Color Matching Cabinet-Light Box
$0.00
Color Matching Cabinet-Light Box

Color Matching Cabinet-Light Box
Color Matching Cabinet -light Box
A Color Matching Cabinet-Light box (also known as a Light Box) is a standardized visual assessment tool used to evaluate the color consistency of materials like fabric, paint, plastic, paper, and leather under different lighting conditions.
Purpose of Color Matching Cabinet-Light Box :
To detect color variations and metamerism (color changes under different lights).
Ensures accurate color matching across production batches and materials.
How Color Matching Cabinet-Light Box Works:
The cabinet is equipped with multiple standardized light sources (e.g., D65, TL84, UV, CWF, A).
Samples are placed inside, and their colors are observed under each light to check for consistency.
Common Light Sources of Color Matching Cabinet-Light Box:
D65 – Daylight (standard)
TL84 – Store lighting (fluorescent)
CWF – Cool white fluorescent
UV – Ultraviolet (for fluorescent content)
A – Incandescent (home light)
U30/U35 – Warm white for showroom lighting
Applications of Color Matching Cabinet-Light Box:
Textile and garment inspection
Paint and coating industry
Plastics and packaging
Printing and graphic design
Benefits of Color Matching Cabinet-Light Box:
Accurate Color Assessment – Ensures color consistency across products by simulating different lighting conditions. Detects Metamerism – Identifies if colors appear differently under various lights, preventing mismatches. Improves Quality Control – Enhances visual inspection processes in textiles, printing, and packaging.
Standardized Viewing Conditions – Provides consistent light sources for reliable and repeatable evaluations.
Reduces Rework and Returns – Helps detect color defects early, saving time and production costs.
Supports Industry Standards – Meets international color evaluation standards like ASTM D1729, ISO 3664.
Easy to Use of Color Matching Cabinet -Light Box – Simple controls with clearly labeled light source buttons. Multiple Light Source Options – Enables testing under conditions matching retail, daylight, home, and UV lighting.
Features of Color Matching Cabinet-Light Box:
Multiple Standard Light Sources – Includes D65 (daylight), TL84 (store light), CWF, UV, A (home light), and optional U30/U35.
Digital Hour Meter – Tracks usage time for each light source to schedule timely replacements.
Uniform Light Distribution – Diffused lighting ensures consistent and shadow-free viewing.
Push Button Control Panel- Easy switching between different light sources.
No Warm-Up Time – Instant-on lighting allows immediate use.
Sturdy Metal Body – Durable and well-coated to reduce light reflection and distortion.
Viewing Area Markings – Guides for proper sample placement and comparison.
Optional Dimming Function – Adjustable light intensity (in advanced models) for fine-tuned observation.
Standardized Viewing Angles – Ensures observer views samples under consistent angles for accurate color judgment.
Description of Color Matching Cabinet-Light Box
Color Matching TILO 2 Feet 5/6 Option Light Box Cabinet (P60-5/6)
TILO 2 Feet 5/6 Option Light Box Cabinet (P60-5/6) is equipped with 5 light sources. The consistency of the light sources in all Tilo Color Assessment Cabinets gives excellent viewing conditions for reliable color critical decisions under consistent lighting. TILO 2 Feet 5 Option Light Box Cabinet (P60-5) can be applied to the industries that need to perform color difference testing as follows: as the premiere designer and manufacturer of color matching instrument products for the Graphic arts, Photographic, Textile, Dyeing, Packaging, Printing, Leather, Inks, Knitwear, Plastic, Automotive and Ceramics industries.
TILO 2 Feet 5 Option Light Box Cabinet (P60-5) offers an exact and dependable way to survey colors beneath different lighting conditions. This apparatus is planned to offer assistance experts in the material, paint, and plastic businesses to coordinate and assess colors with exactness. This high-quality item in Bangladesh at the best cost. The color Cabinet box permits for an ideal seeing environment for color inspection.
Features of TILO 2 Feet 5 Option Light Box Cabinet (P60-5)
Multiple Light Sources of Color Matching Cabinet-Light Box
The lTILO 2 Feet 5 Option Light Box Cabinet (P60-5) incorporates a assortment of light sources. These sources can reenact common sunshine, tungsten, and other counterfeit lighting conditions. By changing light sources, clients can compare colors in diverse situations, guaranteeing precise results.
Adjustable Light Intensity of Color Matching Cabinet-Light Box
The color coordinating light box highlights flexible light concentrated. You can control the brightness to coordinate distinctive real-world conditions. It guarantees a more point by point investigation of how colors alter beneath different lighting intensities.
Compact and Solid Design
This color appraisal cabinet comes in a compact plan, making it simple to put in any workspace. Its strong structure guarantees long-term utilize, indeed in requesting environments.
Precise Color Evaluation
The light box gives a controlled environment that makes a difference clients assess colors in a steady way. This highlight is particularly valuable in businesses where correct color coordinating is basic, such as in materials or paints.
Energy Efficient
The color cabinet is outlined to be energy-efficient. It employments Driven lights that devour less control whereas still advertising dependable and precise color assessment.
Simple Client Interface
The user-friendly interface of the color coordinating cabinet makes it simple for anybody to work. The controls are straightforward, and clients can alter settings effortlessly.
Portable Design
The color coordinating light box is lightweight, making it simple to move from one area to another. This movability is particularly valuable when you require to take the cabinet to diverse parts of the generation floor or to different client locations.
Ideal for Different Industries
Whether you work in materials, car, or fabricating, the color appraisal cabinet offers the exactness and unwavering quality required for color coordinating. It ensures consistency over distinctive materials and generation lines.
FEATURES
Certified by ASTM D1729, ISO3664, DIN, ANSI and BSI.
Automatic changeable into another light source by switching.
Usage time display, name of lamp, total number of switches for each.
Violated time sensor for tracking lamp service or replacement.
Large display & individual switch, easy to operate each light source.
No warm-up time, just plug and play.
The energy-saving device which generates lower heat & high efficiency.
The name of the light source can be changed.
SPECIFICATION OF TILO 2 FEET 5 OPTION LIGHT_BOX CABINET (P60-5)
Name Details
Model P60(5)
Brand TILO
Origin Hong Kong
Dimensions (WxDxH) (710 x 405 x 570)mm
Standards ASTM D1729, ISO3664, DIN, ANSI and BSI
Light source Five light source.
Power Source Electric.
Voltage 220 ~ 240V
Body Material Fiber-reinforce
Warranty One year free service
LIGHT SOURCE OF TILO 2 FEET 5 OPTION LIGHT_BOX CABINET (P60-5)
Light Source Color viewing applications / Uses of Light Color Temp. (K) Power (W) Brand Info Quantity
D65 International standard Artificial Daylight / Natural Daylight 6500 18 PHILIPS; TL-D/18-965 2 Pieces
TL84 Applied to stores in Europe, Japan and China 4000 18 PHILIPS; TL-D/18-840 2 Pieces
F “Sun-setting Light Yellow” incandescent light source 2700 40 PHILIPS 4 Pieces
UV ultraviolet light to detect and evaluate optical brighteners or fluorescent pigments Wave length: 365nm 20 PHILIPS 18W BLB 1 Pieces
CWF (Cool White Fluorescent) American Standard 4150 18 PHILIPS; TL-D/18-640 2 Pieces
Related products
Controller For IR Dyeing Machine
Controller For IR Dyeing Machine
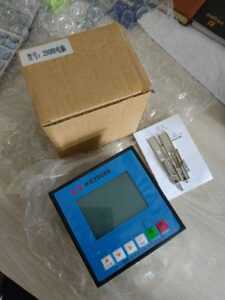
IR Dyeing machine controller
- Temperature Control:- Precisely regulates the infrared heaters to maintain uniform temperature across the dye bath. - Supports customizable heating curves (ramp-up, hold, and cool-down phases).
- Programmable Logic Control (PLC): - Allows operators to set and automate dyeing programs for different fabrics and dye types. - Supports multiple recipes or programs for different batches.
- Real-Time Monitoring and Feedback: - Monitors parameters like temperature, fabric rotation, bath circulation, and timing. - Provides real-time data and alarms for deviations.
- Touchscreen Interface / HMI (Human Machine Interface): - User-friendly interface for configuring and monitoring processes. - Multi-language support and graphical display of process curves.
- Data Logging and Traceability: - Records process data for quality control and traceability.
- Energy Efficiency Optimization: - Manages IR heater output to reduce energy usage. - Often includes features for auto shut-off or idle mode.
- Safety Features: - Includes emergency stop, over-temperature protection, and fault detection systems. 8. Connectivity: - Modern controllers may support Ethernet, Modbus, or other industrial communication protocols for integration into factory automation systems.
- Improved Dyeing Accuracy and Consistency
- Enhanced Energy Efficiency- Infrared heating is more energy-efficient than traditional heating methods.- The controller optimizes energy use by adjusting the IR output based on process needs, reducing overall energy consumption.
- Time Savings- Faster heating and cooling cycles due to infrared technology.- Automated processes reduce manual intervention and cycle times. 4. Better Process Control- Programmable dyeing cycles and precise control over each stage (heating, dyeing, rinsing, cooling).- Real-time monitoring and adjustments improve reliability.
- Reduced Water and Chemical Usage- More efficient dye penetration and fixation mean less water and fewer chemicals are needed for reprocessing or corrections.6. Lower Operational Costs
- Enhanced Safety Built-in alarms, emergency shut-off and automatic fault detection enhance operational safety.8. Data Logging and Traceability- Ability to record and review dyeing process data helps in quality control and troubleshooting.- Facilitates compliance with industry standards and audits.
- User-Friendly Operation- Modern touchscreen interfaces make it easier for operators to manage and monitor processes.- Multilingual support and visual feedback enhance usability.
ICI Pilling & Snagging Test Machine
Laboratory Padder
Laboratory Padder
A Laboratory Padder is a compact, laboratory-scale machine used to apply liquids like dyes, chemicals, and finishes to fabric samples. It simulates the padding process in textile manufacturing, where fabric is passed through a liquid solution, then squeezed between rollers to ensure uniform application and absorption. Key Features of a Laboratory Padder:- Adjustable Rollers - The fabric is passed through two or more rollers to apply even pressure and squeeze out excess solution, ensuring uniform chemical or dye application.
- Variable Pressure Control - Allows adjustment of roller pressure for different fabric types and chemical formulations, ensuring optimal penetration without damage.
- Solution Bath - Holds the liquid (e.g., dye, finish, or other chemical treatments) in a bath through which the fabric is dipped before passing through the rollers.
- Fabric Speed Control - Adjustable conveyor speed allows for control over the time the fabric spends in contact with the liquid solution, affecting the degree of treatment.
- Digital Control Panel - Provides easy adjustment of pressure, speed, and solution volume to ensure precise and reproducible results.
- Compact Design - Smaller, lab-scale version of industrial padders, ideal for research, development, and small-scale testing.
- Safety Features - Safety guards, emergency stops, and proper handling mechanisms to prevent accidents during operation.
- Precise Application of Chemicals - Provides uniform and controlled application of dyes, finishes, and other chemicals, ensuring consistent results.
- Small-Scale Testing - Ideal for small sample testing, allowing for fabric treatment without needing full-scale production equipment.
- Versatile Use - Suitable for dyeing, finishing, and applying various chemical treatments, making it a flexible tool for R&D labs.
- Cost-Effective - Reduces the need for large-scale machinery and the associated costs, while providing reliable results for small batches.
- Controlled Fabric Treatment - Offers adjustable pressure, speed, and solution concentration, enabling fine-tuned processing for different fabric types and applications.
- Accelerates Development - Speeds up the testing and development of new products or finishes, improving time-to-market for textile manufacturers.
- Energy Efficient - Consumes less energy compared to larger, industrial-scale machines, making it suitable for lab use.
- Compact and Space-Saving - Designed for laboratory environments with limited space, without compromising on functionality.
- Reproducible Results - Ensures consistent application of treatments across multiple samples, aiding in accurate testing and comparison.
- Adjustable Roller Pressure - Allows precise control over the pressure applied to the fabric, ensuring uniform chemical or dye application.
- Variable Speed Control - Adjustable conveyor speed for controlling the time the fabric spends in the solution bath, influencing the absorption rate.
- Solution Bath - Holds dye, chemicals, or finishes, and the fabric passes through this bath before moving to the rollers.
- Digital Control Panel - Easy-to-use interface for setting and adjusting parameters like speed, pressure, and solution concentration.
- Compact and Lab-Friendly Design - Designed for smaller, space-efficient use in textile labs, allowing for small sample testing.
- Roller Gap Adjustment - Allows for fine-tuning of the gap between rollers to regulate the amount of solution squeezed out of the fabric.
- Stainless Steel Construction - Durable and resistant to corrosion from the chemicals used in textile treatments.
- Safety Mechanisms - Includes safety guards, emergency stops, and user protection features during operation.
- Even and Controlled Application - Ensures even distribution of treatments (dye, finish, etc.) on fabric with minimal waste.
- Versatility in Application - Can be used for a wide range of textiles and treatments, including dyeing, softening, flame-retardant treatments, etc.
- Prepare the Fabric Sample - Cut the fabric sample to the required size for the experiment. Ensure it’s clean and free of any debris.
- Prepare the Solution - Mix the dye, chemical, or finish solution according to the desired concentration and the fabric's needs. Ensure that the solution is homogeneous.
- Set the Parameters - Pressure: Adjust the roller pressure based on the fabric type. Different fabrics require different pressure levels to ensure uniform application. - Speed: Set the fabric conveyor speed depending on the desired treatment time (longer exposure for deeper treatment).
- Load the Fabric into the Machine - Place the fabric carefully into the machine. The fabric should go through the solution bath and then pass between the rollers.
- Start the Machine - Turn on the machine and allow the fabric to pass through the rollers. The solution will be evenly applied to the fabric as it moves through the bath and is squeezed by the rollers.
- Monitor the Process - Keep an eye on the fabric to ensure it is being treated uniformly and there are no blockages or fabric jams.
- Unload the Fabric - Once the fabric has been treated, carefully remove it from the machine. Inspect for even application of the solution and any excess liquid.
- Dry or Process Further - Depending on the treatment, proceed with further steps such as drying, heat setting, or curing, as required by the experiment or process.

Mini Lab Dyeing Padder
Fabric Stiffness Tester
Fabric Stiffness Tester
Fabric Stiffness Tester is a lab instrument used to measure the stiffness or flexural rigidity of fabric materials. It evaluates how resistant a fabric is to bending, which influences its drape, comfort, and handling characteristics. Purpose of Fabric Stiffness Tester: To determine the stiffness of textiles by measuring the bending length and calculating flexural rigidity, often using methods like the Cantilever Test (as per ASTM D1388 or ISO 9073-7). Working Principle of Fabric Stiffness Tester: A fabric strip is slid over a horizontal platform until its free end bends under its own weight to a specific angle (usually 41.5°). The length at which this occurs is used to calculate bending length and stiffness. Main Components of Fabric Stiffness Tester: - Test Platform: Flat surface for sample movement. - Graduated Scale: Measures the overhanging length of fabric. - Angle Indicator: Guides the measurement based on standard deflection angle. - Fabric Clamp or Guide: Helps place and move the sample smoothly. Applications of Fabric Stiffness Tester: - Apparel fabrics (e.g., for comfort and drape analysis) - Technical textiles (e.g., automotive, medical fabrics) - Paper, nonwovens, and films Benefits of Fabric Stiffness Tester:- Accurate Measurement of Flexibility - Provides reliable data on fabric stiffness, essential for quality control and product development.
- Improves Product Comfort - Helps assess how soft or rigid a fabric will feel in clothing or furnishings.
- Supports Material Selection - Aids designers and engineers in choosing the right fabric for specific applications based on stiffness.
- Quality Assurance - Detects fabric inconsistencies or defects that affect handling or drape.
- Standards Compliance - Enables testing as per international standards like ASTM D1388 and ISO 9073-7 for global product approval.
- Quick and Simple Operation - Delivers fast results with minimal operator training or preparation.
- Applicable to Multiple Materials - Suitable for woven, nonwoven, knitted fabrics, paper, and films.
- Enhances R&D Accuracy - Supports consistent material testing during product innovation and textile finishing.
- Graduated Measurement Scale - Precise scale to measure overhang length for accurate stiffness calculation.
- Flat Test Platform - Smooth, level surface ensures consistent and reliable fabric movement.
- Standard Deflection Angle Guide - Built-in 41.5° angle reference for consistent stiffness testing (per ASTM/ISO).
- Manual or Motorized Models - Available in both types for simple or automated operation depending on lab needs.
- Compact Design - Space-saving unit ideal for textile labs and quality control rooms.
- Sample Holder or Clamp - Ensures correct alignment and smooth feeding of fabric strips during testing.
- Durable Construction - Made of corrosion-resistant materials like stainless steel or aluminum for long-term use.
- Compliance with Standards - Supports methods like ASTM D1388, ISO 9073-7 for stiffness testing of fabrics.
- Lightweight and Portable - Easy to move and use in various lab settings.
- Low Maintenance - Simple mechanical parts require minimal servicing.
- Prepare the Sample - Cut the fabric into a rectangular strip (e.g., 25 mm × 200 mm), as per standard.
- Place the Sample - Lay the fabric strip flat on the test platform with one end aligned at the zero mark.
- Slide the Fabric - Gently push the fabric forward so it slowly overhangs the platform.
- Watch for Deflection - Stop sliding when the free end of the fabric bends down to the reference angle (typically 41.5°).
- Read the Bending Length - Measure the overhang distance from the scale. This is the bending length (C).
- Calculate Flexural Rigidity
- Repeat for Accuracy - Test both warp and weft directions and average the results for better accuracy.

Digital hot plate-magnetic stirrer
Digital hot plate-magnetic stirrer
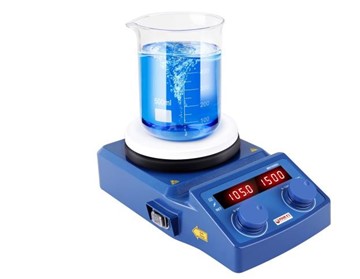
Digital hot plate-magnetic stirrer
- Magnetic Stirrer:
- Digital Display and Controls:
- Temperature Sensors: - Built-in or external probes (like a PT100 or thermocouple) for accurate temperature control.
- Precision and Control- Digital Interface: Allows accurate setting and monitoring of temperature and stirring speed.- Consistent Results: Ensures reproducibility in experiments and solution preparations.
- Efficient Mixing and Heating- Uniform Mixing: Magnetic stirring eliminates hotspots and ensures even distribution of solutes.- Simultaneous Operation: Ability to heat and stir at the same time improves efficiency.
- Safety Features- Overheat Protection: Prevents accidents by automatically shutting off at unsafe temperatures.- Sealed Surface: Reduces risk of contamination and easy to clean.
- Versatility
- Compact and User-Friendly- Takes up minimal bench space.- Simple to operate with user-friendly controls and displays.
- Durability- High-quality materials like ceramic or stainless steel tops resist corrosion and wear.
- Time-Saving Speeds up preparation of solutions and reactions compared to manual stirring and separate heating. Would you like these benefits presented in a slide format or for a product brochure?
Laboratory tenter
Laboratory Tenter
A Laboratory Tenter (or Lab Stenter) is a small-scale version of an industrial tenter machine used in textile finishing. It is designed for heat-setting, drying, and finishing of fabric samples under controlled conditions in textile testing labs or R&D departments. Key Features:- Heat-Setting and Drying - Simulates the process of setting fabric dimensions and applying finishes using controlled temperature and tension.
- Fabric Width Control - Uses clips or pins on chains or rails to hold fabric edges and stretch them to desired width, just like in full-size tenters.
- Adjustable Temperature and Speed - Digital controls allow precise setting of drying/curing temperature and conveyor speed to match production conditions.
- Compact Design - Bench-top or floor-standing units suitable for labs with limited space.
- Transparent Viewing Chamber - Allows visual inspection of fabric behavior during processing.
- Versatile Application Range - Can process woven, knitted, and nonwoven fabrics of various compositions (cotton, polyester, blends, etc.).
- Accurate Simulation of Production - Replicates industrial finishing processes for reliable lab-scale testing and development.
- Improves Fabric Quality- Allows precise control of heat and tension, optimizing fabric properties like shrinkage, dimensional stability, and hand feel.
- Cost-Effective - Enables process trials and fabric development without using full-scale production equipment.
- Speeds Up R&D - Facilitates quick testing and adjustment of settings for new fabric styles or finishes.
- Versatile Applications - Suitable for drying, heat-setting, finishing, and evaluating different types of fabrics and treatments.
- Space-Efficient - Compact design fits easily into textile labs or sample rooms.
- Energy Efficient- Uses less power than industrial machines, ideal for small-scale and repeated testing.
- Process Control and Reproducibility- Digital controls ensure consistent and repeatable results, aiding in quality assurance and product development.
- Enhances Safety - Built with lab use in mind, featuring insulation and safety systems to protect users.
- Precise Temperature Control - Digital temperature setting (typically up to 220–250°C) for accurate heat-setting and drying.
- Adjustable Fabric Width - Equipped with clip or pin chains to hold and stretch fabric across the width, simulating real stentering.
- Variable Conveyor or Chain Speed- Adjustable speed to control fabric dwell time during processing.
- Compact and Lab-Friendly Design - Designed for bench-top or small floor space use in textile labs.
- Transparent Chamber Window - Allows monitoring of fabric behavior during treatment.
- Digital Display and Control Panel - Easy operation for setting temperature, speed, and time.
- Uniform Heat Distribution- Ensures even treatment across the fabric width for accurate testing.
- Stainless Steel Construction - Durable, corrosion-resistant body for long-term use at high temperatures.
- Safety Features - Includes over-temperature protection, insulated body, and emergency stop functions.
- Sample Versatility - Suitable for various fabric types (woven, knit, synthetic, blends) and lab finishing tasks.

laboratory mini tenter
Fastness Rotary Friction Tester
Fastness Rotary Friction Tester
A Fastness Rotary Friction Tester, also known as a Rotary Crock meter, is a specialized instrument used to evaluate the color fastness of textiles and materials when subjected to rotational rubbing. This test simulates the wear and friction that fabrics experience during use, helping manufacturers assess the durability of dyes and finishes. Purpose of Fastness Rotary Friction Tester The primary function of the Fastness Rotary Friction Tester is to determine how well a fabric's color withstands rubbing, both in dry and wet conditions. This is crucial for ensuring the longevity and appearance of textiles in real-world applications, such as clothing, upholstery, and footwear. Working Principle of Fastness Rotary Friction Tester The tester operates by applying a specified pressure to a fabric sample using a standardized rubbing finger covered with a test cloth. The rubbing finger performs a set number of rotational movements (typically 1.125 turns clockwise followed by 1.125 turns counterclockwise) over the fabric surface. After the test, the degree of color transfer to the test cloth and any changes in the fabric's appearance are evaluated against standardized gray scales. Common Testing Standards - AATCC 116: Colorfastness to Crocking: Rotary Vertical Crock meter Method. ISO 105 X16: Textiles—Tests for color fastness—Part X16: Color fastness to rubbing—small areas. - SATRA TM8: Color fastness to rubbing. Key Specifications of Fastness Rotary Friction Tester - Rubbing Head Diameter: Typically 16 mm. - Applied Pressure: Approximately 1134 grams (11.1 N). - Rotation: 1.125 turns clockwise followed by 1.125 turns counterclockwise. - Sample Size: Commonly 60 mm × 60 mm. - Test Cloth: Standardized white cotton cloth, either dry or wetted depending on the test condition. Benefits of Fastness Rotary Friction Tester - Realistic Simulation: Mimics the actual wear and friction fabrics undergo during use. - Versatility: Applicable to a wide range of materials, including textiles, leather, and printed fabrics. - Quality Assurance: Ensures products meet industry standards for color durability. - Standard Compliance: Aligns with international testing standards, facilitating global trade and quality benchmarks. Applications Fastness Rotary Friction Tester - Textile Industry: Assessing the color durability of garments, upholstery, and other fabric products. - Footwear Manufacturing: Testing the colorfastness of shoe uppers and linings. - Automotive Interiors: Evaluating the wear resistance of seat covers and other interior fabrics. Quality Control Laboratories: Routine testing to ensure product consistency and compliance with standards. Benefits of Fastness Rotary Friction Tester:- Accurate Colorfastness Evaluation- Provides precise assessment of how well fabric resists color loss and staining from rubbing.
- Simulates Real-World Wear - Recreates rotational friction found in actual use (e.g., seat covers, apparel wear points).
- Supports Wet & Dry Testing - Can test under both dry and wet conditions for comprehensive results.
- Standardized Testing - Complies with global standards (AATCC 116, ISO 105 X16), ensuring reliable and comparable results.
- Time-Saving & Efficient - Quick to set up and run, allowing for high-throughput testing in labs.
- Versatile Use- Suitable for textiles, leather, coated fabrics, and printed surfaces.
- Improves Quality Control - Identifies potential durability issues early in the production process.
- Enhances Product Performance - Helps in developing fabrics with better resistance to rubbing and abrasion.
- Rotary Rubbing Mechanism - Simulates 1.125 clockwise and 1.125 counterclockwise turns for realistic friction.
- Standardized Rubbing Head - Fixed diameter (typically 16 mm) with specified pressure (≈1134 g) for consistent results.
- Dry and Wet Testing Capability - Can perform tests using dry or wet rubbing cloths.
- Sample Holder- Secure and easy-to-use fixture for holding fabric samples in place.
- Test Cloth Mounting Arm- Quick attachment for standardized white rubbing cloths.
- Simple Operation - Manual or motorized operation depending on model; easy to handle for lab technicians.
- Compliance with Standards - Follows AATCC 116, ISO 105 X16, and SATRA TM8 protocols.
- Prepare the Sample - Cut a fabric piece (typically 60 × 60 mm) and condition it per standard requirements.
- Mount the Fabric - Secure the fabric sample on the sample holder or base plate of the tester.
- Attach Rubbing Cloth - Place a standard white test cloth (dry or wetted as required) over the rubbing head.
- Apply Pressure - Lower the rubbing head onto the fabric. Standard weight is about 1134 g.
- Start the Test - Operate the tester: the head performs 1.125 turns clockwise, then 1.125 turns counterclockwise.- Number of cycles (typically 10 or 20) is set based on the test standard.
- Remove and Inspect - After testing, remove the rubbing cloth and assess any color transfer using a gray scale.
- Evaluate Fabric Surface - Check the fabric for visible changes, fading, or wear.
- Record Results - Grade both staining and fabric change per standard gray scale ratings.

Fatigue tester for Elastic fabric
Fatigue Tester for Elastic Fabric
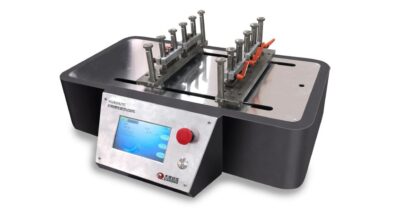
Fatigue tester for Elastic fabric
- Adjustable Stretch Range - Allows setting stretch levels (e.g., 0–100%) to simulate real-life fabric use.
- High-Cycle Capability - Supports up to millions of stretch-relax cycles for long-term fatigue analysis.
- Touch Screen Control - 7-inch color display for easy setup, monitoring, and data entry.
- Servo Motor Driven - Ensures precise and smooth linear motion during testing.
- Customizable Speed - Adjustable test speed (e.g., up to 40 cycles per minute) based on test requirements.
- Multi-Sample Testing - Some models allow testing multiple specimens simultaneously.
- Cycle Counter with Alarm - Built-in counter with programmable stop after preset cycles and auto-alert feature.
- Durable Construction - Robust metal frame suitable for continuous testing in lab environments.
- Standard Compliance - Designed to follow standards like GB/T 37635 for elastic fabric testing.
- Prepare the Sample
- Mount the Sample - Secure both ends of the fabric in the upper and lower clamps.
- Set Test Parameters
- Start the Test - Press start on the touch screen interface. - The machine will cyclically stretch and release the sample.
- Monitor Progress - Observe operation or let it run automatically.
- Remove and inspect - Take out the fabric and measure elongation, recovery, or visual defects.
- Record and Compare Results - Compare with initial measurements or standard performance criteria.
Fatigue tester for Elastic fabric