Digital Temperature Humidity Meter
$0.00
Digital Temperature Humidity Meter
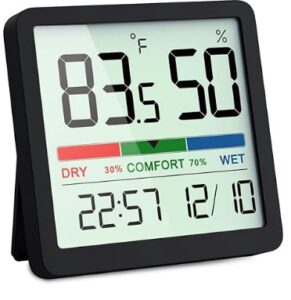
Digital Temperature Humidity Meter
A Digital Temperature Humidity Meter, also known as a digital hygrometer, is an electronic device used to measure and display the relative humidity (RH) of the air, often along with temperature. It’s commonly used in laboratories, industrial settings, storage areas, and homes to monitor moisture levels.
Key Features of Digital Temperature Humidity Meter:
– Digital Display: Shows humidity (in % RH) and often temperature (in °C/°F).
– Sensor-Based Measurement: Uses capacitive or resistive sensors for accurate readings.
– Compact & Portable: Available in handheld or wall-mountable forms.
– Data Logging (in some models): Records humidity levels over time for analysis.
– Min/Max Readings: Displays historical high and low humidity values.
Common Applications of Digital Temperature Humidity Meter:
– Laboratories: Maintaining stable humidity for experiments or sample storage.
– Warehouses: Monitoring conditions for sensitive goods (e.g., electronics, paper, pharmaceuticals).
– HVAC Systems: Ensuring proper climate control.
– Homes: Preventing mold growth or overly dry conditions.
Benefits of Digital Temperature Humidity Meter:
– Accurate and quick readings
– Easy to use and read
– Helps in maintaining comfort, safety, and product integrity
Would you like recommendations for models or guidance on calibration?
Benefits of Digital Humidity meter
Here are the key benefits of using a Digital Humidity Meter:
✅ 1. Accurate Humidity Monitoring
– Provides precise relative humidity (%RH) readings, essential for sensitive environments.
✅ 2. Fast and Real-Time Results
– Displays immediate data, allowing for quick adjustments to environmental conditions.
✅ 3. Dual Measurement
– Many models also measure temperature, offering a more complete picture of ambient conditions.
✅ 4. Easy to Use
– Simple digital interface with clear display, suitable for both professionals and non-technical users.
✅ 5. Compact and Portable
– Lightweight design makes it ideal for field use, indoor monitoring, or mounting on walls.
✅ 6. Prevents Damage
– Helps avoid moisture-related issues like mold, corrosion, static buildup, and product degradation.
✅ 7. Supports Quality Control
– Essential for labs, warehouses, and manufacturing environments to maintain product integrity.
✅ 8. Data Logging (Optional)
How to use Digital Humidity meter
Here are the key features of a Digital Humidity Meter:
1. Digital Display
– Shows real-time humidity (%) and often temperature (°C/°F).
– Some include backlit screens for easy viewing.
2. High Accuracy Sensors
– Uses capacitive or resistive sensors for accurate and stable humidity readings.
3. Min/Max & Hold Functions
– Displays minimum, maximum, and current readings.
– “Hold” function freezes the current reading for review.
4. Data Logging (in advanced models)
– Records humidity data over time for monitoring trends.
5. Portable or Wall-Mountable
– Available as handheld, desktop, or wall-mounted units for different environments.
6. Battery or USB Powered
– Operates on standard batteries or via USB power for flexibility.
7. Optional External Probes
– Some models support external humidity/temperature sensors for remote monitoring.
8. Calibration Option
– Allows manual or automatic calibration to maintain accuracy.
Here’s a quick step-by-step guide on how to use a Digital Temperature Humidity Meter:
✅ 1. Power On the Device
– Insert batteries (if portable) or plug it in (if wall-mounted).
– Press the power button to turn it on.
✅ 2. Place It Properly
– Set the meter in an open, well-ventilated area.
– Avoid placing near windows, vents, or direct heat sources for accurate readings.
✅ 3. Wait for Stabilization
– Allow the device a few seconds to stabilize and show accurate humidity and temperature readings.
✅ 4. Read the Display
– Humidity will be shown as % RH (Relative Humidity).
– Most models also display temperature in °C or °F.
✅ 5. Use Additional Features (if available)
– Press buttons to view Min/Max, Data Log, or switch units.
– Some advanced models may have Bluetooth or USB for data transfer.
✅ 6. Maintain the Device
– Clean sensor area gently if dusty.
– Calibrate periodically if required (check manual).
Related products
Counting Balance-Weighing Scale
Counting Balance-Weighing Scale
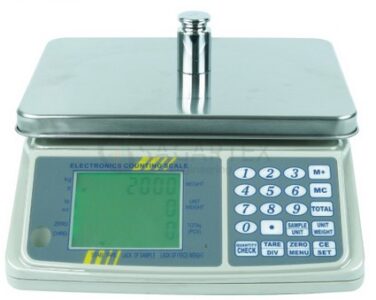
Counting Balance-Weighing Scale
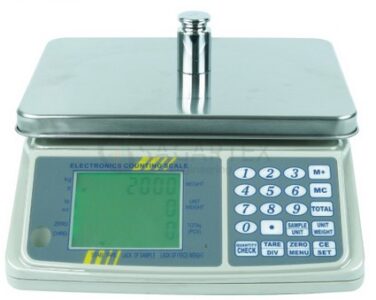
Counting Balance-Weighing Scale
Fiber Oil Fast Extractor
Fiber Oil Fast Extractor
A Fiber Oil Fast Extractor is a laboratory instrument designed to determine the oil or finish content in fibers, yarns, or fabrics, particularly wool and synthetic materials. It operates on the principle of solvent extraction followed by evaporation. Working Principle of Fiber Oil Fast Extractor:- Sample Preparation: Cut the fabric or fiber into small pieces.
- Solvent Addition: Place the sample into a metal tube and add an appropriate solvent (e.g., petroleum ether, ethyl ether).
- Extraction: Apply weight to the sample to facilitate the dissolution of oils into the solvent.
- Evaporation: The solvent-oil mixture drips onto a heated plate where the solvent evaporates, leaving behind the oil.
- Measurement: Weigh the remaining oil and calculate its percentage relative to the initial sample mass.
- Accurate Oil Content Measurement- Precisely determines oil or finish content in fibers, crucial for quality control.
- Rapid Extraction Process - Delivers fast results, improving lab efficiency and productivity.
- Simultaneous Multi-Sample Testing - Multiple workstations (e.g., 4 at once) reduce testing time for bulk samples.
- Improved Product Quality - Helps maintain consistent oil levels, which affect dyeing, processing, and fabric performance.
- Automatic Operation - Automated pressing and heating reduce manual effort and operator error.
- Digital Monitoring - Built-in timer, temperature control, and oil calculator enhance accuracy and usability.
- Compliance with Standards - Supports industry methods like GB/T 6504-2017, ensuring reliable and standard-compliant results.
- Safe Solvent Handling - Enclosed design minimizes solvent exposure and evaporation loss.
- Multiple Test Stations - Usually equipped with 2 to 4 independent work units for parallel testing.
- Automatic Weight Pressing System - Applies consistent pressure on samples for uniform solvent extraction.
- Microcomputer Temperature Control - Maintains precise heating (typically 90–120°C) with ±1°C accuracy.
- Built-in Timer and Calculator - Allows setting extraction time and calculates oil content directly.
- Solvent Evaporation Plate- Heats and evaporates solvent quickly, leaving only the oil residue.
- Digital Display - Shows time, temperature, and process status for user-friendly operation.
- Compact and Durable Design - Made with corrosion-resistant materials suited for chemical handling.
- Safety Features - Includes overheat protection and enclosed solvent chamber to reduce exposure risk.
- Standard Compliant - Designed to meet GB/T 6504-2017 and similar industry testing standards.
- Prepare the Sample - Cut 5–10 g of fiber or yarn into small pieces and place in the sample tube.
- Add Solvent - Pour a suitable solvent (e.g., petroleum ether) into the tube to cover the sample.
- Apply Weight - Place the extractor's weight or press system onto the sample to aid extraction.
- Start Extraction - Activate the machine. The solvent dissolves the oils and flows to the heating plate.
- Heat for Evaporation - Set the temperature (typically 90–120°C). The solvent evaporates, leaving oil on the plate.
- Measure Oil Content- After drying, weigh the remaining oil. Use the built-in calculator or formula:
- Clean the Unit - After cooling, clean all parts to prepare for the next test.
Fiber Oil Fast Extractor
Tensile Strength tester
Perspiration Tester
Perspiration Tester

Perspiration Tester
- Fabric samples are treated with synthetic perspiration solution (acidic or alkaline).
- They are sandwiched with adjacent fabric and placed between glass or acrylic plates.
- The assembly is loaded into the tester and pressed under specific pressure.
- it’s then incubated at 37°C (body temperature) for a fixed time (typically 4 or 16 hours).
- Afterward, color change and staining are evaluated using a gray scale.
- Accurate Sweat Simulation - Mimics real-life effects of acidic and alkaline perspiration on fabrics.
- Improves Product Quality - Ensures textiles retain color and don’t bleed or stain when worn.
- Supports Standard Compliance - Follows ISO and AATCC test standards for global market approval.
- Protects Brand Reputation- Reduces customer complaints due to dye transfer or fading.
- Simple and Repeatable- Provides consistent pressure and conditions for reliable results.
- Multi-Sample Testing- Tests multiple specimens at once, saving time in labs.
- Durable and Low Maintenance- Robust frame with minimal moving parts makes it long-lasting and easy to care for.
- Stainless Steel Frame - Corrosion-resistant body for durability and long-term use.
- Multi-Sample Capacity - Can hold up to 20 or more specimens for batch testing.
- Standardized Loading Weight- Applies uniform pressure (usually 12.5 kPa) across all samples.
- Removable Plates - Glass or acrylic plates ensure even contact and easy cleaning.
- Compact Design- Space-saving, bench-top model ideal for lab environments.
- Complies with Test Standards - Meets ISO 105 E04, AATCC 15, and related perspiration fastness standards.
- Ease of Operation - Simple loading, unloading, and incubation process.
- High-Temperature Resistance - Can be used inside incubators at 37°C or ovens as required.
- Prepare the Test Solution - Mix artificial acidic or alkaline perspiration as per standard (ISO or AATCC).
- Cut the Fabric Samples - Cut both the test fabric and adjacent white fabric (usually cotton) to standard size.
- Soak the Samples - Immerse the fabric sandwich (test + adjacent) in the test solution for 30 minutes.
- Remove Excess Liquid - Gently squeeze or blot to remove extra moisture—do not dry.
- Load in the Tester- Place each sandwich between glass or acrylic separator plates in the tester.
- Apply Pressure - Tighten the top plate or place the standard weight on top to apply uniform pressure.
- Incubate - Keep the loaded tester in an oven or incubator at 37°C for 4–16 hours (depending on the method).
- Accurate Sweat Simulation - Mimics real-life effects of acidic and alkaline perspiration on fabrics.
- Improves Product Quality - Ensures textiles retain color and don’t bleed or stain when worn.
- Supports Standard Compliance - Follows ISO and AATCC test standards for global market approval.
- Protects Brand Reputation- Reduces customer complaints due to dye transfer or fading.
- Simple and Repeatable- Provides consistent pressure and conditions for reliable results.
- Multi-Sample Testing- Tests multiple specimens at once, saving time in labs.
- Durable and Low Maintenance- Robust frame with minimal moving parts makes it long-lasting and easy to care for.
- Dry and Evaluate - Remove, air dry the samples, then assess color change and staining using a gray scale.
- Fabric samples are treated with synthetic perspiration solution (acidic or alkaline).
- They are sandwiched with adjacent fabric and placed between glass or acrylic plates.
- The assembly is loaded into the tester and pressed under specific pressure.
- it’s then incubated at 37°C (body temperature) for a fixed time (typically 4 or 16 hours).
- Afterward, color change and staining are evaluated using a gray scale.
Perspiration Tester
Stretch Recovery Tester Static Method
Stretch Recovery Tester Static Method

Stretch Recovery Tester
- A sample is stretched to a predetermined extension or force.
- The stretch is maintained for a set period.
- After removing the load, the recovery (return to original length) is measured after a fixed time.
- The fabric sample is clamped and stretched to a specific length or force.
- It’s held for a fixed duration (e.g., 1–5 minutes).
- The tension is released, and the sample is allowed to recover.
- The recovered length is measured after a set time.


Stretch Recovery Tester
Xenon Arc Light Fastness Tester
Fabric drape tester
Fabric Drape Tester
Fabric Drape Tester is a lab device used to measure the drape ability of fabric—how it hangs under its own weight. It assesses how fabric conforms in folds or waves, which affects garment appearance and comfort. Purpose of Fabric Drape Tester: To evaluate the aesthetic and functional behavior of a fabric when suspended, especially important in apparel and home textiles. Working Principle: A circular fabric specimen is placed over a smaller disc. The unsupported edges drape downward. A light source casts a shadow of the draped shape onto a recording surface or scanner. The area of the shadow is measured to calculate the drape coefficient. Main Components of Fabric Drape Tester: - Rotating Support Disc: Holds the fabric. - Light Source: Projects the drape shadow. - Paper or Digital Scanner: Captures the drape outline. - Template: For cutting fabric to standard test size. - Software or Plan meter: Calculates the drape coefficient. Applications of Fabric Drape Tester: - Fashion and apparel design - Fabric development - Quality control in woven, knitted, or nonwoven fabrics Benefits of Fabric Drape Tester:- Quantifies Fabric Flow - Measures drape behavior accurately, crucial for garments and furnishings.
- Supports Design Decisions - Helps designers select fabrics that match the intended look and movement of a product.
- Improves Garment Fit and Comfort - Ensures fabrics behave naturally on the body, enhancing wear ability.
- Enhances Product Aesthetics - Prevents stiff or limp fabric choices in fashion, interior, or technical textiles.
- Standardized Evaluation - Enables comparison across fabrics using drape coefficient, based on standards (e.g., BS 5058).
- Supports R&D - Useful in developing new fabrics or finishes to improve drape quality.
- Non-Destructive Testing - Tests fabric without damaging it, allowing for further analysis.
- Boosts Quality Control - Identifies batch inconsistencies or performance issues early in production.
- Rotating Support Disc - Holds the fabric sample over a smaller disc to create natural drape.
- Standard Sample Size Support - Designed for circular fabric samples, usually 30 cm in diameter.
- Light Projection System - Projects the draped fabric’s shadow onto a screen or recording surface.
- Drape Coefficient Calculation - Measures the shadow area to compute the drape coefficient (percentage of unsupported area covered by the shadow).
- Digital or Manual Options - Available in models with digital image processing or manual plan meter tracing.
- Stable Base and Structure - Ensures consistent and vibration-free testing conditions.
- Sample Templates Provided - For cutting precise, standard-sized fabric specimens.
- User-Friendly Interface - Simple controls for rotation and light alignment.
- Compact and Lab-Ready Design - Fits easily on lab benches and in testing environments.
- Compliance with Testing Standards - Supports BS 5058 and other relevant drape measurement methods.
- Prepare the Fabric Sample - Cut a circular fabric sample, typically 30 cm in diameter, using the provided template.
- Place the Fabric - Center the fabric sample over the smaller support disc (usually 18 cm diameter) on the tester.
- Turn on the Light Source - Illuminate the fabric from above so it casts a shadow onto the recording surface or paper below.
- Capture the Shadow Outline - Trace the shadow manually on paper or capture it digitally, depending on the model.
- Measure the Shadow Area - Use a plan meter (manual) or software (digital) to determine the shadow’s area.
- Calculate Drape Coefficient (DC) - Use the formula:
- Record the Result - Log the drape coefficient to evaluate how stiff or flexible the fabric is.
- Repeat for Accuracy - Test multiple samples and average the results for consistency.
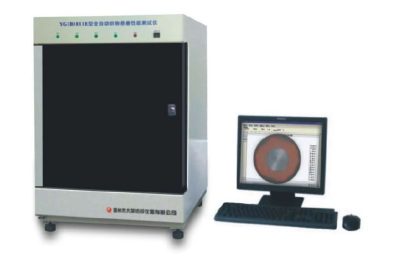
Analog Thickness Gauge
Analog Thickness Gauge
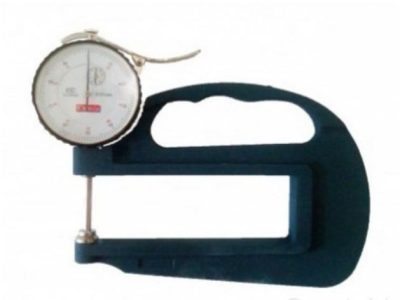
Analog Thickness Gauge
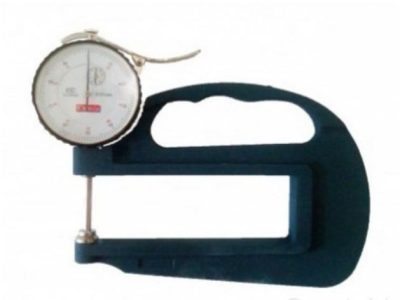
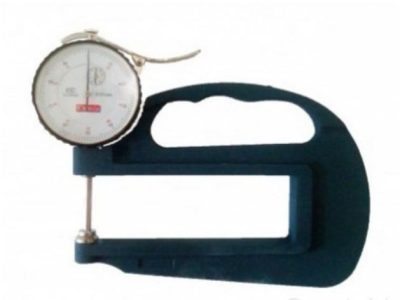
An Analog Thickness Gauge is a manual instrument used to measure the thickness of materials such as fabric, paper, leather, rubber, and plastic. Unlike digital gauges, it displays readings through a mechanical dial or scale.