GSM Cutter with Balance
$0.00
GSM Cutter with Balance

GSM Cutter with Balance
A GSM Cutter with Balance is a lab toolset used to determine the GSM (Grams per Square Meter) of fabrics, which indicates the fabric’s weight and density. The kit includes a GSM round cutter and a precision weighing balance.
Purpose GSM Cutter with Balance:
To accurately measure the weight per unit area of textile, paper, or nonwoven samples for quality control and product classification.
How It Works:
GSM Cutter: – A circular blade cuts a fixed area (usually 100 cm²) from the fabric.
Weighing Balance: – The cut piece is weighed, and the result is multiplied by 100 to get GSM.
GSM = Weight (in grams) × 100
Applications of GSM Cutter with Balance:
Textile and garment industry
Nonwovens and paper manufacturing
QC labs and R&D
Benefits of GSM Cutter with Balance:
Accurate GSM Measurement – Ensures precise fabric weight analysis for quality control.
Quick and Simple Operation – Allows fast sampling and GSM calculation in minutes.
No Need for Area Calculation – Cutter gives a fixed area (usually 100 cm²), simplifying the formula.
Improves Product Consistency – Helps maintain uniform fabric weight across batches.
Portable and User-Friendly – Compact design makes it ideal for labs and production floors.
Cost-Effective Tool – Offers high accuracy without the need for expensive equipment.
Versatile Use – Suitable for fabrics, paper, leather, films, and more.
Features of GSM Cutter with Balance:
Rotary Blade Cutter – Stainless steel blades for clean and accurate circular cuts.
Fixed Sample Area – Typically 100 cm², eliminating the need for area measurement.
Precision Digital Balance – Measures in grams with high resolution (0.01 g or better).
Rubber Cutting Pad – Protects blade and provides a smooth surface for cutting.
Safety Lock – Prevents accidental blade exposure.
Compact & Durable Design- Long-lasting, lab-friendly construction.
How to Use GSM Cutter with Balance:
Prepare the Fabric Sample- Place the fabric on the rubber cutting pad.
Cut the Sample – Hold the GSM cutter firmly and rotate it to cut a 100 cm² circular sample.
Turn on the Balance – Power up the digital weighing scale and tare it to zero.
Weigh the Sample – Place the cut fabric piece on the balance and note the weight in grams.
Calculate GSM – Multiply the weight by 100 to get GSM. – GSM = Sample weight (g) × 100
Record the Result- Log the GSM value for quality control or analysis.
Clean and Store – Wipe the cutter and balance, and store them safely after use.
GSM Calculation Formula:
GSM (g/m²) = (Weight of Sample in grams) × 100
When using a GSM cutter (100 cm²):
The cutter gives a fixed area of 100 cm², which is 1/100th of a square meter.
So, multiplying the sample’s weight by 100 gives the GSM directly.
Example:
If the sample weighs 1.75 g, then:
GSM = 1.75 × 100 = 175 g/m²
Balance Calibration Guide (Manual Calibration):
Warm-Up – Turn on the balance and let it warm up for 10–15 minutes if required.
Level the Balance – Use the built-in bubble level and adjust leveling feet until the bubble is centered.
Tare the Balance – Press the “TARE” or “ZERO” button to reset the display to 0.000 g.
Enter Calibration Mode – Press the “CAL” or “MODE” button (depends on the model).
– Some balances may require holding the button for a few seconds.
Use Standard Weight – When prompted, place a certified calibration weight (e.g., 100g, 200g) on the pan. – Wait for the display to stabilize.
Confirm Calibration – The balance will beep or show “PASS” once successful. – Remove the weight when done. Recheck Zero – Ensure the display returns to 0.000 g after removing the weight.
Tips:
Use certified weights for accuracy (Class F1 or E2).
Calibrate in a draft-free, vibration-free environment.
Calibrate daily or before critical measurements.
GSM Cutter & Balance
GSM Cutter
Brand: Schroder
Origin: Germany
Capacity: 100 Sq.cm
Supplied with 1 pcs cutting Pad and 04 pcs cutting blade.
Digital Electronics balance
Precision GSM Weight Balance 0.01g to 200g
Model: GSM200
Brand: Schroder
Origin: Germany
Related products
Fastness Rotary Friction Tester
Fastness Rotary Friction Tester
A Fastness Rotary Friction Tester, also known as a Rotary Crock meter, is a specialized instrument used to evaluate the color fastness of textiles and materials when subjected to rotational rubbing. This test simulates the wear and friction that fabrics experience during use, helping manufacturers assess the durability of dyes and finishes. Purpose of Fastness Rotary Friction Tester The primary function of the Fastness Rotary Friction Tester is to determine how well a fabric's color withstands rubbing, both in dry and wet conditions. This is crucial for ensuring the longevity and appearance of textiles in real-world applications, such as clothing, upholstery, and footwear. Working Principle of Fastness Rotary Friction Tester The tester operates by applying a specified pressure to a fabric sample using a standardized rubbing finger covered with a test cloth. The rubbing finger performs a set number of rotational movements (typically 1.125 turns clockwise followed by 1.125 turns counterclockwise) over the fabric surface. After the test, the degree of color transfer to the test cloth and any changes in the fabric's appearance are evaluated against standardized gray scales. Common Testing Standards - AATCC 116: Colorfastness to Crocking: Rotary Vertical Crock meter Method. ISO 105 X16: Textiles—Tests for color fastness—Part X16: Color fastness to rubbing—small areas. - SATRA TM8: Color fastness to rubbing. Key Specifications of Fastness Rotary Friction Tester - Rubbing Head Diameter: Typically 16 mm. - Applied Pressure: Approximately 1134 grams (11.1 N). - Rotation: 1.125 turns clockwise followed by 1.125 turns counterclockwise. - Sample Size: Commonly 60 mm × 60 mm. - Test Cloth: Standardized white cotton cloth, either dry or wetted depending on the test condition. Benefits of Fastness Rotary Friction Tester - Realistic Simulation: Mimics the actual wear and friction fabrics undergo during use. - Versatility: Applicable to a wide range of materials, including textiles, leather, and printed fabrics. - Quality Assurance: Ensures products meet industry standards for color durability. - Standard Compliance: Aligns with international testing standards, facilitating global trade and quality benchmarks. Applications Fastness Rotary Friction Tester - Textile Industry: Assessing the color durability of garments, upholstery, and other fabric products. - Footwear Manufacturing: Testing the colorfastness of shoe uppers and linings. - Automotive Interiors: Evaluating the wear resistance of seat covers and other interior fabrics. Quality Control Laboratories: Routine testing to ensure product consistency and compliance with standards. Benefits of Fastness Rotary Friction Tester:- Accurate Colorfastness Evaluation- Provides precise assessment of how well fabric resists color loss and staining from rubbing.
- Simulates Real-World Wear - Recreates rotational friction found in actual use (e.g., seat covers, apparel wear points).
- Supports Wet & Dry Testing - Can test under both dry and wet conditions for comprehensive results.
- Standardized Testing - Complies with global standards (AATCC 116, ISO 105 X16), ensuring reliable and comparable results.
- Time-Saving & Efficient - Quick to set up and run, allowing for high-throughput testing in labs.
- Versatile Use- Suitable for textiles, leather, coated fabrics, and printed surfaces.
- Improves Quality Control - Identifies potential durability issues early in the production process.
- Enhances Product Performance - Helps in developing fabrics with better resistance to rubbing and abrasion.
- Rotary Rubbing Mechanism - Simulates 1.125 clockwise and 1.125 counterclockwise turns for realistic friction.
- Standardized Rubbing Head - Fixed diameter (typically 16 mm) with specified pressure (≈1134 g) for consistent results.
- Dry and Wet Testing Capability - Can perform tests using dry or wet rubbing cloths.
- Sample Holder- Secure and easy-to-use fixture for holding fabric samples in place.
- Test Cloth Mounting Arm- Quick attachment for standardized white rubbing cloths.
- Simple Operation - Manual or motorized operation depending on model; easy to handle for lab technicians.
- Compliance with Standards - Follows AATCC 116, ISO 105 X16, and SATRA TM8 protocols.
- Prepare the Sample - Cut a fabric piece (typically 60 × 60 mm) and condition it per standard requirements.
- Mount the Fabric - Secure the fabric sample on the sample holder or base plate of the tester.
- Attach Rubbing Cloth - Place a standard white test cloth (dry or wetted as required) over the rubbing head.
- Apply Pressure - Lower the rubbing head onto the fabric. Standard weight is about 1134 g.
- Start the Test - Operate the tester: the head performs 1.125 turns clockwise, then 1.125 turns counterclockwise.- Number of cycles (typically 10 or 20) is set based on the test standard.
- Remove and Inspect - After testing, remove the rubbing cloth and assess any color transfer using a gray scale.
- Evaluate Fabric Surface - Check the fabric for visible changes, fading, or wear.
- Record Results - Grade both staining and fabric change per standard gray scale ratings.

Perspiration Tester
Perspiration Tester

Perspiration Tester
- Fabric samples are treated with synthetic perspiration solution (acidic or alkaline).
- They are sandwiched with adjacent fabric and placed between glass or acrylic plates.
- The assembly is loaded into the tester and pressed under specific pressure.
- it’s then incubated at 37°C (body temperature) for a fixed time (typically 4 or 16 hours).
- Afterward, color change and staining are evaluated using a gray scale.
- Accurate Sweat Simulation - Mimics real-life effects of acidic and alkaline perspiration on fabrics.
- Improves Product Quality - Ensures textiles retain color and don’t bleed or stain when worn.
- Supports Standard Compliance - Follows ISO and AATCC test standards for global market approval.
- Protects Brand Reputation- Reduces customer complaints due to dye transfer or fading.
- Simple and Repeatable- Provides consistent pressure and conditions for reliable results.
- Multi-Sample Testing- Tests multiple specimens at once, saving time in labs.
- Durable and Low Maintenance- Robust frame with minimal moving parts makes it long-lasting and easy to care for.
- Stainless Steel Frame - Corrosion-resistant body for durability and long-term use.
- Multi-Sample Capacity - Can hold up to 20 or more specimens for batch testing.
- Standardized Loading Weight- Applies uniform pressure (usually 12.5 kPa) across all samples.
- Removable Plates - Glass or acrylic plates ensure even contact and easy cleaning.
- Compact Design- Space-saving, bench-top model ideal for lab environments.
- Complies with Test Standards - Meets ISO 105 E04, AATCC 15, and related perspiration fastness standards.
- Ease of Operation - Simple loading, unloading, and incubation process.
- High-Temperature Resistance - Can be used inside incubators at 37°C or ovens as required.
- Prepare the Test Solution - Mix artificial acidic or alkaline perspiration as per standard (ISO or AATCC).
- Cut the Fabric Samples - Cut both the test fabric and adjacent white fabric (usually cotton) to standard size.
- Soak the Samples - Immerse the fabric sandwich (test + adjacent) in the test solution for 30 minutes.
- Remove Excess Liquid - Gently squeeze or blot to remove extra moisture—do not dry.
- Load in the Tester- Place each sandwich between glass or acrylic separator plates in the tester.
- Apply Pressure - Tighten the top plate or place the standard weight on top to apply uniform pressure.
- Incubate - Keep the loaded tester in an oven or incubator at 37°C for 4–16 hours (depending on the method).
- Accurate Sweat Simulation - Mimics real-life effects of acidic and alkaline perspiration on fabrics.
- Improves Product Quality - Ensures textiles retain color and don’t bleed or stain when worn.
- Supports Standard Compliance - Follows ISO and AATCC test standards for global market approval.
- Protects Brand Reputation- Reduces customer complaints due to dye transfer or fading.
- Simple and Repeatable- Provides consistent pressure and conditions for reliable results.
- Multi-Sample Testing- Tests multiple specimens at once, saving time in labs.
- Durable and Low Maintenance- Robust frame with minimal moving parts makes it long-lasting and easy to care for.
- Dry and Evaluate - Remove, air dry the samples, then assess color change and staining using a gray scale.
- Fabric samples are treated with synthetic perspiration solution (acidic or alkaline).
- They are sandwiched with adjacent fabric and placed between glass or acrylic plates.
- The assembly is loaded into the tester and pressed under specific pressure.
- it’s then incubated at 37°C (body temperature) for a fixed time (typically 4 or 16 hours).
- Afterward, color change and staining are evaluated using a gray scale.
Perspiration Tester
Digital Elmendorf tearing tester
Digital Elmendorf Tearing Tester
Digital Elmendorf Tearing Tester is a precision instrument used to measure the tear strength of materials like woven fabrics, paper, plastic films, and nonwovens. It determines how much force is required to continue tearing a pre-slit sample. Key Functions of Digital Elmendorf Tearing Tester: - Measures propagation tear resistance, not initial tear. - Uses a pendulum to apply force; the energy lost during tearing is calculated to determine tear strength. - Equipped with a digital display for direct reading of results in grams or millinewtons. Core Components: - Pendulum Arm: Applies tearing force. - Clamps: Secure the sample before and after the tear. - Cutting Blade: Creates a precise slit at the start of the test. - Digital Display Unit: Shows the tearing force result clearly and instantly. - Counterweights: Optional weights for increasing test range (for stronger materials). Applications of Digital Elmendorf Tearing Tester: - Testing tear resistance of: - Textile fabrics (especially woven) - Paper and cardboard - Plastic films - Nonwovens - Packaging materials Benefits of Digital Elmendorf Tearing Tester:- Accurate Tear Strength Measurement - Provides precise data on tear resistance, critical for quality control and product performance.
- Digital Readout - Easy-to-read display gives instant, reliable results without manual calculations.
- High Reproducibility - Ensures consistent test outcomes due to controlled tearing angle and speed.
- Fast Testing Process - Simple loading and quick test cycle increase lab efficiency.
- Suitable for Various Materials - Tests a wide range of flexible materials like textiles, paper, plastic, and packaging.
- Customizable Range - Use of optional weights extends the test range for low to high tear strength materials.
- Low Sample Waste - Requires small fabric or material samples, reducing waste during testing.
- Standards Compliance - Meets international testing standards (e.g., ASTM D1424, ISO 13937) for credibility and uniformity.
- Precision Sample Clamp - Securely holds samples in place to ensure accurate tear initiation.
- Pre-Cutting Blade - Integrated knife creates a precise initial slit in the sample before tearing.
- User-Friendly Interface - Simple buttons and screen navigation for ease of operation.
- Standard Test Compliance - Compatible with ASTM D1424, ISO 1974, ISO 13937, and other tear strength standards.
- Sturdy Construction - Made with durable materials for long-lasting performance and stable operation.
- Compact Design - Space-efficient footprint ideal for laboratory environments.
- Data Output Options- Some models offer USB or printer connectivity for result documentation.
- Prepare the Sample - Cut the material (fabric, paper, film, etc.) to standard size (typically 100 × 63 mm for textiles) and slit it with the pre-cutter as required.
- Select Pendulum Weight - Choose the appropriate pendulum or add counterweights based on expected tear strength.
- Calibrate the Machine - Set the pendulum to its starting position and zero the display.
- Clamp the Sample - Fix one half of the sample in the stationary clamp and the other in the moving clamp.
- Cut the Initial Slit - Use the integrated blade to make a precise cut at the marked slit area (usually 20 mm).
- Release the Pendulum - Trigger the pendulum to swing and tear the sample through the pre-slit.
- Read the Result - The digital display will show the tearing force automatically (in g, mN, or cN).
- Record or Export Data - Save or print the result if your model supports USB or printer connection.
- Reset for Next Test - Reposition the pendulum and prepare a new sample for the next cycle.

High speed hard winding machine
High Speed Hard Winding Machine

High Speed Hard Winding Machine
- Increased Productivity - High-speed operation reduces winding time significantly.
- Consistent Package Quality - Ensures uniform and firm yarn packages ideal for further processing.
- Reduced Yarn Breakage - Precise tension control minimizes yarn damage during winding.
- Versatility - Handles different types of yarns including delicate and coarse fibers.
- User-Friendly Operation - Simple controls and automation reduce operator fatigue.
- Improved Efficiency - Automatic package build-up reduces manual adjustments.
- Space Saving - Compact design fits well in production lines and labs.
- Set Up the Machine - Switch on the power and check all safety guards.
- Load Yarn - Thread the yarn through tension guides and eyelets as per the manual.
- Adjust Tension - Set tension according to yarn type to avoid slack or breakage.
- Place Empty Cone/Package - Mount the empty cone or package holder securely.
- Start Winding- Press the start button; machine will begin winding at set speed.
- Monitor the Process - Observe yarn package build-up and make adjustments if necessary.
- Stop and Remove Package - Once winding is complete, stop the machine and remove the yarn package carefully.
- Maintenance - Clean the machine regularly and lubricate moving parts as needed.
- High-Speed Operation - Capable of winding yarns at fast speeds (up to 3000 RPM) to boost productivity.
- Precise Tension Control - Adjustable tension mechanism to prevent yarn breakage and ensure tight winding.
- Automatic Package Formation - Uniform, firm package build-up for consistent yarn quality.
- Versatile Yarn Compatibility - Suitable for cotton, polyester, wool, and blended yarns.
- User-Friendly Interface - Easy controls with digital or analog panels for speed and tension adjustment.
- Robust Construction - Durable stainless steel or metal frame for long-term reliability.
- Safety Features - Includes emergency stop buttons and yarn break sensors.
- Compact Design - Space-saving structure ideal for labs and production floors.
- Low Maintenance - Designed for easy cleaning and minimal upkeep.

High Speed Hard Winding Machine
Counting Balance-Weighing Scale
Counting Balance-Weighing Scale
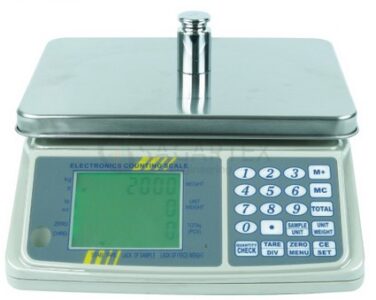
Counting Balance-Weighing Scale
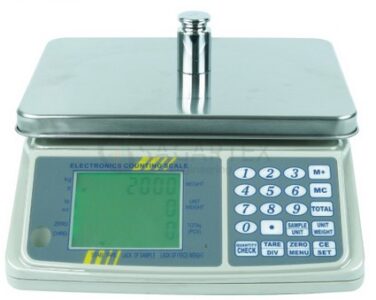
Counting Balance-Weighing Scale
Bursting strength tester
Bursting strength tester

true burst
- Available with automatic test strip feeder Measurements are simple to make with the Mullen type Bursting Strength Tester. Fast automatic measurements Measurement starts automatically once a test piece has been placed in the measuring gap. The clamping foot descends, and a bursting strength measurement is made.
- Bursting pressure can reach up to 1.2MPa 5. The maximum burst and expansion degree can reach 70mm. 6. Strengthen the lighting system on the test surface. 7. The main aerodynamic force helps to clamp the sample system. 8. A variety of test areas are available, and the switching is easy.
- A variety of unit conversions between Chinese and English. 10. Reliable anti-pinch safety protection design. [Technical parameter]: 1. Test range: (0~1)Mpa (the range above 1Mpa needs to be customized) 2. The minimum graduation value: 0.0001Mpa 3. Pressurization mode: direct pressurization, timing pressurization, and expansion degree pressurization.
Tensile Strength tester
Automatic Bobbin Hydro extractor
Automatic Bobbin Hydro extractor

Automatic Bobbin Hydro extractor
- Computer system: Foshan HuaGao Chinese English computer, equipped with LG PLC.
- Electromagnetic valve: Ningbo Jiaerling
- Frequency converter: Use Made in China frequency converters.
- Pump: self-made high head and large flow centrifugal water pump.
- Main pump motor: Anhui Wannan Motor.
- Master cylinder liquid level: Use 4-20mA analog signal output.
- Level of deputy temporary worker: use foam water level gauge. (American Mike)
- Temperature detection and display: digital temperature display instrument, dual temperature measuring probes.
- The safety system has a triple cylinder head safety interlock mechanism, and the main cylinder is equipped with a stainless
- steel safety valve.
- Heat exchanger: external spacer heating.
- Feeding system: Quantitative feeding based on the process curve.
- Circulation system: The main pump flows internally and externally, which is automatically controlled by a computer or manually controlled by a relay.
- Valves: Y valves are used for heating, stainless steel Y valves are used for single inlet and single row, and other Y valves are produced by joint ventures.
- Temperature control: on-off temperature control, controlled by a computer, with automatic heating, cooling, and insulation functions.
- Dyeing method: air cushion type.
- Opening method: manual opening.
- Surface treatment: polishing inside and outside the cylinder.
- Cage: Each dyeing machine is equipped with butterfly blades and self-locking locks.
- Body plate: high-quality stainless steel. (S31603)
- Bath ratio: 1:5-1:6
- Chemical material system: including heating and water adding functions, including overflow type salt melting device.
- Overflow cleaning: The cleaning port is installed on the upper part of the cylinder port, and the bottom of the cylinder is filled with water, while the cylinder is drained for easy cleaning.
- Commutation method: Novel "U" type commutation.
- Random accessories: Each model comes with one set of mechanical seals, pot mouth rings, and reversing seals for the main and auxiliary pumps.
Automatic Bobbin Hydro extractor