmendorf tearing tester
$0.00
Digital Elmendorf Tearing Tester
Digital Elmendorf Tearing Tester is a precision instrument used to measure the tear strength of materials like woven fabrics, paper, plastic films, and nonwovens. It determines how much force is required to continue tearing a pre-slit sample.
Key Functions of Digital Elmendorf Tearing Tester:
– Measures propagation tear resistance, not initial tear.
– Uses a pendulum to apply force; the energy lost during tearing is calculated to determine tear strength.
– Equipped with a digital display for direct reading of results in grams or millinewtons.
Core Components:
– Pendulum Arm: Applies tearing force.
– Clamps: Secure the sample before and after the tear.
– Cutting Blade: Creates a precise slit at the start of the test.
– Digital Display Unit: Shows the tearing force result clearly and instantly.
– Counterweights: Optional weights for increasing test range (for stronger materials).
Applications of Digital Elmendorf Tearing Tester:
– Testing tear resistance of:
– Textile fabrics (especially woven)
– Paper and cardboard
– Plastic films
– Nonwovens
– Packaging materials
Benefits of Digital Elmendorf Tearing Tester:
- Accurate Tear Strength Measurement – Provides precise data on tear resistance, critical for quality control and product performance.
- Digital Readout – Easy-to-read display gives instant, reliable results without manual calculations.
- High Reproducibility – Ensures consistent test outcomes due to controlled tearing angle and speed.
- Fast Testing Process – Simple loading and quick test cycle increase lab efficiency.
- Suitable for Various Materials – Tests a wide range of flexible materials like textiles, paper, plastic, and packaging.
- Customizable Range – Use of optional weights extends the test range for low to high tear strength materials.
- Low Sample Waste – Requires small fabric or material samples, reducing waste during testing.
- Standards Compliance – Meets international testing standards (e.g., ASTM D1424, ISO 13937) for credibility and uniformity.
Features of Digital Elmendorf Tearing Tester:
Digital Display – Provides accurate and direct reading of tear strength in grams, mN, or cN. Pendulum Mechanism – Uses a swinging pendulum to simulate tear propagation with consistent force. Adjustable Test Range – Includes interchangeable pendulum weights to test various material strengths.
- Precision Sample Clamp – Securely holds samples in place to ensure accurate tear initiation.
- Pre-Cutting Blade – Integrated knife creates a precise initial slit in the sample before tearing.
- User-Friendly Interface – Simple buttons and screen navigation for ease of operation.
- Standard Test Compliance – Compatible with ASTM D1424, ISO 1974, ISO 13937, and other tear strength standards.
- Sturdy Construction – Made with durable materials for long-lasting performance and stable operation.
- Compact Design – Space-efficient footprint ideal for laboratory environments.
- Data Output Options- Some models offer USB or printer connectivity for result documentation.
How to Use a Digital Elmendorf Tearing Tester:
- Prepare the Sample – Cut the material (fabric, paper, film, etc.) to standard size (typically 100 × 63 mm for textiles) and slit it with the pre-cutter as required.
- Select Pendulum Weight – Choose the appropriate pendulum or add counterweights based on expected tear strength.
- Calibrate the Machine – Set the pendulum to its starting position and zero the display.
- Clamp the Sample – Fix one half of the sample in the stationary clamp and the other in the moving clamp.
- Cut the Initial Slit – Use the integrated blade to make a precise cut at the marked slit area (usually 20 mm).
- Release the Pendulum – Trigger the pendulum to swing and tear the sample through the pre-slit.
- Read the Result – The digital display will show the tearing force automatically (in g, mN, or cN).
- Record or Export Data – Save or print the result if your model supports USB or printer connection.
- Reset for Next Test – Reposition the pendulum and prepare a new sample for the next cycle.
Safety Tip: – Always ensure your hands are clear before releasing the pendulum.
Digital Elmendorf tearing tester
Scope of application
It is used for the determination of the tear resistance of various woven
fabrics (Elmendorf method), and it can also be used for the determination
of the tear resistance of thick paper, plastic sheeting, electrical tape, etc.
Related standards
GB/T 3917.1 FZ/T60006 FZ/T75001 ISO1974/9290 ASTM D1424/5734
etc.
Instrument characteristics
1. Maximum 300N test range
2. Microcomputer control, digital decoding, support online
communication
3. Color touch screen control, Chinese and English menu operation
interface
4. Pneumatic clamping, automatic cutting
5. A variety of measurement units (cN, gf) selection
6. Fully automatic operation with safe operation protection.
7. Automatically increase potential energy
[Technical parameter]:
1. Test range: first gear: (0~16)N second gear: (0~32)N third gear: (0~
64)N fourth gear: (0~128)N fifth gear: (0~300)N
2. Test accuracy: ≤±0.2%F·S
3. Tearing length: 43mm (non-standard 30-60mm can be set)
4. Automatic incision length: (20±0.2)mm
5. Sample size: (100×63)mm
6. Specimen clamping: pneumatic way
7. Sample test: Up to 10 sets per group on the device side, and 30 sets
of data can be selected to be saved
8. Power supply: AC220V±10% 50Hz 100W
9. Dimensions: (650×660×680)mm
10. Weight: 50kg
[Sample of control interface]:(English version is also available.)
Related products
Controller For IR Dyeing Machine
Controller For IR Dyeing Machine
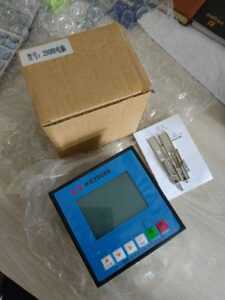
IR Dyeing machine controller
- Temperature Control:- Precisely regulates the infrared heaters to maintain uniform temperature across the dye bath. - Supports customizable heating curves (ramp-up, hold, and cool-down phases).
- Programmable Logic Control (PLC): - Allows operators to set and automate dyeing programs for different fabrics and dye types. - Supports multiple recipes or programs for different batches.
- Real-Time Monitoring and Feedback: - Monitors parameters like temperature, fabric rotation, bath circulation, and timing. - Provides real-time data and alarms for deviations.
- Touchscreen Interface / HMI (Human Machine Interface): - User-friendly interface for configuring and monitoring processes. - Multi-language support and graphical display of process curves.
- Data Logging and Traceability: - Records process data for quality control and traceability.
- Energy Efficiency Optimization: - Manages IR heater output to reduce energy usage. - Often includes features for auto shut-off or idle mode.
- Safety Features: - Includes emergency stop, over-temperature protection, and fault detection systems. 8. Connectivity: - Modern controllers may support Ethernet, Modbus, or other industrial communication protocols for integration into factory automation systems.
- Improved Dyeing Accuracy and Consistency
- Enhanced Energy Efficiency- Infrared heating is more energy-efficient than traditional heating methods.- The controller optimizes energy use by adjusting the IR output based on process needs, reducing overall energy consumption.
- Time Savings- Faster heating and cooling cycles due to infrared technology.- Automated processes reduce manual intervention and cycle times. 4. Better Process Control- Programmable dyeing cycles and precise control over each stage (heating, dyeing, rinsing, cooling).- Real-time monitoring and adjustments improve reliability.
- Reduced Water and Chemical Usage- More efficient dye penetration and fixation mean less water and fewer chemicals are needed for reprocessing or corrections.6. Lower Operational Costs
- Enhanced Safety Built-in alarms, emergency shut-off and automatic fault detection enhance operational safety.8. Data Logging and Traceability- Ability to record and review dyeing process data helps in quality control and troubleshooting.- Facilitates compliance with industry standards and audits.
- User-Friendly Operation- Modern touchscreen interfaces make it easier for operators to manage and monitor processes.- Multilingual support and visual feedback enhance usability.
Digital hot plate-magnetic stirrer
Digital hot plate-magnetic stirrer
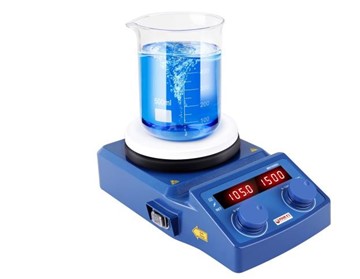
Digital hot plate-magnetic stirrer
- Magnetic Stirrer:
- Digital Display and Controls:
- Temperature Sensors: - Built-in or external probes (like a PT100 or thermocouple) for accurate temperature control.
- Precision and Control- Digital Interface: Allows accurate setting and monitoring of temperature and stirring speed.- Consistent Results: Ensures reproducibility in experiments and solution preparations.
- Efficient Mixing and Heating- Uniform Mixing: Magnetic stirring eliminates hotspots and ensures even distribution of solutes.- Simultaneous Operation: Ability to heat and stir at the same time improves efficiency.
- Safety Features- Overheat Protection: Prevents accidents by automatically shutting off at unsafe temperatures.- Sealed Surface: Reduces risk of contamination and easy to clean.
- Versatility
- Compact and User-Friendly- Takes up minimal bench space.- Simple to operate with user-friendly controls and displays.
- Durability- High-quality materials like ceramic or stainless steel tops resist corrosion and wear.
- Time-Saving Speeds up preparation of solutions and reactions compared to manual stirring and separate heating. Would you like these benefits presented in a slide format or for a product brochure?
Laboratory mini stenter Dryer
Laboratory mini stenter Dryer
A Laboratory Mini Stenter Dryer is a compact, lab-scale machine designed to simulate the drying and heat-setting processes used in textile finishing. It mimics the function of industrial stenter machines but on a much smaller scale, making it ideal for testing fabric behavior, shrinkage, and finish quality under controlled conditions. Key Features:- Controlled Heating System
- Adjustable Fabric Width
- Variable Speed Conveyor - Allows control over fabric dwell time for drying or heat-setting.
- Compact and Bench-Top Design - Space-saving design ideal for textile labs and R&D units.
- Digital Controls - Easy-to-use digital interface for setting temperature, conveyor speed, and process time.
- Transparent Viewing Window - Allows operators to monitor fabric movement and drying visually.
- Low Energy Consumption - Designed for lab use, consuming less power than industrial models.
- Accurate Simulation of Production - Mimics industrial stenter conditions on a lab scale, ideal for pre-production testing and R&D.
- Cost-Effective Testing - Enables testing and fabric finishing without the high cost or space requirements of full-scale machines.
- Energy Efficient - Consumes less power compared to large stenters, making it economical for small-scale or frequent use.
- Precise Control - Offers accurate control of temperature, speed, and fabric tension, ensuring consistent results.
- Space-Saving Design - Compact and bench-top friendly, perfect for laboratories with limited space.
- Multiple Applications - Useful for drying, heat-setting, shrinkage testing, and evaluating chemical finishes.
- Faster Development Cycles - Speeds up new product development by allowing rapid sample testing and adjustments.
- Improved Fabric Quality - Helps optimize finishing parameters for better dimensional stability, hand feel, and appearance.
- Safe and User-Friendly- Designed with lab safety in mind, including temperature safety controls and easy operation.
- Compact Bench-Top Design - Ideal for laboratory use with limited space requirements.
- Adjustable Temperature Control - Precise heating (usually up to 220–250°C) with digital controllers for accurate processing.
- Variable Conveyor Speed- Allows adjustment of fabric dwell time for different drying or heat-setting needs.
- Width Adjustment Mechanism - Equipped with clips or pins to stretch and fix fabric width-wise, simulating industrial stenter conditions.
- Transparent Viewing Window - Enables visual monitoring of fabric movement and drying inside the chamber.
- Digital Display Panel- Easy-to-use interface for setting and monitoring temperature, speed, and time.
- Stainless Steel Construction- Durable and corrosion-resistant for long-term use at high temperatures.
- Uniform Heat Distribution- Ensures consistent fabric treatment across the width.
- Safety Features- Over-temperature protection and insulated body for operator safety.
- Versatile Applications - Suitable for drying, heat-setting, shrinkage testing, and chemical finish evaluations.
Fastness Rotary Friction Tester
Fastness Rotary Friction Tester
A Fastness Rotary Friction Tester, also known as a Rotary Crock meter, is a specialized instrument used to evaluate the color fastness of textiles and materials when subjected to rotational rubbing. This test simulates the wear and friction that fabrics experience during use, helping manufacturers assess the durability of dyes and finishes. Purpose of Fastness Rotary Friction Tester The primary function of the Fastness Rotary Friction Tester is to determine how well a fabric's color withstands rubbing, both in dry and wet conditions. This is crucial for ensuring the longevity and appearance of textiles in real-world applications, such as clothing, upholstery, and footwear. Working Principle of Fastness Rotary Friction Tester The tester operates by applying a specified pressure to a fabric sample using a standardized rubbing finger covered with a test cloth. The rubbing finger performs a set number of rotational movements (typically 1.125 turns clockwise followed by 1.125 turns counterclockwise) over the fabric surface. After the test, the degree of color transfer to the test cloth and any changes in the fabric's appearance are evaluated against standardized gray scales. Common Testing Standards - AATCC 116: Colorfastness to Crocking: Rotary Vertical Crock meter Method. ISO 105 X16: Textiles—Tests for color fastness—Part X16: Color fastness to rubbing—small areas. - SATRA TM8: Color fastness to rubbing. Key Specifications of Fastness Rotary Friction Tester - Rubbing Head Diameter: Typically 16 mm. - Applied Pressure: Approximately 1134 grams (11.1 N). - Rotation: 1.125 turns clockwise followed by 1.125 turns counterclockwise. - Sample Size: Commonly 60 mm × 60 mm. - Test Cloth: Standardized white cotton cloth, either dry or wetted depending on the test condition. Benefits of Fastness Rotary Friction Tester - Realistic Simulation: Mimics the actual wear and friction fabrics undergo during use. - Versatility: Applicable to a wide range of materials, including textiles, leather, and printed fabrics. - Quality Assurance: Ensures products meet industry standards for color durability. - Standard Compliance: Aligns with international testing standards, facilitating global trade and quality benchmarks. Applications Fastness Rotary Friction Tester - Textile Industry: Assessing the color durability of garments, upholstery, and other fabric products. - Footwear Manufacturing: Testing the colorfastness of shoe uppers and linings. - Automotive Interiors: Evaluating the wear resistance of seat covers and other interior fabrics. Quality Control Laboratories: Routine testing to ensure product consistency and compliance with standards. Benefits of Fastness Rotary Friction Tester:- Accurate Colorfastness Evaluation- Provides precise assessment of how well fabric resists color loss and staining from rubbing.
- Simulates Real-World Wear - Recreates rotational friction found in actual use (e.g., seat covers, apparel wear points).
- Supports Wet & Dry Testing - Can test under both dry and wet conditions for comprehensive results.
- Standardized Testing - Complies with global standards (AATCC 116, ISO 105 X16), ensuring reliable and comparable results.
- Time-Saving & Efficient - Quick to set up and run, allowing for high-throughput testing in labs.
- Versatile Use- Suitable for textiles, leather, coated fabrics, and printed surfaces.
- Improves Quality Control - Identifies potential durability issues early in the production process.
- Enhances Product Performance - Helps in developing fabrics with better resistance to rubbing and abrasion.
- Rotary Rubbing Mechanism - Simulates 1.125 clockwise and 1.125 counterclockwise turns for realistic friction.
- Standardized Rubbing Head - Fixed diameter (typically 16 mm) with specified pressure (≈1134 g) for consistent results.
- Dry and Wet Testing Capability - Can perform tests using dry or wet rubbing cloths.
- Sample Holder- Secure and easy-to-use fixture for holding fabric samples in place.
- Test Cloth Mounting Arm- Quick attachment for standardized white rubbing cloths.
- Simple Operation - Manual or motorized operation depending on model; easy to handle for lab technicians.
- Compliance with Standards - Follows AATCC 116, ISO 105 X16, and SATRA TM8 protocols.
- Prepare the Sample - Cut a fabric piece (typically 60 × 60 mm) and condition it per standard requirements.
- Mount the Fabric - Secure the fabric sample on the sample holder or base plate of the tester.
- Attach Rubbing Cloth - Place a standard white test cloth (dry or wetted as required) over the rubbing head.
- Apply Pressure - Lower the rubbing head onto the fabric. Standard weight is about 1134 g.
- Start the Test - Operate the tester: the head performs 1.125 turns clockwise, then 1.125 turns counterclockwise.- Number of cycles (typically 10 or 20) is set based on the test standard.
- Remove and Inspect - After testing, remove the rubbing cloth and assess any color transfer using a gray scale.
- Evaluate Fabric Surface - Check the fabric for visible changes, fading, or wear.
- Record Results - Grade both staining and fabric change per standard gray scale ratings.

Rainin Digital Pipette
Rainin Digital Pipette
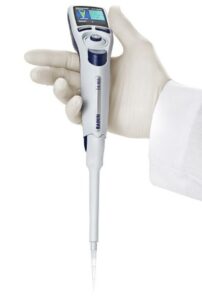
Digital Pipette
- Digital Volume Setting
- High Accuracy and Precision
- Ergonomic Design
- Easy Calibration and Maintenance
- Durable and Chemically Resistant - Built with high-quality materials that resist damage from chemicals and frequent use.
- Models and Volume Ranges - Available in single-channel and multi-channel versions.
- LTS (LiteTouch System) - Many Rainin pipettes use the LTS tip system which reduces tip ejection force and ensures a consistent seal.
- Compliance and Traceability - Some digital models offer data storage or integration with lab information systems for traceability.
- High Accuracy and Precision - Ensures reliable and reproducible results, essential for sensitive experiments.
- Digital Volume Control - Reduces human error with easy and precise volume setting via digital interface.
- Ergonomic Design- Minimizes hand strain and fatigue during prolonged use; ideal for repetitive pipetting tasks.
- LiteTouch System (LTS) - Eases tip attachment and ejection, reducing risk of RSI (Repetitive Strain Injury) and improving comfort.
- Versatile Volume Range - Available in multiple models to handle volumes from microliters to milliliters.
- Durable and Reliable - Built with high-quality materials for long life and resistance to chemicals and frequent use.
- Easy Maintenance and Calibration - Simplified calibration and cleaning ensure long-term performance and compliance.
- Data Integrity and Traceability -Some models store data, supporting audit trails and regulatory compliance.
- Enhanced Productivity - Quick setup, easy operation, and consistent performance speed up lab workflows.
- Digital Volume Adjustment - Precise and easy-to-read digital display for accurate volume setting.
- High Precision and Accuracy- Delivers consistent results, meeting ISO and GLP/GMP standards.
- Ergonomic Design- Lightweight, balanced with low plunger and tip ejection force to reduce fatigue.
- LiteTouch Tip Ejection System (LTS) - Reduces tip attachment/ejection force, improving comfort and consistency.
- Durable Construction - Built with high-quality, chemically resistant materials for long-term use.
- Wide Volume Range - Available in multiple models from 0.1 µL to 10 mL.
- Single-Channel and Multi-Channel Options - Suitable for various applications including high-throughput assays.
- Autoclavable Components- Some parts can be autoclaved for sterilization and contamination control.
- Easy Calibration and Maintenance - User-friendly calibration settings with accessible parts for cleaning.
- Optional Electronic Models - Some versions include programmable features, multiple modes (e.g., reverse pipetting), and memory storage.
Color Matching Cabinet-Light Box
Color Matching Cabinet-Light Box

Color Matching Cabinet-Light Box
Pantone book
Pantone Book

Pantone Book
- Formula Guide (Solid Coated & Uncoated) – For spot color printing.
- Color Bridge – Shows Pantone spot colors alongside CMYK equivalents.
- Pantone Fashion, Home + Interiors (FHI) – For textiles, soft goods, and home decor.
- Pantone CMYK and Pastels & Neons Guides – For process printing and special effect colors.
- Formula Guide (Solid Coated & Uncoated)
- Color Bridge Guide (Coated & Uncoated)
- CMYK Guide (Coated & Uncoated)
- Pastels & Neons Guide
- Metallics Guide
- FHI Color Guide (TPG – Paper)
- FHI Cotton Passport & Cotton Planner (TCX – Textile)
- FHI Polyester Swatch Book
- Pantone SkinTone Guide
- Pantone Plastic Standard Chips

Pantone Book
Fatigue tester for Elastic fabric
Fatigue Tester for Elastic Fabric
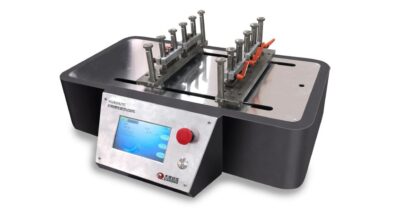
Fatigue tester for Elastic fabric
- Adjustable Stretch Range - Allows setting stretch levels (e.g., 0–100%) to simulate real-life fabric use.
- High-Cycle Capability - Supports up to millions of stretch-relax cycles for long-term fatigue analysis.
- Touch Screen Control - 7-inch color display for easy setup, monitoring, and data entry.
- Servo Motor Driven - Ensures precise and smooth linear motion during testing.
- Customizable Speed - Adjustable test speed (e.g., up to 40 cycles per minute) based on test requirements.
- Multi-Sample Testing - Some models allow testing multiple specimens simultaneously.
- Cycle Counter with Alarm - Built-in counter with programmable stop after preset cycles and auto-alert feature.
- Durable Construction - Robust metal frame suitable for continuous testing in lab environments.
- Standard Compliance - Designed to follow standards like GB/T 37635 for elastic fabric testing.
- Prepare the Sample
- Mount the Sample - Secure both ends of the fabric in the upper and lower clamps.
- Set Test Parameters
- Start the Test - Press start on the touch screen interface. - The machine will cyclically stretch and release the sample.
- Monitor Progress - Observe operation or let it run automatically.
- Remove and inspect - Take out the fabric and measure elongation, recovery, or visual defects.
- Record and Compare Results - Compare with initial measurements or standard performance criteria.
Fatigue tester for Elastic fabric